Besides combining vertical and horizontal five-face milling with vertical turning capabilities, a machine tool from Taiwan-based You Ji Machine Industrial Co. Ltd. is designed to provide rigidity and high torque.
So says Lorain, Ohio-based Absolute Machine Tools Inc., which has added the machine, called the VMT-1000+Y vertical mill/turn center, to its line of large vertical turning lathes from You Ji Machine Industrial. The VMT-1000+Y offers five-sided and 4+1-axis milling and turning of workpieces in a single setup.
“Traditionally, a standard vertical lathe had either two or three axes,” said Klaus Miller, vice president of sales at Absolute Machine Tools. “Not until the last five or six years did they come up to five and even six axes sometimes.”
Absolute Machine Tools points out that the simple design of the five-axis VMT-1000+Y doesn’t require belts and gears for the axes. Instead, servomotors drive 2"-dia. Class 3 precision ballscrews during machining.
Also notable are the heavily ribbed Meehanite castings used to make the machine’s vertical column and base. These castings minimize thermal distortion and dampen vibration, according to the company.
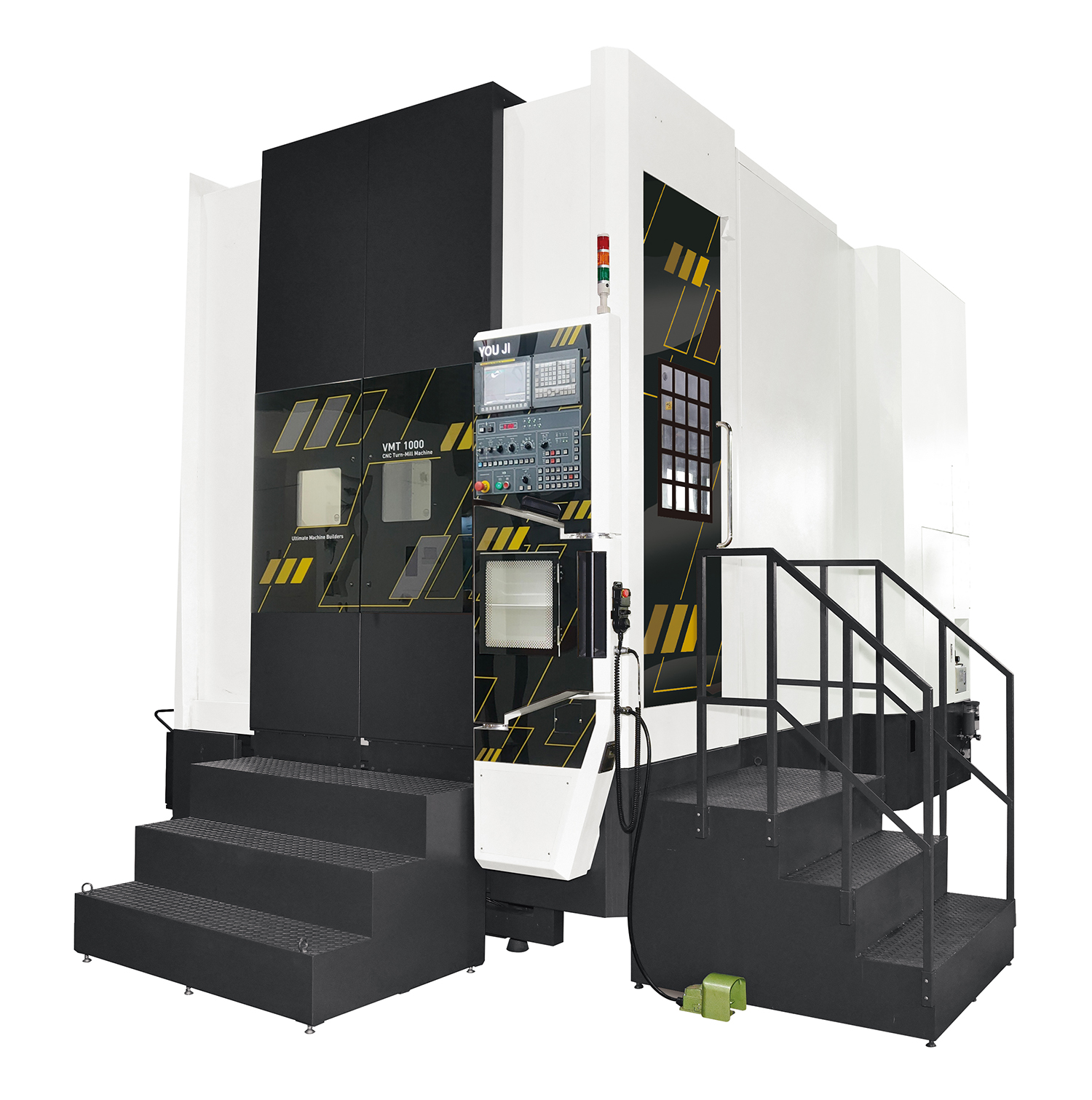
In fact, Miller said one of the main selling points of the machine is its construction. Featuring a rigid box guideway structure, the one-piece unit is built like a boring mill-type column, he noted.
“This is not a light-duty machine,” he said. “It’s an extremely heavy machine, far heavier than other machine tools like this.”
For smooth operation, the machine includes a forced lubrication system. In addition, the mating surfaces of the box guideways are hand-scraped and coated with Turcite-B.
Another feature touted by Absolute Machine Tools is the machine’s 20 hp, 50-taper milling spindle. Powered by a two-speed ZF planetary gearbox spindle drive, the 30 hp double-wound Fanuc P series main spindle motor delivers more torque at lower speeds than a 50 hp single-wound motor, according to the company.
The VMT-1000+Y also includes a standard 24-tool arm-type automatic toolchanger with a 55-lb. tool weight capacity.
Offering a standard turning diameter and maximum turning height of 39.4" (1,000 mm), the machine is suitable for medium-to-large-size workpieces.
“It’s a rather large machine with large capacities,” Miller said.
He noted that the VMT-1000+Y is ideal for machine shops that ordinarily would move parts from a vertical turning lathe to a boring mill.
“It saves time when you no longer have to do a secondary milling operation in another machine tool,” Miller said.
As for applications, he reports that the VMT-1000+Y is becoming popular with pump manufacturers. For this, he credits the vertical turning and milling capabilities, which make it possible to machine multiple sides of a part in one setup.
In addition to pump manufacturers, Miller said a number of companies that make gearboxes and valve bodies have either purchased the machine or shown “very serious interest” in it.
Although Absolute Machine Tools has provided VMT-1000+Y quotes to high-volume manufacturers, he believes that the machine is a better fit for high-mix, low-volume machining operations because it eliminates the need for multiple setups.
In those operations, “you can machine a part complete in one (or) maybe two setups at most,” Miller said.
On the downside, he pointed out that combining milling and turning in a single machine can slow production. The reason, he explained, is that shops that have separate machines for milling and turning can do both simultaneously, but the processes must be done one at a time by an individual mill/turn machine.
With a machine like the VMT-1000+Y, however, Miller said shops are better able to deal with the labor shortage in the machining industry.
“The upside,” he said, “is that you only have one setup and you only need one operator.”
Contact Details
Related Glossary Terms
- automatic toolchanger
automatic toolchanger
Mechanism typically included in a machining center that, on the appropriate command, removes one cutting tool from the spindle nose and replaces it with another. The changer restores the used tool to the magazine and selects and withdraws the next desired tool from the storage magazine. The changer is controlled by a set of prerecorded/predetermined instructions associated with the part(s) to be produced.
- boring
boring
Enlarging a hole that already has been drilled or cored. Generally, it is an operation of truing the previously drilled hole with a single-point, lathe-type tool. Boring is essentially internal turning, in that usually a single-point cutting tool forms the internal shape. Some tools are available with two cutting edges to balance cutting forces.
- gang cutting ( milling)
gang cutting ( milling)
Machining with several cutters mounted on a single arbor, generally for simultaneous cutting.
- lathe
lathe
Turning machine capable of sawing, milling, grinding, gear-cutting, drilling, reaming, boring, threading, facing, chamfering, grooving, knurling, spinning, parting, necking, taper-cutting, and cam- and eccentric-cutting, as well as step- and straight-turning. Comes in a variety of forms, ranging from manual to semiautomatic to fully automatic, with major types being engine lathes, turning and contouring lathes, turret lathes and numerical-control lathes. The engine lathe consists of a headstock and spindle, tailstock, bed, carriage (complete with apron) and cross slides. Features include gear- (speed) and feed-selector levers, toolpost, compound rest, lead screw and reversing lead screw, threading dial and rapid-traverse lever. Special lathe types include through-the-spindle, camshaft and crankshaft, brake drum and rotor, spinning and gun-barrel machines. Toolroom and bench lathes are used for precision work; the former for tool-and-die work and similar tasks, the latter for small workpieces (instruments, watches), normally without a power feed. Models are typically designated according to their “swing,” or the largest-diameter workpiece that can be rotated; bed length, or the distance between centers; and horsepower generated. See turning machine.
- milling
milling
Machining operation in which metal or other material is removed by applying power to a rotating cutter. In vertical milling, the cutting tool is mounted vertically on the spindle. In horizontal milling, the cutting tool is mounted horizontally, either directly on the spindle or on an arbor. Horizontal milling is further broken down into conventional milling, where the cutter rotates opposite the direction of feed, or “up” into the workpiece; and climb milling, where the cutter rotates in the direction of feed, or “down” into the workpiece. Milling operations include plane or surface milling, endmilling, facemilling, angle milling, form milling and profiling.
- milling machine ( mill)
milling machine ( mill)
Runs endmills and arbor-mounted milling cutters. Features include a head with a spindle that drives the cutters; a column, knee and table that provide motion in the three Cartesian axes; and a base that supports the components and houses the cutting-fluid pump and reservoir. The work is mounted on the table and fed into the rotating cutter or endmill to accomplish the milling steps; vertical milling machines also feed endmills into the work by means of a spindle-mounted quill. Models range from small manual machines to big bed-type and duplex mills. All take one of three basic forms: vertical, horizontal or convertible horizontal/vertical. Vertical machines may be knee-type (the table is mounted on a knee that can be elevated) or bed-type (the table is securely supported and only moves horizontally). In general, horizontal machines are bigger and more powerful, while vertical machines are lighter but more versatile and easier to set up and operate.
- toolchanger
toolchanger
Carriage or drum attached to a machining center that holds tools until needed; when a tool is needed, the toolchanger inserts the tool into the machine spindle. See automatic toolchanger.
- turning
turning
Workpiece is held in a chuck, mounted on a face plate or secured between centers and rotated while a cutting tool, normally a single-point tool, is fed into it along its periphery or across its end or face. Takes the form of straight turning (cutting along the periphery of the workpiece); taper turning (creating a taper); step turning (turning different-size diameters on the same work); chamfering (beveling an edge or shoulder); facing (cutting on an end); turning threads (usually external but can be internal); roughing (high-volume metal removal); and finishing (final light cuts). Performed on lathes, turning centers, chucking machines, automatic screw machines and similar machines.