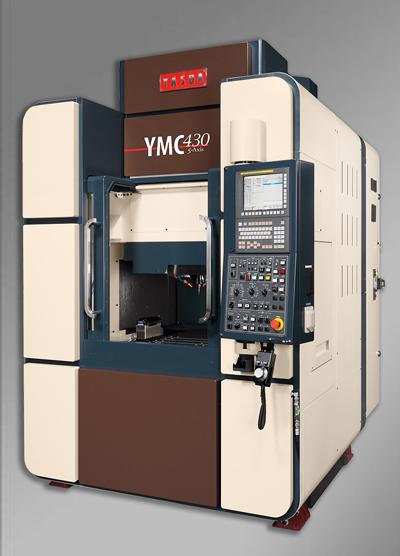
Methods Machine Tools Inc. has announced the introduction of the YASDA YMC 430 Ver. II, a new micromachining center for the ultraprecise manufacturing and fine surface finishes required on small, complex features in components and dies/molds in industries such as medical and semiconductor. Linear motor-driven controlled axes and a highly rigid machine structure offer users the highest speed, precision and surface quality machining in its class. The YASDA Micro Center YMC 430 Ver. II has a high-speed 40,000 RPM spindle and is available with 3-Axis or 5-Axis capabilities.
"We are very pleased to offer our customers who manufacture molds and components with challenging, microsized angles and geometry with a hard milling solution from YASDA," said Steve Previti, YASDA product manager. "A highly rigid symmetric frame design and unique thermal distortion stabilizing system provide consistency and repeatability, to assure users unsurpassed high accuracy."
Linear positioning and circularity accuracy of less than oneµm (according to ISO 230-2 1997) is achieved. The HSK-E32 spindle on the YMC 430 Ver. II is designed and manufactured by YASDA to minimize vibration and offer high reliability and repeatability in micro milling applications, including roughing to finishing on hardened steel and other exceptionally hard materials. A symmetrical H-shaped column and a low center of gravity structure provide high rigidity to the YMC 430 Ver. II machine structure.
The YMC 430 X-Y table has linear guideways and a linear motor drive, enabling highly precise machining and excellent vibration dampening. Linear motor drives include optical scales that support and sustain submicron milling performance. In the optional 5-Axis micro milling capability, the YMC 430 is equipped with a direct drive motor-driven, high-precision tilting rotary table. This combination provides multi-face indexing and machining as well as simultaneous 5-Axis machining without rechucking. Applying the direct drive motor to a tilted and rotary axis creates backlash-free, high-speed, high-precision positioning.
The YASDA Micro Center YMC 430 Ver. II has X,Y,Z travels of 16.5" x 11.8" x 9.8" (420mm x 300mm x 250mm), respectively. The table work surface measures 23.6" x 13.8" (600mm x 350mm). An automatic toolchanger holds 32 tools and is available in a 90-tool, large-capacity configuration. The powerful, FANUC 31i-Model B5 control is furnished standard.
Contact Details
Related Glossary Terms
- automatic toolchanger
automatic toolchanger
Mechanism typically included in a machining center that, on the appropriate command, removes one cutting tool from the spindle nose and replaces it with another. The changer restores the used tool to the magazine and selects and withdraws the next desired tool from the storage magazine. The changer is controlled by a set of prerecorded/predetermined instructions associated with the part(s) to be produced.
- gang cutting ( milling)
gang cutting ( milling)
Machining with several cutters mounted on a single arbor, generally for simultaneous cutting.
- linear motor
linear motor
Functionally the same as a rotary motor in a machine tool, a linear motor can be thought of as a standard permanent-magnet, rotary-style motor slit axially to the center and then peeled back and laid flat. The major advantage of using a linear motor to drive the axis motion is that it eliminates the inefficiency and mechanical variance caused by the ballscrew assembly system used in most CNC machines.
- milling
milling
Machining operation in which metal or other material is removed by applying power to a rotating cutter. In vertical milling, the cutting tool is mounted vertically on the spindle. In horizontal milling, the cutting tool is mounted horizontally, either directly on the spindle or on an arbor. Horizontal milling is further broken down into conventional milling, where the cutter rotates opposite the direction of feed, or “up” into the workpiece; and climb milling, where the cutter rotates in the direction of feed, or “down” into the workpiece. Milling operations include plane or surface milling, endmilling, facemilling, angle milling, form milling and profiling.
- toolchanger
toolchanger
Carriage or drum attached to a machining center that holds tools until needed; when a tool is needed, the toolchanger inserts the tool into the machine spindle. See automatic toolchanger.