Dear Doc: We’re ID grinding and suffering from deflection, taper and chatter. We’re thinking of switching to a carbide quill. Will that help?
The Doc replies: Yes, it will help. Carbide has about three times the Young’s Modulus, E, or stiffness, of steel. Therefore, you can expect about one-third the spindle deflection as shown in the figure for the formula for hs, spindle deflection.
But switching to carbide is not always my first choice. Why is that? It has to do with exponents. Deflection depends on E1 (quill stiffness), L3 (quill length) and DIA4 (quill diameter). Where will you get the most bang for your buck? Quill diameter (exponent 4), then quill length (exponent 3), then quill stiffness (exponent 1).
Let’s say you’ve got a quill length of 50 mm. If you can get that down to 35 mm, that’ll give you one-third the deflection: (35/50)3 = 0.343. That’s the same as switching from steel to carbide.
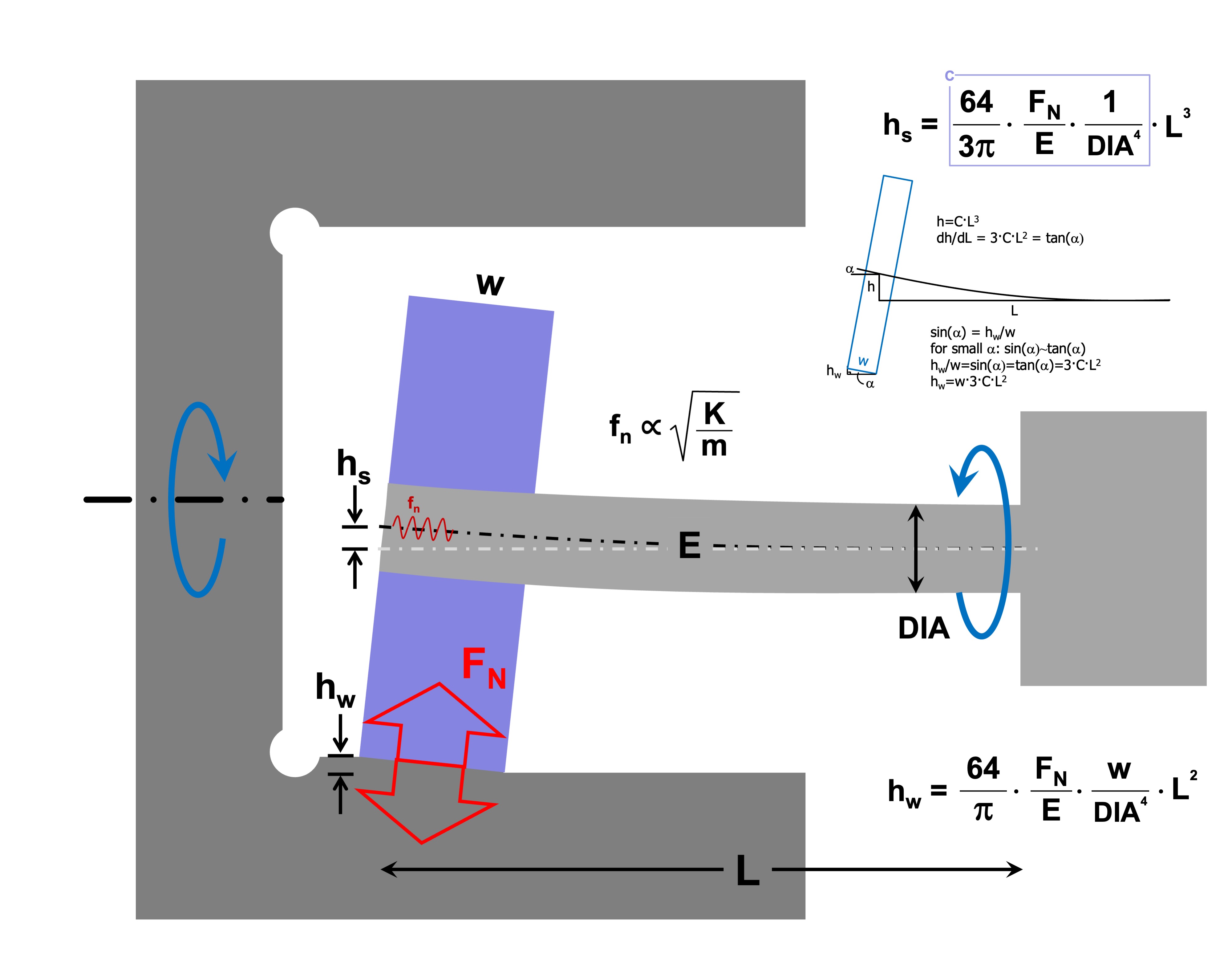
Look at diameter. It has an exponent of 4. Let’s say you have a quill diameter of 30 mm. If you can increase it to 40 mm, you’ll get about one-third the deflection: (30/40)4 = 0.316. Your diameter is only a third bigger, but you get three times the benefit. That’s the power of exponents.
That spindle deflection is what causes taper, hw, and the “bell mouth” shape that we see in cylindrical ID grinding. How to deal with it? Reduce normal force (FN), increase quill diameter (DIA), reduce quill length (L), decrease wheel width (w), or increase quill stiffness (E). Pay attention to exponents to see which one has the most effect. (Don’t forget that coolant hydroplaning can play a large roll in FN, even during spark-out.)
Finally, here’s another reason I don’t immediately jump into switching from steel to carbide: chatter. That spindle is going to bounce up and down at its natural frequency. (It always bounces at least a little.) We want it to bounce up and down at a high frequency to put those chatter marks closer together. Carbide has about double the density of steel. Unfortunately, that extra mass will decrease its natural frequency (see the equation) — not a huge amount but enough to counter at least some of the benefit of the increased stiffness. Yes, increasing the quill diameter will do the same — but only as DIA2, whereas the stiffness depends on DIA4. And length? Reducing it actually decreases mass and increases stiffness. Both of those increase the natural frequency.
Now it’s getting messy — what to prioritize? I tend to prioritize diameter (particularly near the bearings where it’s more important than near the wheel), then length, then normal force, then quill stiffness. Mostly. But not always. It depends on what’s easiest to change and whether I’m battling deflection or chatter.
That’s the simplified version. It becomes more complicated as stiffness and natural frequencies depend on numerous factors, not just what’s happening in the quill. But as far as simplified concepts go, it works.
Related Glossary Terms
- chatter
chatter
Condition of vibration involving the machine, workpiece and cutting tool. Once this condition arises, it is often self-sustaining until the problem is corrected. Chatter can be identified when lines or grooves appear at regular intervals in the workpiece. These lines or grooves are caused by the teeth of the cutter as they vibrate in and out of the workpiece and their spacing depends on the frequency of vibration.
- coolant
coolant
Fluid that reduces temperature buildup at the tool/workpiece interface during machining. Normally takes the form of a liquid such as soluble or chemical mixtures (semisynthetic, synthetic) but can be pressurized air or other gas. Because of water’s ability to absorb great quantities of heat, it is widely used as a coolant and vehicle for various cutting compounds, with the water-to-compound ratio varying with the machining task. See cutting fluid; semisynthetic cutting fluid; soluble-oil cutting fluid; synthetic cutting fluid.
- grinding
grinding
Machining operation in which material is removed from the workpiece by a powered abrasive wheel, stone, belt, paste, sheet, compound, slurry, etc. Takes various forms: surface grinding (creates flat and/or squared surfaces); cylindrical grinding (for external cylindrical and tapered shapes, fillets, undercuts, etc.); centerless grinding; chamfering; thread and form grinding; tool and cutter grinding; offhand grinding; lapping and polishing (grinding with extremely fine grits to create ultrasmooth surfaces); honing; and disc grinding.
- inner diameter ( ID)
inner diameter ( ID)
Dimension that defines the inside diameter of a cavity or hole. See OD, outer diameter.
- spark-out ( sparking out)
spark-out ( sparking out)
Grinding of a workpiece at the end of a grind cycle without engaging any further down feed. The grinding forces are allowed to subside with time, ensuring a precision surface.
- stiffness
stiffness
1. Ability of a material or part to resist elastic deflection. 2. The rate of stress with respect to strain; the greater the stress required to produce a given strain, the stiffer the material is said to be. See dynamic stiffness; static stiffness.