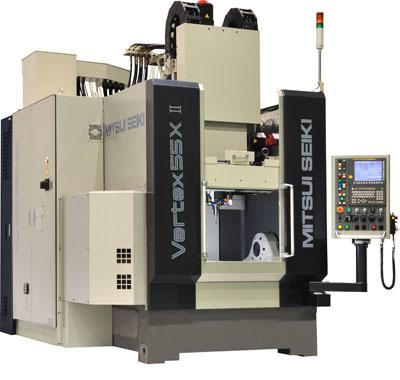
Mitsui Seiki has evolved its popular "Vertex 550-5X" line of machines with new features and capabilities, and a broader range of options and configurations within the series. The new model series, comprising six distinct models, is now called Vertex 55X II. Linear axes (X, Y, Z) strokes are 550mm (21.7") x 600mm (23.6") x 500mm (19.7").
"One of the key new features is an enhanced ultra high accuracy package. This option enhances Mitsui Seiki's existing, well-established construction techniques for accuracy and precision," said Tom Dolan, Vice President of Sales & Marketing. "As such, the Vertex line of machines are very well suited for tight-tolerance mold and die work, aerospace, energy, and other high precision component applications. Users can gain significant production improvements eliminating the traditional machine ‘warm up' time for very demanding precision jobs. Machine geometry is still unparalleled, and Positioning Accuracy in X, Y, and Z axes is 0.001mm (0.000040"). A-axis: ±6 arc seconds; C-axis: ±4 arc seconds."
In response to customer feedback and market demands, Mitsui Seiki now offers a new 30,000 rpm spindle with the Vertex 55X II, in addition to the 15,000 and 25,000 rpm choices. Customers can now take full advantage of the machine's acceleration and deceleration characteristics and high speed machining functions. An HSK-80 taper spindle connection (for those requiring more heavy-duty machining) is available as an option to compliment the existing HSK-63 and 40-taper tool interfaces.
The Vertex 55X II line includes several configurations in the range, based on table sizes and types from 225mm (9") to 400mm (15.7") diameter. A choice of rotary axis drive systems – high torque geared type or direct drive – allows for the optimum machine configuration to suit the customer needs.
Additionally, the new Vertex is available in the "B"-series version. This is a high speed 5-axis VMC dedicated to turbine blade production, which is of special interest to the aerospace and energy industries. High performance coolant and chip handling systems are available to suit customer needs. Automation devices and systems may also be integrated for on-machine inspection and work handling to further reduce setup time, and improve overall quality throughput.
Contact Details
Related Glossary Terms
- coolant
coolant
Fluid that reduces temperature buildup at the tool/workpiece interface during machining. Normally takes the form of a liquid such as soluble or chemical mixtures (semisynthetic, synthetic) but can be pressurized air or other gas. Because of water’s ability to absorb great quantities of heat, it is widely used as a coolant and vehicle for various cutting compounds, with the water-to-compound ratio varying with the machining task. See cutting fluid; semisynthetic cutting fluid; soluble-oil cutting fluid; synthetic cutting fluid.