The thicker the PVD coating is on an insert, the longer users expect it to last. But a coating that is too thick tends to flake, reducing the coating’s effective life, according to Mike Raper, national sales manager for Techniks Inc. That is why most manufacturers’ PVD coatings are only 4µm thick, he noted. However, the toolmaker’s Nexus line of milling, turning and boring inserts have a PVD TiAlN LT10 coating up to 8µm thick for milling and a LT1000 coating up to 14µm thick for turning.
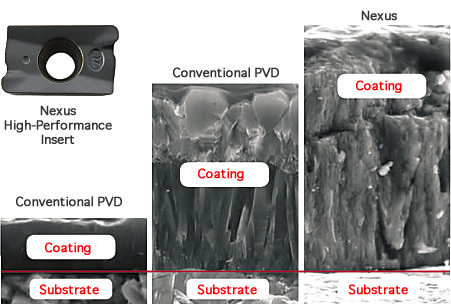
Courtesy of Techniks
The thickness of the Nexus Magia PVD coating compared to a conventional PVD coating and a conventional CVD coating.
Raper explained that the unique PVD formula for the Magia coating, developed by partner Lamina Technologies SA, Yverdon-les-Bains, Switzerland, prevents flaking while enabling the highest possible adhesion of the PVD to the submicron grain carbide insert, which has a special edge preparation. Prior to coating, the inserts are subjected to a micro-sandblast technique to hone the cutting edge radius to within a ±5µm tolerance. This process takes the place of brush honing, which creates an uneven edge, according to Raper.
“Our coating ends up being smoother and more uniform,” he said, adding that a post-coating polishing treatment also reduces friction.
With traditional coatings, increasing the hardness usually means reducing toughness and vice versa. Nexus’ nanocomposite coating structure, LT1000, has a high hardness and toughness at the same time, according to Chris Deis, director of marketing for Techniks. He claimed that LT1000 is the thickest supernitride PVD coating on the market and provides greater thermal insulation and more resistance to plastic deformation and shock than CVD or traditional PVD coatings.
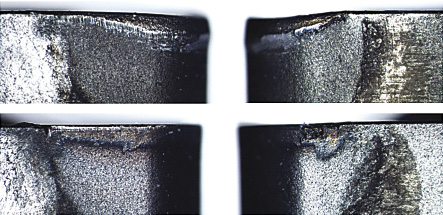
Courtesy of Techniks
A comparison of tool life for the Nexus CMMG 120408 NN MG10 insert (bottom two) vs. another toolmaker’s brand (top two) after wet machining 42CRMo4 at a cutting speed of 660 sfm, a feed of 0.020 ipm and a 0.079 " DOC for 22.0 minutes (Nexus) and 11.5 minutes (other brand).
In addition to extending tool life, the Nexus inserts are suitable for machining multiple materials, including low-carbon steel, stainless steel, alloy steel hardened up to 60 HRC, cast iron, titanium and heat-resistant superalloys. The company offers a separate LT05 grade coated with chromium nitride for machining aluminum alloys, but the other Nexus LT grades are also effective in aluminum with a silicon content higher than 8 percent, Raper added. “You can go from material to material and job to job with the same insert,” he said. “With us, you buy an insert for its shape, not by grade for a certain material.”
Multiple-material machining ability not only reduces cutting tool inventory, it eliminates guesswork when selecting a grade, increases production efficiency and flexibility and reduces costs, according to the company. “Machinists don’t have to go looking for inserts every time they change jobs,” Raper said. “They just go with what they’ve got in the machine and it works extremely well.”
For more information, contact Techniks Inc., Indianapolis, at (800) 597-3921 or www.techniksusa.com/nexus.
Related Glossary Terms
- alloys
alloys
Substances having metallic properties and being composed of two or more chemical elements of which at least one is a metal.
- aluminum alloys
aluminum alloys
Aluminum containing specified quantities of alloying elements added to obtain the necessary mechanical and physical properties. Aluminum alloys are divided into two categories: wrought compositions and casting compositions. Some compositions may contain up to 10 alloying elements, but only one or two are the main alloying elements, such as copper, manganese, silicon, magnesium, zinc or tin.
- boring
boring
Enlarging a hole that already has been drilled or cored. Generally, it is an operation of truing the previously drilled hole with a single-point, lathe-type tool. Boring is essentially internal turning, in that usually a single-point cutting tool forms the internal shape. Some tools are available with two cutting edges to balance cutting forces.
- chemical vapor deposition ( CVD)
chemical vapor deposition ( CVD)
High-temperature (1,000° C or higher), atmosphere-controlled process in which a chemical reaction is induced for the purpose of depositing a coating 2µm to 12µm thick on a tool’s surface. See coated tools; PVD, physical vapor deposition.
- cutting speed
cutting speed
Tangential velocity on the surface of the tool or workpiece at the cutting interface. The formula for cutting speed (sfm) is tool diameter 5 0.26 5 spindle speed (rpm). The formula for feed per tooth (fpt) is table feed (ipm)/number of flutes/spindle speed (rpm). The formula for spindle speed (rpm) is cutting speed (sfm) 5 3.82/tool diameter. The formula for table feed (ipm) is feed per tooth (ftp) 5 number of tool flutes 5 spindle speed (rpm).
- edge preparation
edge preparation
Conditioning of the cutting edge, such as a honing or chamfering, to make it stronger and less susceptible to chipping. A chamfer is a bevel on the tool’s cutting edge; the angle is measured from the cutting face downward and generally varies from 25° to 45°. Honing is the process of rounding or blunting the cutting edge with abrasives, either manually or mechanically.
- feed
feed
Rate of change of position of the tool as a whole, relative to the workpiece while cutting.
- gang cutting ( milling)
gang cutting ( milling)
Machining with several cutters mounted on a single arbor, generally for simultaneous cutting.
- hardness
hardness
Hardness is a measure of the resistance of a material to surface indentation or abrasion. There is no absolute scale for hardness. In order to express hardness quantitatively, each type of test has its own scale, which defines hardness. Indentation hardness obtained through static methods is measured by Brinell, Rockwell, Vickers and Knoop tests. Hardness without indentation is measured by a dynamic method, known as the Scleroscope test.
- inches per minute ( ipm)
inches per minute ( ipm)
Value that refers to how far the workpiece or cutter advances linearly in 1 minute, defined as: ipm = ipt 5 number of effective teeth 5 rpm. Also known as the table feed or machine feed.
- milling
milling
Machining operation in which metal or other material is removed by applying power to a rotating cutter. In vertical milling, the cutting tool is mounted vertically on the spindle. In horizontal milling, the cutting tool is mounted horizontally, either directly on the spindle or on an arbor. Horizontal milling is further broken down into conventional milling, where the cutter rotates opposite the direction of feed, or “up” into the workpiece; and climb milling, where the cutter rotates in the direction of feed, or “down” into the workpiece. Milling operations include plane or surface milling, endmilling, facemilling, angle milling, form milling and profiling.
- physical vapor deposition ( PVD)
physical vapor deposition ( PVD)
Tool-coating process performed at low temperature (500° C), compared to chemical vapor deposition (1,000° C). Employs electric field to generate necessary heat for depositing coating on a tool’s surface. See CVD, chemical vapor deposition.
- plastic deformation
plastic deformation
Permanent (inelastic) distortion of metals under applied stresses that strain the material beyond its elastic limit.
- polishing
polishing
Abrasive process that improves surface finish and blends contours. Abrasive particles attached to a flexible backing abrade the workpiece.
- superalloys
superalloys
Tough, difficult-to-machine alloys; includes Hastelloy, Inconel and Monel. Many are nickel-base metals.
- titanium aluminum nitride ( TiAlN)
titanium aluminum nitride ( TiAlN)
Often used as a tool coating. AlTiN indicates the aluminum content is greater than the titanium. See coated tools.
- tolerance
tolerance
Minimum and maximum amount a workpiece dimension is allowed to vary from a set standard and still be acceptable.
- turning
turning
Workpiece is held in a chuck, mounted on a face plate or secured between centers and rotated while a cutting tool, normally a single-point tool, is fed into it along its periphery or across its end or face. Takes the form of straight turning (cutting along the periphery of the workpiece); taper turning (creating a taper); step turning (turning different-size diameters on the same work); chamfering (beveling an edge or shoulder); facing (cutting on an end); turning threads (usually external but can be internal); roughing (high-volume metal removal); and finishing (final light cuts). Performed on lathes, turning centers, chucking machines, automatic screw machines and similar machines.