Manufacturing higher-quality and more complex cut, stamped, deep-drawn and formed sheet metal parts while minimizing tool wear is a major challenge. The challenge is magnified when processing high-strength steels, such as 1.4310 spring steel. The modular hy-PRESS laser-assisted machining press upgrade from Fraunhofer Institute for Production Technology enables manufacturers to achieve those goals, according to Markus Eckert, group leader of laser system technology and medicine technology at Fraunhofer IPT.
“We can achieve up to a 100 percent clear-cut surface ratio with a conventional shearing process,” he said, noting that such a high-quality cut typically requires a costly fine-blanking process. “And, on the other side, we are able to increase the formability of the material.” For example, Fraunhofer IPT engineers reportedly reduced the bending radius of a 1mm-thick sheet of spring steel from 2mm to 0.25mm in the rolling direction of the sheet.
In another application, the laser- assisted machining press system embossed high-strength materials, raising surface areas about 50 percent without damaging the embossing tools, Eckert noted. “With a conventional tool and a conventional press, you can’t emboss high-strength materials because the hardness of the material is higher than the hardness of the tool, so you emboss the tool and not the material,” he explained. “The [hy-PRESS upgrade] widens the borders of sheet metal working processes.”
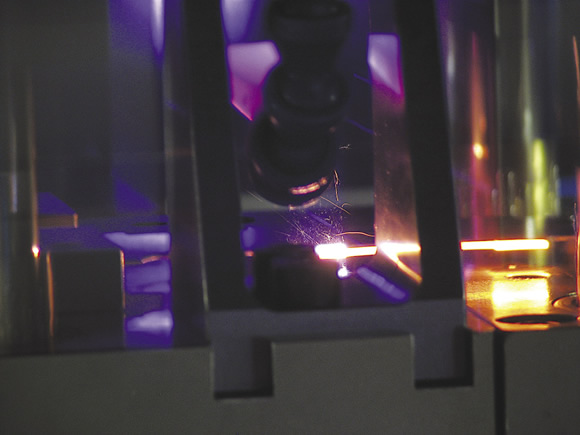
Courtesy of Fraunhofer Institute for Production Technology
Laser-assisted sheet metal working using the hy-PRESS system (below) from Fraunhofer IPT creates surfaces with continuously smooth cuts.
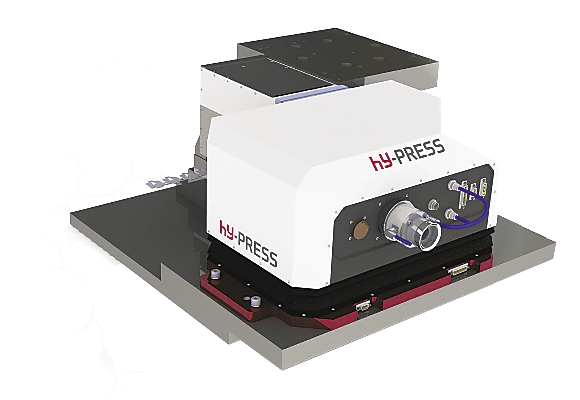
The Fraunhofer IPT reported that a hybrid oscillation decoupling system permits highly dynamic, high-power laser scanners to be integrated within progressive dies, allowing heat to be flexibly applied to selected areas of the workpiece. The heat softens localized areas of the workpiece material, reducing its strength while increasing formability.
The laser scanner uses two retaining mirrors to deflect the laser beam and move its focus at more than 20 m/sec. over the workpiece surface. “The speed is so high that the whole area is nearly heated at once,” Eckert said. “This allows us to flexibly irradiate nearly every geometry within the working area.”
The hy-PRESS system, which can be integrated into new presses or retrofit into existing presses, is suitable for processing a range of materials, including aluminum, copper and titanium. The Fraunhofer IPT has performed tests on sheet metal up to 12mm thick but found the best results with materials from 0.5mm to 4mm thick, Eckert noted. He added that in field trials, the system extended tool life up to 50 percent.
The institute collaborated with German metal parts producer Scheuermann + Heilig GmbH, which is using the press technology in a production environment.
For more information, contact Fraun-hofer Institute for Production Technology, Aachen, Germany, at +49 241 8904-319 or www.ipt.fraunhofer.de. CTE
Related Glossary Terms
- hardness
hardness
Hardness is a measure of the resistance of a material to surface indentation or abrasion. There is no absolute scale for hardness. In order to express hardness quantitatively, each type of test has its own scale, which defines hardness. Indentation hardness obtained through static methods is measured by Brinell, Rockwell, Vickers and Knoop tests. Hardness without indentation is measured by a dynamic method, known as the Scleroscope test.
- inches per tooth ( ipt)
inches per tooth ( ipt)
Linear distance traveled by the cutter during the engagement of one tooth. Although the milling cutter is a multi-edge tool, it is the capacity of each individual cutting edge that sets the limit of the tool, defined as: ipt = ipm/number of effective teeth 5 rpm or ipt = ipr/number of effective teeth. Sometimes referred to as the chip load.