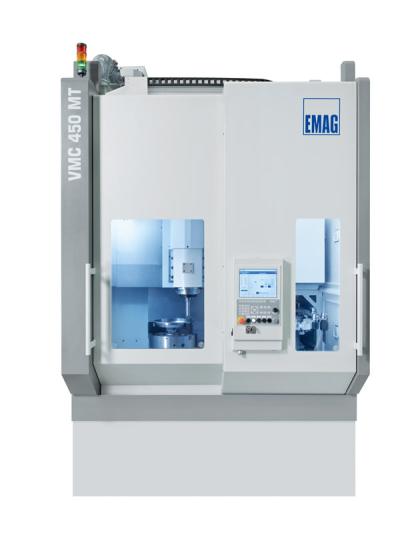
The machines in the VMC MT Series from EMAG LLC, Farmington Hills, Mich., are said to be ideal production systems for chucked parts with complex geometries, according to the company. Whether used for prototype production or for fast changes in small production runs, the VMC MT series is designed to meet the demands of flexible production situations due to the ergonomic accessibility of the machining area and the bottom-mounted workpiece spindle.
Offering several equipment options for the customer to choose from, the basic design of the VMC 300 MT, VMC 450 MT or VMC 600 MT remains the same. The machine base is made of Mineralit® plolymer concrete featuring particularly good damping properties. The turning and milling spindle is mounted on a compound slide with X- and Z-axes to produce excellent, fast machining results. The workpiece itself is clamped on one of the three bottom-mounted spindles available, 49, 83 or 138 / kW, each tailored to the machining job suiting the customer’s demands.
Benefits of the VMC MT series at a glance:
- Highly dynamic axes for short idle times and quick machining processes.
- All the service units are easy to reach.
- Axis monitoring by rotary, indirect absolute encoders. All axes with fully encapsulated linear glass scale (optional).
- Generously dimensioned main spindle, maintenance-free spindle motors and rigid guideways.
- Machine base made of MINERALIT®, 6 to 8 times better damping properties than gray cast iron.
Contact Details
Related Glossary Terms
- gang cutting ( milling)
gang cutting ( milling)
Machining with several cutters mounted on a single arbor, generally for simultaneous cutting.
- milling
milling
Machining operation in which metal or other material is removed by applying power to a rotating cutter. In vertical milling, the cutting tool is mounted vertically on the spindle. In horizontal milling, the cutting tool is mounted horizontally, either directly on the spindle or on an arbor. Horizontal milling is further broken down into conventional milling, where the cutter rotates opposite the direction of feed, or “up” into the workpiece; and climb milling, where the cutter rotates in the direction of feed, or “down” into the workpiece. Milling operations include plane or surface milling, endmilling, facemilling, angle milling, form milling and profiling.
- turning
turning
Workpiece is held in a chuck, mounted on a face plate or secured between centers and rotated while a cutting tool, normally a single-point tool, is fed into it along its periphery or across its end or face. Takes the form of straight turning (cutting along the periphery of the workpiece); taper turning (creating a taper); step turning (turning different-size diameters on the same work); chamfering (beveling an edge or shoulder); facing (cutting on an end); turning threads (usually external but can be internal); roughing (high-volume metal removal); and finishing (final light cuts). Performed on lathes, turning centers, chucking machines, automatic screw machines and similar machines.