By Thomas Namola and Jeremiah Wolf
The use of single-layer diamond tools on various composite types has been practiced for decades. Most grades of fiberglass, carbon-fiber-reinforced plastics and even ceramic matrix composites can be cut and shaped with these tools. There are varied tool design characteristics and operating conditions under which natural-fiber-reinforced composite material can be processed successfully.
Single-layer diamond grinding wheels consist of three components: the core (often called the blank), the bond matrix and diamond mesh. The core, usually made from steel, establishes the form and mounting configuration for use. The bond matrix attaches the diamond to the core. The two most common bonding methods are nickel entrapment and brazing. Both can be used for this application.
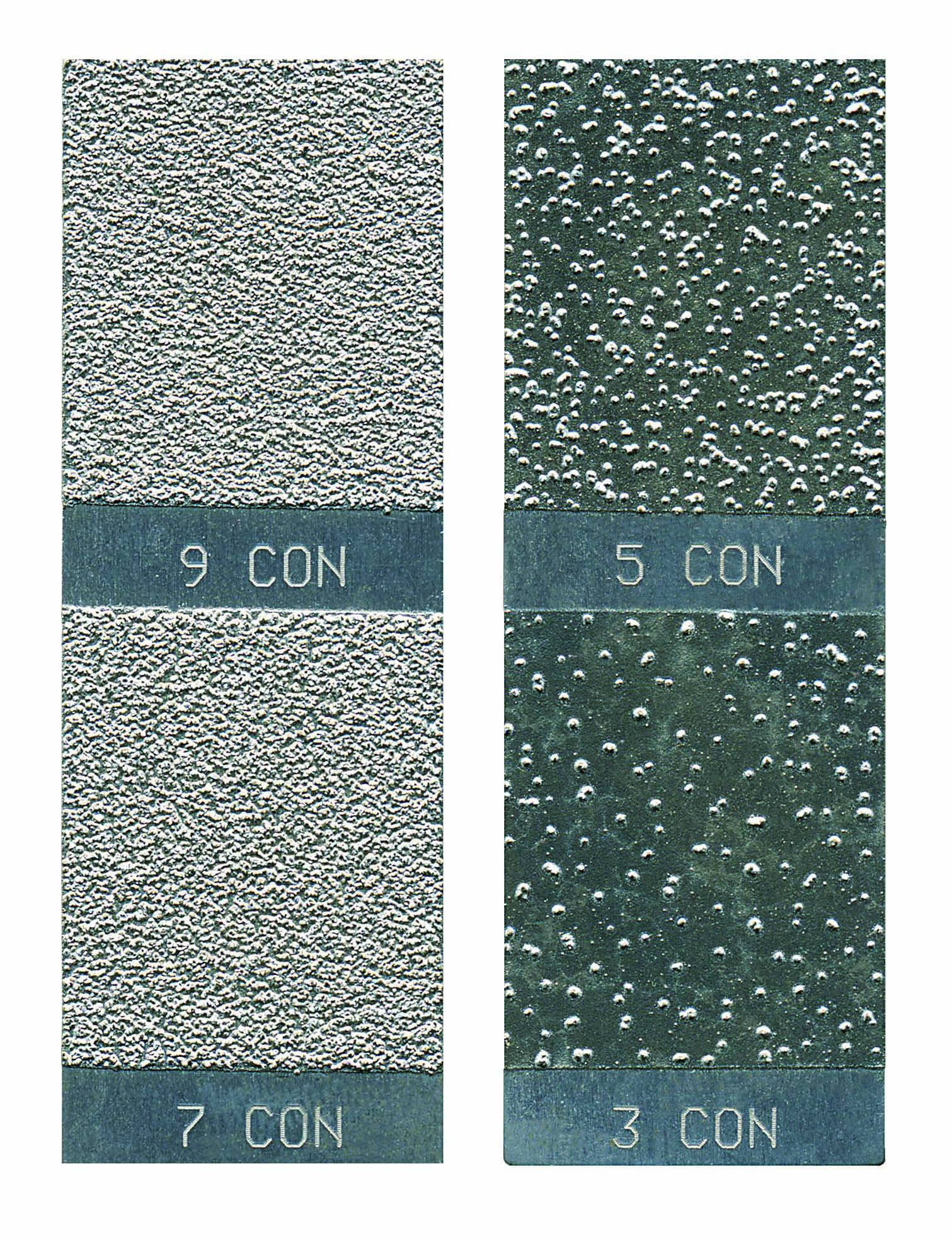
The main challenge when using single-layer diamond tools on natural-fiber-reinforced composite material is short tool life due to tool loading. All applications that will be discussed here will involve dry grinding — no coolant or cold air. Tool loading can be reduced by using coolant. However, many applications with this material are performed dry. The need for the process to be dry may be driven by the equipment, the desire to avoid potential material contamination and/or the wish to avoid post-process part cleaning.
Edged carbide and polycrystalline diamond tools, which commonly are used in these materials, are more resistant to loading than standard single-layer diamond tools with these materials. The end of life for carbide/PCD occurs with edge dulling, which leads to part chipping. This chipping might cause rejected parts and often forces a manufacturer to leave excessive material to avoid entirely scrapping a part. Single-layer diamond tools reach the ends of their lives from burr/fuzz generation due to tool loading. Burrs easily can be removed from the parts, reducing rejects. The cost of a single-layer diamond tool likely will be higher than a carbide alternative, but that increase in cost can be outweighed by the reduction in scrap, along with increased tool life.
Four features of a single-layer wheel design affect tool loading: the abrasive bonding system, the abrasive particle size, the abrasive shape and the abrasive concentration (surface coverage).
Because loading is a life-limiting issue, tool design needs to be tailored for the material to be cut. To make the single-layer diamond tool more free cutting, the amount of diamond grain exposure can be increased while reducing the
abrasive concentration. Both design changes allow grinding swarf and heat to escape the cut zone more easily, which is critical when working with relatively soft materials without coolant. Using a brazed bond provides the ability to further reduce the bond level without compromising the strength of the bond (entrapment of the diamond particle). It has been found that a 30% entrapment level is sufficient to hold the diamond grains in place with a brazed bond while a minimum of 40% entrapment is required with a plated bond to ensure diamond grain retention. Both bond systems have been used successfully, but the braze system enables better control over abrasive concentration due to manufacturing methods. The plated system can provide better dimensional tolerance if required.
With natural-fiber-reinforced composites, a larger diamond yields longer tool life with single-layer tools. However, other considerations may limit diamond size. Surface finish requirements, fit/edge needs and feature size all can limit diamond size. Diamond size ranges are 20/25 mesh through 40/50 mesh for saw cutting and roughing operations and 40/50 mesh through 120/140 mesh for finishing.
Diamond grains are available in a wide variety of shapes. They can be cubes, which are referred to as blocky, or they can be long, narrow shards referred to as nonblocky. Along with the shape, the toughness (resistance to fracture) of the diamond is a consideration. It is best to use a diamond with good cutting efficiency; thus, we want sharp edges. This is balanced by not wanting a diamond that fractures too easily as tool life will be reduced. Therefore, a semiblocky diamond with a medium/low friability (toughness rating) would be selected.
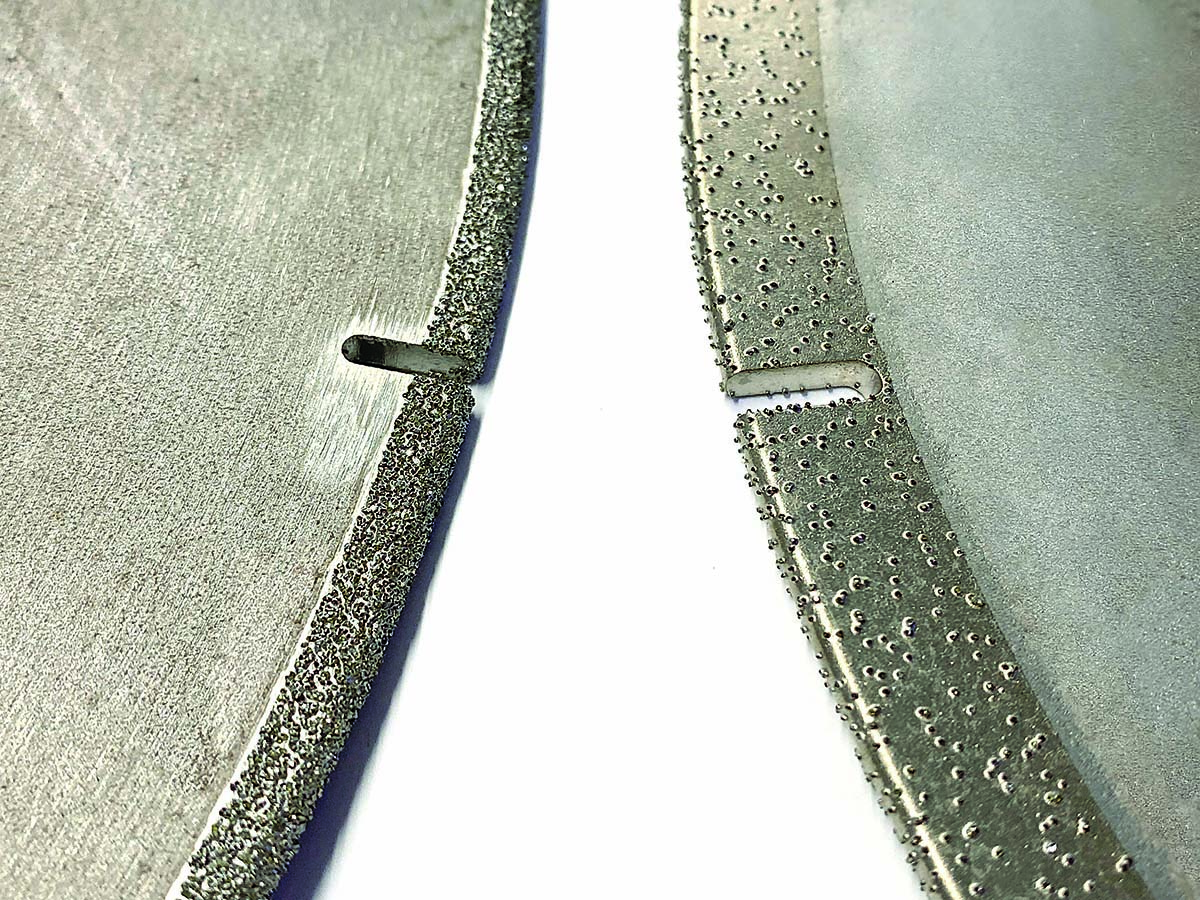
By design, a single-layer wheel has only one layer of diamond to wear during use, so the amount of diamond on the surface of the tool is a large driver of tool life. When loading occurs before appreciable diamond wear, the loading must be eliminated to gain tool life.
Wheel periphery speed is a factor in loading. A slow wheel speed of below 4,000 sfm can cause loading as each abrasive grain is taking too large a bite. If the wheel speed is higher, then the specific energy is also higher. Loading will happen when nearing the melting/transition temperature of the material being ground. Tests have shown that melting/burning takes place immediately at 18,000 sfm in a wood-fiber-filled thermoplastic.
Reducing the diamond concentration on the tool is a way to mitigate these competing forces. The sweet spot for diamond concentration on the tool will depend on the properties of the material being cut and the processing speeds available. We have found the ideal concentration to be between 30% and 70% of the standard full diamond coverage.
Two versions of a single-layer brazed diamond saw were tested against a PCD-tipped saw in a cutoff application. The material was a wood-fiber-filled thermoplastic. The blades were all 18" dia., the saw ran at a fixed 1,750 rpm (8,247 sfm), and the feed rate was approximately 200 ipm. The diamond saws were brazed bonded 20/25 mesh abrasive, and the PCD saw baseline was 40,000 cuts. The standard-concentration diamond completed about 20,000 cuts, so it was not economically feasible. A second saw blade with the diamond coverage adjusted to 40% concentration made 220,000 cuts. (See the second photo.) This reduced the tooling cost per cut. The reduced-concentration diamond saw also cut more accurately and left a better edge. This generated additional savings as the cut length was reduced closer to the final specification, generating less waste material.
In another testing example, cut-to-length operations were performed with a 14", 40/50 mesh, 50% concentration saw. This was a drop-in replacement for a PCD saw. Throughput was improved as reject parts were reduced by improved cut edge quality.
The reduced abrasive concentration can be applied to complex wheel shapes as well. A precisely machined wheel core can be used to profile an edge, potentially replacing a carbide cutter stack or multiple milling operations. An example using wheels instead of saws showed that tool life and part finish were improved over the baseline. A formed carbide cutter stack was replaced with a 40/50 mesh, 40% diamond concentration tool. This tool ran at over a 17,000 sfm wheel speed, a 1" maximum depth of cut and a 50 ipm feed rate. The initial single-layer tool was made with 50% concentration, and the tool started to burn the material when there was still adequate diamond exposure. Reducing the diamond concentration to 40% delayed the burn response, giving better tool life.
In conclusion, single-layer diamond tools can be used effectively in natural-fiber-reinforced composite material. The keys are selecting the largest diamond size that the application will allow and then tuning the diamond concentration based on the material properties and the application parameters.
About the authors: Thomas Namola and Jeremiah Wolf are product development and applications engineers at Abrasive Technology LLC. For more information, call 740-548-4100 or visit www.abrasive-tech.com.
Contact Details
Related Glossary Terms
- abrasive
abrasive
Substance used for grinding, honing, lapping, superfinishing and polishing. Examples include garnet, emery, corundum, silicon carbide, cubic boron nitride and diamond in various grit sizes.
- composites
composites
Materials composed of different elements, with one element normally embedded in another, held together by a compatible binder.
- coolant
coolant
Fluid that reduces temperature buildup at the tool/workpiece interface during machining. Normally takes the form of a liquid such as soluble or chemical mixtures (semisynthetic, synthetic) but can be pressurized air or other gas. Because of water’s ability to absorb great quantities of heat, it is widely used as a coolant and vehicle for various cutting compounds, with the water-to-compound ratio varying with the machining task. See cutting fluid; semisynthetic cutting fluid; soluble-oil cutting fluid; synthetic cutting fluid.
- cutoff
cutoff
Step that prepares a slug, blank or other workpiece for machining or other processing by separating it from the original stock. Performed on lathes, chucking machines, automatic screw machines and other turning machines. Also performed on milling machines, machining centers with slitting saws and sawing machines with cold (circular) saws, hacksaws, bandsaws or abrasive cutoff saws. See saw, sawing machine; turning.
- depth of cut
depth of cut
Distance between the bottom of the cut and the uncut surface of the workpiece, measured in a direction at right angles to the machined surface of the workpiece.
- feed
feed
Rate of change of position of the tool as a whole, relative to the workpiece while cutting.
- friability
friability
Characteristic of abrasive grains that describes their tendency to fracture or break apart when hit or placed under pressure. Highly friable abrasives cut more easily, but wear faster than other abrasives. Friable abrasives are usually used on soft, gummy materials or where heat produced by worn grits must be carefully controlled. Friability is usually related to the levels of impurities in the manufactured abrasive mineral.
- gang cutting ( milling)
gang cutting ( milling)
Machining with several cutters mounted on a single arbor, generally for simultaneous cutting.
- grinding
grinding
Machining operation in which material is removed from the workpiece by a powered abrasive wheel, stone, belt, paste, sheet, compound, slurry, etc. Takes various forms: surface grinding (creates flat and/or squared surfaces); cylindrical grinding (for external cylindrical and tapered shapes, fillets, undercuts, etc.); centerless grinding; chamfering; thread and form grinding; tool and cutter grinding; offhand grinding; lapping and polishing (grinding with extremely fine grits to create ultrasmooth surfaces); honing; and disc grinding.
- inches per minute ( ipm)
inches per minute ( ipm)
Value that refers to how far the workpiece or cutter advances linearly in 1 minute, defined as: ipm = ipt 5 number of effective teeth 5 rpm. Also known as the table feed or machine feed.
- milling
milling
Machining operation in which metal or other material is removed by applying power to a rotating cutter. In vertical milling, the cutting tool is mounted vertically on the spindle. In horizontal milling, the cutting tool is mounted horizontally, either directly on the spindle or on an arbor. Horizontal milling is further broken down into conventional milling, where the cutter rotates opposite the direction of feed, or “up” into the workpiece; and climb milling, where the cutter rotates in the direction of feed, or “down” into the workpiece. Milling operations include plane or surface milling, endmilling, facemilling, angle milling, form milling and profiling.
- polycrystalline diamond ( PCD)
polycrystalline diamond ( PCD)
Cutting tool material consisting of natural or synthetic diamond crystals bonded together under high pressure at elevated temperatures. PCD is available as a tip brazed to a carbide insert carrier. Used for machining nonferrous alloys and nonmetallic materials at high cutting speeds.
- polycrystalline diamond ( PCD)2
polycrystalline diamond ( PCD)
Cutting tool material consisting of natural or synthetic diamond crystals bonded together under high pressure at elevated temperatures. PCD is available as a tip brazed to a carbide insert carrier. Used for machining nonferrous alloys and nonmetallic materials at high cutting speeds.
- sawing machine ( saw)
sawing machine ( saw)
Machine designed to use a serrated-tooth blade to cut metal or other material. Comes in a wide variety of styles but takes one of four basic forms: hacksaw (a simple, rugged machine that uses a reciprocating motion to part metal or other material); cold or circular saw (powers a circular blade that cuts structural materials); bandsaw (runs an endless band; the two basic types are cutoff and contour band machines, which cut intricate contours and shapes); and abrasive cutoff saw (similar in appearance to the cold saw, but uses an abrasive disc that rotates at high speeds rather than a blade with serrated teeth).
- swarf
swarf
Metal fines and grinding wheel particles generated during grinding.
- tolerance
tolerance
Minimum and maximum amount a workpiece dimension is allowed to vary from a set standard and still be acceptable.