Toolmakers and job coaters can distinguish themselves by quickly and reliably depositing smooth PVD coatings on the cutting tools they produce and process. To achieve that, IHI Hauzer Techno Coating BV developed a new arc technology called Circular Arc Plus, or CARC+, according to Michiel Eerden, product manager for the supplier of coating technology and equipment.
CARC+ can deposit an 80µin. (2µm) layer of AlTiN on the shafts of a batch of tools, corresponding with about 120µin. (3µm) on the cutting edge, in a cycle time of less than 4 hours, the company reported. “With the new CARC+ technology, batch costs improve 44 percent compared with regular circular arc technology,” Eerden said, noting the reduction is based on a shorter cycle time and higher target utilization. “Due to the extremely high target utilization, the target costs per batch are reduced 83 percent.”
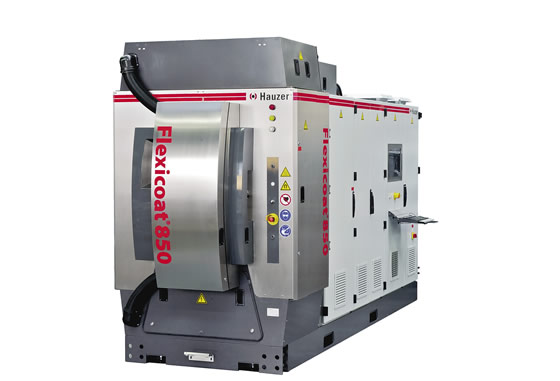
The Hauzer Flexicoat 850 tool coating machine can be upgraded with the company’s CARC+ technology.
He explained that the company optimized the technology’s magnet configuration to create the best balance between low coating roughness and high target utilization, with 50 percent or more of the target weight being consumed before the target must be exchanged. “When comparing the target cost per tool to our competition,” Eerden said, “we outperform them by roughly a factor of two.”
Also outperforming by a factor of two is the new technology’s ability to deposit smoother coatings compared to the company’s previous technology, according to Eerden. For instance, CARC+ can achieve a surface finish of 6.3 µin. (0.16µm) Ra for an 80µin. AlTiN coating. Coatings without a high aluminum content, such as TiN and TiAlN, will be even smoother, because aluminum has a low melting temperature and, therefore, creates more smoothness-impeding metal droplets.
Because the cathode ignition is protected, maintenance is not needed, Eerden noted. Typically, circular arc cathodes are ignited with a trigger in front of the target, leading to continuous coating of the trigger and high maintenance.
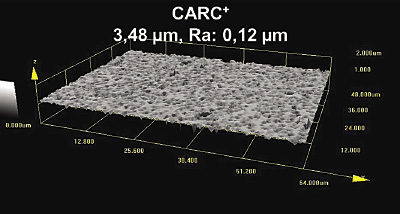
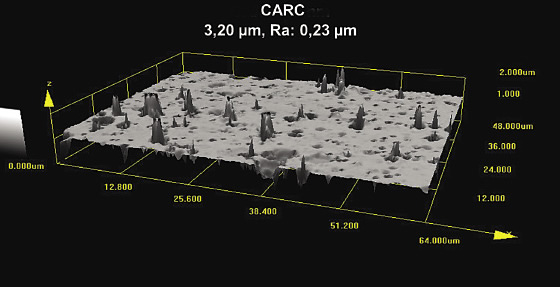
These images were made with a confocal microscope and show the density and height of metal droplets (peaks above the coating) for coatings deposited with two technologies: Hauzer’s CARC+ (3.48µm, or 137.01µin., thick) and CARC, an earlier method (3.20µm, or 125.98µin., thick).
In addition, the technology is stable over a wide pressure range, Eerden said. “We have run our cathode from vacuum [no pressure] up to pressures of approximately 10 mTorr.”
Hauzer’s Flexicoat 850 machine, which has a 15 '×4.6 ' (4.6m × 1.4m) footprint, can be upgraded to enable coating with the new technology. The machine has interchangeable walls, and an existing wall can be exchanged with a wall of CARC+ cathodes. End users must also modify the machine’s control, power supply cabinets and software for the new setup.
“Besides PVD, we have plasma-assisted CVD technologies and plasma nitriding. All these technologies can be combined in one system, which enables deposition of multilayers, superlattices and nanocomposite coatings. We can also do nitriding and PVD/PACVD deposition in one cycle without breaking vacuum between nitriding and coating,” Eerden said. “The flexible configuration offers complete R&D freedom.”
For more information about IHI Hauzer Techno Coating BV, Venlo, The Netherlands, call +31-77-355-97-77 or visit www.hauzertechnocoating.com.
About the Author: Alan Richter is editor of CTE. Contact him at (847) 714-0175 or [email protected].
Related Glossary Terms
- chemical vapor deposition ( CVD)
chemical vapor deposition ( CVD)
High-temperature (1,000° C or higher), atmosphere-controlled process in which a chemical reaction is induced for the purpose of depositing a coating 2µm to 12µm thick on a tool’s surface. See coated tools; PVD, physical vapor deposition.
- nitriding
nitriding
Introducing nitrogen into the surface layer of a solid ferrous alloy. This is done to increase hardness, wear resistance and fatigue strength.
- physical vapor deposition ( PVD)
physical vapor deposition ( PVD)
Tool-coating process performed at low temperature (500° C), compared to chemical vapor deposition (1,000° C). Employs electric field to generate necessary heat for depositing coating on a tool’s surface. See CVD, chemical vapor deposition.
- titanium aluminum nitride ( TiAlN)
titanium aluminum nitride ( TiAlN)
Often used as a tool coating. AlTiN indicates the aluminum content is greater than the titanium. See coated tools.
- titanium nitride ( TiN)
titanium nitride ( TiN)
Added to titanium-carbide tooling to permit machining of hard metals at high speeds. Also used as a tool coating. See coated tools.