While great for increasing productivity, customized automation systems might simply be out of reach for some shops’ budgets. Fortunately, alternatives exist—ones that don’t involve paying operators to load and unload parts for their entire shift. Modular automation allows machine shops to increase efficiency without paying top dollar for customized systems.
These modular systems come in many forms, from pallet loaders to conveyers to self-contained machine cells. “Automation has been around since the 1960s, and today I can leave my office, drive 10 miles in any direction and probably find an integrator that can build me an advanced, custom automation system to accommodate whatever job I’m doing,” said John Roskos, product manager at machine tool builder GF Machining Solutions LLC, Lincolnshire, Ill. “What a modular system offers is more flexible, scalable automation, without the added costs that come with custom engineering.”
Loading Up
GF Machining Solutions sells its Transformer system, a modular automatic loader capable of serving multiple machines. Originally developed for tool, mold and die shops to transfer electrodes manufactured on CNC mills to EDMs, the system has been scaled up to the point where the largest pallets are capable of handling 440 lbs. (200 kg) and is appropriate for job shops, Roskos said.
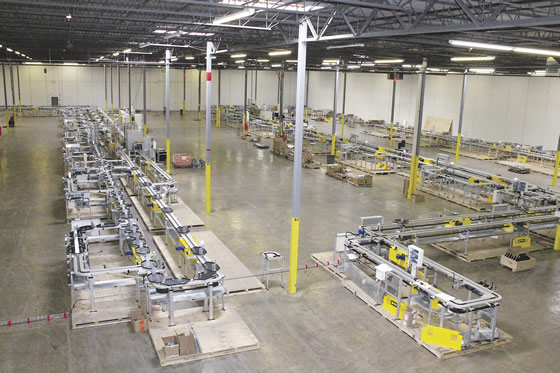
Wes-Tech Automation’s Tech-Trak Mega Modules can be assembled into a conveyor system.
“We’ll build a solution for you, but we’re not engineering it from the ground up,” he explained. “We’ll look at your application—part size, cycle times, machine tools—and come up with a unique cell using standard components.”
The goal is to eliminate production bottlenecks, Roskos added. Because many shops only run a single shift, the machine where the bottleneck occurs can be connected to a Transformer loading system, which lets the machine run overnight.
Because the Transformer’s 2.5-axis rotary loader can feed multiple machines, he continued, shops can then look for other bottlenecks and bring those machines into the cell as well. The system can load as many machines as can be fit within 370° and 60 " (1,524mm) of the loader’s travel. If the cell expands beyond that, a linear track can be added between machines to extend that reach. And when jobs change and new bottlenecks arise, the cell can be reconfigured.
“Job shops’ workloads are constantly changing,” Roskos said. “The system might be loading one machine today, but in 6 months that job is over; with a modular solution, other machines can be moved into the cell for the next job.”
Pallet Pals
While the Transformer loads and unloads palletized workpieces and changes workholding, machine tool builder Okuma America Corp., Charlotte, N.C., offers another option. Its Palletace system, built by Tampere, Finland-based Fastems, is a flexible manufacturing system that stores and moves those pallets.
“Let’s say you have a horizontal machining center with 10 or 12 dedicated jobs,” said Rod Tojdowski, senior manager, applications engineering for Okuma. “Instead of tearing off the old fixture, putting the next fixture on, indicating it, setting it up and proving everything out, you can set an FMS in front of the machine and program it to run the jobs in the order you need.”
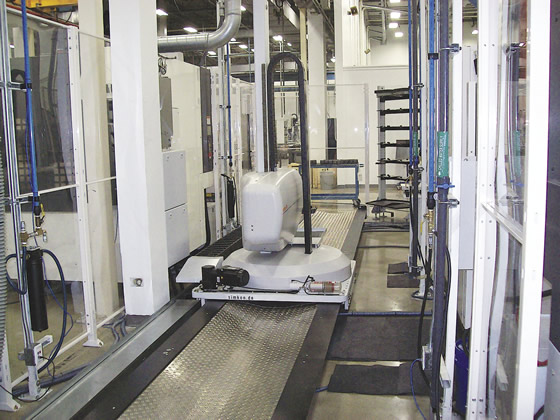
Left: The GF Machining Solutions Transformer robotic loading system at the former Rexam Mold Manufacturing plant in Buffalo Grove, Ill., now owned by Berry Plastics, loads parts and tooling from two rotary turrets into a variety of machines placed around its track. Top: A double gripper on the Transformer robot.
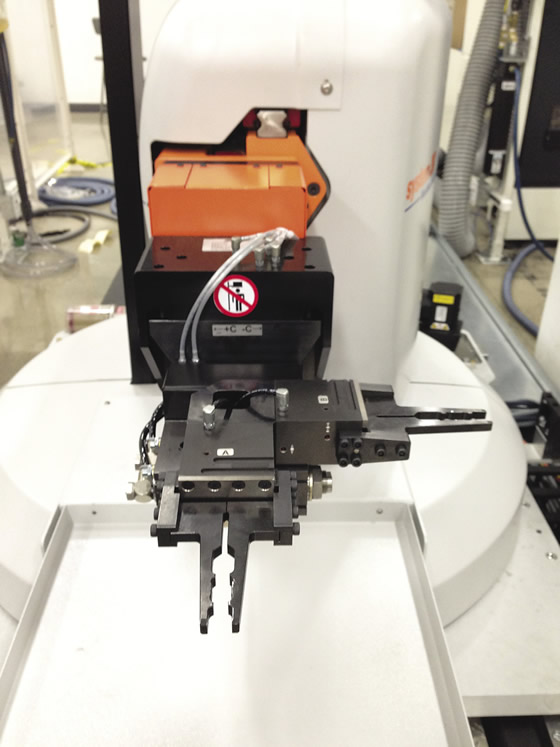
The Palletace FMS, he continued, allows machine operators to schedule jobs one after another, setting up the fixturing and tooling, feeding the pallets, running the job and cycling to the next one. As long as it has jobs programmed and pallets to load, the systems can run virtually nonstop. After an initial setup and prove-out for new jobs, subsequent runs are automatic.
“What sets Palletace apart is the modularity,” Tojdowski said. “If you were to add a second machine, you’d be able to add a second Palletace container very easily, without buying an additional cell controller.” At that point, two machines can run unattended as long as the pallets are loaded. Depending on the size of the machines and the jobs, a third machine can be added to the cell without adding a third container. “In some cases, you might even be able to run multiple machines from just one container. You just need to specify which job goes to which machine and the system takes care of the rest,” he added, noting up to three Palletace systems can be linked on the same controller.
Jobs with short cycle times or that rarely repeat may not see significant efficiency gains, but longer, repeat jobs do because Palletace eliminates the need for an operator to perform basic job setups, according to Tojdowski. While the Palletace clientele has historically been large companies with big budgets, he said the line has been gaining popularity with smaller shops.
Building Blocks
Conveyors are another key part of automation systems, but most systems are custom built. Wes-Tech Automation Solutions, Buffalo Grove, Ill., launched its Tech-Trak Mega Modules at IMTS 2014, a palletized conveyer system comprised of standard modules that can be linked in many configurations.
“We’ve been in business for almost 40 years and have had conveyor products for almost 30 of them,” said Technical Sales Engineering Manager Bill Bauer. “The typical way we had been building our conveyors was like an Erector set, where we would start with individual pieces, then put each conveyor together piece by piece according to customer specifications.”
While such an engineered solution delivers exactly what the customer needs, it takes longer to design and build a custom system from scratch. Wes-Tech noticed that a lot of customers ended up using similar automation modules, so the company standardized those modules, assigning each one a single catalog number. This allows customers to assemble different configurations and rearrange them as needed.
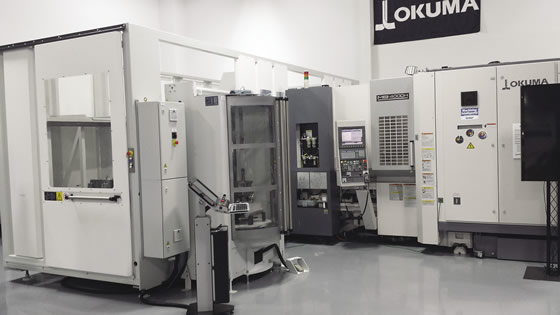
Okuma’s Palletace, shown here (left) with an Okuma MB-4000H horizontal machining center (right), is capable of feeding various jobs to multiple machines 24/7, allowing for lights-out manufacturing and switching from one job to another.
“Now you’re not building with an Erector set, you’re building with kits of Legos, which is much easier and less expensive. It cuts down on installation and design time,” Bauer said.
With Tech-Trak Mega Module conveyers, lines can be comprised of only standard modules or can include standard and custom modules. A conveyer system can be retrofitted to handle any of the 20 standard pallet sizes the company offers, Bauer said. The modules are stackable and fit within a standard cargo container (see photo on page 61) because each module’s footprint is less than 8 '×20 " (2.4m × 6.1m).
“This system lends itself more to higher-volume scenarios, where customers are pumping out hundreds or thousands of parts in a day,” Bauer said. “If parts need to be transported between sequential operations in a two-step process, that’s usually fairly simple; but if there are multiple machine tools performing the same operations, routing the part from one machine to another in a multistep process gets more complicated. The Mega Modules let you route parts from a single operation or a single load point to wherever they need to be.”
Robo-Shop
But what about nonpalletized parts? Naturally, there are automation solutions that specialize in part handling. Fuji Machine America Corp., Vernon Hills, Ill., offers two distinct takes on modularity.
The company’s single-turret ANS and double-turret ANW lines are conventional machine tools offering large-envelope, high-horsepower machining, while the DLFn line is made up of compact modules—each one measures 450mm × 3,960mm (17.7 "×156 ")—designed to handle parts up to 8 " (203.2mm) in diameter. However, according to William S. Gore, regional sales manager, nearly every Fuji machine comes with an integrated robot.
“From the time a raw blank enters the line, our machines perform virtually every job needed,” he said. “From drilling to milling to turning to even some gear hobbing and parts washing, you have the ability to qualify each part as it passes through the system into auto gaging.”
ANS/ANW modules include fully-articulated robots that load the raw part into the machine, retrieve the machined part and pass it to the next machine.
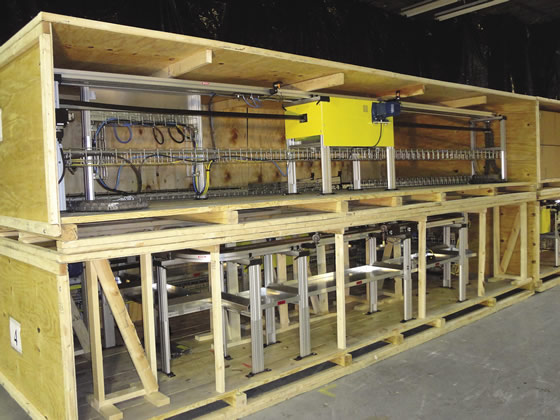
Wes-Tech’s Mega Modules fit into standard storage containers for easy shipping.
“There are multiple ways to load raw material into the work nest, from which it enters the machine,” Gore explained. This includes work stockers, which stack and palletize, and conveyer systems, which “singulate” raw components, feed them into magazines and then feed a part into the system. “It all depends at what point in the flow a part is when it gets to our line. But between the loader and unloader, the whole string of machines is fully automated and self-enclosed.”
In addition, auto-gaging stations can be added to any machine line, allowing for measurement and tool wear auto compensation.
The company’s DLFn line can also include several machine modules tended by robots, but shrinks the system down from conventional, auto-loaded CNC machine tools. Up to 10 modules can be strung together. Turning, milling, measurement, loading, unloading are available, with part washing and gear hobbing modules in development for U.S. release. A robot can serve up to four machining modules, plus a loading or unloading module.
“These robots will reach out and ‘shake hands’ with each other, reaching past the machine they are attached to in order to take a part directly from another,” Gore said. “With the DLFn line, the handshake happens between, say, modules No. 5 and No. 6, and the reason for that is takt time: If you had one robot traversing between 10 different modules, the robot could never keep up with the short cutting time. So, we have deliberately put in that limitation to maximize efficiency.”
Modular automation allows for parallel operations, Gore continued. “Let’s say op-10 (an industry term for the first operation in the process) takes 60 seconds, and op-20 (the second operation) takes 30 seconds,” he said. “When a part is finished on op-20, that machine will sit idle for 30 seconds until the next part is completed in op-10. That’s lost time. With a modular system, you can have two machines in the line, one with an op-10a and the other with an op-10b, so that it’s balanced. By doubling the number of machines, you cut the time in half, so your op-10 is feeding a part every 30 seconds, matching the op-20 spindle cut time.”
If initial volume requirements don’t merit that extra productivity from a second op-10 module, the second machine can be added later when production volume increases. This means shops need not invest in a complete automation system from the outset.
Granted, there are downsides to modular automation. GF’s Transformer isn’t equipped for parts handling, making it unsuitable for high-speed production. Okuma’s Palletace is good for recurring jobs, but one-offs will see sharply diminished returns. Wes-Tech’s Tech-Trak Mega Modules will likely have a bigger footprint than a custom-engineered conveyer, an issue where floor space is at a premium.
However, these modular systems allow machine shops to quickly integrate automation, with installation occurring in weeks rather than months. By making the technology more accessible, modular solutions have the potential to help automate shops of different sizes. cte
Contributors
Fuji Machine America Corp.
(847) 821-2432
www.fujimachine.com
GF Machining Solutions LLC
(847) 913-5300
www.gfms.com/us
Okuma America Corp.
(704) 588-7000
www.okuma.com
Wes-Tech Automation Solutions
(847) 541-5070
www.wes-tech.com
Related Glossary Terms
- computer numerical control ( CNC)
computer numerical control ( CNC)
Microprocessor-based controller dedicated to a machine tool that permits the creation or modification of parts. Programmed numerical control activates the machine’s servos and spindle drives and controls the various machining operations. See DNC, direct numerical control; NC, numerical control.
- feed
feed
Rate of change of position of the tool as a whole, relative to the workpiece while cutting.
- fixture
fixture
Device, often made in-house, that holds a specific workpiece. See jig; modular fixturing.
- flexible manufacturing system ( FMS)
flexible manufacturing system ( FMS)
Automated manufacturing system designed to machine a variety of similar parts. System is designed to minimize production changeover time. Computers link machine tools with the workhandling system and peripherals. Also associated with machine tools grouped in cells for efficient production. See cell manufacturing.
- flexible manufacturing system ( FMS)2
flexible manufacturing system ( FMS)
Automated manufacturing system designed to machine a variety of similar parts. System is designed to minimize production changeover time. Computers link machine tools with the workhandling system and peripherals. Also associated with machine tools grouped in cells for efficient production. See cell manufacturing.
- gang cutting ( milling)
gang cutting ( milling)
Machining with several cutters mounted on a single arbor, generally for simultaneous cutting.
- machining center
machining center
CNC machine tool capable of drilling, reaming, tapping, milling and boring. Normally comes with an automatic toolchanger. See automatic toolchanger.
- milling
milling
Machining operation in which metal or other material is removed by applying power to a rotating cutter. In vertical milling, the cutting tool is mounted vertically on the spindle. In horizontal milling, the cutting tool is mounted horizontally, either directly on the spindle or on an arbor. Horizontal milling is further broken down into conventional milling, where the cutter rotates opposite the direction of feed, or “up” into the workpiece; and climb milling, where the cutter rotates in the direction of feed, or “down” into the workpiece. Milling operations include plane or surface milling, endmilling, facemilling, angle milling, form milling and profiling.
- parallel
parallel
Strip or block of precision-ground stock used to elevate a workpiece, while keeping it parallel to the worktable, to prevent cutter/table contact.
- turning
turning
Workpiece is held in a chuck, mounted on a face plate or secured between centers and rotated while a cutting tool, normally a single-point tool, is fed into it along its periphery or across its end or face. Takes the form of straight turning (cutting along the periphery of the workpiece); taper turning (creating a taper); step turning (turning different-size diameters on the same work); chamfering (beveling an edge or shoulder); facing (cutting on an end); turning threads (usually external but can be internal); roughing (high-volume metal removal); and finishing (final light cuts). Performed on lathes, turning centers, chucking machines, automatic screw machines and similar machines.