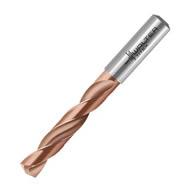
Walter USA LLC has expanded its Walter Titex X-treme line of versatile, high-performance solid carbide drills with the addition of a drill for shallow hole drilling, while maintaining high rigidity requirements. Suitable for use in a range of industries, this new drill, which augments the X-treme long drill introduced last year, is notable for both its high productivity and its hole surface finish and quality.
While the longer version drill possesses a length/diameter ratio of 5 x D, the new short version has an L/D ratio of 3 x D. Since rigidity increases as the cutting depth is reduced, this short version exhibits superior accuracy and process reliability for critical applications.
The X-treme short version is especially good at drilling angled entry/exit surfaces, convex workpiece surfaces, and cross holes. That's because a 140 degree point angle with optimized geometry and four- margins designs keep the drill in line and ensures the drilling location and processing reliability. The four margins are also beneficial in improving the surface quality of the drilled hole.
Productivity is boosted due to the drill's excellent stability; the user can reduce the number of operations such as milling a level surface or drilling a pilot hole. Additional features such as internal coolant supply and an aluminum chromium nitride-based XPL coating facilitates very high feed rates and maximum tool life. A further criterion for cost-effectiveness is the suitability of the short version drill, like all of the Walter Titex X-treme drills, for all ISO material groups. The new drill is ideal for use in an extremely wide range of industries, including general machine construction, vehicle manufacturing, the energy industry, and die and mold.
All Walter Titex X-treme drills are available from 1⁄8" to ¾" and 3 to 25mm. Cylindrical and whistle notch shank forms are available. The shank diameter tolerance is suitable for shrink fit chucks.
Contact Details
Related Glossary Terms
- coolant
coolant
Fluid that reduces temperature buildup at the tool/workpiece interface during machining. Normally takes the form of a liquid such as soluble or chemical mixtures (semisynthetic, synthetic) but can be pressurized air or other gas. Because of water’s ability to absorb great quantities of heat, it is widely used as a coolant and vehicle for various cutting compounds, with the water-to-compound ratio varying with the machining task. See cutting fluid; semisynthetic cutting fluid; soluble-oil cutting fluid; synthetic cutting fluid.
- feed
feed
Rate of change of position of the tool as a whole, relative to the workpiece while cutting.
- gang cutting ( milling)
gang cutting ( milling)
Machining with several cutters mounted on a single arbor, generally for simultaneous cutting.
- milling
milling
Machining operation in which metal or other material is removed by applying power to a rotating cutter. In vertical milling, the cutting tool is mounted vertically on the spindle. In horizontal milling, the cutting tool is mounted horizontally, either directly on the spindle or on an arbor. Horizontal milling is further broken down into conventional milling, where the cutter rotates opposite the direction of feed, or “up” into the workpiece; and climb milling, where the cutter rotates in the direction of feed, or “down” into the workpiece. Milling operations include plane or surface milling, endmilling, facemilling, angle milling, form milling and profiling.
- point angle
point angle
Included angle at the point of a twist drill or similar tool; for general-purpose tools, the point angle is typically 118°.
- shank
shank
Main body of a tool; the portion of a drill or similar end-held tool that fits into a collet, chuck or similar mounting device.
- tolerance
tolerance
Minimum and maximum amount a workpiece dimension is allowed to vary from a set standard and still be acceptable.