Dear Doc: We cylindrical-OD-grind camshafts with a CBN wheel. We start to see chatter after about 80 camshafts, so we dress the wheel every 60 camshafts — 0.002 mm × eight passes. What’s happening? And is there a way not to dress so often and consume less wheel?
The Doc replies: It sounds like you’re getting wheel regenerative chatter as opposed to workpiece regenerative chatter. What’s the difference? Let’s start with workpiece regenerative chatter.
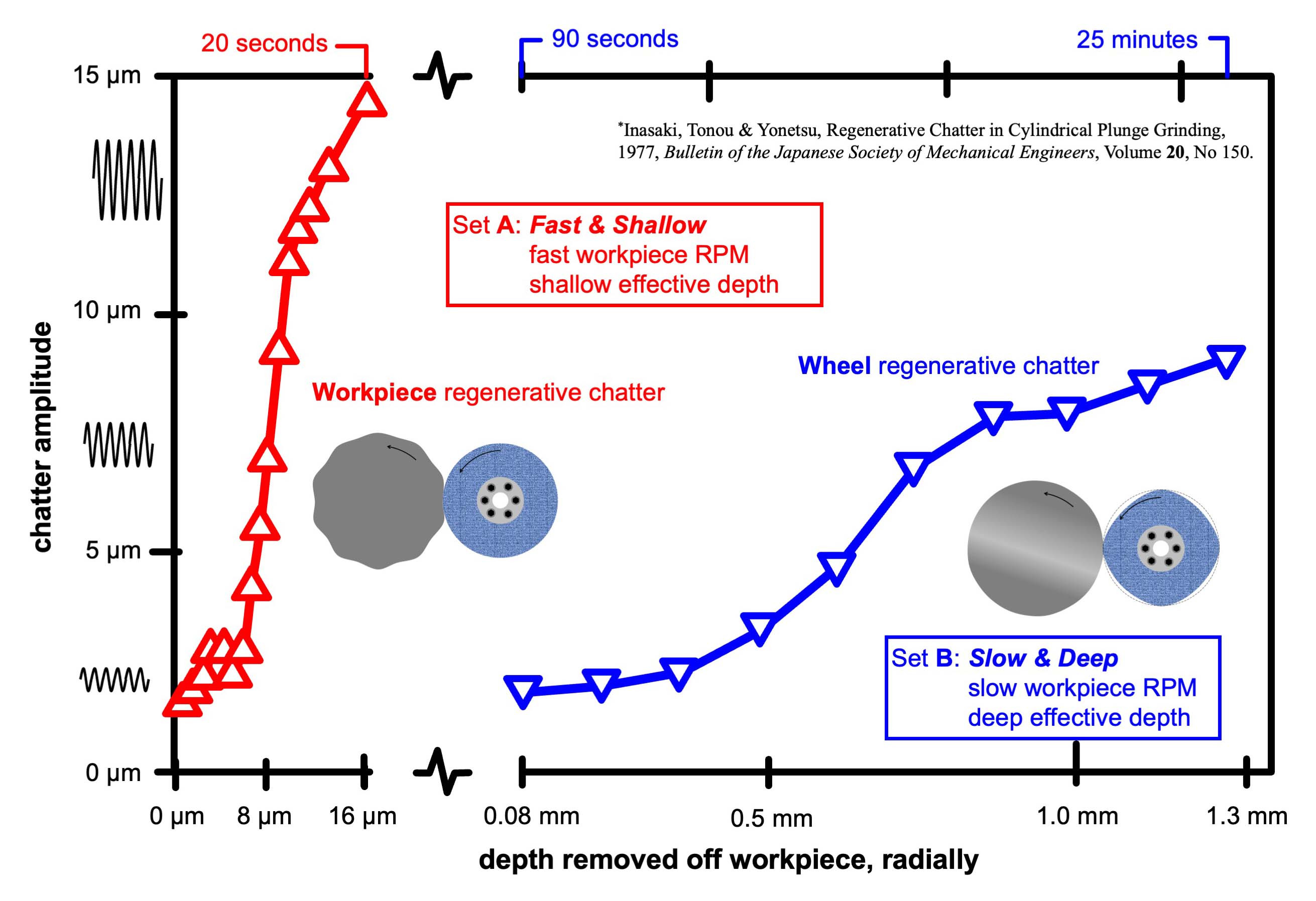
During grinding, the wheel bounces up and down at its natural frequency. (All wheels bounce at least a little.) This creates lobes on the workpiece. When they come around again on the next workpiece revolution, they cause a variation on the depth of cut, which causes a variation in the force. This variation in the force excites the system, and the wheel starts bouncing up and down even more. This creates bigger lobes, which cause bigger depth variation, which causes bigger force variation, which excites the system even more, creating even bigger lobes. The maddening cycle continues until chatter is out of control.
Because these large lobes require only a few workpiece revolutions to develop, workpiece regenerative chatter typically begins quickly — within a few seconds.
Wheel regenerative chatter is a different animal. Here, the wheel bounces up and down a little. (Again, all wheels bounce at least a little, even with a stiff spindle.) This causes the wheel to wear unevenly, creating lobes on it. They excite the system, which causes the wheel to bounce up and down even more, which creates bigger lobes on it, which excites the system even more. Next thing you know, chatter is out of control.
Because CBN wheels wear slowly, these lobes take a while to develop — maybe 15 minutes, maybe two hours. Since you’re not seeing chatter until 60 camshafts, that points to wheel regenerative chatter.
What’s the solution? Dress the wheel and get rid of the lobes.
But you’re trying to consume less wheel. So let’s do this: Instead of dressing 0.016 mm every 60 parts, let’s dress 0.004 mm every 30 parts. We’ll be removing those lobes before they become bad enough to create chatter, and we’ll be doubling wheel life.
The figure shows measurements done by Japanese grinding guru Ichiro Inasaki. When he was grinding with a fast workpiece rpm (a bad idea when trying to avoid chatter), he got workpiece regenerative chatter. Things got out of hand very quickly, within just 20 seconds. He then reduced his workpiece rpm. This eliminated the workpiece regenerative chatter. Eventually, wheel regenerative chatter started to develop. But this took 25 minutes instead of 20 seconds.
The first step to battling chatter is understanding its cause. In your case, it sounds like wheel regenerative chatter. Dress that lobed wheel and make it round again.
Related Glossary Terms
- chatter
chatter
Condition of vibration involving the machine, workpiece and cutting tool. Once this condition arises, it is often self-sustaining until the problem is corrected. Chatter can be identified when lines or grooves appear at regular intervals in the workpiece. These lines or grooves are caused by the teeth of the cutter as they vibrate in and out of the workpiece and their spacing depends on the frequency of vibration.
- cubic boron nitride ( CBN)
cubic boron nitride ( CBN)
Crystal manufactured from boron nitride under high pressure and temperature. Used to cut hard-to-machine ferrous and nickel-base materials up to 70 HRC. Second hardest material after diamond. See superabrasive tools.
- depth of cut
depth of cut
Distance between the bottom of the cut and the uncut surface of the workpiece, measured in a direction at right angles to the machined surface of the workpiece.
- dressing
dressing
Removal of undesirable materials from “loaded” grinding wheels using a single- or multi-point diamond or other tool. The process also exposes unused, sharp abrasive points. See loading; truing.
- grinding
grinding
Machining operation in which material is removed from the workpiece by a powered abrasive wheel, stone, belt, paste, sheet, compound, slurry, etc. Takes various forms: surface grinding (creates flat and/or squared surfaces); cylindrical grinding (for external cylindrical and tapered shapes, fillets, undercuts, etc.); centerless grinding; chamfering; thread and form grinding; tool and cutter grinding; offhand grinding; lapping and polishing (grinding with extremely fine grits to create ultrasmooth surfaces); honing; and disc grinding.