Separate yet combined is an apt description of Stock Drive Products/Sterling Instrument. Located on New York’s Long Island, in New Hyde Park, both sides of the company were founded, and are still managed, by engineers. They machine and manufacture an array of mechanical components—offering more than 130,000 line items.
Although typically referred to as one entity, ISO 9001-registered SDP focuses on producing standard synchronous-drive products, while AS9100-registered SI primarily provides custom components to solve complex challenges for its customers, with standard tolerances as tight as ±0.0001 ". For SDP, which has machining and plastic molding capabilities, products include gears, couplings, bearings, timing pulleys and timing belts. Custom products, however, are not out of the question at SDP. For example, SDP can cut timing belt widths to exact specifications from its vast inventory of sleeves.
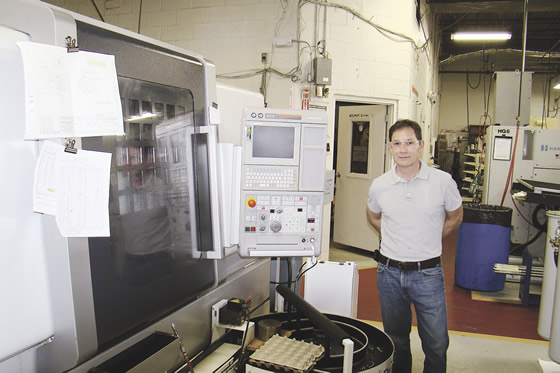
John Lowe, foreman for Sterling Instrument, is one of the company’s many long-time employees.
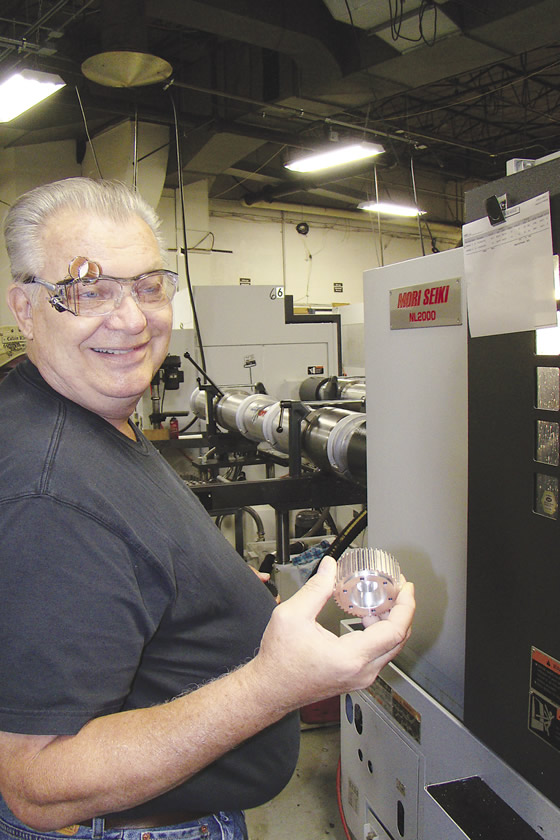
Bob Gaulrapp, shop foreman for Stock Drive Products, displays a part produced on a Mori Seiki NL2000 horizontal lathe.
SI specializes in precision gears, gearboxes, differentials, sprockets and aerospace parts made from a host of materials, including titanium, stainless steel, aluminum and nylon. Major customers include Boeing Satellite Systems, Hamilton Sundstrand, Raytheon Systems, Flir and Israel Aerospace.
“We do it all,” said John Lowe, SI foreman, “including anything that is driven or has to be connected to an encoder, motor or transmission.”
Linda Shuett, marketing manager for New Hyde Park-based Designatronics Inc., which owns both divisions, noted SI began operations about 50 years ago and SDP came into existence a few years later. Especially for the SDP side, she added that the plan was to be the go-to source for synchronous-drive products, from prototype to production quantities, and began including items in the catalog just as a benefit for customers. “[The idea was to] add other components, so if somebody is buying a gear, why not sell them something else they also might need?”
Early on, Lowe explained, the company noticed that customers needed certain gears SI wasn’t producing as well as belt-driven products. To produce the additional products required to meet this demand, the company developed the SDP side, which eventually became the larger of the two. “The Sterling side still maintains what it does best and that’s design,” he said. “We’re not just a manufacturer of standard components. Our biggest strength is our engineering staff. We’ll take your widget or gadget and develop that product until you’re happy, and that’s how a lot of relationships start.”
Other times, a customization project begins when an end user sees a product, such as a gear or transmission device, in one of SDP/SI’s catalogs but determines it isn’t exactly what’s needed. From there, Lowe said, the company will modify the product and develop prototypes to test before going into production. “Anybody can call and say, ‘We have a problem. How can you help us?’ ”
Cutting Metal
Regardless of which side of the building you are in—you have to pass through a doorway to go from one shop to the other—you will see a lot of machining equipment on a visit to SDP/SI. The list includes 48 CNC and 22 manual lathes, 15 CNC milling machines and machining centers, 20 grinders, 34 pieces of drilling equipment, four deburring machines and more than 120 gear hobbing, shaping and generating machines. To verify parts are in tolerance and otherwise meet specification requirements, the company has more than 140 pieces of inspection and test equipment, as well as miscellaneous inspection tools, micrometers, calipers and gages. It also has an ISO 7/class 10,000 clean room.
Many of those machine tools are from one builder. “We’re one of the largest purchasers of Mori Seiki equipment in the Northeast,” Lowe said.
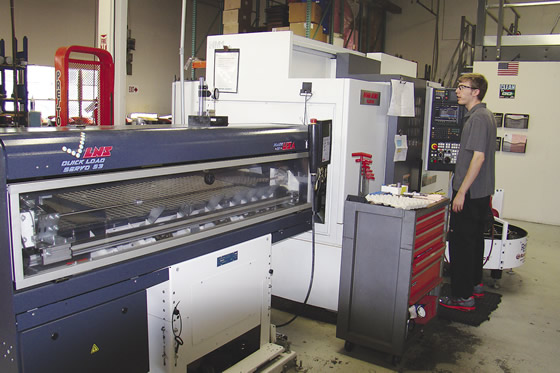
CNC machinist Jonathan Corda monitors a Mori Seiki machine tool that is integrated with an LNS bar feeder to provide long-run production.
About 5 years ago, SI purchased its first mill/turn machine, one from Mori Seiki’s original NL series. Since then, multitask machining has proven to be a beneficial addition, according to Lowe. “We were like ‘wow,’ ” he said about the company’s first mill/turn machine, “and bought a second one and said ‘wow’ again. This looks like the way our future is going.”
Lowe explained that prior to acquiring multitask technology, lathes were in one area and milling machines were across the aisle. Parts were transferred from machine to machine as needed. Now those machining tasks can be done in one setup unless the material requires heat treatment. He said: “Going forward, every possible opportunity goes through the mill/turn machine, even if it goes out for heat treating to bring up the Rockwell. We have successfully machined materials up to 64 HRC. The Mori Seiki machines are so consistent that we can hold 0.0001 " or 0.0002 " tolerances all day long when hard turning.”
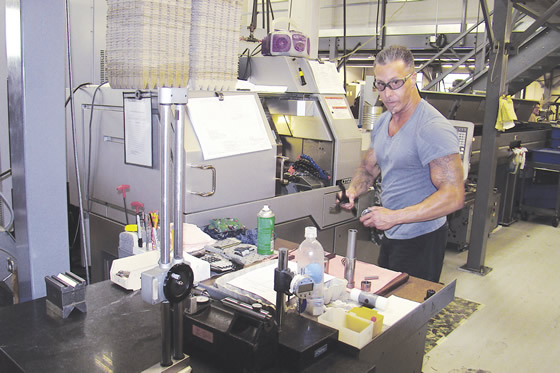
CNC machinist Damon Bahr sets up a Citizen Swiss-style machine.
In another effort to increase productivity, SDP/SI eliminated secondary operations while improving the quality of Swiss-style machined parts by acquiring updated equipment. This includes an 11-axis Star ECAS-32T Swiss-style machine, which runs three simultaneous programs and special editing software to write programs because the three programmed channels must work together.
When operating 25-year-old Swiss turning machines, SI would have to do a lot of secondary operations to finish-turn the journals, grind them, set the centers and inspect and check everything, Lowe said. “Now, we’re doing the same part with four, five, maybe six operations in one setup.”
Automation also plays a role in increasing productivity, enabling SDP/SI, which runs two shifts, to perform lights-out machining the remainder of the time. “The system will hold 0.0002 " tolerances all night,” said Susan Anderson, vice president and general manager for SI. “We come in and there is a bucket of parts.”
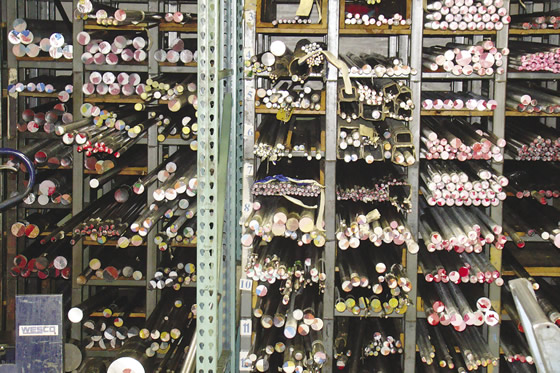
Bar stock is color-coded for easy identification, and every bar is assigned to a specific job.
In addition, the company regularly receives assistance from cutting tool manufacturers, such as Sandvik Coromant, Iscar Metals and Greenleaf, to help overcome machining challenges, which has paid dividends. “We don’t really have any machining problems anymore with heat-treated materials, titanium alloys or superalloys,” Lowe said.
Nonetheless, cutting tool testing continues with the goal of making further process improvements. “We throw them all into a pot and whoever can make it happen—best tool life, best surface finish, best tolerance—is the one who’ll work on that project,” Lowe added.
Attracting Skilled Workers
Similar to other part manufacturers, SDP/SI finds it “extremely difficult” to find skilled labor, according to Lowe. “We’ve been advertising for 6 months and have only had a couple of hits.”
To find people with the needed skills, the company has approached the three colleges within a 20-mile radius: Suffolk County Community College, Queensborough Community College and Farmingdale State College. They offer manufacturing engineering technology degrees, and SDP/SI was able to attract some promising candidates, but “the commute was killing them,” Lowe said about many. “Twenty-five miles in Long Island traffic is a nightmare.” The lack of skilled workers negatively impacts future company growth, he added.
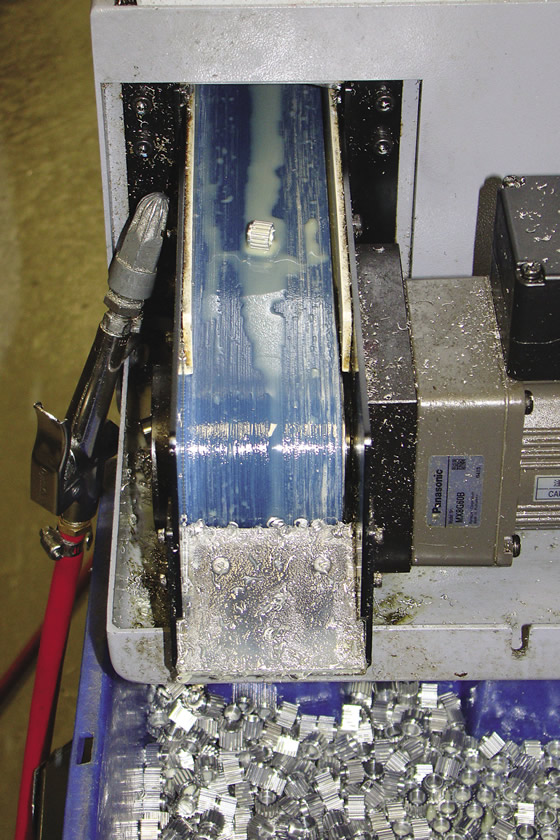
A finished part exits a Swiss-style machine at Sterling Instrument.
One hire who did work out is CNC machinist Damon Bahr. After losing his two food businesses in the Great Recession, he took a 1-year manufacturing technology course at Suffolk County Community College, continuing the education he gained early in his career setting up machines. “Damon came on board as a trainee and now he’s setting up one of the most sophisticated machines we have, a Citizen [Swiss-style machine],” Lowe said.
Lowe recalled how a 3-year engineering applications program in Toronto helped prepare him for a manufacturing career. In addition to working for a manufacturer 37 hours a week, the program required attending night school for 6 hours a day, 4 days a week. “It was tough,” he said. “If you screwed up on either end, you were done. But I liked working with my hands more than I liked sitting in the classroom with a slide rule.”
As the 300-employee company continues to grow, with the goal of moving from $60 million in annual sales to $100 million in 5 years, SDP/SI is looking for a new building to consolidate its four New Hyde Park facilities. The plan is to remain in the area to avoid any commuting or relocation issues for employees. This is especially critical for long-term workers, Shuett noted, adding that a couple have been with the company for more than 40 years. “[They’re] never late and never absent,” Lowe added. CTE
For more information about Stock Drive Products/Sterling Instrument, visit www.sdp-si.com or call (800) 819-8900.
Related Glossary Terms
- alloys
alloys
Substances having metallic properties and being composed of two or more chemical elements of which at least one is a metal.
- centers
centers
Cone-shaped pins that support a workpiece by one or two ends during machining. The centers fit into holes drilled in the workpiece ends. Centers that turn with the workpiece are called “live” centers; those that do not are called “dead” centers.
- computer numerical control ( CNC)
computer numerical control ( CNC)
Microprocessor-based controller dedicated to a machine tool that permits the creation or modification of parts. Programmed numerical control activates the machine’s servos and spindle drives and controls the various machining operations. See DNC, direct numerical control; NC, numerical control.
- gang cutting ( milling)
gang cutting ( milling)
Machining with several cutters mounted on a single arbor, generally for simultaneous cutting.
- hard turning
hard turning
Single-point cutting of a workpiece that has a hardness value higher than 45 HRC.
- lathe
lathe
Turning machine capable of sawing, milling, grinding, gear-cutting, drilling, reaming, boring, threading, facing, chamfering, grooving, knurling, spinning, parting, necking, taper-cutting, and cam- and eccentric-cutting, as well as step- and straight-turning. Comes in a variety of forms, ranging from manual to semiautomatic to fully automatic, with major types being engine lathes, turning and contouring lathes, turret lathes and numerical-control lathes. The engine lathe consists of a headstock and spindle, tailstock, bed, carriage (complete with apron) and cross slides. Features include gear- (speed) and feed-selector levers, toolpost, compound rest, lead screw and reversing lead screw, threading dial and rapid-traverse lever. Special lathe types include through-the-spindle, camshaft and crankshaft, brake drum and rotor, spinning and gun-barrel machines. Toolroom and bench lathes are used for precision work; the former for tool-and-die work and similar tasks, the latter for small workpieces (instruments, watches), normally without a power feed. Models are typically designated according to their “swing,” or the largest-diameter workpiece that can be rotated; bed length, or the distance between centers; and horsepower generated. See turning machine.
- milling
milling
Machining operation in which metal or other material is removed by applying power to a rotating cutter. In vertical milling, the cutting tool is mounted vertically on the spindle. In horizontal milling, the cutting tool is mounted horizontally, either directly on the spindle or on an arbor. Horizontal milling is further broken down into conventional milling, where the cutter rotates opposite the direction of feed, or “up” into the workpiece; and climb milling, where the cutter rotates in the direction of feed, or “down” into the workpiece. Milling operations include plane or surface milling, endmilling, facemilling, angle milling, form milling and profiling.
- shaping
shaping
Using a shaper primarily to produce flat surfaces in horizontal, vertical or angular planes. It can also include the machining of curved surfaces, helixes, serrations and special work involving odd and irregular shapes. Often used for prototype or short-run manufacturing to eliminate the need for expensive special tooling or processes.
- superalloys
superalloys
Tough, difficult-to-machine alloys; includes Hastelloy, Inconel and Monel. Many are nickel-base metals.
- tolerance
tolerance
Minimum and maximum amount a workpiece dimension is allowed to vary from a set standard and still be acceptable.
- turning
turning
Workpiece is held in a chuck, mounted on a face plate or secured between centers and rotated while a cutting tool, normally a single-point tool, is fed into it along its periphery or across its end or face. Takes the form of straight turning (cutting along the periphery of the workpiece); taper turning (creating a taper); step turning (turning different-size diameters on the same work); chamfering (beveling an edge or shoulder); facing (cutting on an end); turning threads (usually external but can be internal); roughing (high-volume metal removal); and finishing (final light cuts). Performed on lathes, turning centers, chucking machines, automatic screw machines and similar machines.