With hardness greater than 40 Gpa, diamond-like coatings (DLCs) provide a low coefficient of friction, resist chemical attack and protect against abrasive wear for a host of applications, such as cutting tools and wear components in machine tools.
Conventional pulsed-laser deposition (PLD) takes place in a vacuum chamber and deposits thin films of coatings, such as DLCs, but it’s difficult to deposit uniform coatings and form the required particle-free coatings, according to Picodeon Ltd. Oy, a coating equipment manufacturer. These challenges limit the scalability of the process to industrial production.
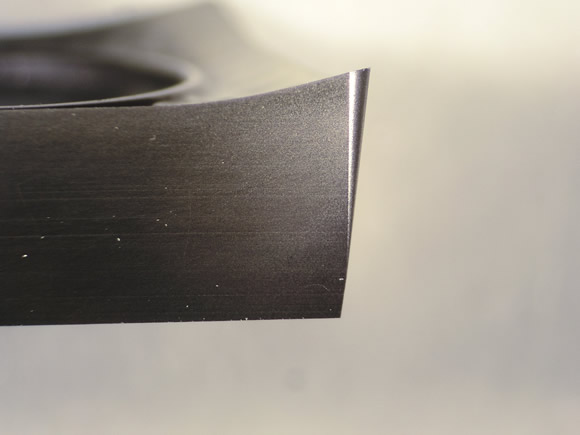
A cutting tool insert with a diamond-like coating deposited via Picodeon’s Coldab US PLD process.
To achieve the desired composition, the company reported that it developed the ultrashort PLD cold-ablation process based on a high-power laser beam with a pulse duration typically less than 10 picoseconds. (A picosecond is one trillionth—0.000000000001—of a second.) This enables coating substrates at temperatures below 100° to 150° C. In addition, a cold-ablation method’s plasma does not contain a significant proportion of molten material and particles, which are found in hot-ablation processes that use lasers with pulse lengths in the nanosecond regime.
Called Coldab, the US PLD technology is suitable for depositing DLCs and other coatings with thicknesses from a few hundred nanometers to 2µm to 3µm on virtually any substrate, including metals, ceramics, composites, elastomers and even tissue paper.
“Any components that need to have the highest possible hardness or wear resistance can achieve improved life cycles, greater heat and pressure resistance and/or improved performance with diamond-like coatings,” said Picodeon CEO Marko Mylläri. “Our US PLD process can deliver the exact surface defined by our customers’ engineers because of the high level of tuning enabled by our process.”
The tunable process parameters include pulse energy, pulse length, repetition rate and substrate preheating, the company stated. In addition to cleaning substrates to remove dirt and moisture prior to coating, some materials are preheated from 800° to 950° C (1,472° to 1,742° F) to promote the formation of a suitable surface structure.
Because cubic boron nitride and carbon nitride coatings are stable at extreme temperatures and offer low chemical reactivity when cutting hardened steels and other ferrous materials, the company is developing technology for depositing those materials as coatings. However, they are quite difficult to produce as thin coatings.
For more information about Picodeon Ltd. Oy, Li, Finland, call +358-40-533-3432 or visit www.picodeon.com. CTE
About the Author: Alan Richter is editor of CTE. Contact him at (847) 714-0175 or [email protected].Related Glossary Terms
- abrasive
abrasive
Substance used for grinding, honing, lapping, superfinishing and polishing. Examples include garnet, emery, corundum, silicon carbide, cubic boron nitride and diamond in various grit sizes.
- ceramics
ceramics
Cutting tool materials based on aluminum oxide and silicon nitride. Ceramic tools can withstand higher cutting speeds than cemented carbide tools when machining hardened steels, cast irons and high-temperature alloys.
- composites
composites
Materials composed of different elements, with one element normally embedded in another, held together by a compatible binder.
- cubic boron nitride ( CBN)
cubic boron nitride ( CBN)
Crystal manufactured from boron nitride under high pressure and temperature. Used to cut hard-to-machine ferrous and nickel-base materials up to 70 HRC. Second hardest material after diamond. See superabrasive tools.
- hardness
hardness
Hardness is a measure of the resistance of a material to surface indentation or abrasion. There is no absolute scale for hardness. In order to express hardness quantitatively, each type of test has its own scale, which defines hardness. Indentation hardness obtained through static methods is measured by Brinell, Rockwell, Vickers and Knoop tests. Hardness without indentation is measured by a dynamic method, known as the Scleroscope test.
- preheating
preheating
Heating before some further thermal or mechanical treatment.
- wear resistance
wear resistance
Ability of the tool to withstand stresses that cause it to wear during cutting; an attribute linked to alloy composition, base material, thermal conditions, type of tooling and operation and other variables.