Hard chrome plating (HCP) is the industry standard for coating parts that operate in demanding environments, such as cylinders and pistons. That coating, however, has downsides, according to James Oldroyd, managing director at Apex Hydraulics Ltd., which specializes in meeting the hydraulic requirements of the oil and gas industry.
For one, the HCP process produces hexavalent chromium, or Cr(VI), as a byproduct. As a known carcinogen, hexavalent chromium targets the respiratory system, kidneys, liver, skin and eyes. “It’s estimated that 558,000 workers are potentially exposed to Cr(VI) in the United States alone,” Oldroyd said.
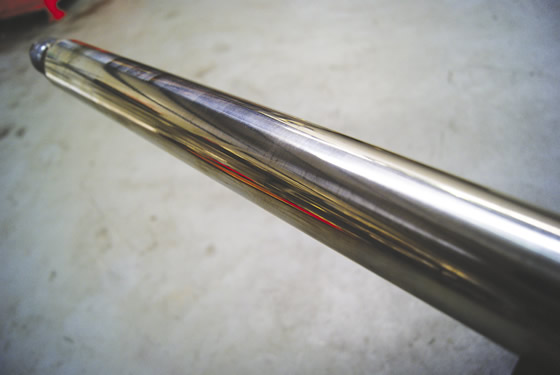
A part coated with the Corex tungsten-chromium-carbide compound from Apex Hydraulics.
In addition, HCP porosity is 5 to 10 percent, and HCP experiences microcracking in all circumstances, with the amount varying based on the manufacturer, according to Oldroyd. As an alternative, Apex Hydraulics introduced the Corex tungsten-chromium-carbide compound after 2 years of R&D. Oldroyd pointed out that the dense, cohesive rod coating has a porosity of less than 1 percent, a hardness up to 1,400 HV, a bond strength greater than 10,000 psi and doesn’t experience microcracking. In comparison, HCP has a hardness of 750 to 850 HV and a bond strength of less than 5,000 psi.
“Hard chrome plating offers good all-round performance,” he said. “But where improvements are needed, Corex is the superior solution.”
Those applications include mechanical components in the hydraulic industry, because they suffer extreme abrasive wear and corrosion under high environmental pressures and long, continuous usage. The coating thickness is from 0.004 " to 0.012 " (0.102mm to 0.305mm), and Corex increases cylinder life, durability, efficiency and performance, according to the company. Therefore, the coating enables machinery to cope with low-lubricity fluids.
Oldroyd added that Corex-coated cylinders can run on pure water, and the coating’s hardness resists high levels of contamination. “Contamination will always reduce the life of any cylinder, but the cause of failure can be moved from an expensive rod to [lower-cost] soft parts,” he said, noting any metal can be coated. “We also upgrade other components with the coating, creating big gains in applications where contact with contaminated fluid is unavoidable.”
For more information about Apex Hydraulics Ltd., Leeds, England, call +44 776-681-8714 or visit www.apex hydraulics.co.uk. CTE
Related Glossary Terms
- Vickers hardness number ( HV)
Vickers hardness number ( HV)
Number related to the applied load and surface area of the permanent impression made by a square-based pyramidal diamond indenter having included face angles of 136º. The Vickers hardness number is a ratio of the applied load in kgf, multiplied by 1.8544, and divided by the length of diagonal squared.
- abrasive
abrasive
Substance used for grinding, honing, lapping, superfinishing and polishing. Examples include garnet, emery, corundum, silicon carbide, cubic boron nitride and diamond in various grit sizes.
- hardness
hardness
Hardness is a measure of the resistance of a material to surface indentation or abrasion. There is no absolute scale for hardness. In order to express hardness quantitatively, each type of test has its own scale, which defines hardness. Indentation hardness obtained through static methods is measured by Brinell, Rockwell, Vickers and Knoop tests. Hardness without indentation is measured by a dynamic method, known as the Scleroscope test.