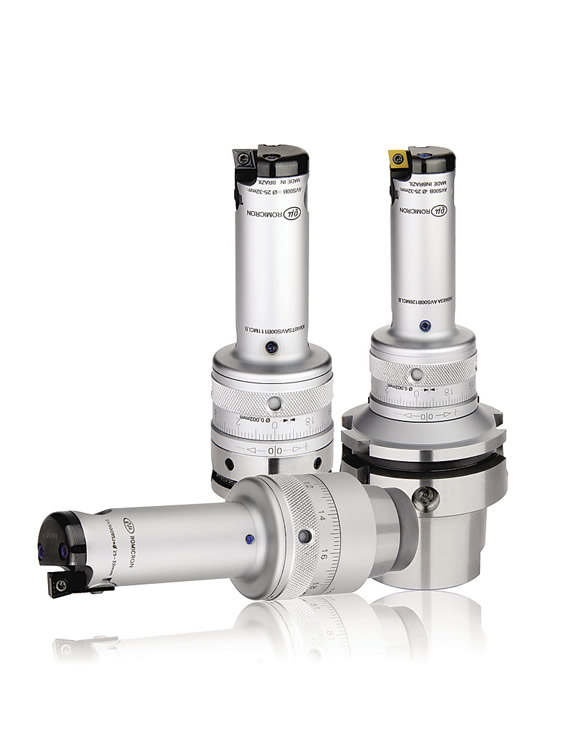
Fine-boring systems achieve closed-loop boring
The Romicron fine-boring systems from Kennametal Inc. allow users to dial-in close tolerances while a boring tool is mounted in the machine tool. They can produce finish bores with tolerances of a few microns in diameter and bore-to-bore variations of a few tenths of a micron, according to the company. Using cartridges or boring bars, Romicron tools can be adjusted in diameter with a dial ring in 2µm increments. To provide instant adjustment feedback, the system has a clicking mechanism so machine operators not only see the adjustment on the scale, but hear and feel it. The tools can run in spindles up to 20,000 rpm and with high-pressure coolant up to 120 bar (1,740 psi).
Kennametal Inc.; www.kennametal.com
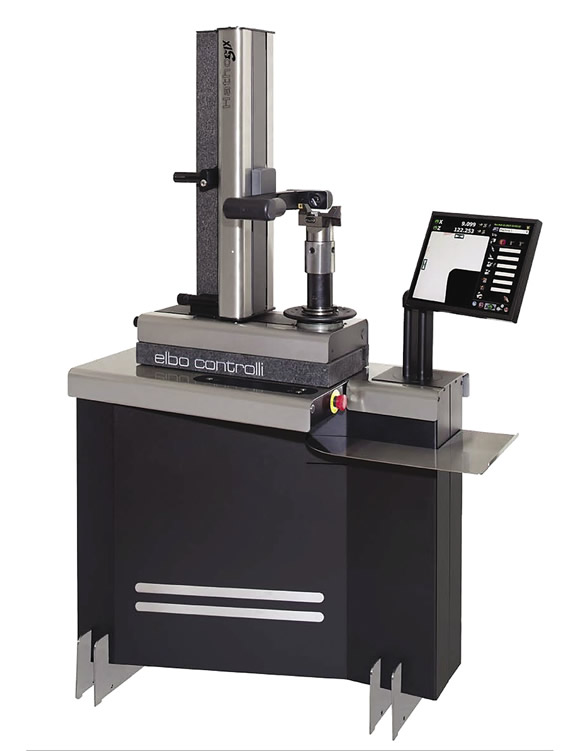
New generation of tool presetters can be used in shops
Koma Precision Inc. offers the Hathor Six (pictured) and Sethy Six tool presetters from Elbo Controlli. The Hathor Six is the floor model and the Sethy Six is the bench model. The presetters have a measuring range of 600mm (23.62 "), fixed target function in micrometric registration of the X and Z axes, and a high-definition 15 " TTF touch screen. Manual control of the C-axis is optional. The units have a ground granite column and base, a spindle body assembled on spring roller cages and optical scales. The movement accuracy of the X and Z axes is guaranteed through the use of stable granite supporting surfaces, according to the company. The thermal inertia of granite allows a presetter to be placed in a shop environment.
Koma Precision Inc.; www.komaprecision.com
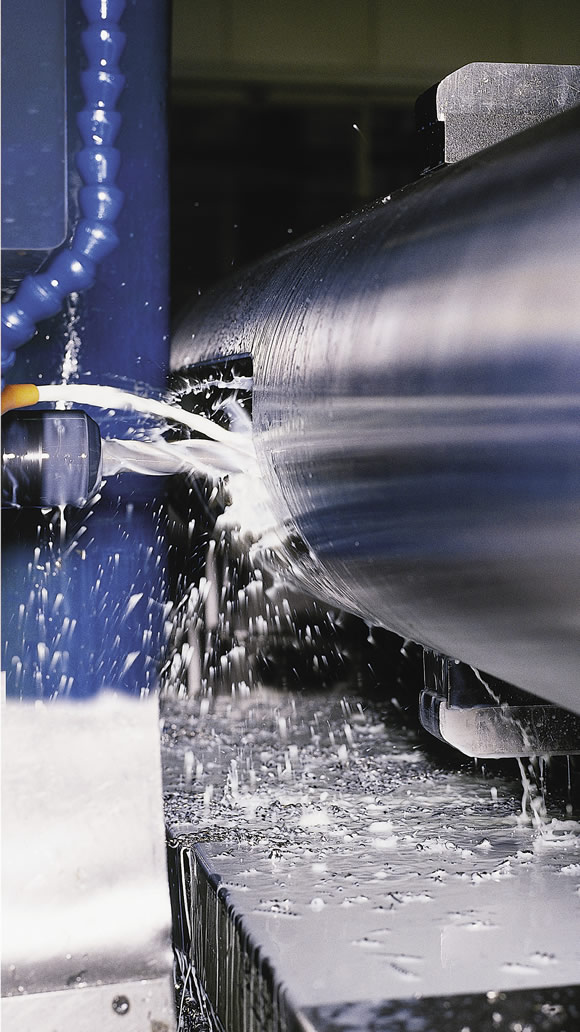
Semisynthetic coolant targeted to aerospace industry
Vasco 7000 metalworking fluid from Blaser Swisslube Inc. is a water-miscible, bio-based, semisynthetic emulsion formulated for high-speed milling of aerospace-grade titanium and nickel-base superalloys. The emulsions are sustainable and registered for use under the USDA BioPreferred Program. According to the company, the low-misting metalworking fluid, with enhanced washing action, does not require secondary amines or formaldehyde-releasing condensates to maintain long sump life. It is chlorine-free and reportedly provides high-cutting performance, increased productivity and long tool life when cutting exotic alloys.
Blaser Swisslube Inc.; www.blaser.com
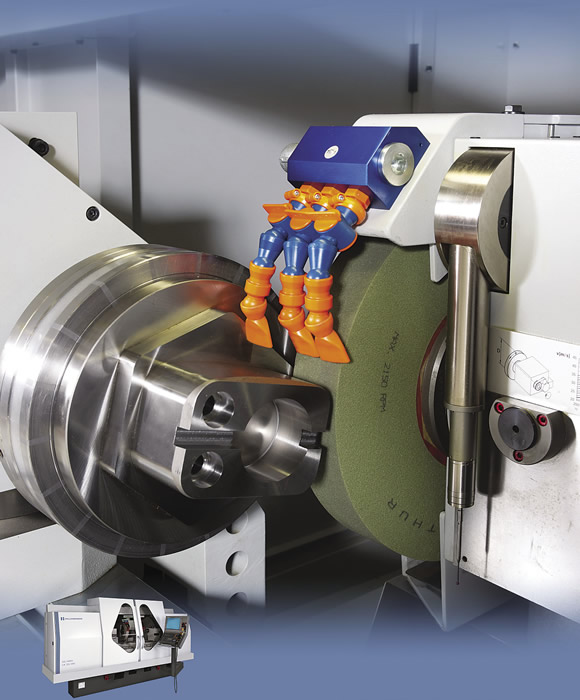
Cylindrical grinder has a direct-drive workhead for heavy parts
The Kellenberger Kel-Vari CNC universal cylindrical grinding machine from Hardinge Inc. has a robot and a rigid, direct-drive workhead for grinding heavy parts. A torque drive allows heavy parts to be quickly and precisely accelerated and braked without backlash during bidirectional movements for increased productivity, according to the company. Users can perform cylindrical, OD and ID, out-of-round, thread and jig grinding in one setup. The direct-drive workhead has an infinitely variable spindle speed, from 1 to 500 rpm, with a maximum weight capacity of 600 lbs. (272.2 kg) and an option of ±60-second microcorrection for adjustment of cylindricity. A sleeve retraction of up to 50mm (1.97 ") is pneumatically or hydraulically operated. Maximum weight between centers is 550 lbs. (250 kg). The swiveling, hydrostatic, direct-drive B-axis provides simultaneous interpolation of the X, Z and B axes.
Hardinge Inc.; www.hardinge.com
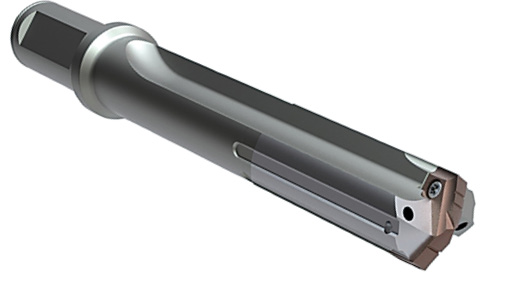
Drill targets deep-hole applications
Allied Machine & Engineering Corp.’s Guided T-A drill is for deep-hole drilling. The tool accepts AM200-coated inserts, or blades. The coating resists heat, which increases tool life up to 50 percent, and the tool offers penetration rates up to twice that of a gundrill, according to the company. The drill provides a tight, true position and a straight hole throughout the operation. Engineered for breaking out on an uneven surface, the drill is available in carbide-clad and chrome-plated styles and accepts the company’s standard HSS and carbide T-A and GEN2 T-A blades.
Allied Machine & Engineering Corp.; www.alliedmachine.com
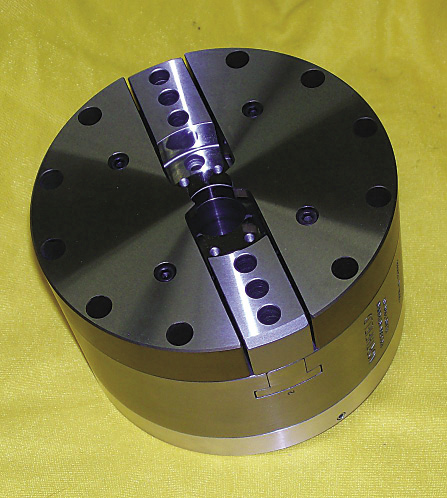
Air chuck grips hole saw blanks
Northfield Precision Instrument Corp.’s Model 627-W 6 "-dia. chuck has a 0.0001 " TIR and grips hole-saw blanks for turning and tapping. The 2-jaw, coolant/air blast-through chuck features a 1 "-dia. counterbore for clearance. Subjaws with two bullet-nose pins grip the blanks between two holes. The jaws are about ¾ " wide to fit between two hardened and ground circle segments mounted to the chuck face to support the workpiece during machining.
Northfield Precision Instrument Corp.; www.northfield.com
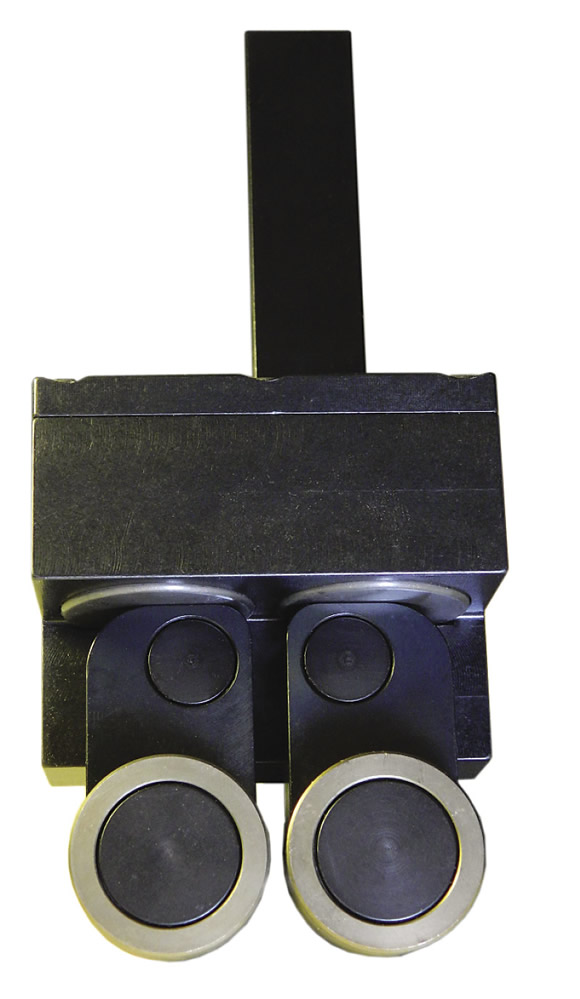
Self-adjusting bar puller for turning centers
The EZ-Puller from Accudyne Corp. is a self-adjusting bar puller used in turning centers to provide automatic operation of a CNC machine. It allows the programmer or setup person to change bar sizes in the machine without manually adjusting the tool. The bar puller functions via polyurethane springs that provide force to the pivoting arms. These arms, in turn, apply force to circular grippers at the end of the arms. The grippers rotate only under extreme load and have a serration geometry that minimally penetrates stock while maximizing grip for an accurate pull, according to the company. To set the puller for gripping and pulling bar stock, the tool is moved in the Z-axis until the grippers are at least 0.180 " past the end of the stock, then moved in the X-axis until the grippers are on centerline with the material being pulled.
Accudyne Corp.; www.ezpullerusa.com
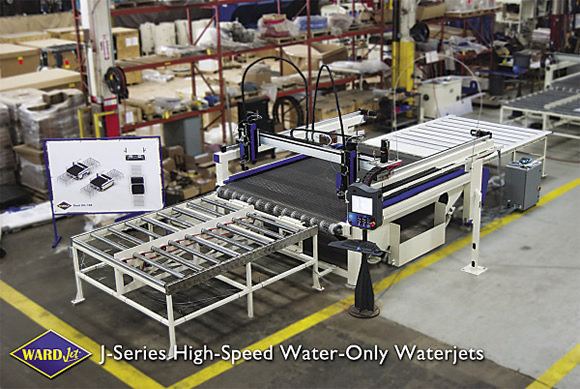
Water-only waterjet is a low-cost option
WARDJet Inc.’s J-Series water-only waterjet cutting machine uses belt-drive technology and cuts without abrasives at speeds up to 2,500 ipm with an acceleration/deceleration rate of 0.2 m/sec.2. The waterjet is suited for companies looking to cut high volumes of parts where margins are low and tolerances are not tight. The machine has a modular design for making design changes and can accommodate material handlers, such as loading and unloading tables, as well as optical sensors to control chain-feed tables or pinch-feed rollers.
WARDJet Inc.; www.wardjet.com
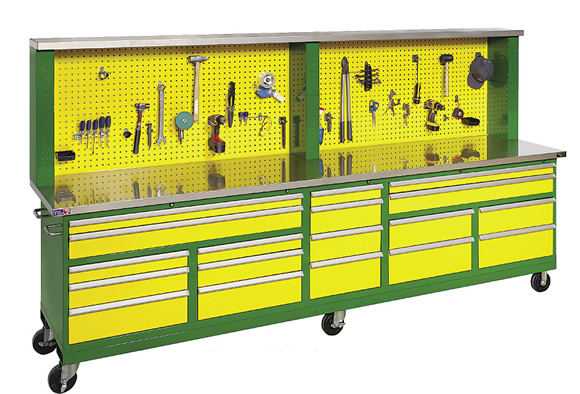
Mobile cabinet maximizes storage space
Stor-Loc has added the MM33 tool storage and drawer system to its product line. The one-piece mobile cabinet measures 44 "×144 "×30 ". It has a stainless steel work surface, a steel pegboard back to allow instant access to frequently used tools and parts, and factory-installed, heavy-duty casters. The cabinet is available in various colors. Optional accessories include under-riser lighting and duplex electrical outlets.
Stor-Loc; www.storloc.com
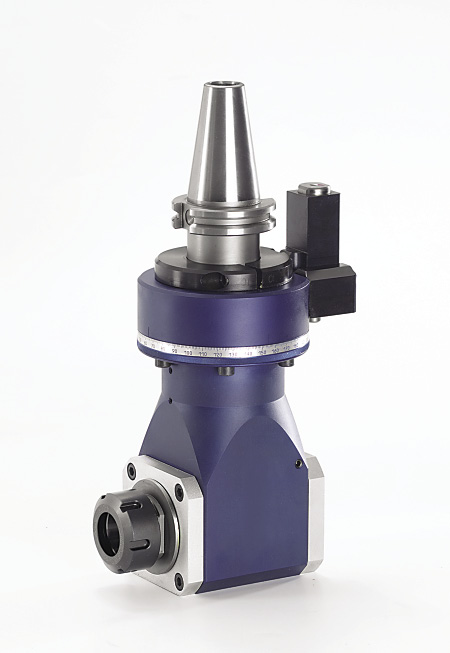
Angle heads accommodate popular tools
Heimatec Inc. says its standard and custom angle heads are available in sizes and styles to accommodate a vast array of CNC machine tools. The angle heads have twin or double-twin sets of matched angular contact bearings and a rear radial-support bearing to provide maximum stability, according to the company. The gears have inclined teeth made from high-resistance gear steel. The teeth are hardened, ground and lapped in sets to provide smooth transmission output. The heads are made from high-tensile-strength aluminum. CAT 50, CAT 40, BT 50, BT 40, BT 30, HSK 100A and HSK 63A taper styles are available, as well as custom modifications, such as 18 " extension shafts. Standard features include 360° body rotation with positive compression locking, 90° incremental repositioning without indicating, torque up to 150 Nm, interchangeable torque arms and spindles speeds to 18,000 rpm.
Heimatec Inc.; www.heimatec.com
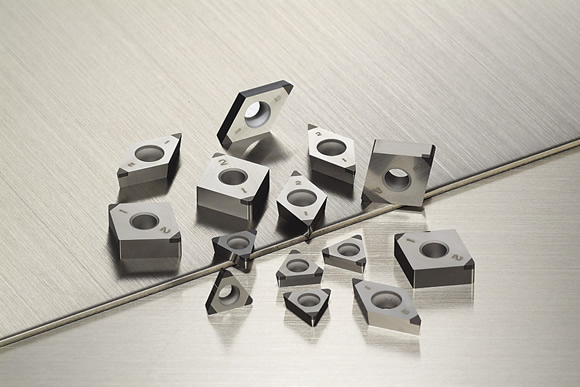
PCBN inserts are for machining P/M parts
Sumitomo Electric Carbide Inc.’s BN7500-grade PCBN inserts are available with five edge preparations for machining sintered alloys. The inserts are suitable for cutting P/M workpieces of any hardness, according to the company. In addition to the standard edge prep, the LF controls burrs, the LE and LS impart fine surface finishes, and the HS controls insert breakage when interrupted cutting. Multiple-tip inserts are available.
Sumitomo Electric Carbide Inc.; www.sumicarbide.com
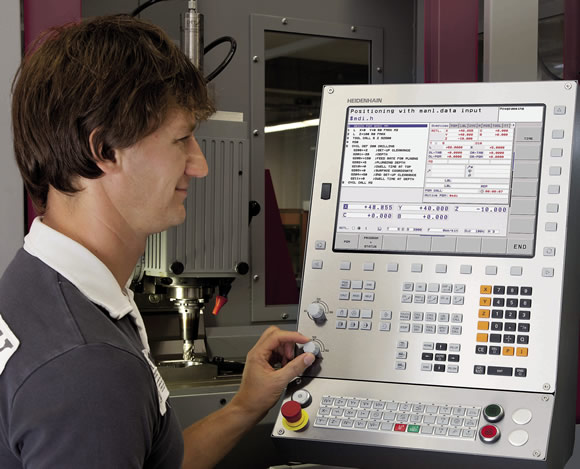
Affordable digital CNC can be customized
The TNC 620 CNC from Heidenhain Corp. can be customized with various features and software options, giving machine tool builders and end users the ability to tailor the control to their specific needs. The DXF converter allows the user to open DXF files directly on the CNC to extract contours, point patterns and machining positions. The control comes with the HSCI interface to provide high noise immunity and simplified troubleshooting and installation, according to the company. When programming away from a machine, the control automatically takes into account machine geometry, tilting the working plane. The active chatter control function reportedly significantly reduces a machine’s tendency to chatter and increases the attainable metal-removal rate during heavy cutting by 25 percent or more.
Heidenhain Corp.; www.heidenhain.com
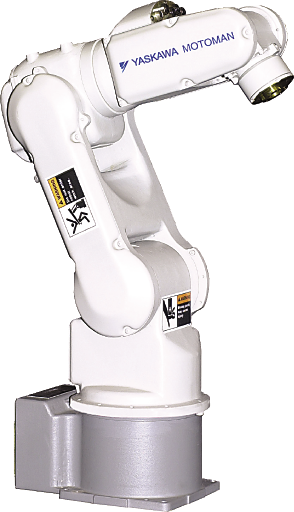
Robot suits compact applications
The MH3F robot from Yaskawa Motoman Robotics is for compact, light-payload applications, such as parts assembly, material handling and packaging. The robot’s base width of 200mm (7.87 ") allows it to be mounted in confined areas. It offers a maximum payload of 3 kg (6 lbs., 10 oz.), an 804mm (31.65 ") vertical reach and a 532mm (20.94 ") horizontal reach. A built-in collision avoidance feature enables two robots to be used together to optimize productivity. Internally routed cables and hoses enhance system reliability, according to the company. The robot’s FS100 controller has open software architecture.
Yaskawa Motoman Robotics; www.motoman.com
Related Glossary Terms
- alloys
alloys
Substances having metallic properties and being composed of two or more chemical elements of which at least one is a metal.
- backlash
backlash
Reaction in dynamic motion systems where potential energy that was created while the object was in motion is released when the object stops. Release of this potential energy or inertia causes the device to quickly snap backward relative to the last direction of motion. Backlash can cause a system’s final resting position to be different from what was intended and from where the control system intended to stop the device.
- boring
boring
Enlarging a hole that already has been drilled or cored. Generally, it is an operation of truing the previously drilled hole with a single-point, lathe-type tool. Boring is essentially internal turning, in that usually a single-point cutting tool forms the internal shape. Some tools are available with two cutting edges to balance cutting forces.
- centers
centers
Cone-shaped pins that support a workpiece by one or two ends during machining. The centers fit into holes drilled in the workpiece ends. Centers that turn with the workpiece are called “live” centers; those that do not are called “dead” centers.
- chatter
chatter
Condition of vibration involving the machine, workpiece and cutting tool. Once this condition arises, it is often self-sustaining until the problem is corrected. Chatter can be identified when lines or grooves appear at regular intervals in the workpiece. These lines or grooves are caused by the teeth of the cutter as they vibrate in and out of the workpiece and their spacing depends on the frequency of vibration.
- chuck
chuck
Workholding device that affixes to a mill, lathe or drill-press spindle. It holds a tool or workpiece by one end, allowing it to be rotated. May also be fitted to the machine table to hold a workpiece. Two or more adjustable jaws actually hold the tool or part. May be actuated manually, pneumatically, hydraulically or electrically. See collet.
- clearance
clearance
Space provided behind a tool’s land or relief to prevent rubbing and subsequent premature deterioration of the tool. See land; relief.
- computer numerical control ( CNC)
computer numerical control ( CNC)
Microprocessor-based controller dedicated to a machine tool that permits the creation or modification of parts. Programmed numerical control activates the machine’s servos and spindle drives and controls the various machining operations. See DNC, direct numerical control; NC, numerical control.
- coolant
coolant
Fluid that reduces temperature buildup at the tool/workpiece interface during machining. Normally takes the form of a liquid such as soluble or chemical mixtures (semisynthetic, synthetic) but can be pressurized air or other gas. Because of water’s ability to absorb great quantities of heat, it is widely used as a coolant and vehicle for various cutting compounds, with the water-to-compound ratio varying with the machining task. See cutting fluid; semisynthetic cutting fluid; soluble-oil cutting fluid; synthetic cutting fluid.
- counterbore
counterbore
Tool, guided by a pilot, that expands a hole to a certain depth.
- cylindrical grinding
cylindrical grinding
Grinding operation in which the workpiece is rotated around a fixed axis while the grinding wheel is fed into the outside surface in controlled relation to the axis of rotation. The workpiece is usually cylindrical, but it may be tapered or curvilinear in profile. See centerless grinding; grinding.
- emulsion
emulsion
Suspension of one liquid in another, such as oil in water.
- gang cutting ( milling)
gang cutting ( milling)
Machining with several cutters mounted on a single arbor, generally for simultaneous cutting.
- grinding
grinding
Machining operation in which material is removed from the workpiece by a powered abrasive wheel, stone, belt, paste, sheet, compound, slurry, etc. Takes various forms: surface grinding (creates flat and/or squared surfaces); cylindrical grinding (for external cylindrical and tapered shapes, fillets, undercuts, etc.); centerless grinding; chamfering; thread and form grinding; tool and cutter grinding; offhand grinding; lapping and polishing (grinding with extremely fine grits to create ultrasmooth surfaces); honing; and disc grinding.
- grinding machine
grinding machine
Powers a grinding wheel or other abrasive tool for the purpose of removing metal and finishing workpieces to close tolerances. Provides smooth, square, parallel and accurate workpiece surfaces. When ultrasmooth surfaces and finishes on the order of microns are required, lapping and honing machines (precision grinders that run abrasives with extremely fine, uniform grits) are used. In its “finishing” role, the grinder is perhaps the most widely used machine tool. Various styles are available: bench and pedestal grinders for sharpening lathe bits and drills; surface grinders for producing square, parallel, smooth and accurate parts; cylindrical and centerless grinders; center-hole grinders; form grinders; facemill and endmill grinders; gear-cutting grinders; jig grinders; abrasive belt (backstand, swing-frame, belt-roll) grinders; tool and cutter grinders for sharpening and resharpening cutting tools; carbide grinders; hand-held die grinders; and abrasive cutoff saws.
- gundrill
gundrill
Self-guided drill for producing deep holes with good accuracy and fine surface finish. Has coolant passages that deliver coolant to the tool/workpiece interface at high pressure.
- hardness
hardness
Hardness is a measure of the resistance of a material to surface indentation or abrasion. There is no absolute scale for hardness. In order to express hardness quantitatively, each type of test has its own scale, which defines hardness. Indentation hardness obtained through static methods is measured by Brinell, Rockwell, Vickers and Knoop tests. Hardness without indentation is measured by a dynamic method, known as the Scleroscope test.
- high-speed steels ( HSS)
high-speed steels ( HSS)
Available in two major types: tungsten high-speed steels (designated by letter T having tungsten as the principal alloying element) and molybdenum high-speed steels (designated by letter M having molybdenum as the principal alloying element). The type T high-speed steels containing cobalt have higher wear resistance and greater red (hot) hardness, withstanding cutting temperature up to 1,100º F (590º C). The type T steels are used to fabricate metalcutting tools (milling cutters, drills, reamers and taps), woodworking tools, various types of punches and dies, ball and roller bearings. The type M steels are used for cutting tools and various types of dies.
- inches per minute ( ipm)
inches per minute ( ipm)
Value that refers to how far the workpiece or cutter advances linearly in 1 minute, defined as: ipm = ipt 5 number of effective teeth 5 rpm. Also known as the table feed or machine feed.
- inner diameter ( ID)
inner diameter ( ID)
Dimension that defines the inside diameter of a cavity or hole. See OD, outer diameter.
- interpolation
interpolation
Process of generating a sufficient number of positioning commands for the servomotors driving the machine tool so the path of the tool closely approximates the ideal path. See CNC, computer numerical control; NC, numerical control.
- jig
jig
Tooling usually considered to be a stationary apparatus. A jig assists in the assembly or manufacture of a part or device. It holds the workpiece while guiding the cutting tool with a bushing. A jig used in subassembly or final assembly might provide assembly aids such as alignments and adjustments. See fixture.
- metal-removal rate
metal-removal rate
Rate at which metal is removed from an unfinished part, measured in cubic inches or cubic centimeters per minute.
- metalworking
metalworking
Any manufacturing process in which metal is processed or machined such that the workpiece is given a new shape. Broadly defined, the term includes processes such as design and layout, heat-treating, material handling and inspection.
- micron
micron
Measure of length that is equal to one-millionth of a meter.
- milling
milling
Machining operation in which metal or other material is removed by applying power to a rotating cutter. In vertical milling, the cutting tool is mounted vertically on the spindle. In horizontal milling, the cutting tool is mounted horizontally, either directly on the spindle or on an arbor. Horizontal milling is further broken down into conventional milling, where the cutter rotates opposite the direction of feed, or “up” into the workpiece; and climb milling, where the cutter rotates in the direction of feed, or “down” into the workpiece. Milling operations include plane or surface milling, endmilling, facemilling, angle milling, form milling and profiling.
- modular design ( modular construction)
modular design ( modular construction)
Manufacturing of a product in subassemblies that permits fast and simple replacement of defective assemblies and tailoring of the product for different purposes. See interchangeable parts.
- outer diameter ( OD)
outer diameter ( OD)
Dimension that defines the exterior diameter of a cylindrical or round part. See ID, inner diameter.
- payload ( workload)
payload ( workload)
Maximum load that the robot can handle safely.
- polycrystalline cubic boron nitride ( PCBN)
polycrystalline cubic boron nitride ( PCBN)
Cutting tool material consisting of polycrystalline cubic boron nitride with a metallic or ceramic binder. PCBN is available either as a tip brazed to a carbide insert carrier or as a solid insert. Primarily used for cutting hardened ferrous alloys.
- robotics
robotics
Discipline involving self-actuating and self-operating devices. Robots frequently imitate human capabilities, including the ability to manipulate physical objects while evaluating and reacting appropriately to various stimuli. See industrial robot; robot.
- sawing machine ( saw)
sawing machine ( saw)
Machine designed to use a serrated-tooth blade to cut metal or other material. Comes in a wide variety of styles but takes one of four basic forms: hacksaw (a simple, rugged machine that uses a reciprocating motion to part metal or other material); cold or circular saw (powers a circular blade that cuts structural materials); bandsaw (runs an endless band; the two basic types are cutoff and contour band machines, which cut intricate contours and shapes); and abrasive cutoff saw (similar in appearance to the cold saw, but uses an abrasive disc that rotates at high speeds rather than a blade with serrated teeth).
- superalloys
superalloys
Tough, difficult-to-machine alloys; includes Hastelloy, Inconel and Monel. Many are nickel-base metals.
- tapping
tapping
Machining operation in which a tap, with teeth on its periphery, cuts internal threads in a predrilled hole having a smaller diameter than the tap diameter. Threads are formed by a combined rotary and axial-relative motion between tap and workpiece. See tap.
- total indicator runout ( TIR)
total indicator runout ( TIR)
Combined variations of all dimensions of a workpiece, measured with an indicator, determined by rotating the part 360°.
- turning
turning
Workpiece is held in a chuck, mounted on a face plate or secured between centers and rotated while a cutting tool, normally a single-point tool, is fed into it along its periphery or across its end or face. Takes the form of straight turning (cutting along the periphery of the workpiece); taper turning (creating a taper); step turning (turning different-size diameters on the same work); chamfering (beveling an edge or shoulder); facing (cutting on an end); turning threads (usually external but can be internal); roughing (high-volume metal removal); and finishing (final light cuts). Performed on lathes, turning centers, chucking machines, automatic screw machines and similar machines.
- waterjet cutting
waterjet cutting
Fine, high-pressure (up to 50,000 psi or greater), high-velocity jet of water directed by a small nozzle to cut material. Velocity of the stream can exceed twice the speed of sound. Nozzle opening ranges from between 0.004" to 0.016" (0.l0mm to 0.41mm), producing a very narrow kerf. See AWJ, abrasive waterjet.