Tracking down the right tool turns a nightmare job into a dream at AB CNC.
Most machine shops start small. AB CNC Services & Consulting Inc. is no exception, starting with one person, one machine and one job. For Andy Baczynski, company president, the story of how the shop came to be began many years ago.
“I’ve been in machining since I was 16,” Baczynski said. “First at a trade school in Europe and, since 1981, working for various U.S. companies.” Along the way, he garnered expertise in boosting machining productivity. In 2005, he began doing consulting work, using his expertise to help other companies improve their setups and machining operations.
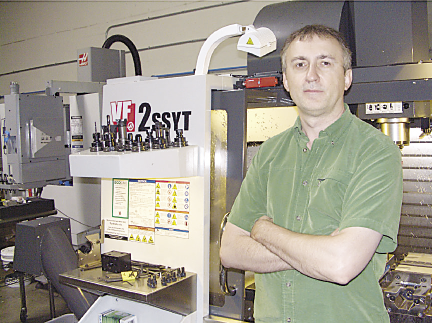
Andy Baczynski, president of AB CNC Services & Consulting
“While I was consulting, people started asking me why I didn’t start my own shop,” Baczynski said.
Then, in 2006, a company Baczynski had worked for offered to sell him one of its CNC machines, an advanced Index ABC lathe with live tooling and a bar feeder. “They called me because I knew the machine very well and they guessed—correctly—that I might be interested,” he said. “I told them I’d buy the machine as long as they gave me some work to get me started, so they did.”
About half of all small businesses fail within the first 5 years, but Baczynski’s has not only survived, it has prospered. He has added two employees, two machines—a Haas VF-2 and a Haas Mini Mill—and moved from his original 1,600-sq.-ft. facility to a 3,000-sq.-ft. one.
“My bread and butter was and still is turning parts that require multiple, additional operations, such as milling and drilling, and doing it all in a single setup,” Baczynski said. “Thanks to the capability of my dual-spindle Index lathe and my experience with these sorts of parts, I can offer customers a ‘done-in-one’ capability that can save them time and money.”
Baczynski’s expertise, craftsmanship and attention to detail have won him a growing list of customers in diverse industries. He noted with pride that he does parts for the British Broadcasting Corp., aircraft cargo conversion (rollers, locking systems and other components on the floor of cargo planes used to move and retain the cargo), and water purification and filtration.
Tough Challenge
It was a part for the water industry that recently presented him with one of his greatest challenges. “It was a small order, just 100 parts,” Baczynski said. The part was a clip that secured components in a pump assembly for a water filtration system. It measured 1.75 "×1 "×0.1875 " and four clips were cut from a 1.875 "×4.9 "×0.25 " plate.
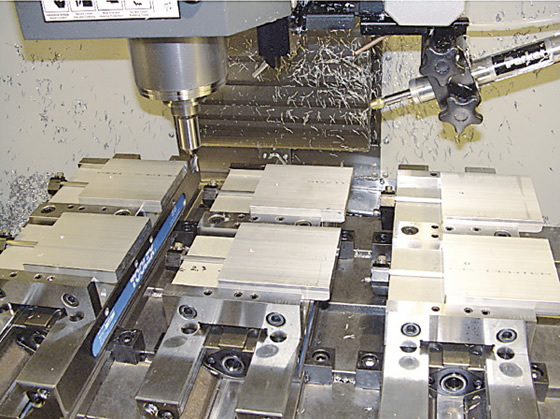
Courtesy of All images: Walter USA
Machining of clips for pump assembles used in water filtration systems. The clips are made of Super Duplex 2507 stainless steel.
At first glance, there didn’t seem to be anything particularly challenging about the job, but the work material was Super Duplex 2507, a stainless steel with 25 percent chromium, 4 percent molybdenum and 7 percent nickel. It provides exceptional strength and corrosion resistance. Because of the material’s high nickel content, it was expected to be difficult to cut, but just how difficult only became apparent after Baczynski put tool to metal.
“I started with a solid-carbide endmill that I had used in the past because the geometry of the tool looked much stronger than any other endmill I had in the shop,” he said.
The application actually required two tools: a ½ "-dia. endmill for most of the part and a ¼ "-dia. endmill for finishing and milling areas where the cut had to be stepped down. Neither of those tools made it through the first plate. “I tried other endmills as well but none of them held up,” Baczynski said. “The part was being machined on the Haas Mini Mill. It provided enough speed, horsepower and feed to make it work, but the material itself was exceptionally difficult.”
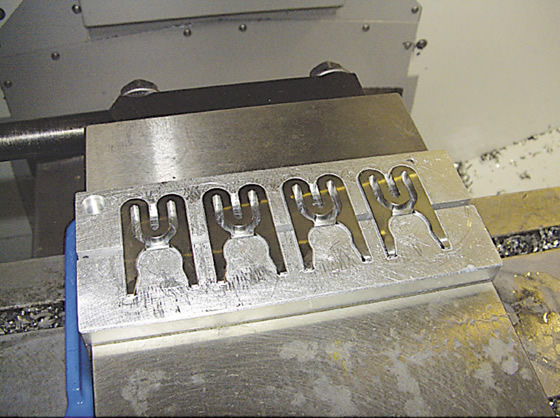
Machining 32 clips used in pump assemblies from Super Duplex 2507 destroyed more than 25 endmills before Walter Prototyp tools were used.
Baczynski experimented by adjusting the speed and feed rate and DOC with the various tools, trying multiple combinations. “Even though part thickness was only 0.1875 ", I still had to adjust the DOC to make these endmills last a little longer because the material was proving so difficult,” he said.
So difficult, in fact, that Baczynski destroyed more than 25 endmills to complete just eight plates. The tools wore prematurely and then broke. Long chips led to chip recutting, a situation caused by tool geometry problems and weakness at the endmills’ leading edge. Multiple tool changes and frequent breaks to devise new machining strategies meant the Haas Mini Mill was tied up for 3 weeks while machining the eight plates.
New Solution
That’s when Brandon Prater, a field sales engineer for Walter USA LLC, Waukesha, Wis., stepped in. “Brandon was working on a different job in the shop, trying to find the right combination of feeds and speeds for some Super Duplex valves I was turning on my Index ABC. When he looked at this job and saw the trouble I was having machining the clips, he suggested I try two Walter Prototyp solid-carbide endmills, a ½ "- and a ¼ "-dia. model. “I told him ‘at this point I’m open to anything—I just need something that will hold up so I can finish the job and get it off the machine,’ ” Baczynski said.
Prater provided two Prototyp Protostar Qmax HR Kordel F40s with a TAX TiAlN coating that stood up to the material. The tool design allows it to cut more freely. Fine serrations on the flutes give the tool superior chipbreaking ability, minimizing chip recutting, according to Walter. This, along with the tool’s stability and the optimized grain structure of the carbide formulation, allow it to work effectively on lower-powered, less-rigid machine tools.
Good Results
The result was immediate and dramatic. “Doing one plate, which is four parts, with the other tools, what with the breakage, replacement and rerunning, was taking me 1½ hours,” Baczynski said. “With the Walter Prototyps, though we had determined that a slightly slower speed and feed rate would be optimal, I was completing a plate in 45 minutes. That was because the Prototyps held up, so no tool change was necessary, and I was able to take a full DOC of 0.1875 ". With the old tools, I had to take multiple shallow cuts to keep them from breaking.”
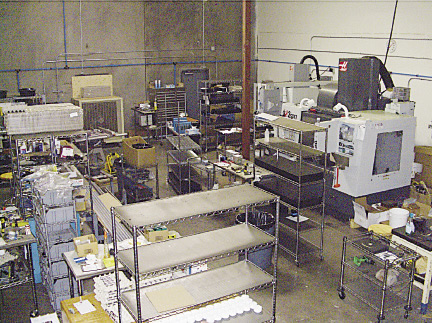
AB CNC operates three machine tools and employs two machinists.
The Prototyp endmills were able to complete the final 17 plates without a tool change. “I thought they would be worn out, so toward the end of the job I was watching the load meter on the machine closely,” Baczynski said. “If the load meter was climbing, it would tell me that an endmill was no longer cutting well. But the load meter remained stable and the tool just kept on cutting.”
The technical assistance on the job proved invaluable. “The help I got from Brandon and Walter went beyond the call of duty,” Baczynski said. “He spent a lot of time with me making notes so he could offer intelligent suggestions, and his pick on this Super Duplex milling application allowed me to turn a nightmare of a job into a success.
“Over the years I’ve acquired some knowledge about picking the right tools,” he continued, “but I realize I don’t know everything. That’s why it’s important to have a good relationship with a tool supplier, because they know the tools and what works in a given situation and what doesn’t.” CTE
For more information about AB CNC Services & Consulting Inc., Rockline, Calif., call (916) 740-6867. For more information about Walter USA LLC’s cutting tools, call (800) 945-5554 or visit www.walter-tools.com/us.
SaveSave
Related Glossary Terms
- Rockwell hardness number ( HR)
Rockwell hardness number ( HR)
Number derived from the net increase in the depth of impression as the load on the indenter is increased from a fixed minor load to a major load and then returned to the minor load. The Rockwell hardness number is always quoted with a scale symbol representing the indenter, load and dial used. Rockwell A scale is used in connection with carbide cutting tools. Rockwell B and C scales are used in connection with workpiece materials.
- computer numerical control ( CNC)
computer numerical control ( CNC)
Microprocessor-based controller dedicated to a machine tool that permits the creation or modification of parts. Programmed numerical control activates the machine’s servos and spindle drives and controls the various machining operations. See DNC, direct numerical control; NC, numerical control.
- corrosion resistance
corrosion resistance
Ability of an alloy or material to withstand rust and corrosion. These are properties fostered by nickel and chromium in alloys such as stainless steel.
- endmill
endmill
Milling cutter held by its shank that cuts on its periphery and, if so configured, on its free end. Takes a variety of shapes (single- and double-end, roughing, ballnose and cup-end) and sizes (stub, medium, long and extra-long). Also comes with differing numbers of flutes.
- feed
feed
Rate of change of position of the tool as a whole, relative to the workpiece while cutting.
- flutes
flutes
Grooves and spaces in the body of a tool that permit chip removal from, and cutting-fluid application to, the point of cut.
- gang cutting ( milling)
gang cutting ( milling)
Machining with several cutters mounted on a single arbor, generally for simultaneous cutting.
- lathe
lathe
Turning machine capable of sawing, milling, grinding, gear-cutting, drilling, reaming, boring, threading, facing, chamfering, grooving, knurling, spinning, parting, necking, taper-cutting, and cam- and eccentric-cutting, as well as step- and straight-turning. Comes in a variety of forms, ranging from manual to semiautomatic to fully automatic, with major types being engine lathes, turning and contouring lathes, turret lathes and numerical-control lathes. The engine lathe consists of a headstock and spindle, tailstock, bed, carriage (complete with apron) and cross slides. Features include gear- (speed) and feed-selector levers, toolpost, compound rest, lead screw and reversing lead screw, threading dial and rapid-traverse lever. Special lathe types include through-the-spindle, camshaft and crankshaft, brake drum and rotor, spinning and gun-barrel machines. Toolroom and bench lathes are used for precision work; the former for tool-and-die work and similar tasks, the latter for small workpieces (instruments, watches), normally without a power feed. Models are typically designated according to their “swing,” or the largest-diameter workpiece that can be rotated; bed length, or the distance between centers; and horsepower generated. See turning machine.
- milling
milling
Machining operation in which metal or other material is removed by applying power to a rotating cutter. In vertical milling, the cutting tool is mounted vertically on the spindle. In horizontal milling, the cutting tool is mounted horizontally, either directly on the spindle or on an arbor. Horizontal milling is further broken down into conventional milling, where the cutter rotates opposite the direction of feed, or “up” into the workpiece; and climb milling, where the cutter rotates in the direction of feed, or “down” into the workpiece. Milling operations include plane or surface milling, endmilling, facemilling, angle milling, form milling and profiling.
- milling machine ( mill)
milling machine ( mill)
Runs endmills and arbor-mounted milling cutters. Features include a head with a spindle that drives the cutters; a column, knee and table that provide motion in the three Cartesian axes; and a base that supports the components and houses the cutting-fluid pump and reservoir. The work is mounted on the table and fed into the rotating cutter or endmill to accomplish the milling steps; vertical milling machines also feed endmills into the work by means of a spindle-mounted quill. Models range from small manual machines to big bed-type and duplex mills. All take one of three basic forms: vertical, horizontal or convertible horizontal/vertical. Vertical machines may be knee-type (the table is mounted on a knee that can be elevated) or bed-type (the table is securely supported and only moves horizontally). In general, horizontal machines are bigger and more powerful, while vertical machines are lighter but more versatile and easier to set up and operate.
- sawing machine ( saw)
sawing machine ( saw)
Machine designed to use a serrated-tooth blade to cut metal or other material. Comes in a wide variety of styles but takes one of four basic forms: hacksaw (a simple, rugged machine that uses a reciprocating motion to part metal or other material); cold or circular saw (powers a circular blade that cuts structural materials); bandsaw (runs an endless band; the two basic types are cutoff and contour band machines, which cut intricate contours and shapes); and abrasive cutoff saw (similar in appearance to the cold saw, but uses an abrasive disc that rotates at high speeds rather than a blade with serrated teeth).
- titanium aluminum nitride ( TiAlN)
titanium aluminum nitride ( TiAlN)
Often used as a tool coating. AlTiN indicates the aluminum content is greater than the titanium. See coated tools.
- turning
turning
Workpiece is held in a chuck, mounted on a face plate or secured between centers and rotated while a cutting tool, normally a single-point tool, is fed into it along its periphery or across its end or face. Takes the form of straight turning (cutting along the periphery of the workpiece); taper turning (creating a taper); step turning (turning different-size diameters on the same work); chamfering (beveling an edge or shoulder); facing (cutting on an end); turning threads (usually external but can be internal); roughing (high-volume metal removal); and finishing (final light cuts). Performed on lathes, turning centers, chucking machines, automatic screw machines and similar machines.