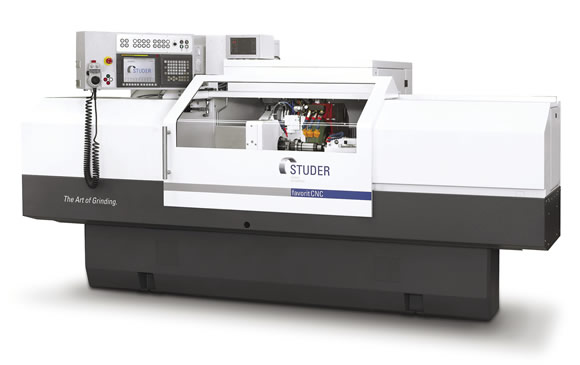
United Grinding offers universal cylindrical grinder
United Grinding Technologies Inc.’s Studer favoritCNC universal cylindrical grinder is for processing medium-sized workpieces in individual and serial production. The machine offers a 25.6" grinding length, a 6.9" center height, a workpiece-weight capacity of 176 lbs. and accepts grinding wheels with maximum diameters of 20"×2.5"×8". The machine bed is made of solid Granitan S103 to enhance damping behavior and ensure a fine workpiece surface finish, according to the company. The V and flat guide ways for the cross slides are molded directly into the machine base and are finished with a nonabrasive Granitan S200 slide-way coating. The surface structure prevents the slides from hydroplaning and eliminates the stick-slip effect. The longitudinal and cross slides are manufactured from gray cast iron and have ground V and flat guide ways, with the distance between guide ways optimally suited to the machine’s overall rigidity, according to the company. The slides are advanced by 40mm-dia. circulating ballscrews connected to a three-phase servomotor via torsion-resistant, bellow-type couplings. The turret wheelhead can be used for external and internal grinding. The turret can be equipped with an extra grinding wheel and internal grinding spindle for this purpose. The user can manually index the turret wheelhead in a Hirth gear within a swiveling range of -15°/ +195°. Options include in-process gaging, balancing systems, contact detection and length positioning.
United Grinding Technologies Inc.
www.grinding.com
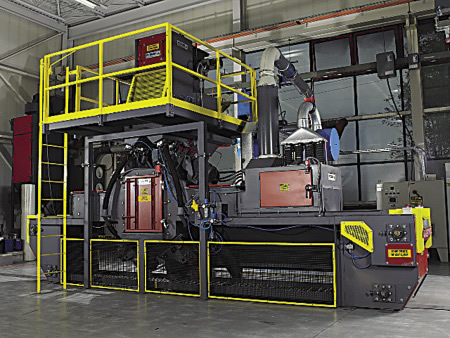
Belt machines for continuous blasting
Rosler Metal Finishing USA LLC's RDGE series wire mesh belt machines are for continuous blasting treatment of flat and dimensional components. With four or eight high-power Hurricane blast turbines vertically or horizontally mounted around the housing, the machines can be used to treat complex parts, such as ones with pockets, intricate designs and difficult-to-reach areas, the company reports. A belt guiding system enables the lower turbines to blast only through one belt position to keep masking to a minimum. The wear-resistant wire mesh belt, with tension adjustment, reliably transports parts, according to the company.
Rosler Metal Finishing USA LLC
www.rosler.us
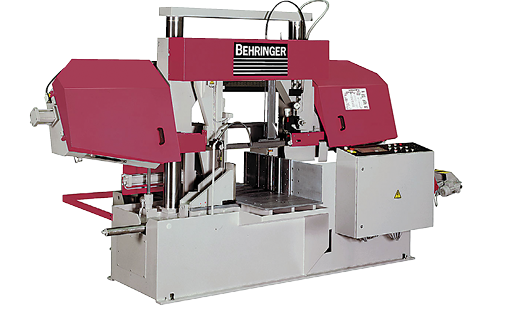
Automatic bandsaw cuts bars and pipes
Behringer Saws Inc.'s HBP-610A bandsaw is for cutting pipes and solid bars up to 24" in diameter. The cast iron saw frame has a dual-column design, which utilizes positive hydraulic down feed. The solid cast bow frame eliminates vibration and provides rigid support for blade tensioning, according to the company. The high-torque, frequency-controlled saw drive provides cutting speeds from 62 to 426 sq. ft./min. An automatic pressure sensing system monitors the down feed power and saw blade pressure. Cutting pressure data is analyzed and the system automatically makes blade pressure adjustments as needed to ensure an optimal balance between the feed rate and blade pressure.
Behringer Saws Inc.
www.behringersaws.com
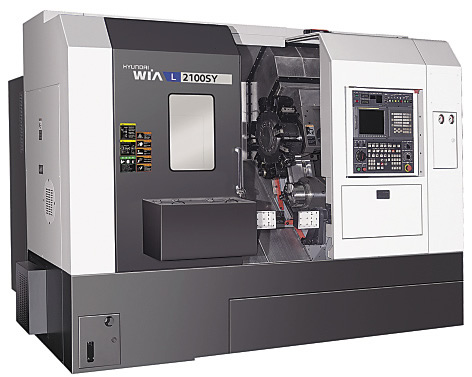
Machining centers from Hyundai WIA
The L2100Y/SY CNC multitask turning centers from Hyundai WIA Machine Corp. have a wedge-type Y-axis and a BMT 65 (VDI 140) turret for milling and turning complex parts in a single setup. The 4,500-rpm synchronized 8" main spindle and 6" subspindle on S-configured machines enable turning of the front and back of cylindrical parts. The swing over the bed is 630mm, swing over the carriage is 300mm, maximum turning diameter is 335mm and maximum turning length is 468mm (455mm on SY). All axes are driven by double-nut ballscrews to eliminate thermal growth during machining, according to the company. All ballscrews are connected directly to the servo drive motors without gears or belts, eliminating backlash.
Hyundai WIA Machine Corp.
www.en.hyundai-wia.com
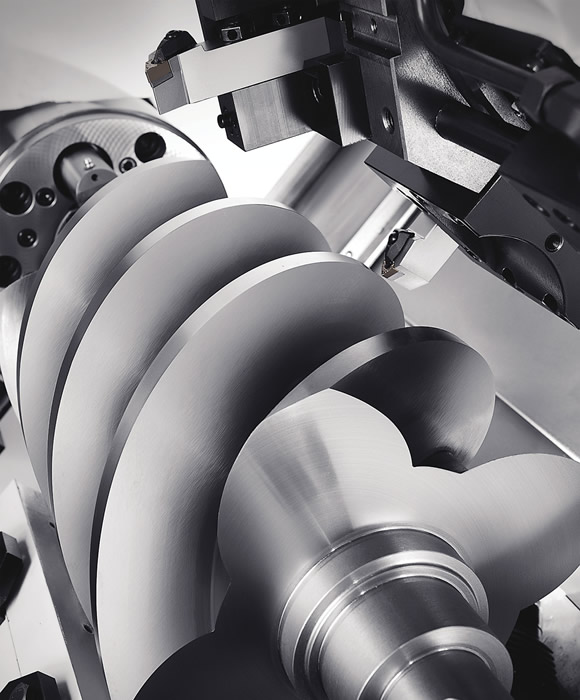
Heavy-duty lathe has small footprint
The Hi-TECH 450 horizontal turning center from Hwacheon Machinery America has a 500mm turning diameter and 1,350mm turning length. A spindle with integral motor offers a low speed of 800 rpm for high-torque turning and a maximum speed of 3,500 rpm. The rapid feed rate is 20 m/min. for the X-axis and 24 m/min. for the Z-axis. Turret indexing time to adjacent tools is 0.25 seconds, and turret capacity is 12 tools. The machine has an integrated 45° bed frame to minimize heat distortion and promote chip shedding and access to the work area, according to the company. The hand-scraped guide surface and bed design absorb vibration to enhance stability during hard turning. The geared transmission system is separate from the spindle motor to avoid the negative impact of transmission heat and vibration on the spindle. Six machine configurations are available, according to Hwacheon. A Y-axis is optional, which can be added to the MC/SMC type of the machine, reportedly reducing cycle times for multiple-function operations.
Hwacheon Machinery America
www.hwacheon.com
Related Glossary Terms
- backlash
backlash
Reaction in dynamic motion systems where potential energy that was created while the object was in motion is released when the object stops. Release of this potential energy or inertia causes the device to quickly snap backward relative to the last direction of motion. Backlash can cause a system’s final resting position to be different from what was intended and from where the control system intended to stop the device.
- bandsaw
bandsaw
Machine that utilizes an endless band, normally with serrated teeth, for cutoff or contour sawing. See saw, sawing machine.
- centers
centers
Cone-shaped pins that support a workpiece by one or two ends during machining. The centers fit into holes drilled in the workpiece ends. Centers that turn with the workpiece are called “live” centers; those that do not are called “dead” centers.
- computer numerical control ( CNC)
computer numerical control ( CNC)
Microprocessor-based controller dedicated to a machine tool that permits the creation or modification of parts. Programmed numerical control activates the machine’s servos and spindle drives and controls the various machining operations. See DNC, direct numerical control; NC, numerical control.
- feed
feed
Rate of change of position of the tool as a whole, relative to the workpiece while cutting.
- flat ( screw flat)
flat ( screw flat)
Flat surface machined into the shank of a cutting tool for enhanced holding of the tool.
- gang cutting ( milling)
gang cutting ( milling)
Machining with several cutters mounted on a single arbor, generally for simultaneous cutting.
- grinding
grinding
Machining operation in which material is removed from the workpiece by a powered abrasive wheel, stone, belt, paste, sheet, compound, slurry, etc. Takes various forms: surface grinding (creates flat and/or squared surfaces); cylindrical grinding (for external cylindrical and tapered shapes, fillets, undercuts, etc.); centerless grinding; chamfering; thread and form grinding; tool and cutter grinding; offhand grinding; lapping and polishing (grinding with extremely fine grits to create ultrasmooth surfaces); honing; and disc grinding.
- grinding wheel
grinding wheel
Wheel formed from abrasive material mixed in a suitable matrix. Takes a variety of shapes but falls into two basic categories: one that cuts on its periphery, as in reciprocating grinding, and one that cuts on its side or face, as in tool and cutter grinding.
- hard turning
hard turning
Single-point cutting of a workpiece that has a hardness value higher than 45 HRC.
- in-process gaging ( in-process inspection)
in-process gaging ( in-process inspection)
Quality-control approach that monitors work in progress, rather than inspecting parts after the run has been completed. May be done manually on a spot-check basis but often involves automatic sensors that provide 100 percent inspection.
- lathe
lathe
Turning machine capable of sawing, milling, grinding, gear-cutting, drilling, reaming, boring, threading, facing, chamfering, grooving, knurling, spinning, parting, necking, taper-cutting, and cam- and eccentric-cutting, as well as step- and straight-turning. Comes in a variety of forms, ranging from manual to semiautomatic to fully automatic, with major types being engine lathes, turning and contouring lathes, turret lathes and numerical-control lathes. The engine lathe consists of a headstock and spindle, tailstock, bed, carriage (complete with apron) and cross slides. Features include gear- (speed) and feed-selector levers, toolpost, compound rest, lead screw and reversing lead screw, threading dial and rapid-traverse lever. Special lathe types include through-the-spindle, camshaft and crankshaft, brake drum and rotor, spinning and gun-barrel machines. Toolroom and bench lathes are used for precision work; the former for tool-and-die work and similar tasks, the latter for small workpieces (instruments, watches), normally without a power feed. Models are typically designated according to their “swing,” or the largest-diameter workpiece that can be rotated; bed length, or the distance between centers; and horsepower generated. See turning machine.
- milling
milling
Machining operation in which metal or other material is removed by applying power to a rotating cutter. In vertical milling, the cutting tool is mounted vertically on the spindle. In horizontal milling, the cutting tool is mounted horizontally, either directly on the spindle or on an arbor. Horizontal milling is further broken down into conventional milling, where the cutter rotates opposite the direction of feed, or “up” into the workpiece; and climb milling, where the cutter rotates in the direction of feed, or “down” into the workpiece. Milling operations include plane or surface milling, endmilling, facemilling, angle milling, form milling and profiling.
- sawing machine ( saw)
sawing machine ( saw)
Machine designed to use a serrated-tooth blade to cut metal or other material. Comes in a wide variety of styles but takes one of four basic forms: hacksaw (a simple, rugged machine that uses a reciprocating motion to part metal or other material); cold or circular saw (powers a circular blade that cuts structural materials); bandsaw (runs an endless band; the two basic types are cutoff and contour band machines, which cut intricate contours and shapes); and abrasive cutoff saw (similar in appearance to the cold saw, but uses an abrasive disc that rotates at high speeds rather than a blade with serrated teeth).
- turning
turning
Workpiece is held in a chuck, mounted on a face plate or secured between centers and rotated while a cutting tool, normally a single-point tool, is fed into it along its periphery or across its end or face. Takes the form of straight turning (cutting along the periphery of the workpiece); taper turning (creating a taper); step turning (turning different-size diameters on the same work); chamfering (beveling an edge or shoulder); facing (cutting on an end); turning threads (usually external but can be internal); roughing (high-volume metal removal); and finishing (final light cuts). Performed on lathes, turning centers, chucking machines, automatic screw machines and similar machines.