If you’re interested in boosting efficiency and cutting costs — and what manufacturer isn’t? — creating a work cell may very well be worth your while. Today, the task often involves acquiring some form of robotic assistance. To those put off by this idea, some experts point out that the current crop of factory robots includes those designed with cost-conscious and complexity-averse buyers in mind.
For those unfamiliar with the concept, a work cell is an arrangement of manufacturing resources aimed at reducing production time and costs while also increasing product quality. Based on the principles of lean manufacturing, work cells are designed to achieve these goals by
improving the flow of production processes and eliminating waste.
Work cells take manufacturers in a direction opposite that in which they traditionally moved. In the past, those that wanted to increase their production capabilities would keep building additional facilities and adding employees, noted Andrew Rowley, general sales manager at SW North America Inc. in New Hudson, Michigan, a supplier of CNC machining centers, automation and complete system solutions. But with building costs skyrocketing and labor becoming more expensive and harder to find, production processes have to become more compact and more efficient — and that’s where work cells come in.
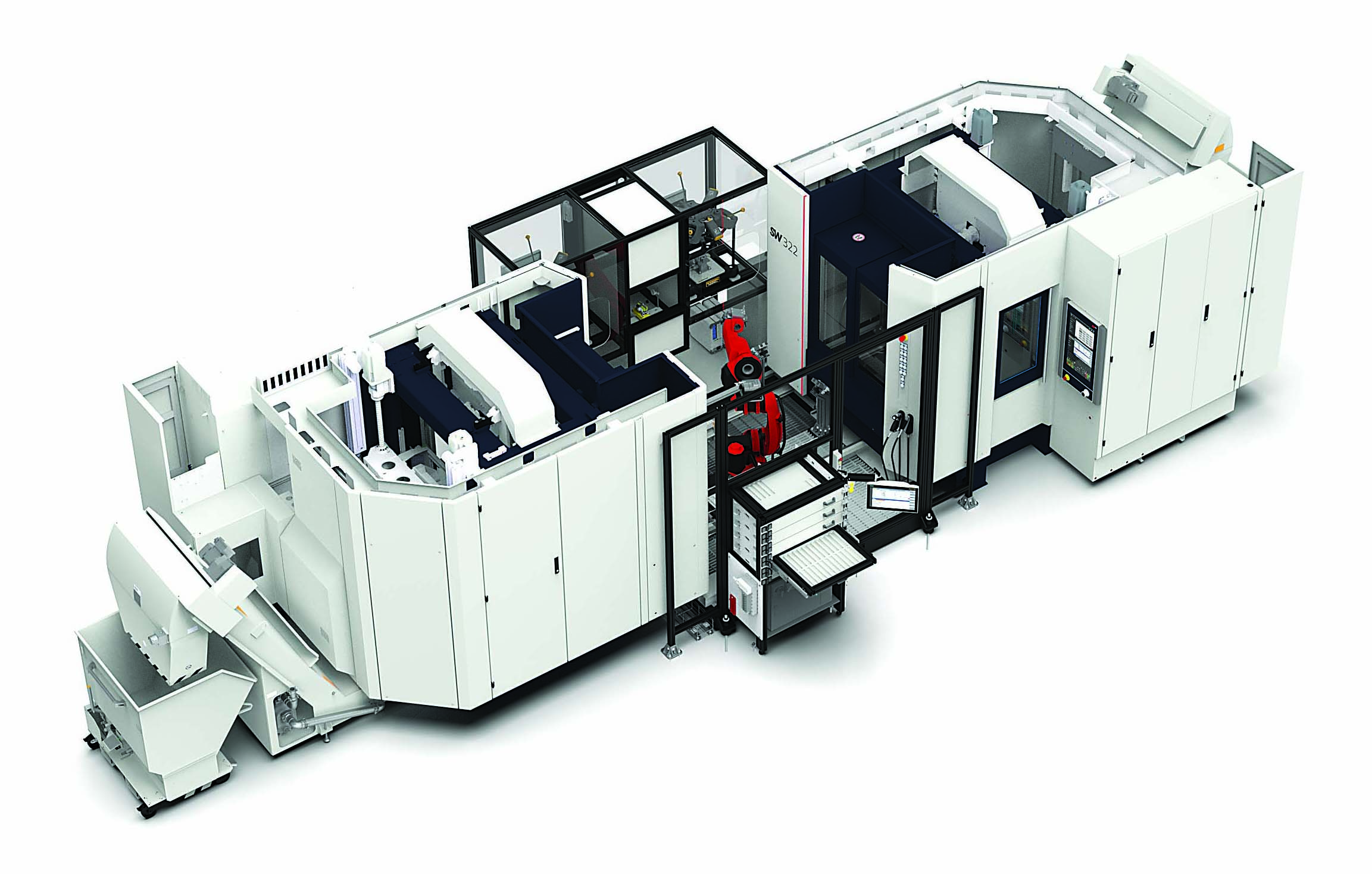
“With a work cell, you’re trying to get everything completed in a limited amount of floor space and with a limited amount of human or operator engagement,” Rowley said.
That means workers don’t have to walk across the shop floor or to adjacent buildings to accomplish different tasks involved in completing a production process.
“You want to try to make it like an assembly line — nice and efficient,” said Joe Sanders, sales engineering assistant manager at Mazak Corp., a machine manufacturer in Florence, Kentucky.
With less space and fewer employees involved in manufacturing, product costs go down, Rowley said, which gives companies more opportunities to make competitive bids for new business. In addition, he pointed out that the less parts are handled during production, the better part quality tends to be.
Automation Boom
Today, many work cells include some form of automation. Before the pandemic, Rowley reports that SW customers weren’t asking for automation.
“They used to be able to just throw bodies at a machine,” he said.
But with workers becoming scarce and expensive, interest in automation has spiked, he noted. And once customers decide to automate, they start considering all the possibilities for a robot on the shop floor.
“So now you’re looking at a work cell where the robot can do not only machine tending but also additional work like laser marking and deburring,” he said. “And then operators are available to do a higher level of work.”
Relieved of menial and time-consuming production tasks, machinists are freed up to take on more cerebral and creative work, such as programming, setting up new jobs and creating jigs and fixtures, said Craig Zoberis, founder and president of RoboJob-USA in Burr Ridge, Illinois, a systems integrator of robotic automation for CNC mills and lathes.
Once shops decide to add automation to a work cell, one of the first questions they have to answer is how much they want to spend on it. According to Sanders, a low-end option would be a simple cobot, which could handle some basic tasks but would still leave shop floor personnel with plenty to do. At the higher end would be customized systems featuring an industrial robot capable of handling operations such as gauging, laser marking and cleaning, in addition to machine tending.
SW uses simulation software to come up with appropriate automation solutions for specific work cells.
“We look at how much can we do with automation and how much would there still have to be human interaction in that cell,” Rowley said. “Then we calculate the costs for the customer.”
Generally speaking, Rowley said those costs can range from less than $100,000 for a low-end cobot-based cell to millions of dollars for a large, fully integrated automated cell. As for the time it takes to produce an automated cell from concept to completion, he added, that normally ranges roughly from 30-some weeks to a year. This includes the time it takes to get a clear understanding of a customer’s needs and design the appropriate automation system, as well as the wait for system components to become available.
“There are still a lot of lead time issues in today’s market,” Rowley said. “There are certain robots that can take us a year to get. Others we can buy pretty much off the shelf.”
No matter what type of automation system is installed, it won’t have an entirely positive impact on a production process if shop personnel believe it’s simply a means of cutting staff or that it takes away from their jobs. So Sanders pointed out that management must sell automation to workers, telling them it will add to their skill sets and make them more efficient so the company can compete more effectively with other firms.
By making it clear to people that they’ll be trained to do more than just operate a machine and move parts in and out of it, management can turn automation into a net plus in its dealings with both current and potential employees, Zoberis said.
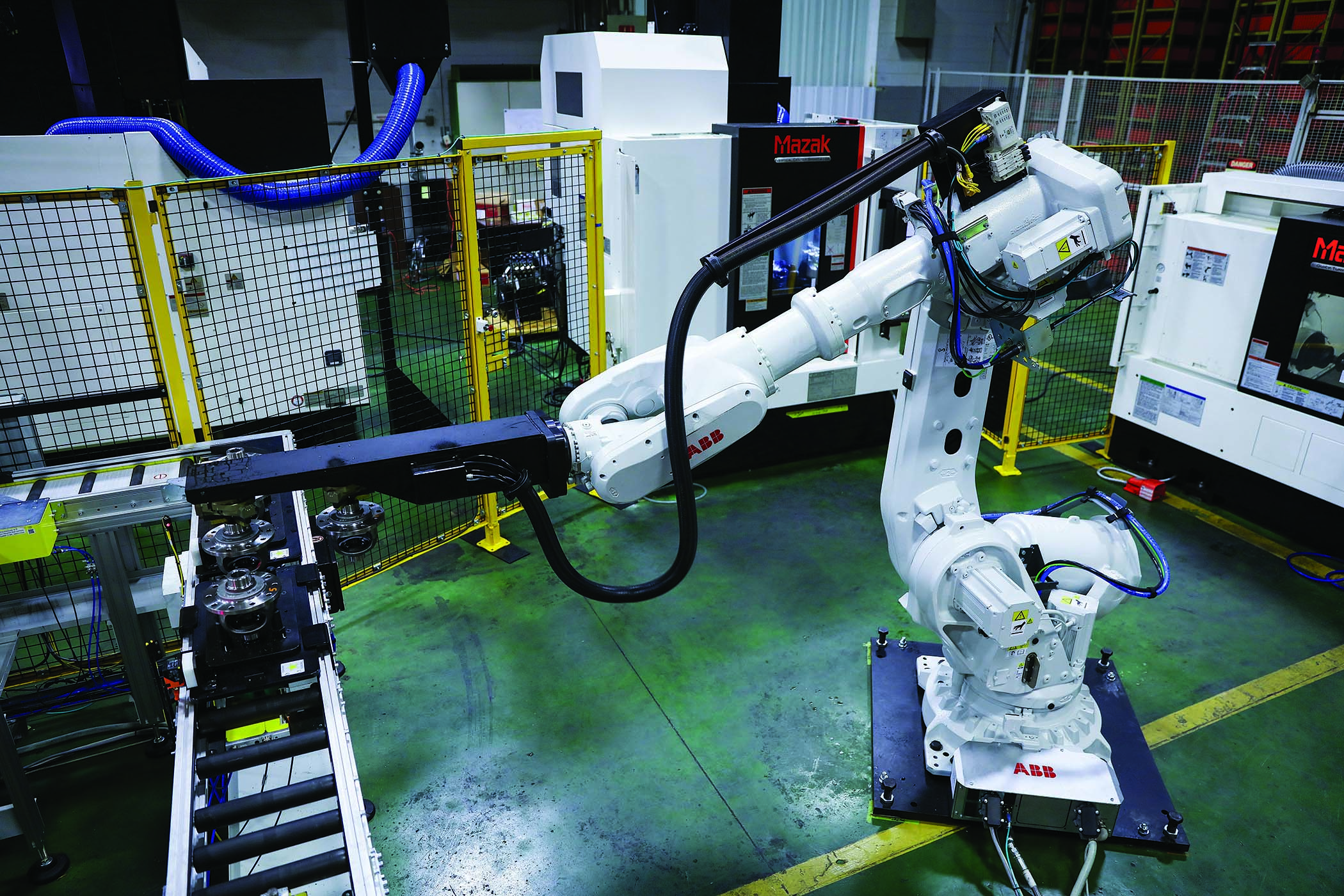
Handled the right way, he said, “robotic automation is not just a retention factor for keeping good personnel. It’s a factor for attracting the right talent to work in the organization.”
Normally, SW asks customers to choose one person as the lead in their automation project and then send that person to its facility for a few days of training while work on their cell is in its final stages. SW typically also requests that the chosen person be sent to an automation school run by robot suppliers, such as Fanuc or ABB, for a few days of additional training. Rowley believes that this type of training regimen is “pretty standard” for all companies that supply automation solutions.
Reaping the Benefits
How much of a difference can an automated work cell make in a manufacturing operation? Rowley cites a customer that had a traditional workflow that required parts to be taken by operators to nine different stations.
By modernizing this work cell and combining operations, he said, “we were able to (turn) that workflow into a centralized system so that one work cell was able to produce what nine individual cells were producing.”
As a result, he reported, the number of workers required for the process dropped from 18 to two and the floor space needed was reduced by two-thirds.
In this case, the automation design consists of an overhead gantry for machine tending and a cobot system on the floor that handles tasks, such as laser marking, part washing and packaging.
“So the customer basically drops raw parts in and completed parts come out,” Rowley said.
Of course, the benefits of adding automation to a work cell don’t always justify it when measured against the costs.
“If I’ve got only 10 parts and they take me five minutes to make, do I take the time and spend the money to automate? Of course not,” Sanders said. “But if I’m doing 5,000 of them and they take two hours to make, I want to be more efficient with my time, and that justifies it.”
In cases where the right choice isn’t clear-cut, a cost analysis must be done to determine whether work cell automation is worthwhile. The automation could be as simple as an auto chuck or a bar feeder, Sanders noted.
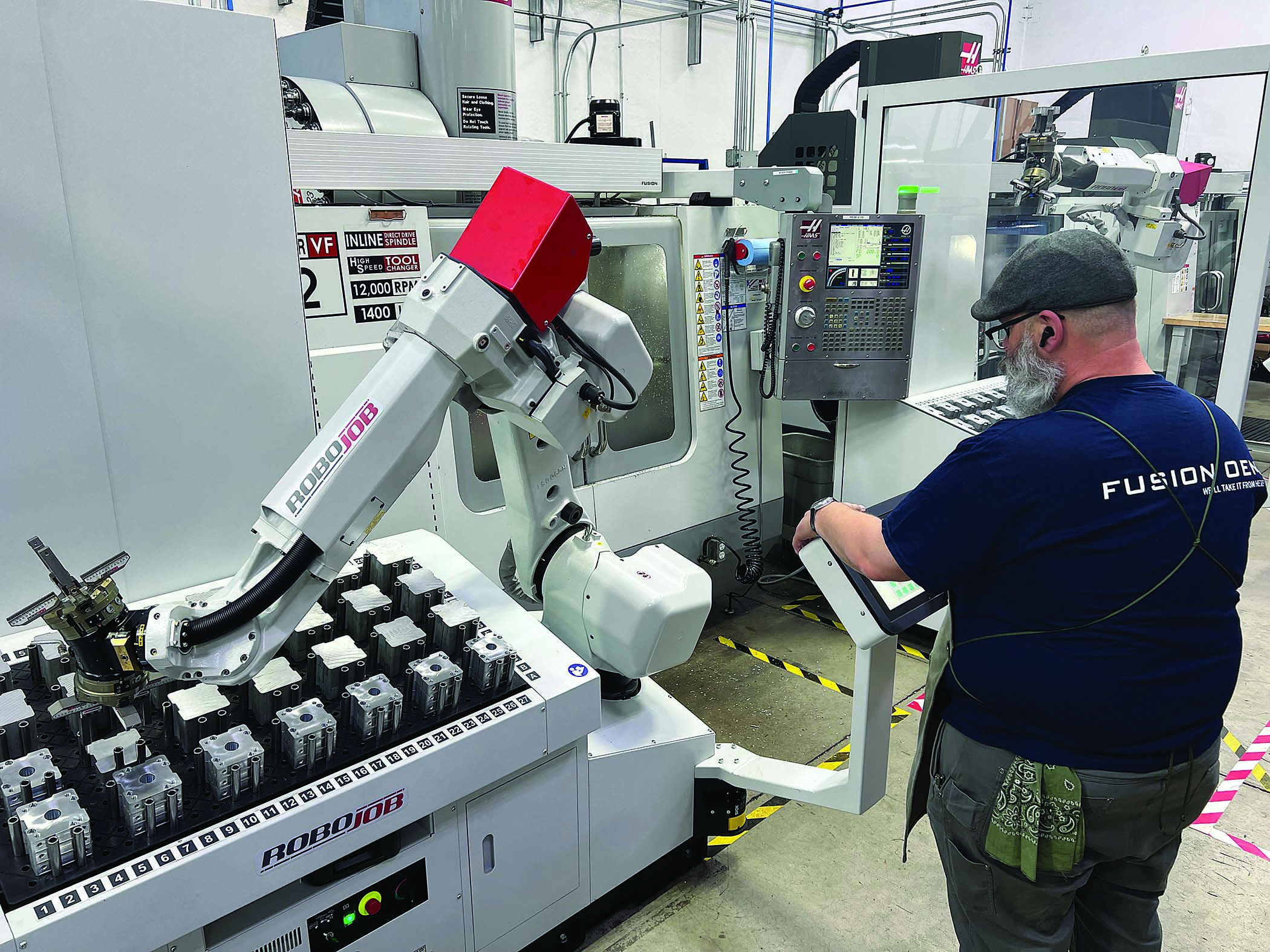
A $40,000 investment in a bar feeder might be worth it, he said, “if I free a guy up and now he’s working on two machines instead of just one with a little bit of automation.”
According to Zoberis, RoboJob’s automation systems usually pay for themselves in six months if users are running three shifts a day, five days a week. If it’s two shifts a day, payback could take up to a year, while customers running a single shift a day might have to wait as long as 18 months to recoup their investment. But he maintained that the amount of time it takes to break even on the investment is almost irrelevant if you look at the bigger picture.
“After the break-even point, you have subsequent years of labor savings that could be in the millions of dollars,” he said. “That’s because the robot has a useful life of 15 to 20 years even before going through overhaul.”
Another justification for the cost of automation is the positive impact it can have on the health of workers.
“If I’m dedicating a guy all day to making one part number thousands of times, and if he’s doing the same motion over and over again, you want to automate that process to not cause physical pain to your employees,” Sanders noted, adding that automation can also be warranted on health grounds when it takes the place of workers who are constantly moving heavy parts in and out of machines.
On the other hand, Zoberis pointed out that automated work cells are not right for processes that are not completely stable from start to finish. He said these could be applications that require in-process operator inspections because a part geometry or material is difficult to machine.
Better Than Ever
Although not a good fit for every work cell, automation has become a more attractive option thanks to a number of recent developments. The biggest such advancement Sanders has seen in recent years is a move toward the so-called “open cell” concept. In an open cell, the physical fencing that traditionally protected workers from robots in motion is replaced by light curtains and area scanners. Featuring infrared laser sensors, light curtains make it easier and faster for workers to move in and out of a cell. Instead of using keys to unlock gates when they need to get into a cell, workers simply walk through the light curtain, which stops automatic operations in the cell.
Another significant advancement cited by Sanders is improved robot vision.
While in the past robots could see only in two dimensions, “now it’s moved to 3D — and 3D has gotten much better,” he said.
So instead of having to fixture parts on a conveyor to make sure they’re picked up by a robot, he said operators can just drop parts anywhere on a conveyor and a robot equipped with the latest 3D vision technology will be able to accurately locate them for pick-and-place operations. This saves both time and fixturing costs, which reduces the overall cost of operating the cell.
Then there are developments that Zoberis says have made work cell automation more “approachable” for those who have stayed away in the past. Years ago, for example, this automation cost a small fortune because it was always custom-designed for a specific application. Today, however, manufacturers can opt for what he calls “productized” CNC automation.
Based on industry standards and featuring software designed specifically for CNC applications, these automation products “are right off the shelf,” he said. “You can install them, and they will meet your requirements right away for CNC machine tending.”
Zoberis also touts what he sees as a paradigm shift in the automation industry. Traditionally, automation was used strictly for low-mix, high-volume production in larger machining operations.
Today, however, automation “isn’t just for the big guys anymore,” he noted.
Now more affordable and easier to use than ever, automation solutions are being offered for high-mix, low-volume production.
“A lot of shops might automate a process like that just because it relieves them from a shift of machine tending,” he said.
Automation has gotten so user-friendly that all the necessary training can now be done on-site during installation. Zoberis credits the strides made in this area chiefly to advances in automation software.
The latest software of this kind “is just like an app on your phone,” he said. “It’s very icon-driven. And you just put basic part information in there, and away you go.”
Contact Details
Contact Details
Contact Details
Related Glossary Terms
- burr
burr
Stringy portions of material formed on workpiece edges during machining. Often sharp. Can be removed with hand files, abrasive wheels or belts, wire wheels, abrasive-fiber brushes, waterjet equipment or other methods.
- centers
centers
Cone-shaped pins that support a workpiece by one or two ends during machining. The centers fit into holes drilled in the workpiece ends. Centers that turn with the workpiece are called “live” centers; those that do not are called “dead” centers.
- chuck
chuck
Workholding device that affixes to a mill, lathe or drill-press spindle. It holds a tool or workpiece by one end, allowing it to be rotated. May also be fitted to the machine table to hold a workpiece. Two or more adjustable jaws actually hold the tool or part. May be actuated manually, pneumatically, hydraulically or electrically. See collet.
- computer numerical control ( CNC)
computer numerical control ( CNC)
Microprocessor-based controller dedicated to a machine tool that permits the creation or modification of parts. Programmed numerical control activates the machine’s servos and spindle drives and controls the various machining operations. See DNC, direct numerical control; NC, numerical control.
- fixture
fixture
Device, often made in-house, that holds a specific workpiece. See jig; modular fixturing.
- industrial robot
industrial robot
Robot designed for industrial use. Primarily used as a material-handling device but also used for changing tools, assembling parts, and manipulating special tools and measuring devices. Depending on design, an industrial robot can be programmed to perform a task by means of a controller, or it can be “walked” through the required movements by utilizing a digitizing system that translates movements into commands that the robot can be “taught.” See robot; teaching pendant.
- lean manufacturing
lean manufacturing
Companywide culture of continuous improvement, waste reduction and minimal inventory as practiced by individuals in every aspect of the business.
Contributors
Mazak Corp.
859-342-1700
www.mazakusa.com
RoboJob-USA
866-952-9020
www.robojob-usa.com
SW North America Inc.
248-617-3800
www.sw-machines.com