When shops purchase new machinery, a common error some make is accepting the standard live tooling package from the builder without considering other options. This is not a criticism of those packages, but end users should do as much evaluation of their processes when determining the proper tooling package as they do when evaluating machine tools. This examination can range from the simple, such as external vs. internal coolant, to the sublime, such as adjustable vs. extended tooling configurations, to the truly exotic.
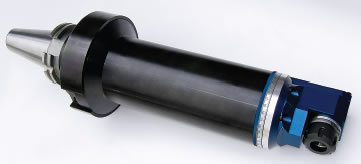
A large, deep-pocket tool, such as this one from Heimatec, might initially seem too expensive, but a machining test can prove otherwise. Image courtesy Heimatec.
Live tooling is driven by the CNC, the spindle turret and powered subspindle config-urations on CNC lathes to perform various operations while the workpiece remains oriented to the main spindle. As opposed to static tools applied when turning, these devices, whether with BMT (base mount tooling) or VDI (German acronym for the Association of German Engineers) connections, are also called driven tools and are usually customized for a particular machine tool builder’s turret assembly.
Live tooling is generally offered in standard straight and 90º con-figurations with various tool output clamping systems, including col-let chuck, arbor, Weldon, Capto, whistle notch, hydraulic, HSK, CAT and ABS.
The types of live tooling appro-priate for shops depend on the jobs they machine. Two seemingly iden-tical job shops can have vastly differ-ent tooling needs because, for ex-ample, one serves the automotive industry and the other serves medical, or one specializes in low-volume work while the other predominantly sees long part runs.
Bearing construction and the re-sulting spindle concentricity drive the life of any live tool. Even in-vesting just 10 to 15 percent more to obtain a better design can sig-nificantly extend cutter life and im-part consistently finer surface fin-ishes. For example, roller bearings are consistently superior to spindle bearings in live tooling applications.
Another consideration is whether the turret rpm is sufficient for the work at hand. If not, a speed in-creaser can be used on the tool.
The most often overlooked con-sideration when buying live tooling, however, is the long-term flexibility it provides. The work a shop has currently, the work it is likely to see and the overall costs and benefits of using a changeable adapter system on live tooling are frequently not adequately considered when pur-chasing a machine. Dedicated live tools for large part families may be desirable, but consider a change-able adapter system for low-volume runs that require frequent change-overs and talk to the supplier before making that determination. Like-wise, if the work being bid on in-volves additional product families, think ahead when buying the initial tooling package.
Also, adjustable angle head sys-tems can be costly, but their stabil-ity and rigidity make them worth the price. This is particularly true when producing part families with only slight differences in dimensions.
The following example shows the value of conducting test runs with alternative live tool styles. One com-pany was cross-milling a 6063 alumi-num sheave, using an ER40 output tool on a Eurotech lathe and running at 10 ipm and 4,000 rpm. It was mak-ing three passes and getting a sub-standard, chatter finish on 20,000 pieces per year. Cycle time was 262 seconds. Annual machining cost was more than $130,000. By using an im-proved adapter tool with an ER32AX output and the same parameters, the shop was able to make the part in a single pass, impart a smooth finish and reduce cycle time to 172 seconds. This produced annual sav-ings of $45,000, about 20 times what the tool costs.
In the end, you may not need a +135º/-30 universal adjustable tool, a multispindle live holder or even a quick-change adapter system, but consider the options. Talk to the machine builder, several tool suppli-ers, and especially the most important people in this equation—your shop personnel.
Related Glossary Terms
- arbor
arbor
Shaft used for rotary support in machining applications. In grinding, the spindle for mounting the wheel; in milling and other cutting operations, the shaft for mounting the cutter.
- chatter
chatter
Condition of vibration involving the machine, workpiece and cutting tool. Once this condition arises, it is often self-sustaining until the problem is corrected. Chatter can be identified when lines or grooves appear at regular intervals in the workpiece. These lines or grooves are caused by the teeth of the cutter as they vibrate in and out of the workpiece and their spacing depends on the frequency of vibration.
- chuck
chuck
Workholding device that affixes to a mill, lathe or drill-press spindle. It holds a tool or workpiece by one end, allowing it to be rotated. May also be fitted to the machine table to hold a workpiece. Two or more adjustable jaws actually hold the tool or part. May be actuated manually, pneumatically, hydraulically or electrically. See collet.
- computer numerical control ( CNC)
computer numerical control ( CNC)
Microprocessor-based controller dedicated to a machine tool that permits the creation or modification of parts. Programmed numerical control activates the machine’s servos and spindle drives and controls the various machining operations. See DNC, direct numerical control; NC, numerical control.
- coolant
coolant
Fluid that reduces temperature buildup at the tool/workpiece interface during machining. Normally takes the form of a liquid such as soluble or chemical mixtures (semisynthetic, synthetic) but can be pressurized air or other gas. Because of water’s ability to absorb great quantities of heat, it is widely used as a coolant and vehicle for various cutting compounds, with the water-to-compound ratio varying with the machining task. See cutting fluid; semisynthetic cutting fluid; soluble-oil cutting fluid; synthetic cutting fluid.
- inches per minute ( ipm)
inches per minute ( ipm)
Value that refers to how far the workpiece or cutter advances linearly in 1 minute, defined as: ipm = ipt 5 number of effective teeth 5 rpm. Also known as the table feed or machine feed.
- lathe
lathe
Turning machine capable of sawing, milling, grinding, gear-cutting, drilling, reaming, boring, threading, facing, chamfering, grooving, knurling, spinning, parting, necking, taper-cutting, and cam- and eccentric-cutting, as well as step- and straight-turning. Comes in a variety of forms, ranging from manual to semiautomatic to fully automatic, with major types being engine lathes, turning and contouring lathes, turret lathes and numerical-control lathes. The engine lathe consists of a headstock and spindle, tailstock, bed, carriage (complete with apron) and cross slides. Features include gear- (speed) and feed-selector levers, toolpost, compound rest, lead screw and reversing lead screw, threading dial and rapid-traverse lever. Special lathe types include through-the-spindle, camshaft and crankshaft, brake drum and rotor, spinning and gun-barrel machines. Toolroom and bench lathes are used for precision work; the former for tool-and-die work and similar tasks, the latter for small workpieces (instruments, watches), normally without a power feed. Models are typically designated according to their “swing,” or the largest-diameter workpiece that can be rotated; bed length, or the distance between centers; and horsepower generated. See turning machine.
- turning
turning
Workpiece is held in a chuck, mounted on a face plate or secured between centers and rotated while a cutting tool, normally a single-point tool, is fed into it along its periphery or across its end or face. Takes the form of straight turning (cutting along the periphery of the workpiece); taper turning (creating a taper); step turning (turning different-size diameters on the same work); chamfering (beveling an edge or shoulder); facing (cutting on an end); turning threads (usually external but can be internal); roughing (high-volume metal removal); and finishing (final light cuts). Performed on lathes, turning centers, chucking machines, automatic screw machines and similar machines.