Lightweighting isn’t the only method available to improve automotive fuel efficiency. Coating engine components, such as cogs, piston rings and piston pins, with hard carbon reduces friction to almost zero, and researchers at the Fraunhofer Institute for Material and Beam Technology IWS have developed the Laser-Arc module (LAM) to apply the coating on a production line.
“Systematic application of our new method could save more than 100 billion liters of fuel each year over the next 10 years,” said Andreas Leson, the institute’s vice director and department head, referencing a study published in the journal Tribology International.
Carbon-based coatings are already applied in volume production, but the institute researchers, led by Leson, Hans-Joachim Scheibe and Volker Weihnacht, have succeeded in producing hydrogen-free, tetrahedral amorphous carbon (ta-C) coatings on an industrial scale at a consistent quality level. At 40 to 70 GPa, these Diamor-trademarked coatings are significantly harder, and therefore more resistant to wear, than conventional diamond-like coatings, according to the institute.
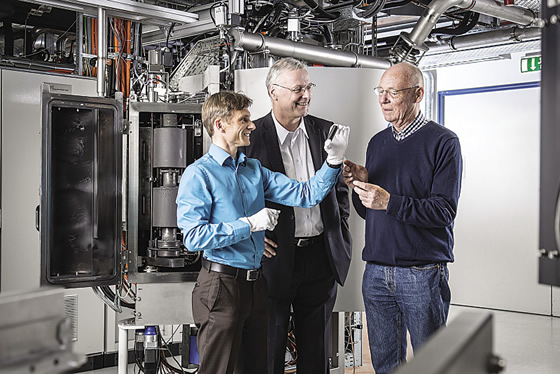
Volker Weihnacht, Andreas Leson and Hans-Joachim Scheibe (left to right) of Fraunhofer IWS developed a Laser-Arc method for depositing diamond-like coatings on components. Image courtesy Dirk Mahler/Fraunhofer.
“Unfortunately, you can’t just scrape off diamond dust and press it onto a component, so we had to look for a different method,” Scheibe said.
Similar to a film projector, LAM generates an arc between an anode and a cathode (the carbon) in a vacuum, the researchers explained. The arc is initiated by a laser pulse on the carbon target. This produces a plasma that consists of carbon ions, and the plasma is deposited as a coating on the workpiece in a vacuum.
To run the process on an industrial scale, a pulsed laser is vertically scanned across a rotating graphite cylinder to control the arc. To ensure a consistently smooth coating, a magnetic field guides the plasma and filters any dirt particles.
The method deposits ta-C coatings up to 20µm (0.0008 ") thick. “High coating thicknesses are crucial for certain applications, especially in the auto industry, where components are exposed to enormous loads over long periods of time,” Weihnacht said.
The Laser-Arc tech-nology is modular so as to ensure independence from any specific coating machine, according to the institute. The LAM 500 was designed for a coating height of 500mm (19.7 ") to be suitable for PVD batch coating processes used in toll coating services. All basic functions of the PVD coater, such as vacuum generation, part movement and plasma cleaning, remain intact and undisturbed.
Fraunhofer reports that automotive and motorcycle manufacturer BMW is working on industrial-scale implementation of ta-C-coated engine parts for its various models to reduce fuel consumption.
In addition to automotive, suitable applications for the coating technology include milling cutters and drills, medical implants, protective films on temperature-sensitive materials and components for the food processing and packaging industries.
For more information about Fraunhofer Institute for Material and Beam Technology IWS, Dresden, Germany, call +49 351-83391-0 or visit www.iws.fraunhofer.de. CTE
Related Glossary Terms
- amorphous
amorphous
Not having a crystal structure; noncrystalline.
- gang cutting ( milling)
gang cutting ( milling)
Machining with several cutters mounted on a single arbor, generally for simultaneous cutting.
- milling
milling
Machining operation in which metal or other material is removed by applying power to a rotating cutter. In vertical milling, the cutting tool is mounted vertically on the spindle. In horizontal milling, the cutting tool is mounted horizontally, either directly on the spindle or on an arbor. Horizontal milling is further broken down into conventional milling, where the cutter rotates opposite the direction of feed, or “up” into the workpiece; and climb milling, where the cutter rotates in the direction of feed, or “down” into the workpiece. Milling operations include plane or surface milling, endmilling, facemilling, angle milling, form milling and profiling.
- physical vapor deposition ( PVD)
physical vapor deposition ( PVD)
Tool-coating process performed at low temperature (500° C), compared to chemical vapor deposition (1,000° C). Employs electric field to generate necessary heat for depositing coating on a tool’s surface. See CVD, chemical vapor deposition.