Like most machine tool builders, Mori Seiki Co. Ltd. is focused on making its machines more energy efficient. In addition, the company is focused on making the factories that make those machines more energy efficient. For example, Nagoya, Japan-based Mori Seiki is implementing energy-reduction programs and equipment at its operations in Iga, Japan.
The Iga campus’ goal is to reduce electricity consumption by 30 percent in 2013 compared to 2012. The campus has already reduced energy consumption 10 percent by installing high-efficiency air conditioners, switching from mercury lamps to high-efficiency fluorescent lamps and operating compressors more efficiently.
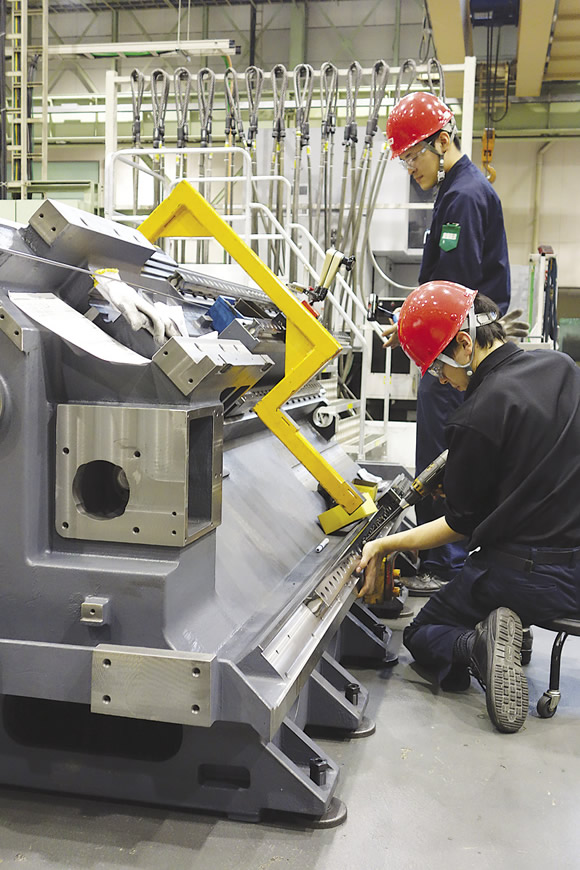
Workers install linear guide ways at Mori Seiki’s Iga plant.
Also, Mori Seiki has installed a photovoltaic solar-energy system made by its partner company Gildemeister AG (DMG), Bielefeld, Germany. Using rails and sensors, the system automatically adjusts the orientation of solar panels according to the position of the sun, which provides 40 percent more power generation efficiency per square meter than a fixed system, according to Gildemeister.
“We are pursuing the installation of solar- and wind-energy systems in other facilities, but it becomes a compromise because we have to pick places where there would be a lot of sun or wind exposure—both systems aren’t always appropriate at each location,” said Gregory Hyatt, vice president and chief technical officer for DMG / Mori Seiki USA, Hoffman Estates, Ill. “We actually have more wind systems in place than solar systems.”
Alternative EnergyDr. Rüdiger Kapitza, chairman of the executive board of DMG, discussed the company’s approach to energy savings at a press conference held jointly with Dr. Masahiko Mori, president of Mori Seiki, at the 26th Japan International Machine Tool Fair, held in November in Tokyo.
Kapitza spoke about the products from three businesses that comprise Gildemeister’s new energy solutions unit: SunCarrier solar power technologies, WindCarrier wind turbines and CellCube high-efficiency battery systems. Kapitza said many emerging markets, such as India, China and Russia, do not have stable energy infrastructures, and such technologies will allow manufacturing facilities located there to generate, store and use renewable energy.
In addition, Mori noted that Mori Seiki’s new machine tool plant in Davis, Calif., was up and running, producing NHX4000 and NHX5000 horizontal machining centers at a rate of 80 units per month. Sites for other new production facilities planned or under construction include Tianjin, China, and Ulyanovsk, Russia. The company’s Seebach, Germany, factory is currently being expanded.
Also, Mori and Kapitza reported that since the cooperative agreement between the two companies began in 2009, more countries have been added each year to the list of where DMG and Mori Seiki cooperate to provide sales and service.
Cells and CampsitesIn addition to focusing on energy efficiency, Mori Seiki’s Iga campus is looking to increase overall manufacturing efficiency. The assembly plant has been using a cellular approach to building machine tools since 2002. In cellular production, one worker is responsible for multiple assembly processes, which eliminates lost time between processes. This leads to a significant reduction in lead time from order to product shipment. For example, shipment time (the time needed to build a machine) has been cut in half, from 8 days to 4 days.
Also, the Iga assembly plant features a “campsite” system. In this system, the plant is divided into separate sites, each of which focuses on building different types of machines, such as lathes, horizontal machining centers or vertical machining centers. For example, one section of the factory uses the campsite method for machines involved in high-volume manufacturing of automotive parts so the Mori Seiki team can observe its machines in an environment similar to those of its customers. Those observations can lead to process improvements.
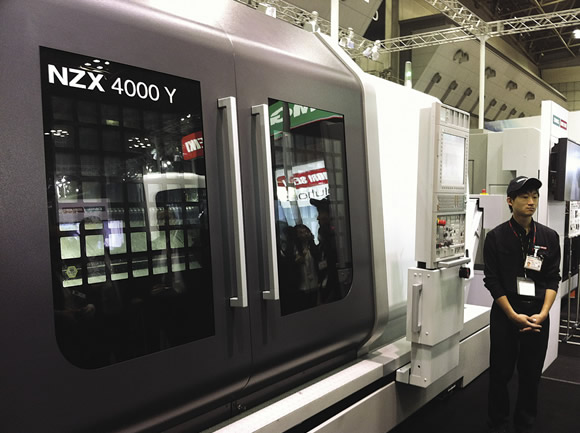
The Mori Seiki NZX4000Y multiaxis turning center can machine workpieces up to 900mm in diameter and 4,000mm long.
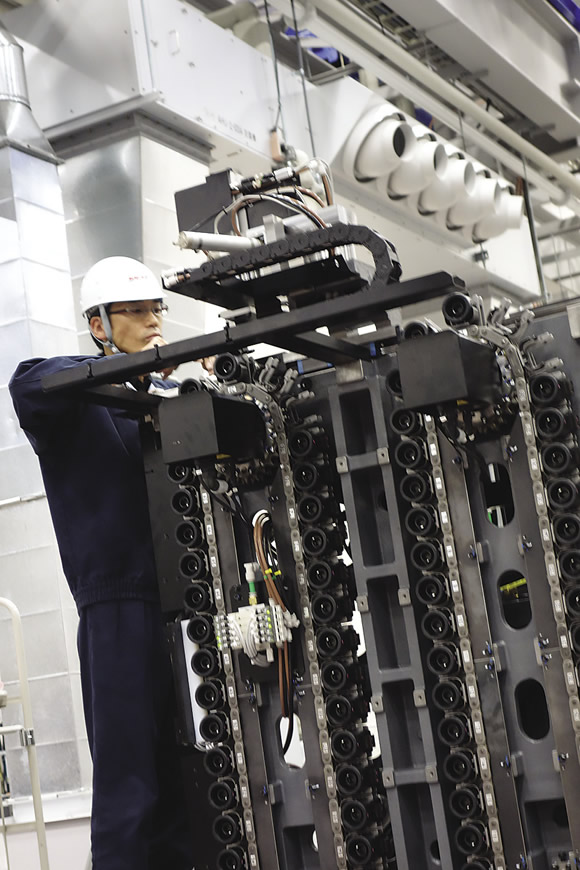
A worker assembles a tool magazine.
By using the campsite system and cellular production, Mori Seiki says it can increase productivity compared to systems utilizing conventional assembly lines. Also, the assembly line method is not suited for short-term or small-lot production of many products.
“On an assembly line, it becomes impossible to balance the work being done at each station of the line because the machines are built to customers’ orders,” Hyatt said. “So if you’re building several machines that have a lot of options or specifications, in an assembly line some stations would be underutilized, others would be overutilized and some stations would be waiting on others, which results in inefficiencies.”
However, sometimes assembly lines are the right system for specific jobs. For example, a turret assembly line at Iga makes it easier to control the manufacturing process by limiting the scope of what has to be done in a campsite. “By building all the turrets, which are not affected by specific machine configurations, on dedicated assembly lines, you’re making the process more efficient,” Hyatt said. This has increased production efficiency, cutting assembly time by 25 percent compared to the previous system.
The Iga plant also manufactures direct-drive motors, which transmit drive power directly to the spindle. This is done without gears, increasing efficiency and eliminating backlash, according to the company.
Machining PlantThe campus also includes a machining plant for multiple-item, small-lot production of almost all of the parts for its machine tools, according to Hyatt. “While some builders that specialize in design and assembly farm out most of the machining of their components, we machine the vast majority of the components that go into our machines, such as bits, columns, turrets, spindles and ballscrews,” he said. “We are very vertically integrated.”
Machines used in this production system include an NHX10000 horizontal milling machine, a DMG DMC 210 FD 5-axis CNC machine, a DIXI DHP100 II milling machine and a universal grinding center.
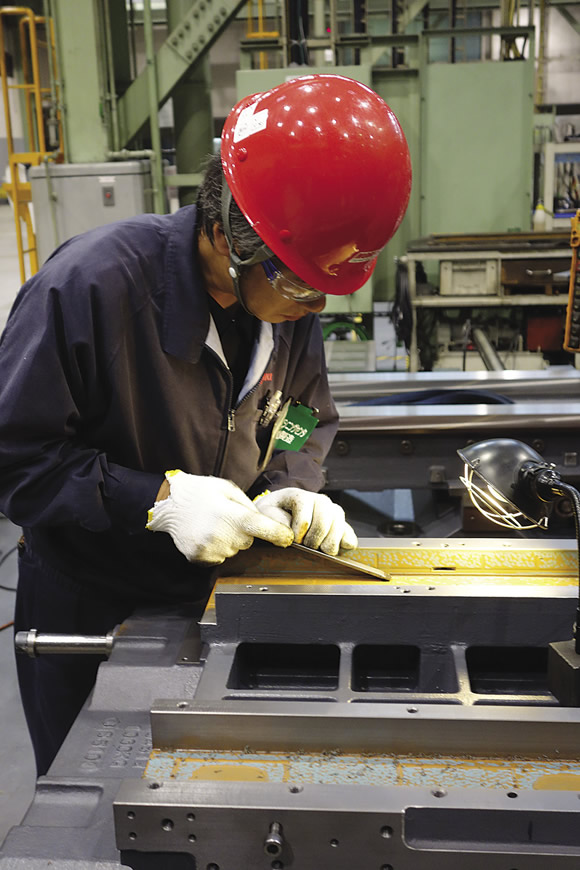
A worker hand scrapes critical mating surfaces.
The Iga plant also has a machining laboratory where machines are operated under the same conditions as at a customer’s site to be able to conduct practical assessments of machine accuracy and maintainability.
The campus has a 112,000-sq.-ft. spindle plant that performs turning and grinding. Established in 2006, the spindle plant improves component quality by creating an integrated system, from parts machining to assembly and inspection. Spindle assembly is performed in a cleanroom.
Also on the campus is a 33,000-sq.-ft. ballscrew plant that can complete a standard ballscrew in 7 days. Maximum production capacity is 2,800 per month.
The Iga campus also includes a casting plant, heat-treatment plant, development center, 24/7 service center and guest house. CTE
About the Author: Yesenia Salcedo is a senior editor with CTE and MICROmanufacturing magazines. Telephone: (847) 714-0177. E-mail: [email protected].
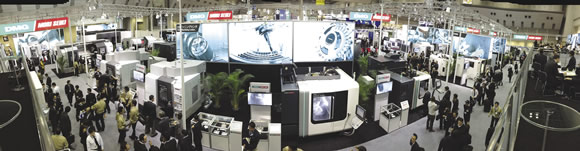
The 25,000-sq.-ft. DMG / Mori Seiki booth at JIMTOF 2012 showcased 32 machines.
JIMTOF attendance tops 118,000
booth at JIMTOF had the opportunity to view Cutting Dream Contest entries on display. Sponsored by Mori Seiki and in its ninth iteration, the contest, which rewards innovative design, is open to Japanese companies, schools and research institutions engaged in machining. This year’s contest drew about 100 entries, showcasing the skill and creativity involved in using machine tools, according to Mori Seiki.
A panel of five judges reviewed entries in several categories, including prototype and test-cut machining; die and mold/free-form machining; and micromachining. Winning entries received cash prizes and awards at a ceremony held during JIMTOF.
—Y. Salcedo
Iga campus quick facts
is the company’s largest production site. Several components make up the approximately 6.2-million-sq.-ft. site, which serves as the company’s main base for manufacturing, R&D, service and education. The factory has 460 pieces of equipment for machining, grinding, welding and pressing. Production capacity is about 350 machines per month, including multiaxis turning centers, CNC lathes, 5-axis vertical machining centers and 5-axis horizontal machining centers. The plant has 1,456 employees, representing about one third of all Mori Seiki employees.
Related Glossary Terms
- backlash
backlash
Reaction in dynamic motion systems where potential energy that was created while the object was in motion is released when the object stops. Release of this potential energy or inertia causes the device to quickly snap backward relative to the last direction of motion. Backlash can cause a system’s final resting position to be different from what was intended and from where the control system intended to stop the device.
- centers
centers
Cone-shaped pins that support a workpiece by one or two ends during machining. The centers fit into holes drilled in the workpiece ends. Centers that turn with the workpiece are called “live” centers; those that do not are called “dead” centers.
- computer numerical control ( CNC)
computer numerical control ( CNC)
Microprocessor-based controller dedicated to a machine tool that permits the creation or modification of parts. Programmed numerical control activates the machine’s servos and spindle drives and controls the various machining operations. See DNC, direct numerical control; NC, numerical control.
- gang cutting ( milling)
gang cutting ( milling)
Machining with several cutters mounted on a single arbor, generally for simultaneous cutting.
- grinding
grinding
Machining operation in which material is removed from the workpiece by a powered abrasive wheel, stone, belt, paste, sheet, compound, slurry, etc. Takes various forms: surface grinding (creates flat and/or squared surfaces); cylindrical grinding (for external cylindrical and tapered shapes, fillets, undercuts, etc.); centerless grinding; chamfering; thread and form grinding; tool and cutter grinding; offhand grinding; lapping and polishing (grinding with extremely fine grits to create ultrasmooth surfaces); honing; and disc grinding.
- milling
milling
Machining operation in which metal or other material is removed by applying power to a rotating cutter. In vertical milling, the cutting tool is mounted vertically on the spindle. In horizontal milling, the cutting tool is mounted horizontally, either directly on the spindle or on an arbor. Horizontal milling is further broken down into conventional milling, where the cutter rotates opposite the direction of feed, or “up” into the workpiece; and climb milling, where the cutter rotates in the direction of feed, or “down” into the workpiece. Milling operations include plane or surface milling, endmilling, facemilling, angle milling, form milling and profiling.
- milling machine ( mill)
milling machine ( mill)
Runs endmills and arbor-mounted milling cutters. Features include a head with a spindle that drives the cutters; a column, knee and table that provide motion in the three Cartesian axes; and a base that supports the components and houses the cutting-fluid pump and reservoir. The work is mounted on the table and fed into the rotating cutter or endmill to accomplish the milling steps; vertical milling machines also feed endmills into the work by means of a spindle-mounted quill. Models range from small manual machines to big bed-type and duplex mills. All take one of three basic forms: vertical, horizontal or convertible horizontal/vertical. Vertical machines may be knee-type (the table is mounted on a knee that can be elevated) or bed-type (the table is securely supported and only moves horizontally). In general, horizontal machines are bigger and more powerful, while vertical machines are lighter but more versatile and easier to set up and operate.
- turning
turning
Workpiece is held in a chuck, mounted on a face plate or secured between centers and rotated while a cutting tool, normally a single-point tool, is fed into it along its periphery or across its end or face. Takes the form of straight turning (cutting along the periphery of the workpiece); taper turning (creating a taper); step turning (turning different-size diameters on the same work); chamfering (beveling an edge or shoulder); facing (cutting on an end); turning threads (usually external but can be internal); roughing (high-volume metal removal); and finishing (final light cuts). Performed on lathes, turning centers, chucking machines, automatic screw machines and similar machines.