Along with the rise of automated guided vehicles (AGVs) on the shop floor come new systems to keep your employees safe while walking the same floor as these mobile robots. Let’s take a closer look at two such systems.
SICK Inc., Minneapolis, Minnesota, offers the safeVisionary2, a new compact 3D time-of-flight camera system with a Performance Level of “c” (PL c), which is an indication of the system’s safety related parts of the control system to perform a safety function under foreseeable conditions.
A comprehensive package for safeguarding AGV systems offered by Pilz Automation Safety L.P., Canton, Michigan. The package includes safe area monitoring that protects against collisions between employees and AGVs.
SICK
The safeVisionary2 is said to be effective for use on autonomous mobile robots because the camera provides precise 3D measurement data that enables AGV navigation. The 3D environment detection enables seamless protection of numerous applications requiring PL c, according to SICK. With a 2 m safety range and up to four field switching cases, the safeVisionary2 is suitable for a wide range of applications, including industrial mobile robots, cobots and mobile service robots.
With safeVisionary2, obstacles above the scanning field level of a safety laser scanner are also reliably detected in the direction of travel, which translates into improved collision avoidance. In addition, the company said side protection safety is also increased during turning and pivoting maneuvers of the vehicle after loading and unloading processes.
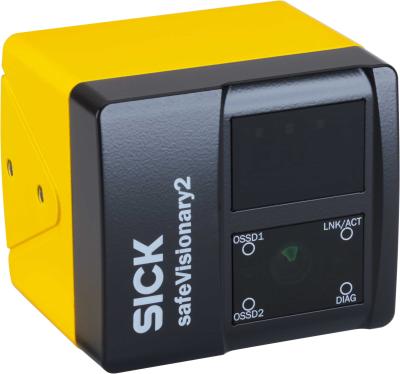
In the world of cobots, the spectrum of human-motion sequences is a particular challenge for safety, SICK noted. The safe 3D environment detection with safeVisionary2 reliably detects a person’s upper body and upper limbs. In many cases, safety distances can be reduced around the cobot.
The safeVisionary2 extends protection of the robot work area at human-head height. So bringing a cobot to a standstill is only necessary when a person moves his or her head into the work area.
In this application scenario, further use of the sensor data is particularly suitable, as the camera performs many tasks from detecting empty pallets to object localization and measurement, according to the company. This combination of safety and automation reduces the implementation effort for additional components.
The safeVisionary2 can be configured via the SICK Safety Designer, which provides extensive diagnostic functions.
Pilz
The new Pilz safety and security package for safeguarding AGVs includes PSENscan safety laser scanners that protect against collisions between your employees and AGVs, a myPNOZ modular safety relay, a PNOZmulti 2 configurable small controller, and the industrial firewall SecurityBridge. Various control and signal devices — such as the evaluation unit from the operating mode selection and access permission system PITmode fusion, PITreader, the E-STOP pushbutton PITestop and the muting lamps PITsign — complete the monitoring package for users.
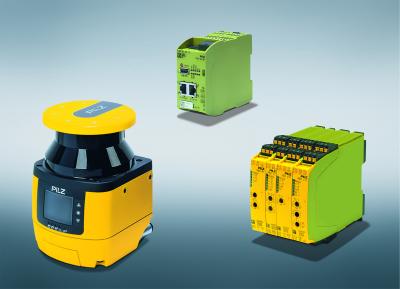
The Pilz solution also covers tamper protection on mobile applications. The integrated security solution via the firewall SecurityBridge is said to protect AGVs or vehicle systems from unauthorized access during wireless communication. As such, according to Pilz, the AGVs and their map data remain protected.
The PSENscan safety laser scanner enables safeguarding and production area monitoring of mobile platforms. On guide path AGVs, the safety laser scanner detects objects along the route, even at high speeds, and adjusts warning and safety zones in a functionally safe manner, according to Pilz.
If additional safety functions are to be covered on the AGVs, such as E-STOP for example, users can apply a flexible product solution that includes PSENscan and the modular safety relay myPNOZ. Should requirements change, myPNOZ can be expanded at will to suit any future addition to the function range. That enables a high degree of flexibility when designing mobile applications, according to Pilz.
For freely navigating mobile platforms, Pilz also offers manufacturers a comprehensive solution for the safe navigation of autonomous mobile robots (AMRs) in accordance with ISO 3691-4. The package includes the PNOZmulti 2 safe small controller with new functionalities for synchronization monitoring and activation of the PSENscan safety laser scanners. Also, the industrial firewall SecurityBridge offers protection against unauthorised access from outside.
Contact Details
Contact Details
Related Glossary Terms
- turning
turning
Workpiece is held in a chuck, mounted on a face plate or secured between centers and rotated while a cutting tool, normally a single-point tool, is fed into it along its periphery or across its end or face. Takes the form of straight turning (cutting along the periphery of the workpiece); taper turning (creating a taper); step turning (turning different-size diameters on the same work); chamfering (beveling an edge or shoulder); facing (cutting on an end); turning threads (usually external but can be internal); roughing (high-volume metal removal); and finishing (final light cuts). Performed on lathes, turning centers, chucking machines, automatic screw machines and similar machines.