Stopping a machine to measure a workpiece is a waste of time. Not only is a high-priced piece of CNC equipment being taken out of production, but the measurements obtained when a machinist leans into a machine with a micrometer or bore gage can’t compare in accuracy to those generated by a coordinate measuring machine or inline probe. Yet shops do just that every day, increasing downtime and jeopardizing part quality. Fortunately, there’s a better way.
Metrology equipment providers have been busier than hummingbirds on a warm spring day, rapidly developing in- situ gaging systems that may eliminate the inspection status quo, common in many shops, of taking it to QC and waiting for someone to check it. Not only do these new systems reduce the cost of inspection and improve machine uptime, they also open the door to unattended machining.
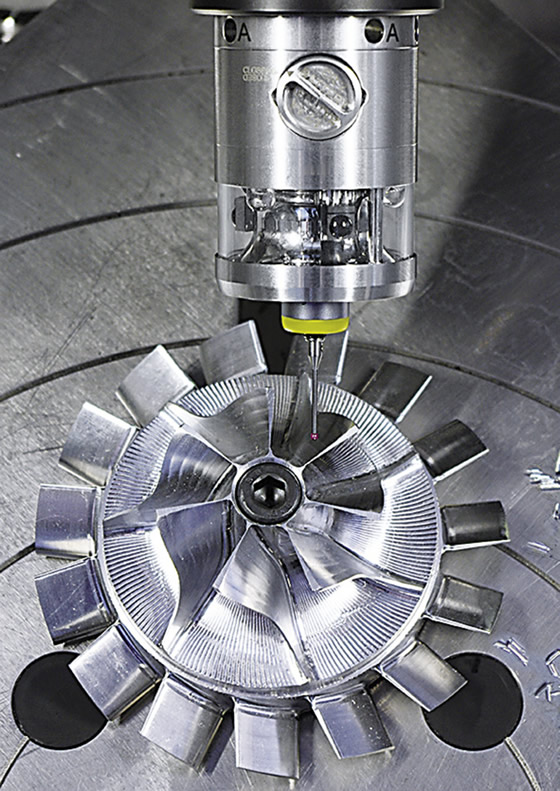
Courtesy of Hexagon Metrology
This Hexagon Metrology system supports probe styli as small as 0.2mm (0.008 ") in diameter.
There’s more to this than uptime, however. As part tolerances grow tighter and geometries become increasingly complex, pulling a part out of the machine for measurement makes about as much sense as giving U.S. politicians more paid vacation. When the CMM indicates a bore is undersize by a few tenths, what are the chances of positioning that part in the machine accurately enough to rework it? It’s far better to have this information before the first clamp is ever loosened.
Send CMMs Packing
Machine-mounted probing has been around since the early 1980s. Aimed primarily at setup time reduction and broken tool detection, these devices have evolved into systems as accurate and repeatable as top-caliber machine tools, making it possible to measure a large percentage of part features and all but the tightest part tolerances without ever setting foot in the inspection room.
Intelligence is just as important as accuracy. Adrian Johnson, in-process business manager for Hexagon Metrology Inc., North Kingstown, R.I., said the key development in today’s probing systems is the ability to do in-situ measurement of complex parts.
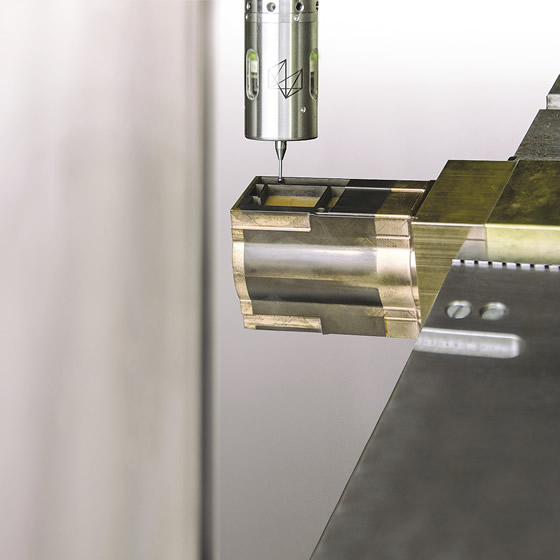
Courtesy of Hexagon Metrology
Using a CAD model, the mh40.50 from Hexagon Metrology can inspect macroscale features and those nearly invisible to the naked eye.
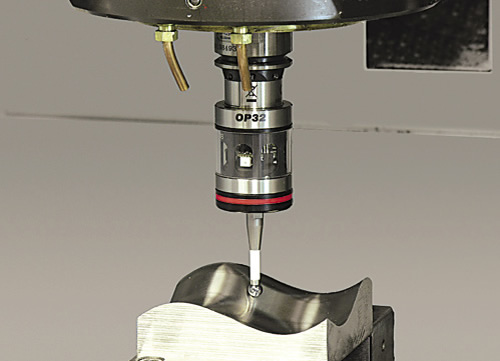
Courtesy of Marposs
Touch probes, such as Marposs' OP32 optical transmission probe, help automate machine tools, from setup to on-machine measurement after machining.
“In the past, the primary limitation with machine probes was the CNC software driving them,” he said. “Probes could measure basic things like diameter or length, but they weren’t smart enough to do any sort of detailed dimensional analyses.”
This intelligence allows shops to measure a part, compare it to a CAD model and send real-time corrections to the machine’s CNC. Carried to its logical extreme, a new breed of self-optimizing machine tools may be on the horizon. This isn’t the prelude to some science fiction movie. Johnson said this level of intelligence is available today, giving manufacturers the potential for a cost-effective, closed-loop system able to measure features that would previously have been relegated to the inspection room.
“This is far more than a probe,” Johnson said. “It provides the ability to sense the state of the workpiece and make automatic adjustments to the machining process. Historically, you would try to control this process by inference. If you were machining titanium knee implants, for example, you would try to monitor factors such as tool wear and machine expansion by measuring three or four datum points, then using that information for process control. But if you can understand the real-time geometry of the workpiece by using a probe that’s controlled by smart software, you can catch the end effect of process errors and make adjustments accordingly.”
No Fox in the Henhouse
Some balk at the notion of inspecting parts in the same machine tool on which they were cut. If the machine is out of calibration, there’s little chance of catching potential errors without offline measurement. Sharad Mundra, Mida probing product manager at Marposs Corp., Auburn Hills, Mich., said this concern can be alleviated by using known datum points as part of the machine setup.
“By touching off on these datums—a set of precision tooling balls, for example, located on a nearby component, such as a fixture—the workpiece can be measured relative to these fixed points in space, reducing any concerns about the machine’s volumetric accuracy,” Mundra said. “Machines still require volumetric calibration at regular intervals, but the interval could be reduced by using a datum ball.”
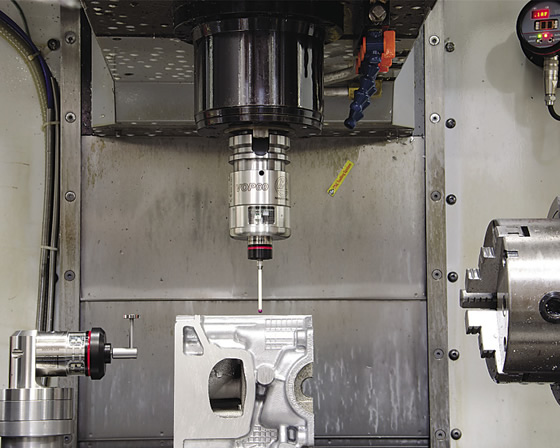
Courtesy of Marposs
Touch probes, such as Marposs’ Mida VOP, help automate machine tools, from setup to on-machine measurement after machining.
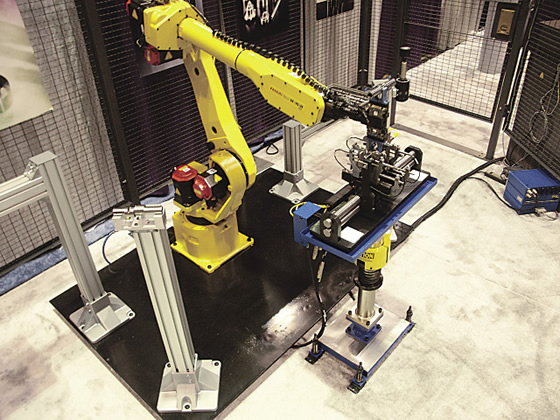
Courtesy of Marposs
A robot loading a machined shaft into a floor-mounted gage. A break-away device protects the gage in case of misalignment.
Mundra conceded that measurements can never be more accurate than the machine tool itself, but with many CNC machines boasting an accuracy of 1µm or better, most part features can be measured in process with a high degree of confidence.
Where probes have historically been used for setting workpiece home positions or measuring tool lengths, Mundra added, they are now capable of much more. Measurement of a part feature results in offset information being sent back to the machine control, or a call is made for a redundant tool once that part feature has deviated from a predefined tolerance band. And if you’re worried about writing the extensive macro programs normally required for complicated decision making such as this, don’t be. Software programs such as CAPPS NC or 3DSI are able to do the heavy lifting and readily integrate with most CAM systems, thus generating the G code needed to drive measurement probes through their paces.
CMMs are likely here to stay, but measuring parts on a machine tool, if done quickly and accurately, makes sense. Avoiding the inspection room saves time and money, and lights-out manufacturing would be all but impossible without some form of automated inspection and feedback to the machine tool. And many workpieces—especially those with tight tolerances and complex geometries—are impossible to put back in the lathe or mill for additional machining once a CMM finds them out of tolerance. Checking parts in the machine with an integrated inspection system effectively validates the machining process, monitors tool wear and gets more parts out the door each day. CTE
Need a sidekick?
Measuring parts in the machine tool isn’t the only path to integrated inspection. Metrology device supplier Renishaw Inc., Hoffman Estates, Ill., offers in-machine probing systems, yet David Chang, technical sales manager of measurement and automation products for Renishaw’s Ontario office, suggested a more conventional approach is often appropriate. The company’s Equator gaging system is, in principle at least, similar to what Marposs’ Sharad Mundra suggested on comparative measurement on CNC machines.
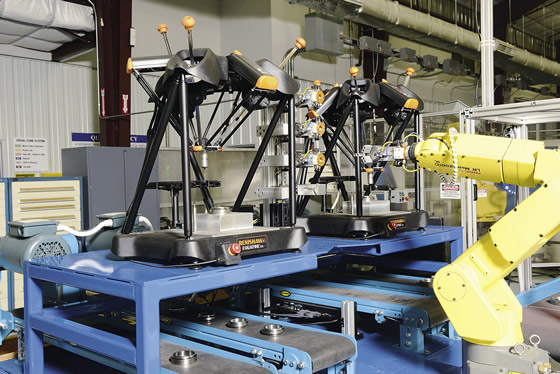
Courtesy of Renishaw
A single robot tends a set of conveyors, loading and unloading workpieces on a pair of Equator measuring machines from Renishaw.
“The Equator is an alternative gaging system for the shop floor,” Chang said. “The fundamental difference between it and a coordinate measuring machine is that the Equator relies on a master part with known dimensions.” The benefit is that if the temperature on the shop floor is a sweltering 90° F (32.2° C) and humid like a Louisiana bayou, a quick calibration against that same master part will bring the machine into harmony with the harsh environment. “We don’t have to rely on any sort of thermal effect compensation for accurate measurement on the shop floor,” he said.
Cool stuff, but what does any of that have to do with inline QC integration? Chang explained that the Equator can also be integrated into an automated machine cell. “Depending on how the system is configured, closed-loop integration is possible. The software can look at what part is loaded and begin the correct gaging program. If something is out of tolerance, the software will send the appropriate corrections to the machine, too.”
If you can talk to one machine, you can talk to a crowd. Chang suggested that a single Equator might play umpire for a machining cell filled with mills and lathes, each running different parts and operations. This isn’t full-blown inspection, though. It should be looked at as process control because inline gaging typically inspects one or two critical features on any given part. Still, a few basic dimensional checks can speak volumes about the overall workpiece. These measurements, coupled with intelligent software, can send feedback to a robot or to a programmable logic controller and help control the machining process.
—K. Hanson
CCD cameras bring on-machine QC to EDMs, grinders
Machine-integrated measurement is a huge step forward in mitigating some of the challenges that come with machining, according to Ken Baeszler, aerospace market segment manager for Lincolnshire, Ill.-based GF Machining Solutions LLC.
“With EDMing, as with grinding, you can build the most accurate machine tool in the world, but there are always some variables that are difficult to control down to the micron level,” he said.
GF is looking to change that, at least on its wire EDMs. The company’s Integrated Vision Unit system (IVU Advance) uses a charged-coupled device camera to examine a workpiece while it’s still in the machine tool, then compares the images to a CAD file. Based on what it sees, the system may suggest offsets or corrections to the toolpath as small as 1µm.
There are some caveats. “It is very hard to correct a part that has already been cut,” Baeszler explained. “But the system works very well if you are doing a bunch of parts or even one or two that are similar in nature. If the workpiece being measured is off by a couple microns somewhere, chances are it’s going to be off by a couple microns on every part.”
Don’t expect to see IVU Advance at the shop down the street. Most of the units sold thus far have gone to European companies. Still, Baeszler said it is available in the U.S., with a price tag “less than a CMM of comparable accuracy.”
Another machine tool builder using CCD cameras to verify in-process workpieces is Amada Machine Tools America Inc., Schaumburg, Ill. The company’s DV1 graphical profile grinder is primarily used to grind punches, but it could potentially grind other profiled parts.
Amada’s grinding sales manager, Bob Hamada, said the DV1 is an improvement over previous optical checking technologies. The company’s earlier generation of CNC optical profile grinders incorporated a large comparator directly on the machine tool. “The operators would actually look at a projected image of the punch, and use a Mylar chart to plot the shape of the punch they wanted to grind.”
By contrast, the DV1’s CCD camera, like GF’s IVU Advance, compares the workpiece profile to a DXF file. A difference between the two technologies is that Amada’s DV1 is completely automated. “The operator’s not involved at all,” Hamada said. “The machine will automatically look at a punch, set the zero points, check the wheel shape and location, and grind the punch.”
The benefit here is that the DV1 takes the punch through the entire grinding process, from roughing to finishing. When complete, the DV1 automatically inspects the form and sends edits to the part program, regrinding the workpiece as necessary. Add an optional FANUC robot and a 16-station pallet loader, and Amada’s machine offers lights-out grinding of one-offs and low-volume punches for roughly $700,000.
—K. Hanson
Stopping at the gage station
What do you do when in-machine measurement isn’t possible, but inspection is still required?
Marposs Product Manager Frank Powell said inline inspection is still a viable option. “For shops with automated cells running many different operations, you need to make sure that everything’s under control. For this reason, gage stations are often incorporated into the machining process.”
Gage stations typically contain an array of measuring devices, Powell explained. A robot or part-handling system carries the part to the station and the gages go into action, checking critical features and feeding the results to the machine tool. Of course, a CMM could be added to the machining cell, but, as Powell pointed out, fast cycle times might outpace the speed at which a CMM can measure parts.
Also, dedicated gaging tables cost less than a CMM. Powell has seen systems priced as low as $20,000, about half the price of a basic automated CMM.
“It depends on your operation,” Powell said. “If you need super-high flexibility for low-volume, high-mix work, a CMM might make more sense. But even with lot sizes of a few hundred pieces, integrated gaging tables can be very practical.”
—K. Hanson
Contributors
Amada Machine Tools America Inc.
(800) 877-4729
www.amadamt.com
GF Machining Solutions LLC
(800) 282-1336
www.gfms.com/us
Hexagon Metrology Inc.
(855) 443-9638
www.hexagonmetrology.us
Marposs Corp.
(248) 370-0404
www.marposs.com
Renishaw Inc.
(847) 286-9953
www.renishaw.com
Related Glossary Terms
- bandsaw blade ( band)
bandsaw blade ( band)
Endless band, normally with serrated teeth, that serves as the cutting tool for cutoff or contour band machines.
- calibration
calibration
Checking measuring instruments and devices against a master set to ensure that, over time, they have remained dimensionally stable and nominally accurate.
- closed-loop system
closed-loop system
CNC system in which the program output, or the distance the slide moves, is measured and compared to the program input. The system automatically adjusts the output to be the same as the input.
- computer numerical control ( CNC)
computer numerical control ( CNC)
Microprocessor-based controller dedicated to a machine tool that permits the creation or modification of parts. Programmed numerical control activates the machine’s servos and spindle drives and controls the various machining operations. See DNC, direct numerical control; NC, numerical control.
- computer-aided design ( CAD)
computer-aided design ( CAD)
Product-design functions performed with the help of computers and special software.
- computer-aided manufacturing ( CAM)
computer-aided manufacturing ( CAM)
Use of computers to control machining and manufacturing processes.
- fixture
fixture
Device, often made in-house, that holds a specific workpiece. See jig; modular fixturing.
- grinding
grinding
Machining operation in which material is removed from the workpiece by a powered abrasive wheel, stone, belt, paste, sheet, compound, slurry, etc. Takes various forms: surface grinding (creates flat and/or squared surfaces); cylindrical grinding (for external cylindrical and tapered shapes, fillets, undercuts, etc.); centerless grinding; chamfering; thread and form grinding; tool and cutter grinding; offhand grinding; lapping and polishing (grinding with extremely fine grits to create ultrasmooth surfaces); honing; and disc grinding.
- lathe
lathe
Turning machine capable of sawing, milling, grinding, gear-cutting, drilling, reaming, boring, threading, facing, chamfering, grooving, knurling, spinning, parting, necking, taper-cutting, and cam- and eccentric-cutting, as well as step- and straight-turning. Comes in a variety of forms, ranging from manual to semiautomatic to fully automatic, with major types being engine lathes, turning and contouring lathes, turret lathes and numerical-control lathes. The engine lathe consists of a headstock and spindle, tailstock, bed, carriage (complete with apron) and cross slides. Features include gear- (speed) and feed-selector levers, toolpost, compound rest, lead screw and reversing lead screw, threading dial and rapid-traverse lever. Special lathe types include through-the-spindle, camshaft and crankshaft, brake drum and rotor, spinning and gun-barrel machines. Toolroom and bench lathes are used for precision work; the former for tool-and-die work and similar tasks, the latter for small workpieces (instruments, watches), normally without a power feed. Models are typically designated according to their “swing,” or the largest-diameter workpiece that can be rotated; bed length, or the distance between centers; and horsepower generated. See turning machine.
- metrology
metrology
Science of measurement; the principles on which precision machining, quality control and inspection are based. See precision machining, measurement.
- micrometer
micrometer
A precision instrument with a spindle moved by a finely threaded screw that is used for measuring thickness and short lengths.
- micron
micron
Measure of length that is equal to one-millionth of a meter.
- milling machine ( mill)
milling machine ( mill)
Runs endmills and arbor-mounted milling cutters. Features include a head with a spindle that drives the cutters; a column, knee and table that provide motion in the three Cartesian axes; and a base that supports the components and houses the cutting-fluid pump and reservoir. The work is mounted on the table and fed into the rotating cutter or endmill to accomplish the milling steps; vertical milling machines also feed endmills into the work by means of a spindle-mounted quill. Models range from small manual machines to big bed-type and duplex mills. All take one of three basic forms: vertical, horizontal or convertible horizontal/vertical. Vertical machines may be knee-type (the table is mounted on a knee that can be elevated) or bed-type (the table is securely supported and only moves horizontally). In general, horizontal machines are bigger and more powerful, while vertical machines are lighter but more versatile and easier to set up and operate.
- numerical control ( NC)
numerical control ( NC)
Any controlled equipment that allows an operator to program its movement by entering a series of coded numbers and symbols. See CNC, computer numerical control; DNC, direct numerical control.
- process control
process control
Method of monitoring a process. Relates to electronic hardware and instrumentation used in automated process control. See in-process gaging, inspection; SPC, statistical process control.
- tolerance
tolerance
Minimum and maximum amount a workpiece dimension is allowed to vary from a set standard and still be acceptable.
- toolpath( cutter path)
toolpath( cutter path)
2-D or 3-D path generated by program code or a CAM system and followed by tool when machining a part.