Using heat to soften materials for easier processing is nothing new. Blacksmiths and glassblowers have long used flame to make their wares pliable. Yet neither of these processes actually removes material—the heat serves only to make the material workable.
Laser-assisted machining (LAM) takes that concept to the next level by combining lasers and conventional machine tools. The energy generated by the laser heats metal or ceramic to high temperatures, which softens the material and makes it easier to slice than a piece of cheese.
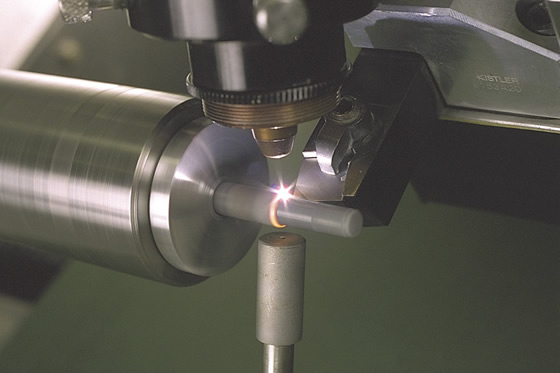
Turning silicon nitride is made much easier using LAM to soften the material prior to cutting it. Image courtesy Purdue University.
This doesn’t mean the decision to adopt LAM is a simple one. For one thing, lasers are relatively expensive. Few shops are willing to invest $50,000 or more to make machining easier, not when conventional means will do the job—albeit more slowly. Adding to the cost is the guarding required, because improperly handled laser light may harm human eyes and skin. And heating a workpiece held in a lathe or machining center must be done carefully to avoid thermal growth and possible damage to bearings and motors.
Despite this, LAM may be gaining appeal as laser prices have dropped. The world’s hunger for advanced ceramics, titanium and other superhard alloys continues to push manufacturers towards ever-more-innovative methods of processing these difficult-to-machine materials. To some, LAM is the silver bullet.
Leaving the Dark Ages
While LAM is still far from mainstream, it has made substantial progress, according to Dr. Yung Shin, professor of the Laser-Assisted Materials Processing Lab at Purdue University’s School of Mechanical Engineering. Shin has been working on the process for 20 years. “When I started, there was very little interest from manufacturers,” he said. “It was more or less the Dark Ages of LAM. That’s all changed over the past decade.”
Shin said commercial LAM development is underway worldwide, with Asia and Germany leading the pack. He noted the primary reason is the small number of U.S. machine tool builders. This makes it difficult for U.S.-based researchers to collaborate with OEMs on machine integration.
Another roadblock is the very nature of LAM. “Laser-assisted machining is a process that requires multiple steps to implement,” Shin explained. “That makes it challenging to market. If it were a product in the sense of a catalog item, it would be much simpler to sell.”
That’s not to say LAM hasn’t attracted interest in the U.S. On the contrary, a large number of companies are exploring the process for their own use. According to Shin, practically every major aerospace and automotive manufacturer has approached Purdue and expressed interest in LAM. “Many of these companies have helped fund our research,” he said. “They recognize the substantial economic benefits and are now in the process of implementing LAM at their own facilities.”
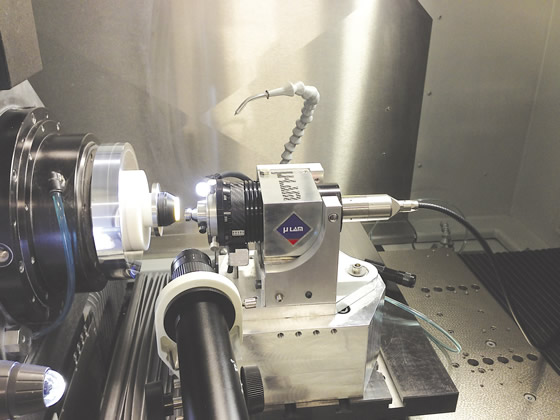
A Micro-LAM system installed on a diamond turning machine is ready to machine a ceramic lens. Image courtesy Micro-LAM Technologies.
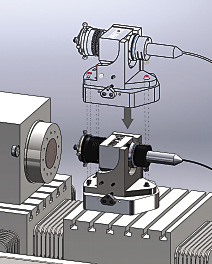
A machine retrofit where a Micro-LAM system is added to a tooling stage. Image courtesy Micro-LAM Technologies.
Due to nondisclosure agreements, Shin is unable to share many details of these projects, but cited one example of a micropart producer that filed a patent on its LAM process, which the company estimated will save $10 million per year in manufacturing costs. Another company using ceramic parts in its fuel injector assemblies was able to replace seven of its form-grinding machines—valued at $1 million each—with a single laser-assisted turning machine.
A less-secret example is a titanium machining project at Boeing Corp., in which Shin helped demonstrate a 30 to 40 percent reduction in machining time via LAM. He said: “That’s probably the main reason this has taken so long to catch on. Back when everyone was mainly machining aluminum and steel, there was no need. But with all the work recently on advanced materials such as composites and high-temperature alloys, machining has become a real challenge.”
Diamonds are a LAM’s Best Friend
One company working on commercialization of laser-assisted machining is Micro-LAM TechnologiesInc., which has a manufacturing facility in Battle Creek, Mich., and a research facility at Western Michigan University. As Chief Technical Officer Deepak Ravindra explained, the company is collaborating with machine builders and users of diamond turning machines to improve precision-optics manufacturing.
“Diamond turning is a very efficient way to produce optical-quality parts, especially ceramic ones,” he said. “However, these materials are so hard that extensive tool wear is a problem, as is fracturing the material under heavy cuts. We’ve developed a hybrid system that shines infrared laser light directly at the point where the cutting tool contacts the workpiece, thus softening the material.”
Micro-LAM treads a “Goldilocks” line of not-too-hot, not-too-cold laser energy, one that if not controlled can easily turn hard, brittle ceramic into a taffy-like mess. Ravindra said the thermal sweet spot is material-dependent, but typically hovers around 700° to 1,000° C (1,292° to 1,832° F). “It’s pretty hot, but you have to remember that the soft area is small—20µm to 100µm across—and the heat falls away with the chips. There are no negative effects on the material. The results are much lower cutting forces, improved surface finish and significantly enhanced tool life.”
Ravindra said Micro-LAM temporarily reduces the hardness of ceramic by 50 percent or more without affecting its post-machining strength or material properties. Micro-LAM also shows promise in reducing machining times on Inconel and other superalloys, although initial results—while impressive—are not in the same league as they are for friable materials, such as ceramics.
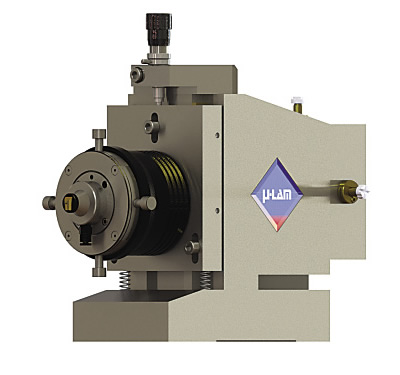
CAD drawing of a commercially available Micro-LAM system that can be retrofit to a diamond turning lathe in less than 20 minutes. Image courtesy Micro-LAM Technologies.
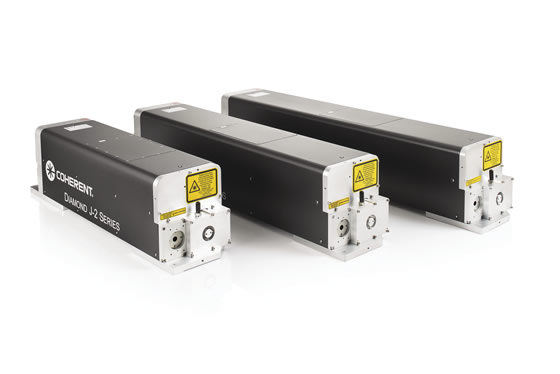
CO2 lasers are used in numerous LAM applications. Image courtesy Coherent.
“We haven’t done extensive testing with superalloys, only because the overwhelming response from the ceramics industry is consuming most of our efforts,” he said. “The value proposition here is significantly higher than that of other materials. Given the potential for quick payback on investment, it’s a massive market.”
That return on investment may be as fast as 6 months for some high-volume manufacturers on an investment of less than $200,000, Ravindra claimed. And, compared to other industrial lasers that consume kilowatts of electricity to operate, Micro-LAM uses less power than a 60w lamp.
Keep it Clean
Someone who knows laser power is Frank Gaebler, marketing director for laser provider Coherent Inc., Santa Clara, Calif. Gaebler agreed there’s substantial interest in LAM, particularly among those manufacturers processing ceramic materials, but the environment in a machine tool presents some obstacles.
“There are cutting fluids and debris that may contaminate optics or even damage them if protective measures aren’t taken,” he said. “This is not much of a problem with industrial cutting lasers because the optics are shielded with a gas stream or protective window, making them less delicate and prone to environmental interference. It’s far different than the controlled and delicate heating of material that occurs with LAM.”
Another consideration is the variety of materials many shops process. As Gaebler explained, the cutting lasers used in sheet metal shops require a shielding gas to create an exothermic reaction, similar to flame or plasma cutting. The same laser can cut stainless steel, brass or aluminum by simply changing the gas. Not so with LAM, which relies on the correct wavelength and power level to heat and, therefore, soften the workpiece.
Nor are there general-purpose, tunable-frequency lasers available, except for scientific applications. “As a rule, you would need to change lasers to process substantially different materials,” Gaebler said. “Despite the challenges, however, I’ve seen LAM used successfully with special alloys and ceramic materials that are very difficult to process otherwise.”
Bearing Down
One of these materials is silicon nitride. Richard Roberts, director of corporate development at Reliance Tool & Manufacturing Co., Elgin, Ill., said the company has developed a proprietary process that heats this superhard ceramic to 1,100° to 1,300° C (2,012° to 2,372° F). “All you’re really doing is getting it hot enough to melt the ceramic binder. The temperature is easily controlled through adjustment of a single parameter in the laser control. We find it to be a whole lot faster than grinding.”
Reliance’s work with LAM evolved from hard turning. “Around 13 years ago,” he said, “we were having trouble turning a ceramic cylinder liner for a racing engine. The boss said, ‘Let’s try heating it up.’ So one of our guys used an acetylene torch. It worked, but we struggled with maintaining the temperature. That’s when we turned to lasers.”
Reliance teamed with Northern Illinois University’s Department of Mechanical Engineering and eventually won a contract from the Department of Defense to commercialize the system. “By and large we succeeded, but if you’re producing components for helicopters and aircraft, it takes years to get approval,” Roberts said. “We do not have the system in production at this point.”
The Reliance system uses a 1,000w laser to heat items 3 " to 4 " (76.2mm to 101.6mm) in diameter, the majority of which are used for hybrid ceramic and steel roller bearings. “We hope to get LAM to the point where it’s efficient enough to produce low-cost ceramic components that can be used in a large number of applications,” Roberts said. “Ceramic is basically indestructible.” CTE
Contributors
Coherent Inc.
(800) 227-8840
www.coherent.com
Micro-LAM Technologies Inc.
(269) 276-3461
www.microlamtechnologies.com
Purdue University School of Mechanical Engineering
(765) 494-9775
www.engineering.purdue.edu/LAMPL
Reliance Tool & Manufacturing Co.
(847) 695-1234
www.reliancetool.com
Related Glossary Terms
- alloys
alloys
Substances having metallic properties and being composed of two or more chemical elements of which at least one is a metal.
- ceramics
ceramics
Cutting tool materials based on aluminum oxide and silicon nitride. Ceramic tools can withstand higher cutting speeds than cemented carbide tools when machining hardened steels, cast irons and high-temperature alloys.
- composites
composites
Materials composed of different elements, with one element normally embedded in another, held together by a compatible binder.
- computer-aided design ( CAD)
computer-aided design ( CAD)
Product-design functions performed with the help of computers and special software.
- grinding
grinding
Machining operation in which material is removed from the workpiece by a powered abrasive wheel, stone, belt, paste, sheet, compound, slurry, etc. Takes various forms: surface grinding (creates flat and/or squared surfaces); cylindrical grinding (for external cylindrical and tapered shapes, fillets, undercuts, etc.); centerless grinding; chamfering; thread and form grinding; tool and cutter grinding; offhand grinding; lapping and polishing (grinding with extremely fine grits to create ultrasmooth surfaces); honing; and disc grinding.
- hard turning
hard turning
Single-point cutting of a workpiece that has a hardness value higher than 45 HRC.
- hardness
hardness
Hardness is a measure of the resistance of a material to surface indentation or abrasion. There is no absolute scale for hardness. In order to express hardness quantitatively, each type of test has its own scale, which defines hardness. Indentation hardness obtained through static methods is measured by Brinell, Rockwell, Vickers and Knoop tests. Hardness without indentation is measured by a dynamic method, known as the Scleroscope test.
- lathe
lathe
Turning machine capable of sawing, milling, grinding, gear-cutting, drilling, reaming, boring, threading, facing, chamfering, grooving, knurling, spinning, parting, necking, taper-cutting, and cam- and eccentric-cutting, as well as step- and straight-turning. Comes in a variety of forms, ranging from manual to semiautomatic to fully automatic, with major types being engine lathes, turning and contouring lathes, turret lathes and numerical-control lathes. The engine lathe consists of a headstock and spindle, tailstock, bed, carriage (complete with apron) and cross slides. Features include gear- (speed) and feed-selector levers, toolpost, compound rest, lead screw and reversing lead screw, threading dial and rapid-traverse lever. Special lathe types include through-the-spindle, camshaft and crankshaft, brake drum and rotor, spinning and gun-barrel machines. Toolroom and bench lathes are used for precision work; the former for tool-and-die work and similar tasks, the latter for small workpieces (instruments, watches), normally without a power feed. Models are typically designated according to their “swing,” or the largest-diameter workpiece that can be rotated; bed length, or the distance between centers; and horsepower generated. See turning machine.
- machining center
machining center
CNC machine tool capable of drilling, reaming, tapping, milling and boring. Normally comes with an automatic toolchanger. See automatic toolchanger.
- superalloys
superalloys
Tough, difficult-to-machine alloys; includes Hastelloy, Inconel and Monel. Many are nickel-base metals.
- turning
turning
Workpiece is held in a chuck, mounted on a face plate or secured between centers and rotated while a cutting tool, normally a single-point tool, is fed into it along its periphery or across its end or face. Takes the form of straight turning (cutting along the periphery of the workpiece); taper turning (creating a taper); step turning (turning different-size diameters on the same work); chamfering (beveling an edge or shoulder); facing (cutting on an end); turning threads (usually external but can be internal); roughing (high-volume metal removal); and finishing (final light cuts). Performed on lathes, turning centers, chucking machines, automatic screw machines and similar machines.
- turning machine
turning machine
Any machine that rotates a workpiece while feeding a cutting tool into it. See lathe.