When Jasper (Indiana) Engines & Transmissions remanufactures a family of engines or transmissions, the process starts with the new product development division researching popular powertrain products, resolving inherent design issues and determining how to improve a product’s longevity. The process continues with core disassembly; thorough cleaning; machining the block, heads, crankshaft, camshaft and connecting rods; and installation of new, qualified or improved components. The final stage is product-specific testing.
The company’s Wernsing Road facility, which is one of four, remanufactures up to 120 gasoline engines daily. To keep remanufacturing costs competitive, the goal is to qualify and reclaim as many parts from the original engine as possible. Jasper Engines & Transmissions reports that when it rejects core components, it replaces them with core parts and castings from the same engine family or new ones.
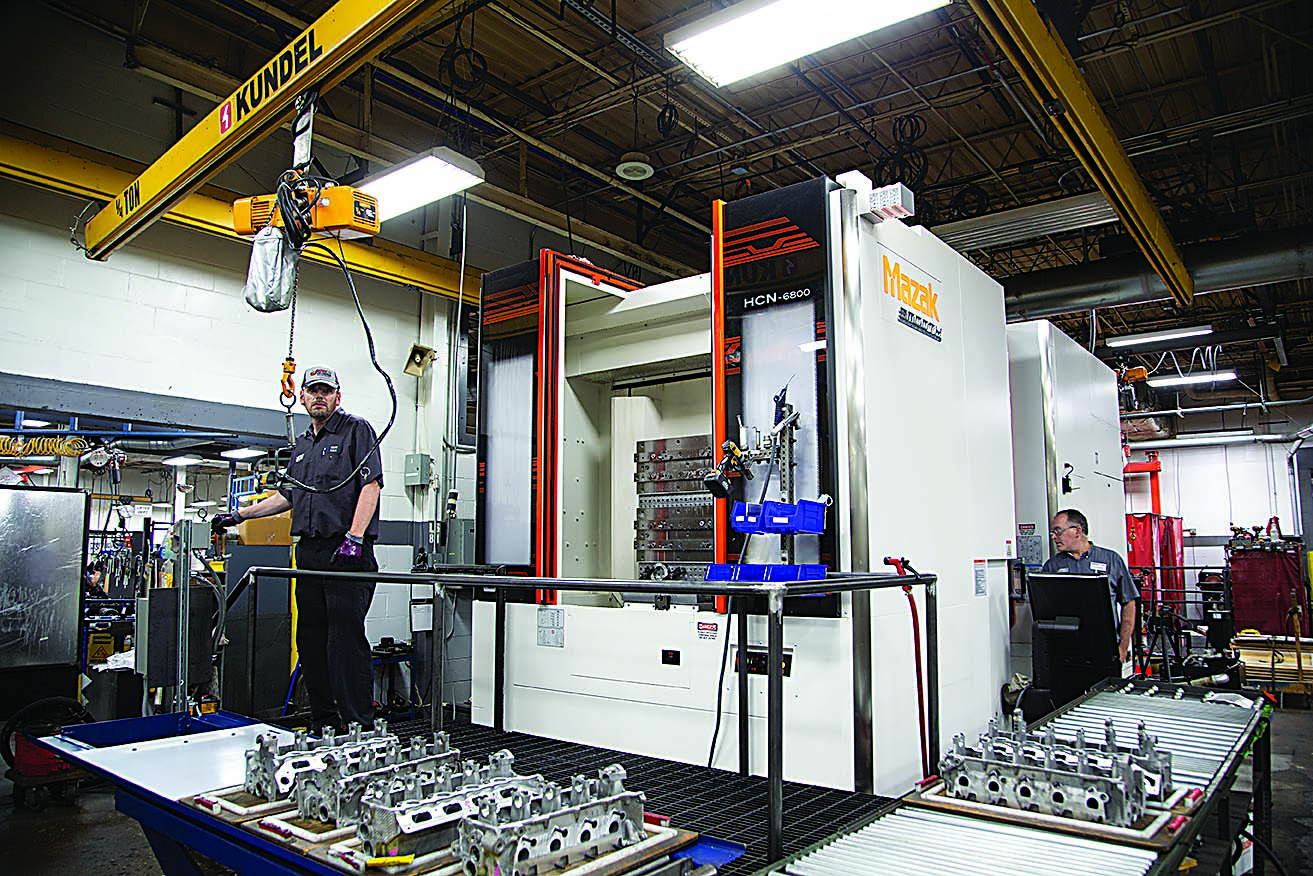
When remanufacturing an overhead cam cylinder head, the production department first oversizes cylinder head cam bores and either builds up camshaft journals or uses a cam-bearing shell in place of the material removed from the bores. Unfortunately, the time required to align camshaft housing bores for specific cylinder heads and meet the company’s production requirements proved to be an ongoing challenge.
Initially, production used right-angle heads on knee mill-type machines and short tools that fit between the cam-bearing caps, the company reported. The one-bore-at-a-time method was unreliable at maintaining concentricity from one bore to the next. Production then modified a gundrilling machine and applied a 762-mm-long (30") single-point line boring and reaming tool. The downside was that this method required manually loading the long, heavy tools — a strenuous task for operators that eventually damaged the machine’s spindle because of excessive wear.
In addition, the manually intensive process produced more rejects than acceptable parts, so Jasper Engines & Transmissions’ production needs still were not being met.
The company determined that it needed a horizontal machining center that could handle the long boring and reaming tools. Already possessing machines built by Mazak Corp. in Florence, Kentucky, including the VC-500A/2PC, VCN-570C and VCN-530C vertical turning centers, as well as the QT-250MSY, QTN-250MSY and QTU-200 multitaskers, Jasper Engines & Transmissions chose Mazak’s HCN-6800 HMC with a two-pallet changer, 80-tool storage capacity and an automatic toolchanger that accommodates 762-mm-long tools, said Garrett Robinson, CNC specialist at Jasper Engines & Transmissions.
Also, the machine’s Mazatrol SmoothG CNC, working in tandem with probing macros that he developed, reportedly significantly reduces the risk of error in part loading and actual machining and frees operators for more value-added tasks.
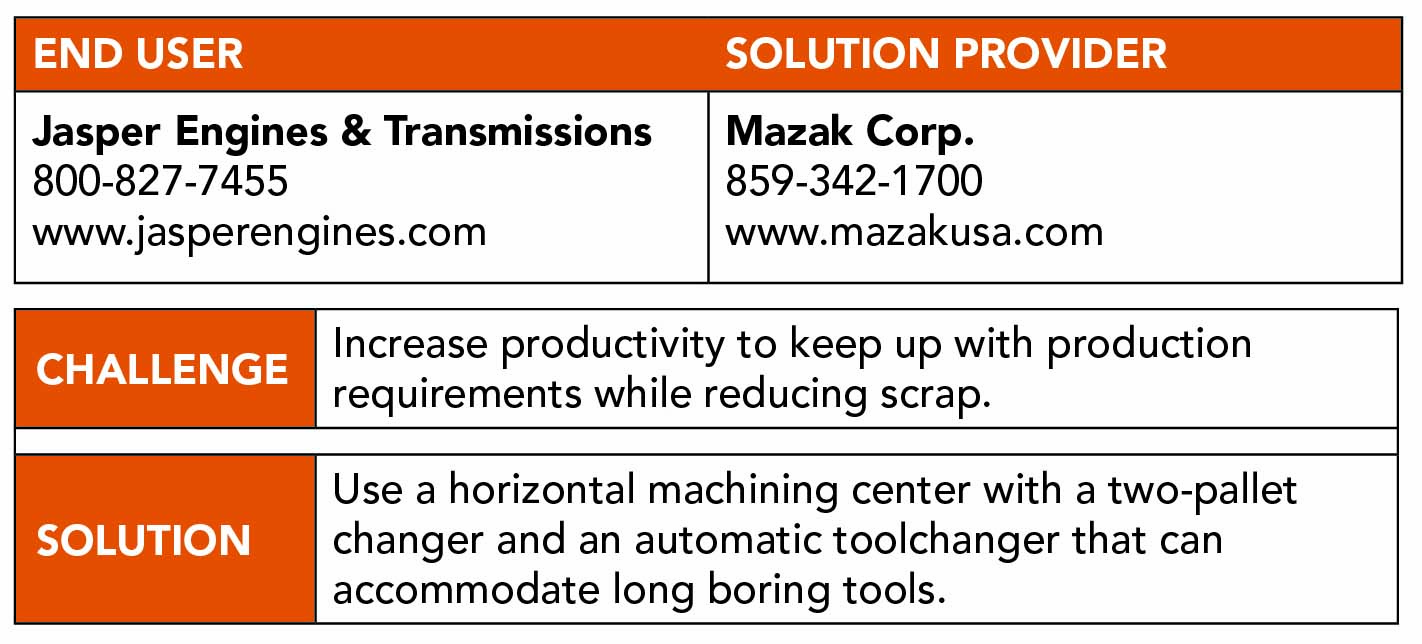
“Prior to the HCN-6800,” Robinson said, “we had to use up to five different processes for oversizing cam bores, and the previous machine lacked the necessary accuracy and speed for the tooling we wanted to use. The HCN-6800 not only allows us to use that tooling but also gives us much better surface finishes and more precise and concentric bores, all at a much faster production level.”
He said the machine also enables Jasper Engines & Transmissions to bore any size overhead camshaft, or OHC, head.
Having a fourth-axis table on the HMC creates a lot of options, including the ability to run up to four parts at a time on two tombstone fixtures, Robinson said. To further automate OHC head machining, his probing routines remove any operator guesswork from identifying and positioning fixtures.
He explained that during a probing routine, the HMC checks for a part in all or any of the four fixture positions. Once the HMC detects a part, the machine runs another touch probe macro to determine which families of heads are clamped on the tombstone. Then the machine selects the appropriate program for the head types, determines how much stock is in the bore and compensates for it by adjusting the speeds and feeds. Because Jasper Engines & Transmissions does not run batches and may have many random variations of the heads that it processes on the machine, this capability it especially beneficial.
“We need machines that are versatile and can handle OHC heads for multiple engine types, along with all their included variations that may be in production at any given time,” Robinson said. “The HCN-6800 allows us to process more parts faster, so our other remanufacturing departments no longer wait for OHC heads.”
With the machine’s control, Jasper Engines & Transmissions can tune the machine for vibration during the cut, adding to the HMC’s ability to consistently hold tight tolerances, said Taylor Friend, a QC captain at the company.
“The HCN-6800 is definitely making my job easier in terms of quality control, mainly because of its high accuracy and repeatability,” he said. “Some of the tolerances we have to hold well below 0.001" (0.0254 mm), and our previous machines produced a lot of rejected parts.”
For more information from Mazak about Jasper Engines & Transmissions, view a video presentation cteplus.delivr.com/25cy5
Contact Details
Related Glossary Terms
- automatic toolchanger
automatic toolchanger
Mechanism typically included in a machining center that, on the appropriate command, removes one cutting tool from the spindle nose and replaces it with another. The changer restores the used tool to the magazine and selects and withdraws the next desired tool from the storage magazine. The changer is controlled by a set of prerecorded/predetermined instructions associated with the part(s) to be produced.
- boring
boring
Enlarging a hole that already has been drilled or cored. Generally, it is an operation of truing the previously drilled hole with a single-point, lathe-type tool. Boring is essentially internal turning, in that usually a single-point cutting tool forms the internal shape. Some tools are available with two cutting edges to balance cutting forces.
- centers
centers
Cone-shaped pins that support a workpiece by one or two ends during machining. The centers fit into holes drilled in the workpiece ends. Centers that turn with the workpiece are called “live” centers; those that do not are called “dead” centers.
- computer numerical control ( CNC)
computer numerical control ( CNC)
Microprocessor-based controller dedicated to a machine tool that permits the creation or modification of parts. Programmed numerical control activates the machine’s servos and spindle drives and controls the various machining operations. See DNC, direct numerical control; NC, numerical control.
- computer-aided manufacturing ( CAM)
computer-aided manufacturing ( CAM)
Use of computers to control machining and manufacturing processes.
- fixture
fixture
Device, often made in-house, that holds a specific workpiece. See jig; modular fixturing.
- gundrilling
gundrilling
Drilling process using a self-guiding tool to produce deep, precise holes. High-pressure coolant is fed to the cutting area, usually through the gundrill’s shank.
- machining center
machining center
CNC machine tool capable of drilling, reaming, tapping, milling and boring. Normally comes with an automatic toolchanger. See automatic toolchanger.
- quality assurance ( quality control)
quality assurance ( quality control)
Terms denoting a formal program for monitoring product quality. The denotations are the same, but QC typically connotes a more traditional postmachining inspection system, while QA implies a more comprehensive approach, with emphasis on “total quality,” broad quality principles, statistical process control and other statistical methods.
- toolchanger
toolchanger
Carriage or drum attached to a machining center that holds tools until needed; when a tool is needed, the toolchanger inserts the tool into the machine spindle. See automatic toolchanger.
- turning
turning
Workpiece is held in a chuck, mounted on a face plate or secured between centers and rotated while a cutting tool, normally a single-point tool, is fed into it along its periphery or across its end or face. Takes the form of straight turning (cutting along the periphery of the workpiece); taper turning (creating a taper); step turning (turning different-size diameters on the same work); chamfering (beveling an edge or shoulder); facing (cutting on an end); turning threads (usually external but can be internal); roughing (high-volume metal removal); and finishing (final light cuts). Performed on lathes, turning centers, chucking machines, automatic screw machines and similar machines.