Let’s face it: Everything about machine tools and their operation is expensive. If you run your own shop, then you know how much a good machining center or turning center can cost. If you ever have worked for a large company and tried to get capital for a new machine, then you know how many hoops must be jumped through to get the money. Machine tools are not only expensive to acquire but expensive to maintain, and when they go down the results can be catastrophic to budgets and customer relations.
Every minute of downtime costs a shop money, and those lost minutes and dollars never can be recovered. For machinists, engineers and maintenance personnel, excessive downtime creates a stressful work environment and unwanted overtime and generally makes for a less-than-desirable workplace. Preventing unplanned downtime is critical to successful machining operations.
Preventing unplanned downtime can be difficult in the best of times, but the shortage of skilled craftspeople and the increasing complexity of modern machine tools have added an extra layer of difficulty. However, some simple things can be done to help stave off downtime and expensive repairs.
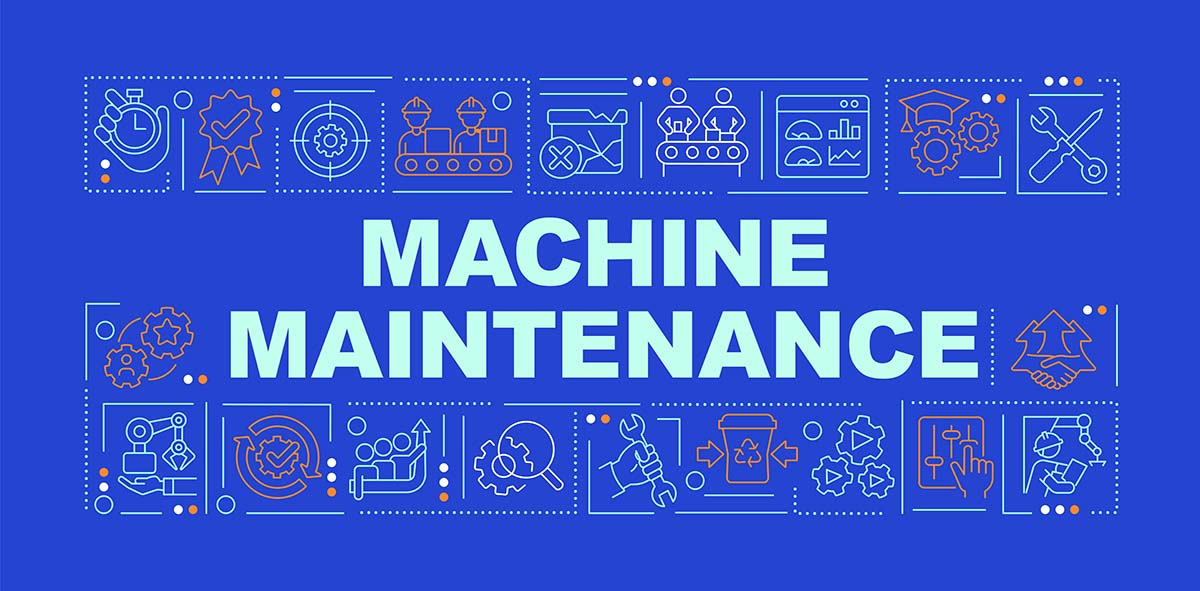
Machines are designed, built and marketed differently based on the work they are expected to perform. High-volume manufacturers like automotive companies often require very robust, heavily built machines whereas smaller shops frequently can suffice with less robust machines. Understanding the capabilities of machine tools is important when preparing the code and tooling for machines.
When I started machining, there was a heavy focus on horsepower, torque and rigidity of guide ways. CNC machines were being purchased in an attempt to automate machining processes, so engineers and machinists were transitioning traditional machining methods to CNC machines. This meant that CNC machines of the time were expected to take heavy cuts in the interest of productivity. Since early CNC machines were controlled versions of old manual
machine designs, this was not an issue.
As the market evolved, machine builders started marketing to smaller shops and lighter, more cost-effective designs appeared on the market, requiring a different approach to programming. Ensuring the longevity of machines requires programmers to adapt to the capabilities of a machine tool and prepare code that does not overburden the machine. Generating toolpaths and cutting parameters that are within the capabilities of a machine prevents premature wear and tear of critical components. Seeing that cutting parameters, such as depth of cut, rotational speed (rpm) and feed rate, are appropriate for a machine is paramount in maintaining a properly functioning machine.
Unintended misuse and abuse of machine tools at the hands of well-meaning craftspeople can significantly shorten the life expectancy of critical components. Ensuring that machine tool operators and machinists have been trained well goes a long way toward extending machine life.
Learning proper setup techniques helps prevent crashes that put undue wear and tear on spindles, servos and guide ways. Correct assembling of toolholders and cutting tools extends the life of spindles and turrets. Learning the right way to load tools into automatic toolchangers assists with eliminating toolchanger crashes. Even the most advanced machines that operate autonomously need trained personnel to keep them operating properly. Also, don’t assume that someone with experience listed on a resume knows what to do. Everyone needs to be trained to operate machines in accordance with the best practices of a company.
Large manufacturers with deep pockets and bountiful resources often implement total productive maintenance. TPM uses data and analytics, combined with the machine builder’s recommendations, to create a detailed maintenance routine focused on preventing unplanned downtime. The foundation of TPM is preventive maintenance practices that go beyond ordinary activities like fluid changes. TPM programs include replacement of major components, such as spindles when their known life spans have expired. Planning and scheduling maintenance of critical machine tools prevents disruptions to production schedules and product delivery. TPM works for big companies because unplanned downtime is far more costly than maintenance.
Although TPM is a highly effective practice, small and medium-size shops usually don’t have the resources to implement robust TPM programs. However, smaller shops can do several things to emulate TPM and promote longevity of critical components.
Just like cars, machine tools need to have fluids and filters replaced at proper intervals. Clean fluids and filters prevent premature wear and blockages of small lines and orifices. Modern machines monitor lubrication systems and will notify users when levels are low or pressures are insufficient. Unfortunately, blocked lubrication lines can go undetected in the most sophisticated machines, ultimately starving them of lubrication in critical areas.
All good machinists understand the importance of wiping down the table of a mill or cleaning the lathe chuck. Wiping chips and dirt from the toolchanger, cleaning the spindle and keeping toolholders clean are just as important. Cleaning the electrical cabinet and changing the fan filters prevent contamination of electrical components. Clearing up the outside of electric motors improves cooling airflow, which reduces operating temperatures, thereby increasing life. Keeping the toolchanger free of chips and grime prevents malfunctions and increases reliability.
Cleaning and fluid maintenance promote longevity and increase life, but they cannot stave off the inevitable. Mechanical components wear out even with the best maintenance, which is why companies implement TPM. They want to replace worn components before failure. Monitoring major components for signs of wear and degradation is not difficult and doesn’t consume large amounts of time. Small companies can do some things, such as checking runout and backlash, to better predict failure, which can help plan for repair expenses.
Checking spindle runout can be done with basic shop tools. Check the spindle at regular intervals, and log the runout. The runout data will show bearing wear over time and allow a shop to budget for repairs.
As ballscrews and couplings wear, a machine will begin to exhibit backlash. This is detected most often when the machine no longer can hold tolerances, which is usually at an inconvenient time. When a spindle is checked, it is a good idea to check the various axes for backlash. Most machine tool manuals have instructions for checking and correcting backlash. Logging and monitoring allow a shop to anticipate an oncoming failure so the work can be planned for a time that doesn’t interrupt production and deliveries.
Of course, there are other inspections and monitoring that a shop can perform to ensure longevity and prevent unplanned downtime. Machine builders, much like automakers, have routine maintenance plans for machines. Following the builder’s recommended maintenance schedule is the best place to start. Also, builders often provide a recommended parts list for inventory. Although a small shop may not be able to keep a complete list of spares, the list can be used as a predictor for components that are likely to go bad.
Maintenance and monitoring are no guarantee that a machine will not break down. However, a strong maintenance regime increases the life of components, and monitoring critical aspects will alert users of impending failures.
Related Glossary Terms
- backlash
backlash
Reaction in dynamic motion systems where potential energy that was created while the object was in motion is released when the object stops. Release of this potential energy or inertia causes the device to quickly snap backward relative to the last direction of motion. Backlash can cause a system’s final resting position to be different from what was intended and from where the control system intended to stop the device.
- chuck
chuck
Workholding device that affixes to a mill, lathe or drill-press spindle. It holds a tool or workpiece by one end, allowing it to be rotated. May also be fitted to the machine table to hold a workpiece. Two or more adjustable jaws actually hold the tool or part. May be actuated manually, pneumatically, hydraulically or electrically. See collet.
- computer numerical control ( CNC)
computer numerical control ( CNC)
Microprocessor-based controller dedicated to a machine tool that permits the creation or modification of parts. Programmed numerical control activates the machine’s servos and spindle drives and controls the various machining operations. See DNC, direct numerical control; NC, numerical control.
- depth of cut
depth of cut
Distance between the bottom of the cut and the uncut surface of the workpiece, measured in a direction at right angles to the machined surface of the workpiece.
- feed
feed
Rate of change of position of the tool as a whole, relative to the workpiece while cutting.
- lathe
lathe
Turning machine capable of sawing, milling, grinding, gear-cutting, drilling, reaming, boring, threading, facing, chamfering, grooving, knurling, spinning, parting, necking, taper-cutting, and cam- and eccentric-cutting, as well as step- and straight-turning. Comes in a variety of forms, ranging from manual to semiautomatic to fully automatic, with major types being engine lathes, turning and contouring lathes, turret lathes and numerical-control lathes. The engine lathe consists of a headstock and spindle, tailstock, bed, carriage (complete with apron) and cross slides. Features include gear- (speed) and feed-selector levers, toolpost, compound rest, lead screw and reversing lead screw, threading dial and rapid-traverse lever. Special lathe types include through-the-spindle, camshaft and crankshaft, brake drum and rotor, spinning and gun-barrel machines. Toolroom and bench lathes are used for precision work; the former for tool-and-die work and similar tasks, the latter for small workpieces (instruments, watches), normally without a power feed. Models are typically designated according to their “swing,” or the largest-diameter workpiece that can be rotated; bed length, or the distance between centers; and horsepower generated. See turning machine.
- machining center
machining center
CNC machine tool capable of drilling, reaming, tapping, milling and boring. Normally comes with an automatic toolchanger. See automatic toolchanger.
- milling machine ( mill)
milling machine ( mill)
Runs endmills and arbor-mounted milling cutters. Features include a head with a spindle that drives the cutters; a column, knee and table that provide motion in the three Cartesian axes; and a base that supports the components and houses the cutting-fluid pump and reservoir. The work is mounted on the table and fed into the rotating cutter or endmill to accomplish the milling steps; vertical milling machines also feed endmills into the work by means of a spindle-mounted quill. Models range from small manual machines to big bed-type and duplex mills. All take one of three basic forms: vertical, horizontal or convertible horizontal/vertical. Vertical machines may be knee-type (the table is mounted on a knee that can be elevated) or bed-type (the table is securely supported and only moves horizontally). In general, horizontal machines are bigger and more powerful, while vertical machines are lighter but more versatile and easier to set up and operate.
- toolchanger
toolchanger
Carriage or drum attached to a machining center that holds tools until needed; when a tool is needed, the toolchanger inserts the tool into the machine spindle. See automatic toolchanger.
- turning
turning
Workpiece is held in a chuck, mounted on a face plate or secured between centers and rotated while a cutting tool, normally a single-point tool, is fed into it along its periphery or across its end or face. Takes the form of straight turning (cutting along the periphery of the workpiece); taper turning (creating a taper); step turning (turning different-size diameters on the same work); chamfering (beveling an edge or shoulder); facing (cutting on an end); turning threads (usually external but can be internal); roughing (high-volume metal removal); and finishing (final light cuts). Performed on lathes, turning centers, chucking machines, automatic screw machines and similar machines.