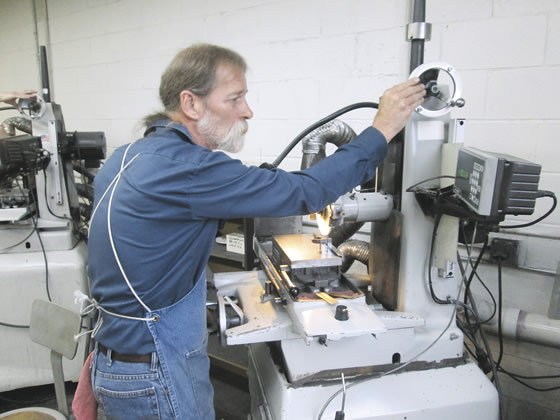
Using a Harig surface grinder, toolmaker Robin Wood grinds the chamfer on a pin (below) that goes into the cooling system for thermal imaging equipment. All images courtesy A. Rooks.
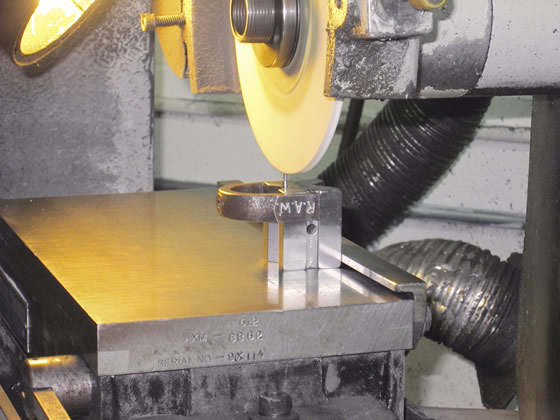
Whether they are large or small, successful cultures have the ability to pass on knowledge and tradition from one generation to the next. Peerless Precision Inc., Westfield, Mass., has accomplished that in several key ways:
— Unlike many machine shops, Peerless, which has 23 employees, has a mix of experienced workers and new hires from the local vocational high school 's co-op program.
— Its president, Kristin Maier, took over the job of leading the shop when her father fell ill.
— Peerless brings “lost” talent to the shop: Frank Coon, who manages the deburring department, joined the company after closing his deburring business and finding that retirement didn’t suit him. He now instructs younger employees on the art of deburring.
The talented crew at Peerless has helped it succeed, grow and become a key supplier for Tier 1 aerospace and defense manufacturers. In addition to Kristin Maier, the management team includes her mom, Debbie Maier, CEO and CFO; Rick Collingwood, foreman; Bill Roy, production manager and CNC programmer; Joe Beavis, estimator and process engineer; and Jim Hebda, quality manager. Peerless continues to hire new talent from Westfield Vocational Technical High School’s co-op program, helping ensure the shop’s future as employees reach retirement age.
Relocation Time
The Maier family’s tenure at Peerless Precision began 916 miles west in Naperville, Ill., where the family was living when Larry Maier began looking for a business to purchase.
“My father was an entrepreneur and had started a vending company that he and my mother ran together, as well as another company that helped other entrepreneurs start their own companies,” Kristin said. “Those two companies were decent, but they didn’t produce enough revenue to support our family, so my dad looked in the Chicago area, in Virginia, where his family lives, and in New England, where my mother’s family lives. The guy who owned Peerless wanted to retire, and it was a great opportunity for us, so we ended up here in 1997, when I was in high school.”
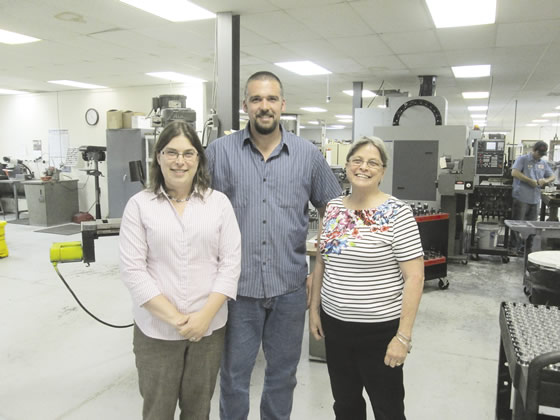
From left: Kristin Maier, president; Rick Collingwood, foreman; Debbie Maier, CEO and CFO.
When Larry Maier purchased it, Peerless Precision primarily did grinding and lapping and some manual turning and milling. About 75 percent of the shop’s sales were computer parts for IBM. Larry Maier saw an opportunity to take Peerless to the next level by adding CNC machining and pursuing aerospace and defense customers.
“A lot of employees didn’t want to do that because it was outside their comfort zone, but you can’t get anything that’s worth having without taking a risk,” Kristin said. “So with a lot of prodding from my dad, we got a couple of aerospace and defense customers. Now they are our top two customers.” One is Triumph Engine Control Systems, West Hartford, Conn., a Tier 1 supplier to aircraft engine maker Pratt & Whitney.
Peerless, founded in 1976, has built up its CNC turning capability to four CNC lathes: a Hyundai-Kia SKT 15 with a 6 ' (1.83m) bar feeder, a Hyundai-Kia SKT-21LMS Twin Spindle with a 6 ' bar feeder, an Okuma Genos L250E with a 2 ' (0.61m) internal bar feeder and an Okuma LB10 with a 2 ' internal bar feeder. In addition, the shop has three CNC mills: a Hyundai-Kia VX500 with 5th-axis positioning, a Hyundai-Kia VX400 with a rotary 4th axis and a Haas VF-3 with a rotary 4th axis. In April, Peerless added a Mazak VCU-400A 5X, adding 5-axis vertical machining to its capabilities.
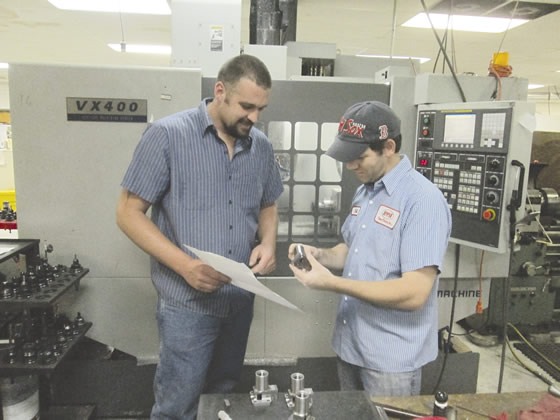
Foreman Rick Collingwood (left) reviews a part’s dimensions with Bill Roy, production manager and CNC programmer. The part goes into a smart missile system used on U.S. Navy submarines and is machined on a Hyundai-Kia VX400 with a rotary 4th axis.
Kristin worked at the shop on and off during high school doing odd jobs, and, after college, took a position in shipping and receiving. However, she wanted to see what she could do on her own. “I needed to branch out beyond the family business, so in March 2005 I moved to San Diego.” After a stint as a warehouse manager for a gourmet cookware store, she became a buyer for a fire alarm contractor and enjoyed the West Coast lifestyle.
However, when she left Massachusetts, Kristin promised her parents that, should anything happen to them, she would return to help run the family business. That call came in March 2012.
“My dad was first diagnosed with cancer in 2009, and after treatment it went into remission but it came back with a vengeance,” she said. “Mom and dad asked me to come back, and I said I would. They were a bit shocked, because they had forgotten about my promise, but in September I returned to run the business.” Larry Maier passed away in October 2012, and Kristin succeeded him as president.
From Strength to Strength
Peerless Precision’s main capability remains making parts up to 6 " (152.4mm) in diameter and 12 " (304.8mm) square with tolerances that range from 0.0010 " to 0.000050 " (25.4µm to 1.27µm). That dimensional accuracy comes from the shop’s heritage as a finishing shop, and its grinding, lapping and honing departments stay busy. This includes manual work on three Norton surface lappers and surface, jig, OD and ID grinding. “We can lap hundreds of parts at one time to within 0.0000050 " of each other,” Kristin said. “We also do a lot of match and hand lapping, which helps maintain tight tolerances. In the grinding department, we can maintain a 0.0030 " wall thickness in titanium. We have good machines, but I attribute most of it to the talent of our guys. They take a lot of pride in their work and have been here for many years. They like working here and we like having them.”
The finishing department helps generate business, as it takes in jobs other machine shops can’t handle. It also brings in new jobs. For example, the division of an existing customer had a problem with a vendor that was supplying out-of-spec pin bushing sets. “The division’s vice president of operations was trying to sand 25 pins down to fit inside the bushing, and he was frustrated,” Kristin said. “Our customer told him to talk to Peerless, so we took on the job of finishing the 25 pieces. We also told him that we’ll do you one better and make 20 of the bushing sets from scratch within tolerances of 0.0000050 ". We said, ‘not only will they match, they will be interchangeable, and if you like them, keep them at no charge.’ We have received quite a few orders since then.”
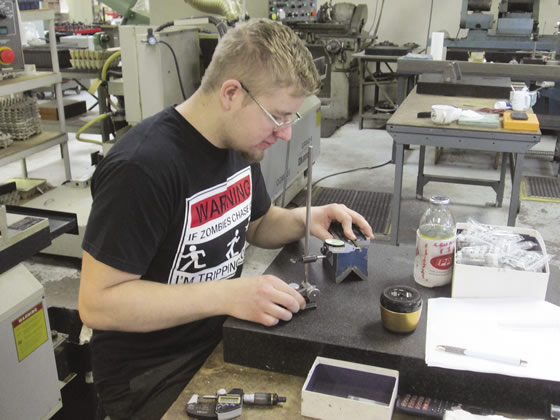
Dmitriy Golenev, who began as a co-op student with Peerless in 2008 and graduated from Westfield Vocational in 2009, checks runout on a regenerator subassembly.
Another key part of Peerless’ success is being proactive about gaining and maintaining certifications. The company received ISO 9001 and AS 9100 certifications in 2003, well before its customers began requiring them. “We like to do things that set us apart from other companies, so we got both certifications in parallel,” Kristin said. As are other certificate holders, Peerless is audited every year and recertified every 2 years.
Peerless, which runs one shift 5 days per week, focuses on manufacturing aerospace parts 6 " in diameter and smaller for engines, fuel systems and hydraulic systems. Some of its parts are in the micro realm, such as a 1mm (0.039 ") pin assembly. The shop also provides microparts to a company that makes forward-looking infrared cameras and night-vision thermal imaging cameras. The parts go into the cameras’ cryogenic cooling systems.
Peerless can offer its customers an expanded range of services by being part of a network of 30 central Massachusetts shops that perform work for each other. “That allows us to say we can do everything from ordering raw material through final inspection, including screw machining, large-part manufacturing, welding, heat treating, plating and nondestructive testing,” Kristin said. “It’s a great network. None of us wants another shop to fail; we all support each other. Our shop was able to have one rush part ready to go in a week thanks to the network.”

Peerless produces these alternator housing assemblies for an aerospace engine. The traveler (document packet) with the job provides customer and order information and routing for machining, finishing and shipping. The traveler allows Peerless to ensure parts are machined the same way every time. Workers initial and date operations as they are completed, record the time or PO number and accept and reject quantities. This allows Peerless to track the part in its QC program and perform corrective actions as needed.
Training Days
Peerless aims to keep its skill levels high by hiring young workers who can learn from its experienced staff, preferring to hire someone out of high school than from another machine shop.
“For example, we were looking for someone with experience in grinding, but we found that the people worth hiring were already taken and the people applying for the job either didn’t have the skills we needed or hadn’t worked in the industry for 20 years,” Kristin said. “Either way, they wanted to do things their way and didn’t want to learn our way.”
Instead, Peerless works closely with Westfield Vocational to identify prospects and trains them as co-op students. “Westfield has one the best manufacturing departments out there, and when their seniors go out for co-op, we interview them,” she said. “Westfield requires at least a 75 percent (C) academic average and a good attendance record for students going out on co-op. During their senior year, they work here full-time 2 weeks each month and part-time the other 2 weeks, when they are doing academics. At the end of the school year, if everything works out, we hire them full-time. We’ve hired six or seven people that way over the past 20 years.”
For example, the most recent Westfield Vocational students or recent graduates who work at Peerless are:
— Aaron George started on a co-op in Sept. 2013. He trained on finishing and joined the finishing department full-time after graduating in June 2014. In Dec. 2014, he transferred to CNC milling.
— Danylo Zarichnyy, a senior co-op student, works in the finishing department and will be hired full-time after he graduates this spring.
— Antony Muto, a junior, is a “shop kid,” providing part-time cleaning and general help. Muto will co-op in the finishing department beginning this summer.
Peerless also helps its established workers grow in their jobs. “We encourage innovation because our people are really smart,” Kristin said. “Often, they can examine a part and come up with a new way of machining it—sometimes on another machine—that takes less time. We encourage that and they don’t have to worry about failing; you can 't learn anything without risking failure, and more often than not the new way succeeds and saves us and the customer money. And since we have profit sharing based on the profitability of individual jobs, some of that can come back to them.”
While Peerless Precision has a strong base in New England’s robust aerospace and defense industry, Kristin Maier would like to expand the shop’s profile. “I 've been going to trade shows around the country. I want to extend our shop’s reach nationally. The majority of our customers are in New England, but we have a customer in Missouri and one in Tijuana, Mexico. We want to grow everywhere.”
For more information about Peerless Precision call (413) 562-2359 or visit www.peerlessprecision.com. CTE
About the Author: Alan Rooks is editorial director of CTE. Contact him at (847) 714-0174 or [email protected].
Related Glossary Terms
- bushing
bushing
Cylindrical sleeve, typically made from high-grade tool steel, inserted into a jig fixture to guide cutting tools. There are three main types: renewable, used in liners that in turn are installed in the jig; press-fit, installed directly in the jig for short production runs; and liner (or master), installed permanently in a jig to receive renewable bushing.
- computer numerical control ( CNC)
computer numerical control ( CNC)
Microprocessor-based controller dedicated to a machine tool that permits the creation or modification of parts. Programmed numerical control activates the machine’s servos and spindle drives and controls the various machining operations. See DNC, direct numerical control; NC, numerical control.
- gang cutting ( milling)
gang cutting ( milling)
Machining with several cutters mounted on a single arbor, generally for simultaneous cutting.
- grinding
grinding
Machining operation in which material is removed from the workpiece by a powered abrasive wheel, stone, belt, paste, sheet, compound, slurry, etc. Takes various forms: surface grinding (creates flat and/or squared surfaces); cylindrical grinding (for external cylindrical and tapered shapes, fillets, undercuts, etc.); centerless grinding; chamfering; thread and form grinding; tool and cutter grinding; offhand grinding; lapping and polishing (grinding with extremely fine grits to create ultrasmooth surfaces); honing; and disc grinding.
- inner diameter ( ID)
inner diameter ( ID)
Dimension that defines the inside diameter of a cavity or hole. See OD, outer diameter.
- jig
jig
Tooling usually considered to be a stationary apparatus. A jig assists in the assembly or manufacture of a part or device. It holds the workpiece while guiding the cutting tool with a bushing. A jig used in subassembly or final assembly might provide assembly aids such as alignments and adjustments. See fixture.
- lapping
lapping
Finishing operation in which a loose, fine-grain abrasive in a liquid medium abrades material. Extremely accurate process that corrects minor shape imperfections, refines surface finishes and produces a close fit between mating surfaces.
- milling
milling
Machining operation in which metal or other material is removed by applying power to a rotating cutter. In vertical milling, the cutting tool is mounted vertically on the spindle. In horizontal milling, the cutting tool is mounted horizontally, either directly on the spindle or on an arbor. Horizontal milling is further broken down into conventional milling, where the cutter rotates opposite the direction of feed, or “up” into the workpiece; and climb milling, where the cutter rotates in the direction of feed, or “down” into the workpiece. Milling operations include plane or surface milling, endmilling, facemilling, angle milling, form milling and profiling.
- nondestructive testing ( NDT)
nondestructive testing ( NDT)
Same as nondestructive inspection but implying use of a method in which the part is stimulated and its response measured quantitatively or semiquantitatively.
- outer diameter ( OD)
outer diameter ( OD)
Dimension that defines the exterior diameter of a cylindrical or round part. See ID, inner diameter.
- parallel
parallel
Strip or block of precision-ground stock used to elevate a workpiece, while keeping it parallel to the worktable, to prevent cutter/table contact.
- sawing machine ( saw)
sawing machine ( saw)
Machine designed to use a serrated-tooth blade to cut metal or other material. Comes in a wide variety of styles but takes one of four basic forms: hacksaw (a simple, rugged machine that uses a reciprocating motion to part metal or other material); cold or circular saw (powers a circular blade that cuts structural materials); bandsaw (runs an endless band; the two basic types are cutoff and contour band machines, which cut intricate contours and shapes); and abrasive cutoff saw (similar in appearance to the cold saw, but uses an abrasive disc that rotates at high speeds rather than a blade with serrated teeth).
- turning
turning
Workpiece is held in a chuck, mounted on a face plate or secured between centers and rotated while a cutting tool, normally a single-point tool, is fed into it along its periphery or across its end or face. Takes the form of straight turning (cutting along the periphery of the workpiece); taper turning (creating a taper); step turning (turning different-size diameters on the same work); chamfering (beveling an edge or shoulder); facing (cutting on an end); turning threads (usually external but can be internal); roughing (high-volume metal removal); and finishing (final light cuts). Performed on lathes, turning centers, chucking machines, automatic screw machines and similar machines.