The pressure to decrease costs and drive up profitability means getting every ounce of efficiency from machine tools and cutting tools. To this end, shops constantly strive to reduce cycle times and extend tool life. However, while pursuing these goals, it is easy to push tools past their useful life, allowing excessive wear and its corresponding problems to occur.
Obviously, the goal is to apply a tool as many times as possible before discarding, which means resharpening it as many times as possible. When tool wear is excessive, the tool grinder must remove a large amount of material to renew the cutting edge. This shortens overall tool life and increases the reconditioning cost by increasing the time needed to renew the cutting edge.
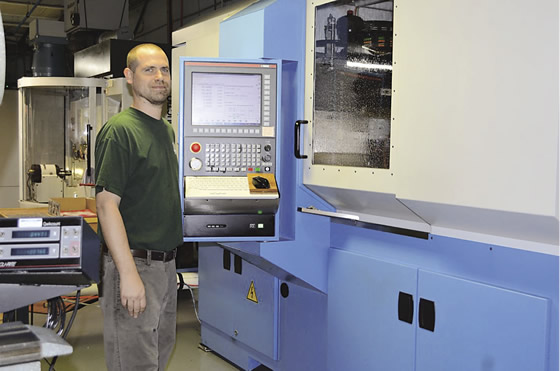
Josh Yeo, a master tool grinder at toolmaker G.W. Schultz Tool, understands that a machine shop’s goal is to apply a tool as many times as possible before discarding, which means resharpening it as many times as possible
Excessive wear also adversely affects tool performance, changing the machining conditions and dynamics. I encountered a situation where machinists were told to change tools only after a specific number of parts had been run. As tools wore, they would have to shift the work coordinates to keep the parts in spec.
Once a machinist produced the required number of parts, he inserted a new tool into the machine. However, the first part machined with the new tool was always bad. This is because a dull tool exerts more pressure on the part than a sharp tool. Therefore, the cutting pressure decreased after a tool change so the part did not push away as it did with the dull tool. Less push off, combined with shifted work coordinates, caused the part to be cut undersize.
Excessive wear can also cause catastrophic tool failure, leading to scrapped parts, rework and machine tool damage.
Tool wear is a general term that has numerous classifications. These include flank wear, adhesive wear, abrasive wear, diffusion, fatigue, delamination, microchipping, notching, gross fracture, plastic deformation, cratering and built-up edge. Each classification is a wear mechanism that can act on the tool in various ways and areas.
Determining the correct time to change a tool is a challenge. If you asked older shop guys, they would tell you to rely on sights and sounds to indicate when a tool is starting to wear. I was curious what an expert would say, so I called my friend Tomas Roman at carbide tool manufacturer G.W. Schultz Tool Inc., Tavares, Fla. He agreed that machining condition is probably the single best indicator of tool wear.
As the tool wears, the interaction of the machine, toolholder and workpiece changes. Changes in these dynamic interactions can be detected through changes in spindle load, chip appearance, surface finish and the sound of the cutting process. Detection can be as simple as feeling the surface finish and examining the parts, tools and chips. Detection can also be complex and involve sophisticated data collection devices that detect, for example, changes in amount of current consumed by the machine spindle.
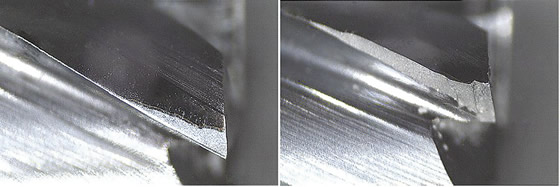
The endmill at right is chipped and will require more regrinding than the endmill on the left. Flank wear shown on the left endmill is acceptable. It is produced when the tools and application are well-matched.
When I asked about the ideal amount of wear, Roman said there is no definitive answer. The user decides the ideal amount of wear based on the application, and that amount can vary from one shop to the next.
According to Roman, when the tool exhibits only flank wear and has an acceptable life span, the tool is probably being properly applied, whereas other forms of wear indicate improper tool application. Clearance angles, coatings and edge preparations are chosen based on the material being machined and the way the tool is to be used. If the incorrect tool is selected, it is reasonable to expect undesirable tool life.
In developed processes and familiar operations, users select appropriate tools and ensure the tool and cutting operation are compatible. However, tool wear can be unpredictable when there is little machining experience to help guide tool selection.
When beginning a new job or machining an unfamiliar material, it is critical to match the tool geometry, coating and substrate to the workpiece and operation, Roman emphasized. Second, ensure the setup is as stable as possible by using high-quality toolholders and sound machining practices. Finally, make sure cutting fluids are correctly mixed and applied.
Managing tool wear is critical in the quest to control machining costs. Know how to properly use the tools by discussing the application with the cutting tool manufacturer. Understand the effect a dull tool has on the machining process and be able to anticipate changes caused by tool wear. Strive for predictability in the process; do not wait for tool failure to drive a decision. CTE
About the Author: Christopher Tate is senior advanced manufacturing engineering for Milwaukee Electric Tool Corp., Brookfield, Wis. He is based at the company’s manufacturing plant in Jackson, Miss. He has 19 years of experience in the metalworking industry and holds a Master of Science and Bachelor of Science from Mississippi State University. E-mail: [email protected].Related Glossary Terms
- abrasive
abrasive
Substance used for grinding, honing, lapping, superfinishing and polishing. Examples include garnet, emery, corundum, silicon carbide, cubic boron nitride and diamond in various grit sizes.
- built-up edge ( BUE)
built-up edge ( BUE)
1. Permanently damaging a metal by heating to cause either incipient melting or intergranular oxidation. 2. In grinding, getting the workpiece hot enough to cause discoloration or to change the microstructure by tempering or hardening.
- clearance
clearance
Space provided behind a tool’s land or relief to prevent rubbing and subsequent premature deterioration of the tool. See land; relief.
- cratering
cratering
Depressions formed on the face of a cutting tool caused by heat, pressure and the motion of chips moving across the tool’s surface.
- diffusion
diffusion
1. Spreading of a constituent in a gas, liquid or solid, tending to make the composition of all parts uniform. 2. Spontaneous movement of atoms or molecules to new sites within a material.
- endmill
endmill
Milling cutter held by its shank that cuts on its periphery and, if so configured, on its free end. Takes a variety of shapes (single- and double-end, roughing, ballnose and cup-end) and sizes (stub, medium, long and extra-long). Also comes with differing numbers of flutes.
- fatigue
fatigue
Phenomenon leading to fracture under repeated or fluctuating stresses having a maximum value less than the tensile strength of the material. Fatigue fractures are progressive, beginning as minute cracks that grow under the action of the fluctuating stress.
- flank wear
flank wear
Reduction in clearance on the tool’s flank caused by contact with the workpiece. Ultimately causes tool failure.
- metalworking
metalworking
Any manufacturing process in which metal is processed or machined such that the workpiece is given a new shape. Broadly defined, the term includes processes such as design and layout, heat-treating, material handling and inspection.
- plastic deformation
plastic deformation
Permanent (inelastic) distortion of metals under applied stresses that strain the material beyond its elastic limit.
- toolholder
toolholder
Secures a cutting tool during a machining operation. Basic types include block, cartridge, chuck, collet, fixed, modular, quick-change and rotating.