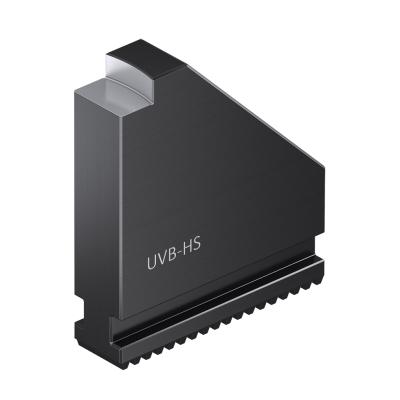
SCHUNK says the intelligent jaw design of the SCHUNK UVB-HS soft chuck jaws defines a new class of efficiency in lathe chuck technology. With a combination of overheight and angle cutting, it achieves a whole bundle of efficiency effects during finish machining of workpieces.
The unusual jaw height allows for a larger clamping surface on the workpiece, which reduces deformations. Alternatively, the distance between the workpiece to the chuck face can be increased and thus accessibility can be optimized. In comparison to conventional monoblock jaws, SCHUNK UVB-HS reduces the jaw weight by up at least 20 percent, depending on the size. This increases energy efficiency and shortens the processing time, since the lathe chuck can be accelerated and braked faster. At the same time, the reduced jaw centrifugal force allows for higher holding forces on the workpiece, which means increased process reliability.
In addition, angle cutting minimizes the danger of collisions with the turret and improves the fluid dynamics during machining. At high speeds, SCHUNK UVB-HS chuck jaws lower noise emissions by up to 10 dB, which halves the level of the perceived noise.
Because significantly lower cooling lubricant is swirled around the machining area, it is easier to see the machining process. This also lowers the amount of aerosols in the air when the machine is opened. The highly efficient monoblock jaws with angle cutting are part of the more than 1,200 jaw types in the company's standard program of chuck jaws . They are available immediately for wedge bar lathe chucks with straight serration in the sizes 200, 250/260 and 315 and can be turned individually to the desired diameter.
Contact Details
Related Glossary Terms
- chuck
chuck
Workholding device that affixes to a mill, lathe or drill-press spindle. It holds a tool or workpiece by one end, allowing it to be rotated. May also be fitted to the machine table to hold a workpiece. Two or more adjustable jaws actually hold the tool or part. May be actuated manually, pneumatically, hydraulically or electrically. See collet.
- lathe
lathe
Turning machine capable of sawing, milling, grinding, gear-cutting, drilling, reaming, boring, threading, facing, chamfering, grooving, knurling, spinning, parting, necking, taper-cutting, and cam- and eccentric-cutting, as well as step- and straight-turning. Comes in a variety of forms, ranging from manual to semiautomatic to fully automatic, with major types being engine lathes, turning and contouring lathes, turret lathes and numerical-control lathes. The engine lathe consists of a headstock and spindle, tailstock, bed, carriage (complete with apron) and cross slides. Features include gear- (speed) and feed-selector levers, toolpost, compound rest, lead screw and reversing lead screw, threading dial and rapid-traverse lever. Special lathe types include through-the-spindle, camshaft and crankshaft, brake drum and rotor, spinning and gun-barrel machines. Toolroom and bench lathes are used for precision work; the former for tool-and-die work and similar tasks, the latter for small workpieces (instruments, watches), normally without a power feed. Models are typically designated according to their “swing,” or the largest-diameter workpiece that can be rotated; bed length, or the distance between centers; and horsepower generated. See turning machine.