Saint-Gobain Abrasives has released the newest generation of Norton Abrasive's Paradigm wheels for the cutting tool market. Norton's Paradigm Plus features a new high-performance grain, combined with the current Paradigm bond technology, for higher material removal rates, improved wheel life, better finishes, and reduced overall cost per part.
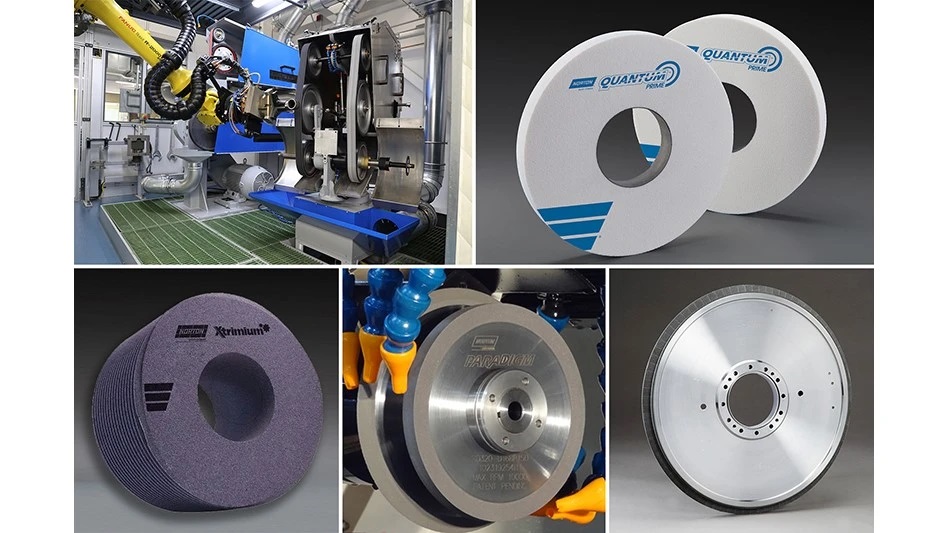
At the recent IMTS 2024 show, Norton Abrasive, a brand of Saint Gobain, showcased its Paradigm Plus diamond grinding and GForce Plus wheels that featured new premium grain technology that Alfredo Barragan, senior application engineer at Norton, said results in a significant upgrade in performance on carbide round tools for fluting and gashing applications, and periphery grinding on carbide, cermet and ceramic inserts grinding.
The new grain technology, together with a new advanced lightweight core, produces lower specific cutting energy with a 25% to 50% higher material removal rate (MRR), and provides significantly improved wheel life when compared with previous generation wheels.
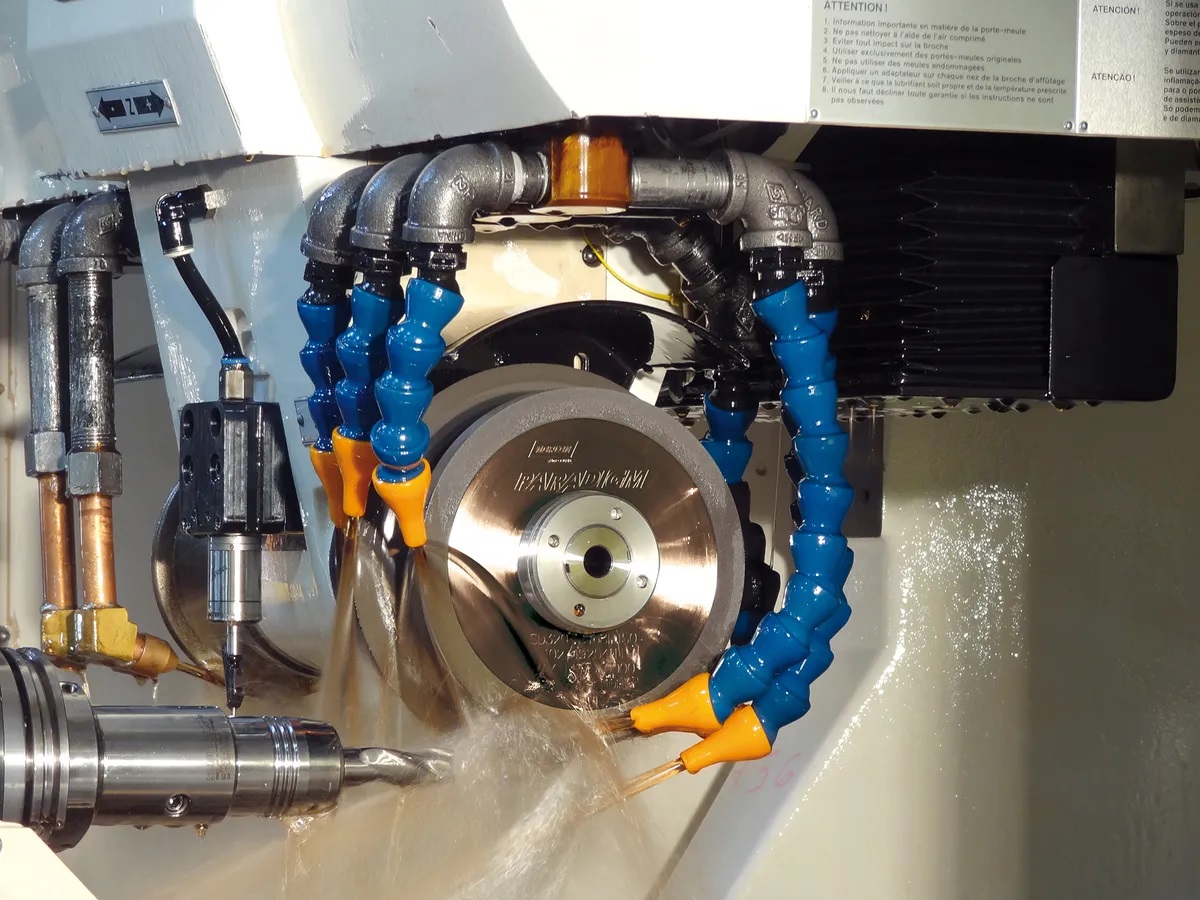
"You can achieve higher material removal rates," he said. "It reduces specific grinding forces, huge gains in productivity, and you can reduce cycle time with the same or better [grinding wheel] life."
The wheels' new grain technology results in lower normal forces and higher performance, which is complemented by an improved hybrid bond technology providing significant improvement ranging from a 25% to 50% increased MRR, and longer wheel life when compared with current G-Force wheels, said Barragan.
New G-Force Plus Wheels offer higher feed rates and reduced cycle times, resulting in more parts per dress and reduced process costs. Improved edge holding, better part quality and surface finish are all key benefits of the new wheels. G-Force Plus Wheels provide cooler cutting when grinding a range of heat- and wear-resistant materials.
One reason that it achieves these improved is the lightweight core that is "no longer made of steel," said Barragan. "Before that, [the core] was made with steel that was really heavy and it tended to put a huge stress on the machine spindle. Usually, it's 50 % or lower [in weight] compared to steel. By going lighter, you definitely have better surface finish, and more vibration dampening, so it's another win-win for the wheel, for the machine.
Get fast solutions to machining challenges
Challenging grinding and machining operations increasingly require custom solutions, and Norton Abrasives said that it has a solution that it calls the abrasive process solutions (APS) program.
According to the company, APS provides custom grinding expertise by helping customers determine the most optimal grinding or finishing solutions for the application at hand, for metal fabrication, for production grinding, or for virtually any abrasives operation.
The APS program draws on the knowledge of the Norton team along with access to 30 different machines, and a state-of-the-art APS robotic automation cell, which is at the core of the new APS program located at the Higgins Grinding Technology Center in Northborough, Massachusetts.
The APS team provides abrasive process development, optimization, automation, and in-house testing. APS services encompass the testing and optimization of new abrasives, improving quality and/ or throughput, and exploring new and customized processes.
Contact Details
Related Glossary Terms
- abrasive
abrasive
Substance used for grinding, honing, lapping, superfinishing and polishing. Examples include garnet, emery, corundum, silicon carbide, cubic boron nitride and diamond in various grit sizes.
- feed
feed
Rate of change of position of the tool as a whole, relative to the workpiece while cutting.
- fluting
fluting
Cutting straight or spiral grooves in drills, endmills, reamers and taps to improve cutting action and remove chips.
- grinding
grinding
Machining operation in which material is removed from the workpiece by a powered abrasive wheel, stone, belt, paste, sheet, compound, slurry, etc. Takes various forms: surface grinding (creates flat and/or squared surfaces); cylindrical grinding (for external cylindrical and tapered shapes, fillets, undercuts, etc.); centerless grinding; chamfering; thread and form grinding; tool and cutter grinding; offhand grinding; lapping and polishing (grinding with extremely fine grits to create ultrasmooth surfaces); honing; and disc grinding.