By James Engineering
Deburring is one of the drawbacks of CNC machining. Do you manually handle it with shop floor personnel using a knife, or do you program a machining center to do it?
If it’s the former, your machine operators or other employees must devote time to that instead of performing different — maybe more valuable — tasks. Plus, results vary from person to person.
If it’s the latter, the machine is tied up performing cleanup work when the machine could be on to the next complex part. Perhaps worse, swarf or abrasives from deburring operations can work their way down to the machine’s linear guides and ballscrews, which could reduce its positioning accuracy and eventually bring that critical piece of equipment down for repair.
Vibratory tumbling is another option. However, this might require masking of vital part features, and for shops with only one such machine, frequent setups may be in store because different media will be required for different jobs.
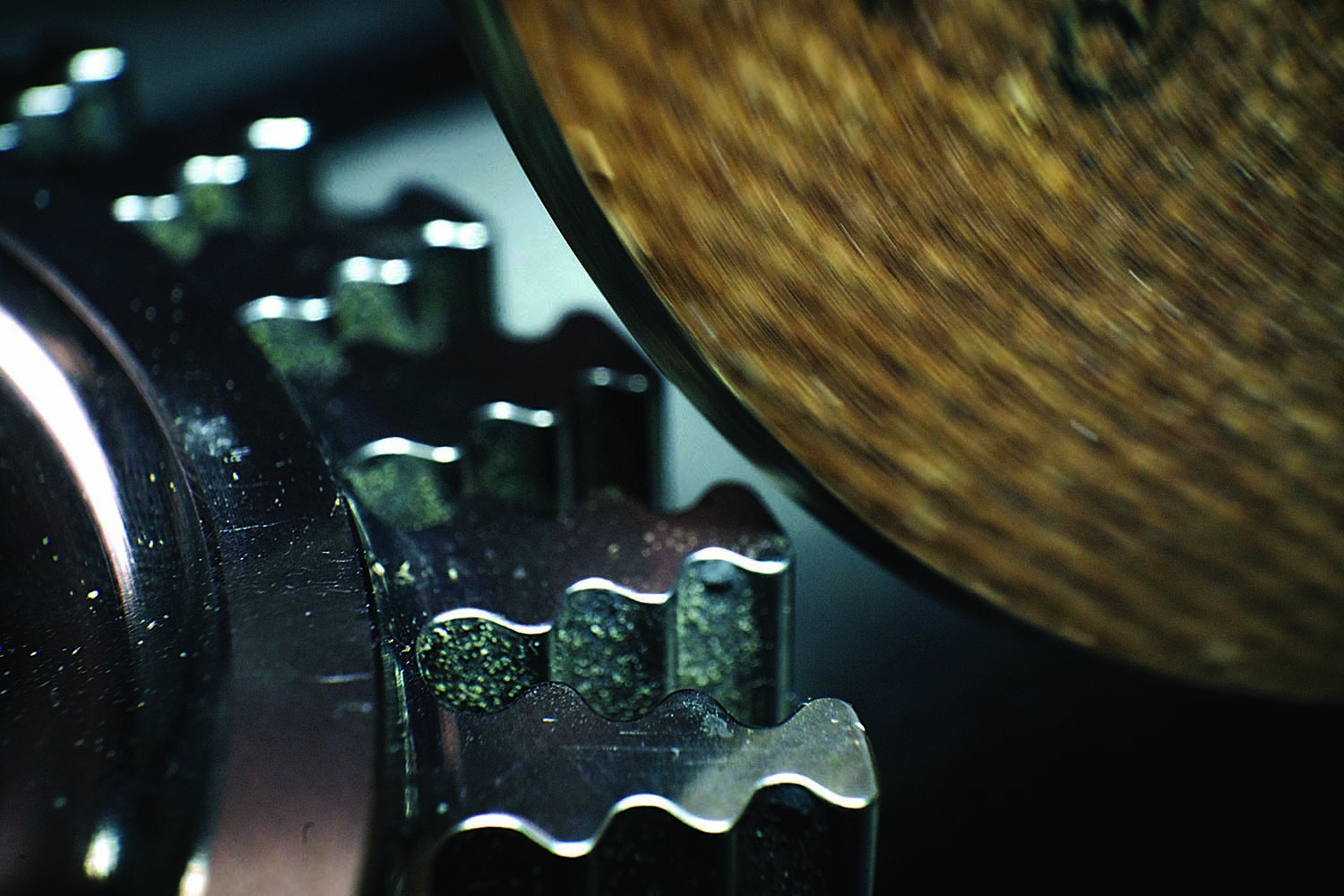
James Engineering in Broomfield, Colorado, builds an automated alternative with its 11-axis Max System CNC deburring and chamfering machine that includes proprietary compliant technology to speed and simplify programming, setup and operation. Compliant technology enables deburring and chamfering tools to maintain a constant force on a part as they follow its features.
Gearing Up
James Richards started the company in the early 1980s. At the time, he developed precision deburring and chamfering techniques to finish gears used in Formula One race cars. He went on to create hundreds of custom gear deburring and chamfering machines for advanced applications in automotive, aerospace and myriad other industries. His most recent development, the Max System, allows the process to be applied not only to gears and shaft components but to prismatic ones.
This machine consists of two five-axis heads and a c-axis rotary table. Servos position the heads via an x/y/z overhead gantry using hardened chrome, ground shafts and carriers with multiple pre-loaded bearings. Movements as fast as 1,500 ipm are possible. Plus, the overhead design means that swarf and abrasive material won’t work their way down into the carrier or onto the gantry shafts. In addition, the machine features nozzles that deliver water-based coolant with rust
inhibitor at 200 gpm not only to keep parts and tools cool during operations but to wash parts and the machine work zone. The two heads can concurrently perform finishing operations using various brushes and abrasive tools to minimize overall cycle times.
Richards also developed a compact 4,000 psi hydraulically driven motor for the heads, providing up to 25,000 rpm using only one moving part and no vanes. Twelve types of tools are available. These install into heads using one bolt.
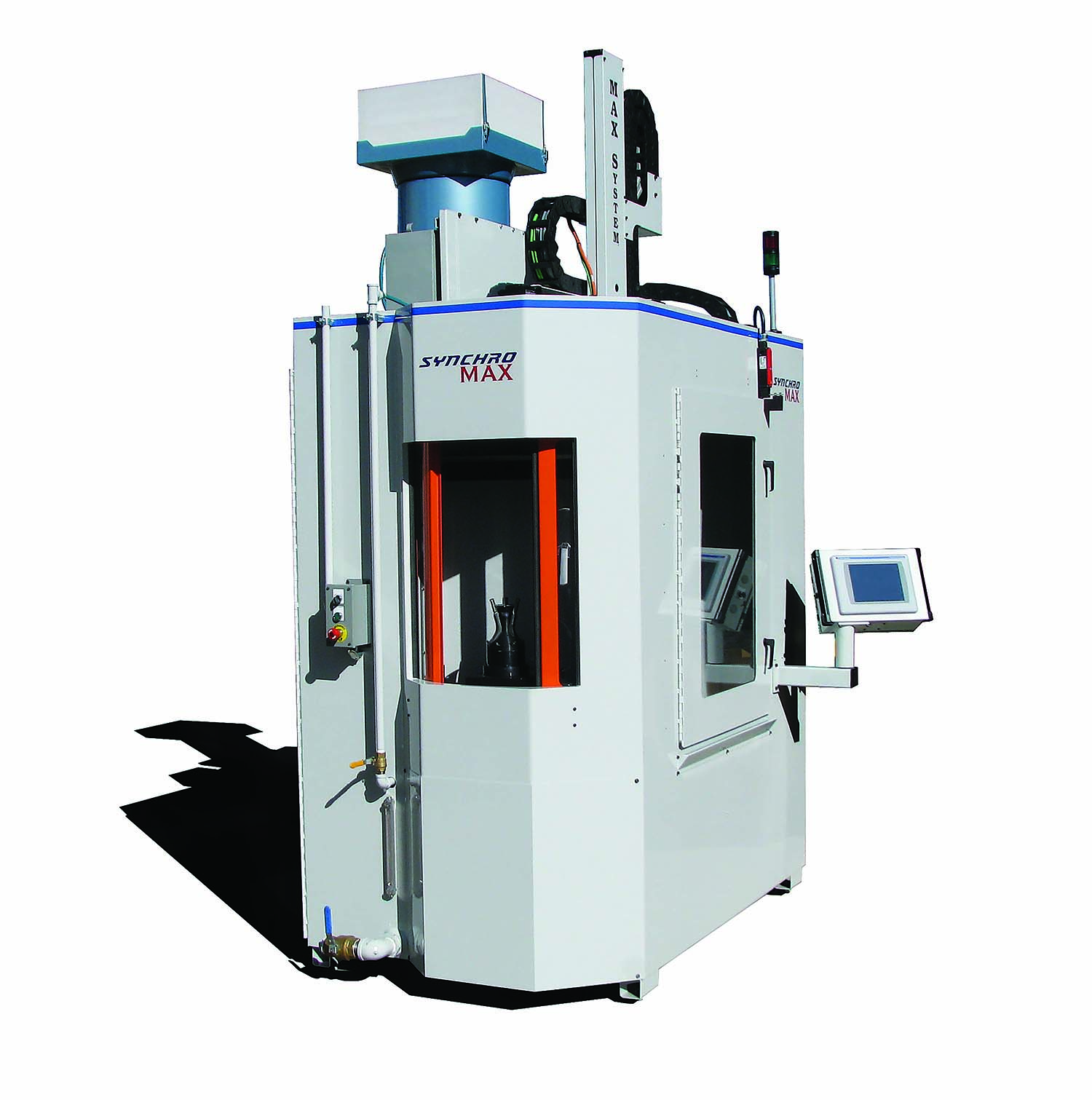
The heart of this process is the compliant technology, which he likens to the front suspension of a car. Using pneumatics and a damping agent enables a tool to maintain a constant force on a part as the tool follows the contour of the features ahead of it to be finished. This means that no change to a programmed toolpath is required to adjust for a perishable tool, such as a brush that might start at 1.25" in diameter and be reduced to 0.75" over its life. (Another compliant technology analogy is the way that a record player needle follows the grooves in an album.) This also simplifies programming and setup.
Programming any deburring system is part manual teach-in and part conversational at the machine’s control. No 3D model of the part is needed. Because of the compliant technology, a tool, such as a brush, does not have to be positioned as precisely as, say, a cutting tool on a milling machine would. An operator would capture the brush’s initial x/y/z coordinates, jog it to the part and record that position — commonly the midpoint of the tool’s range of compliant travel. This is performed for all tools and operations. Values like feed rate and compliant force also are entered — these vary depending on burr size, chamfer accuracy and more — and fine-tuning of tool positions can be performed as well if necessary. Programming Richards’ Max System, for example, is made easier with the machine’s Mitsubishi control.
He said the best programmer at a machine shop is likely the person who has been hand deburring for many years and knows precisely what angle a tool needs to approach a part. The control can store as many as 100 part programs, and programs can be added and removed from a USB as well. James Engineering refers to these as recipes to distinguish them from the operating system running in the background. Individual operations can be chained together much like a word processor’s copy and paste function to further speed programming. Plus, the chosen operations enable what the company calls focused deburring so only the part features requiring such finishing operations are touched.
Why Not a Robot?
Aside from its programming complexities, a robot is a series of joints that always are wearing. They are often harmonic or elliptical gearboxes, and having five to seven of those stacked upon each other creates an issue with tolerance. As the gearboxes wear, they gain slop, also known as losing accuracy. It’s common to have to frequently recalibrate a robot to deal with the slop in the joints, especially with heavier payloads.
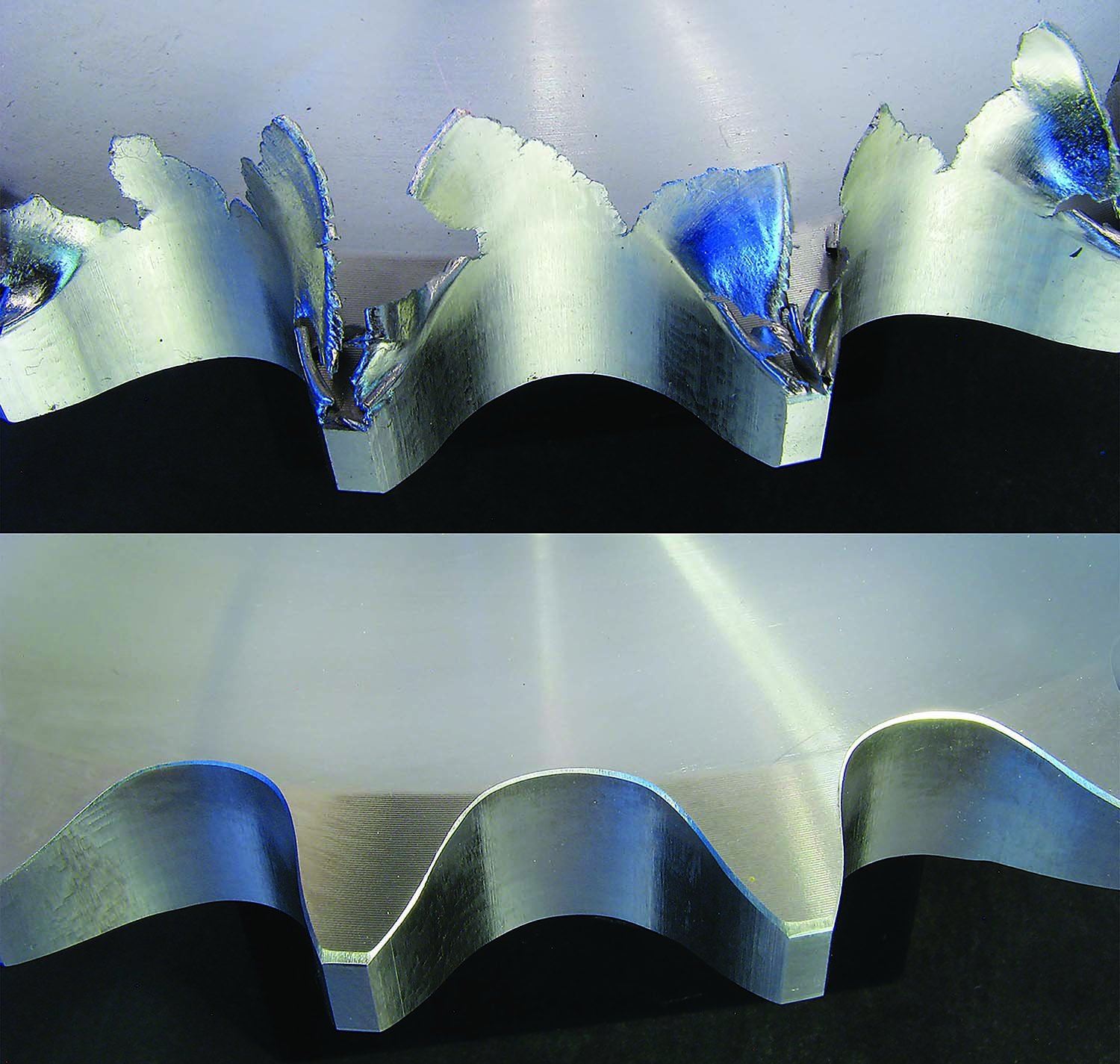
Robots are very sensitive to the weight on the end of the arm as well, so if the robot changes tooling, then the weight of that tooling must be considered and compensated for — if the weight is within the acceptable range of the robot in the first place.
Additionally, robots do not like water. Mix abrasive into the water, and a robot is in big trouble.
Compared with a robot, deburring systems can be incredibly easy to program. Many basic gear programs are created in just a few minutes. Even someone new to deburring systems can be taught in about 10 minutes.
Deburring systems, such as the Max System, are also much more rigid than a robot. The Max System can handle payloads from 2 to 200 lbs., so its processes are extremely repeatable and robust.
Why Not Chamfer Generation Machines?
These types of machines create bruising, swelling and mounding due to the impact of the rotating cutter against the gear surface. Bruising and swelling are common side effects of chamfer generation machines and will increase as the cutters wear out, and secondary burrs will increase as the cutters wear out. The most important takeaway here is that chamfer generation is a diminishing process: The cutter always is wearing out, part after part.
That’s why grinding wheels and brushes are used. These kinds of media renew constantly. With each revolution and each granule removed, a new, fresh cutting surface is revealed. This constant renewing means that the results are always the same, part after part.
For more information about the Max System, view a video presentation at https://qr.ctemag.com/1j22z
James Engineering is based in Broomfield, Colorado. For more information, call 303-444-6787 or visit www.james-engineering.com.
Contact Details
Related Glossary Terms
- abrasive
abrasive
Substance used for grinding, honing, lapping, superfinishing and polishing. Examples include garnet, emery, corundum, silicon carbide, cubic boron nitride and diamond in various grit sizes.
- burr
burr
Stringy portions of material formed on workpiece edges during machining. Often sharp. Can be removed with hand files, abrasive wheels or belts, wire wheels, abrasive-fiber brushes, waterjet equipment or other methods.
- chamfering
chamfering
Machining a bevel on a workpiece or tool; improves a tool’s entrance into the cut.
- computer numerical control ( CNC)
computer numerical control ( CNC)
Microprocessor-based controller dedicated to a machine tool that permits the creation or modification of parts. Programmed numerical control activates the machine’s servos and spindle drives and controls the various machining operations. See DNC, direct numerical control; NC, numerical control.
- coolant
coolant
Fluid that reduces temperature buildup at the tool/workpiece interface during machining. Normally takes the form of a liquid such as soluble or chemical mixtures (semisynthetic, synthetic) but can be pressurized air or other gas. Because of water’s ability to absorb great quantities of heat, it is widely used as a coolant and vehicle for various cutting compounds, with the water-to-compound ratio varying with the machining task. See cutting fluid; semisynthetic cutting fluid; soluble-oil cutting fluid; synthetic cutting fluid.
- feed
feed
Rate of change of position of the tool as a whole, relative to the workpiece while cutting.
- gang cutting ( milling)
gang cutting ( milling)
Machining with several cutters mounted on a single arbor, generally for simultaneous cutting.
- grinding
grinding
Machining operation in which material is removed from the workpiece by a powered abrasive wheel, stone, belt, paste, sheet, compound, slurry, etc. Takes various forms: surface grinding (creates flat and/or squared surfaces); cylindrical grinding (for external cylindrical and tapered shapes, fillets, undercuts, etc.); centerless grinding; chamfering; thread and form grinding; tool and cutter grinding; offhand grinding; lapping and polishing (grinding with extremely fine grits to create ultrasmooth surfaces); honing; and disc grinding.
- inches per minute ( ipm)
inches per minute ( ipm)
Value that refers to how far the workpiece or cutter advances linearly in 1 minute, defined as: ipm = ipt 5 number of effective teeth 5 rpm. Also known as the table feed or machine feed.
- machining center
machining center
CNC machine tool capable of drilling, reaming, tapping, milling and boring. Normally comes with an automatic toolchanger. See automatic toolchanger.
- milling
milling
Machining operation in which metal or other material is removed by applying power to a rotating cutter. In vertical milling, the cutting tool is mounted vertically on the spindle. In horizontal milling, the cutting tool is mounted horizontally, either directly on the spindle or on an arbor. Horizontal milling is further broken down into conventional milling, where the cutter rotates opposite the direction of feed, or “up” into the workpiece; and climb milling, where the cutter rotates in the direction of feed, or “down” into the workpiece. Milling operations include plane or surface milling, endmilling, facemilling, angle milling, form milling and profiling.
- milling machine ( mill)
milling machine ( mill)
Runs endmills and arbor-mounted milling cutters. Features include a head with a spindle that drives the cutters; a column, knee and table that provide motion in the three Cartesian axes; and a base that supports the components and houses the cutting-fluid pump and reservoir. The work is mounted on the table and fed into the rotating cutter or endmill to accomplish the milling steps; vertical milling machines also feed endmills into the work by means of a spindle-mounted quill. Models range from small manual machines to big bed-type and duplex mills. All take one of three basic forms: vertical, horizontal or convertible horizontal/vertical. Vertical machines may be knee-type (the table is mounted on a knee that can be elevated) or bed-type (the table is securely supported and only moves horizontally). In general, horizontal machines are bigger and more powerful, while vertical machines are lighter but more versatile and easier to set up and operate.
- swarf
swarf
Metal fines and grinding wheel particles generated during grinding.
- tolerance
tolerance
Minimum and maximum amount a workpiece dimension is allowed to vary from a set standard and still be acceptable.
- toolpath( cutter path)
toolpath( cutter path)
2-D or 3-D path generated by program code or a CAM system and followed by tool when machining a part.