Most cutting tools are coated via the physical vapor deposition process but chemical vapor deposition still has its place, depending on the application. A PVD coating is effective, for example, when endmilling, where a tool heats and cools as it enters and exits the cut, but a CVD coating better protects turning tools, which are in constant contact with the workpiece, said Martin Gardner, global product manager for ATI Stellram. “If we want to rough machine something, then we tend to use CVD because of the amount of heat being generated.”
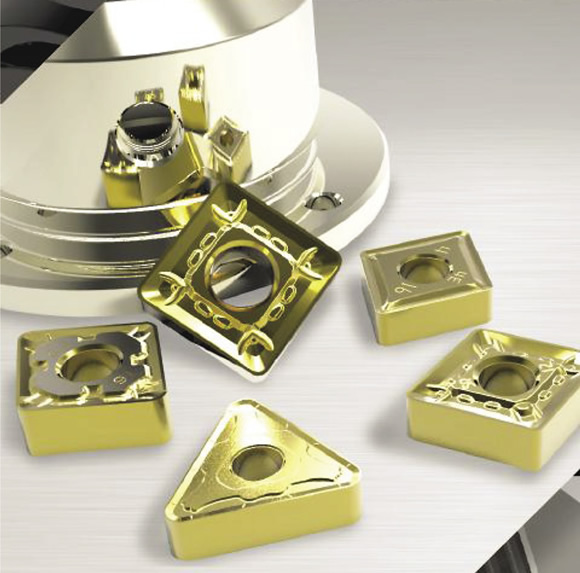
The NL turning inserts from ATI Stellram have a thick CVD coating applied with a new process to control layer thickness.
Gardner added that conventional CVD coatings are from 9µm to 12µm thick, but the toolmaker developed an advanced CVD coating process that deposits multilayer coatings from 20µm to 25µm thick for its five new NL grade turning inserts: NL200, NL250, NL300, NL400 and NL920. The NL grades have a combination of four or five coating layers to suit specific applications, such as NL200 for cast iron.
The five layers are a TiN adhesion and finishing layer, a medium-temperature TiCN layer for wear resistance at high temperatures, a hard alpha-Al2O3 layer with a thermal barrier to resist wear at high surface speeds, a TiN/medium-temperature TiCN/TiN layer for adhesion and wear resistance and a high-temperature TiCN/TiN layer for adhesion and wear resistance at low to medium surface speeds.
To provide an overall thicker CVD coating, Gardner said the new deposition process properly mixes the coatings so they adhere to the substrate and other coatings without chipping or flaking.
In addition, the CVD coating process, combined with innovative geometries, reduces the kinetic friction between the workpiece and insert to potentially achieve 20 to 30 percent higher material-removal rates, finer surface finishes and longer tool life, according to the company. Gardner pointed out that there are two forms of friction: kinetic and static. An example of static friction occurs when someone tries to slide two objects past each other, such as a box on a table, and a small amount of force on the box results in no motion. “That’s static friction holding it in place and some gravity as well,” he said.
Kinetic friction, on the other hand, is when someone applies a little more force and the object “breaks free” and slides, which requires a continual application of force to keep the object sliding.
The same applies to a turning operation, Gardner noted, where a tool flows into the workpiece and stays in contact with the material, making it softer and easier to cut while reducing static friction and kinetic friction. The company’s enhanced surface layering process reportedly reduces static and kinetic friction to improve surface finish and tool life.
The rougher the surfaces of the two objects, the greater the friction. Therefore, Gardner pointed out that ATI Stellram also performs a post-coating surface-treatment process to impart a smooth, “jewelry-like” finish on the inserts and help improve friction resistance. This treatment also relieves the stress inside a CVD-coated insert, he added. “It’s natural for that coating to want to shrink around the substrate like shrink wrap and put it under tension,” Gardner said. “The substrate wants to go the other way and get out of there. The stress relieving we do inside the insert helps produce a better product.”
For more information about ATI Stellram, La Vergne, Tenn., call (800) 232-1200 or visit www.atistellram.com.
Related Glossary Terms
- chemical vapor deposition ( CVD)
chemical vapor deposition ( CVD)
High-temperature (1,000° C or higher), atmosphere-controlled process in which a chemical reaction is induced for the purpose of depositing a coating 2µm to 12µm thick on a tool’s surface. See coated tools; PVD, physical vapor deposition.
- chemical vapor deposition ( CVD)2
chemical vapor deposition ( CVD)
High-temperature (1,000° C or higher), atmosphere-controlled process in which a chemical reaction is induced for the purpose of depositing a coating 2µm to 12µm thick on a tool’s surface. See coated tools; PVD, physical vapor deposition.
- endmilling
endmilling
Operation in which the cutter is mounted on the machine’s spindle rather than on an arbor. Commonly associated with facing operations on a milling machine.
- physical vapor deposition ( PVD)
physical vapor deposition ( PVD)
Tool-coating process performed at low temperature (500° C), compared to chemical vapor deposition (1,000° C). Employs electric field to generate necessary heat for depositing coating on a tool’s surface. See CVD, chemical vapor deposition.
- physical vapor deposition ( PVD)2
physical vapor deposition ( PVD)
Tool-coating process performed at low temperature (500° C), compared to chemical vapor deposition (1,000° C). Employs electric field to generate necessary heat for depositing coating on a tool’s surface. See CVD, chemical vapor deposition.
- stress relieving
stress relieving
Annealing designed to relieve internal stresses caused by machining, welding, casting, cold working, quenching or normalizing.
- titanium carbonitride ( TiCN)
titanium carbonitride ( TiCN)
Often used as a tool coating. See coated tools.
- titanium nitride ( TiN)
titanium nitride ( TiN)
Added to titanium-carbide tooling to permit machining of hard metals at high speeds. Also used as a tool coating. See coated tools.
- turning
turning
Workpiece is held in a chuck, mounted on a face plate or secured between centers and rotated while a cutting tool, normally a single-point tool, is fed into it along its periphery or across its end or face. Takes the form of straight turning (cutting along the periphery of the workpiece); taper turning (creating a taper); step turning (turning different-size diameters on the same work); chamfering (beveling an edge or shoulder); facing (cutting on an end); turning threads (usually external but can be internal); roughing (high-volume metal removal); and finishing (final light cuts). Performed on lathes, turning centers, chucking machines, automatic screw machines and similar machines.
- wear resistance
wear resistance
Ability of the tool to withstand stresses that cause it to wear during cutting; an attribute linked to alloy composition, base material, thermal conditions, type of tooling and operation and other variables.