We all want to be more profitable, and one of the easiest ways to accomplish that is by reducing or eliminating machine setup and changeover times. Fortunately, a range of offerings are available to rapidly change a tool configuration. The catch-all category most often used to describe them is quick-change tools.
Some type of quick-change tool is available for every manufacturing process, and all of them can be placed in two categories: workholders and toolholders. They range from simple work stops to complex machine tool probes.
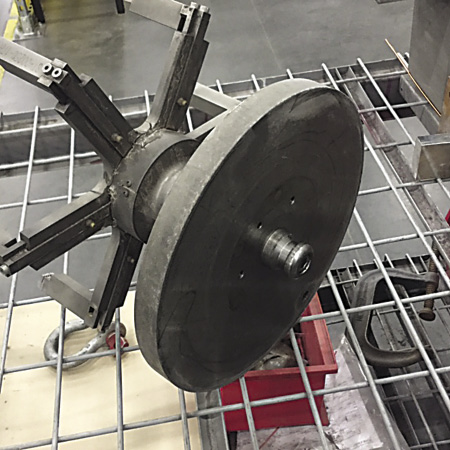
A waterjet machine fixture with the Unilock interface shows the stud that goes into the receiver. All images courtesy C. Tate.
Quick-change workholders are probably the most common if, like me, you consider vises and chucks to be quick-change devices. Chucks and vises are often not sold as quick-change tools, but the devices that can be attached to them are.
Every vise and chuck requires a set of jaws for holding a part, and quick-change jaws are readily available; they are probably the easiest-to-use and lowest-cost quick-change tool available.
Most job shops rely on 3-jaw chucks outfitted with machinable soft jaws to hold their work when turning. For simple jobs, however, it can easily take an hour to find, change and remachine a set of soft jaws. One job changeover per day is equal to 260 hours of set up per year. Because job shops typically recover setup costs, a 50 percent reduction in time means 130 hours of extra revenue.
Standard lathe jaws require a machinist to remove and install two screws per jaw when changing them. Jaws are typically remachined after a change to maintain accuracy. Jaw inserts are available that can be removed and replaced in seconds. Most of these jaws are also highly repeatable, eliminating the need to remachine jaws for most jobs.
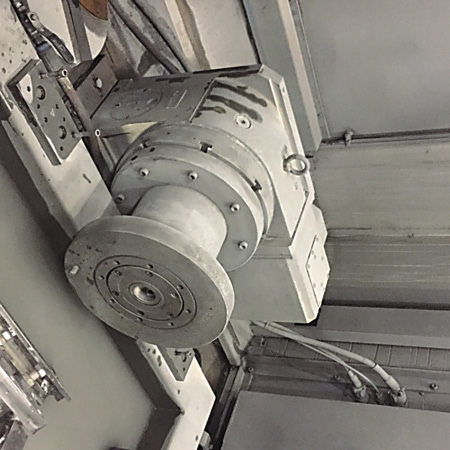
The rotary table inside a waterjet machine has the Unilock receiver in the center of the plate. The receiver is pneumatic and operated with the ball valve (shown in the lower, left-hand corner). It takes only 2 minutes to change fixtures with this setup.
It is common, but expensive and inflexible, for any machine shop to make dedicated workholders for milling machines. Shops can eliminate the need for dedicated fixtures by using machinable vise jaws, such as ones from Detroit-based Snap Jaws Manufacturing that can be removed with a quarter turn of a screw. This allows the user to change workholding in less than a minute. Unlike a dedicated fixture, a set of jaws is relatively inexpensive and can be reused for other jobs.
Dedicated workholding is sometimes required when a vise or chuck cannot be configured to efficiently hold a workpiece. Quick-change tools are available to shorten loading and setup times for dedicated fixtures, such as the Ball Lock mounting system from Jergens Inc., Cleveland. This system works by having a machine-mounted baseplate that can accept subplates with fixtures for holding parts. The baseplate has receivers that accept pins, which locate the subplate and provide substantial pull-down force to hold the subplate on the baseplate. Changeover for small fixtures is fast and accurate enough to eliminate the need for fixture alignment.
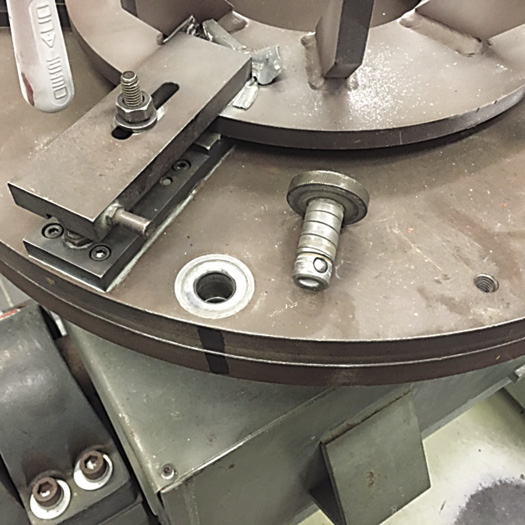
A Ball Lock system on a rotary table in a robotic cell has a pin that slips into the receiver and a setscrew that forces the balls outward to create downward force.
Another option is the Unilock from Schunk Inc., Morrisville, N.C. Unilock relies on a special receiver-and-pin system, where the receiver is mounted on the machine tool and the pin is mounted on the fixture or part. A Unilock pin has a special shape that allows it to be pulled into the receiver similar to how a toolholder is held in a machine spindle. Pins also have a taper, which interfaces with the receiver and provides repeatable fixture positioning.
Because the setup, measurement and data entry associated with cutting tools consumes large amounts of time when changing over, quick-change tools are also available to eliminate or reduce that time. These devices tend to be expensive, primarily because they need to be very accurate.
Capto-style tooling is probably the most common quick-change interface (see photo on page 42). Notice the tri-lobed tapered surface that interfaces with the tapered toolholder for the machining center spindle. Capto toolholders have a positional repeatability of 0.0004 ". This level of accuracy allows cutting tools to be replaced without setting them.
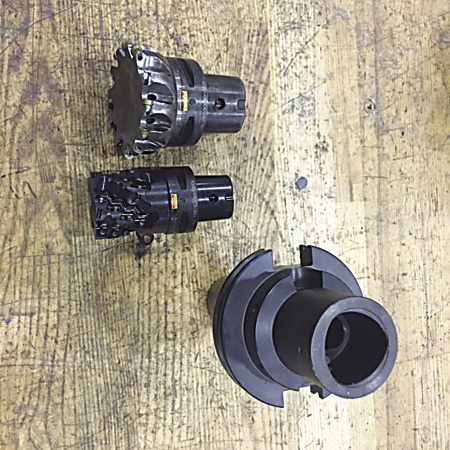
The Capto interface features a tri-lobed shape.
In addition, quick-change toolholders like Capto can improve efficiency on older machines that do not have automatic toolchangers. Older machines often have a spindle or turret that uses threaded hardware to hold cutting tools, which can make tool changes cumbersome and slow. A Capto holder enables a much faster tool change.
For example, turning a gas turbine rotor takes weeks. A single cutting pass can take days, requiring the tool to be changed in the middle of a cut. When our shop purchased large rotor lathes, we installed Capto interfaces on the tool slide. This setup allows the machinist to premeasure tools and have them ready to install while the machine is cutting, reducing the time needed to change the tool and returning to work as fast as possible. Without the Capto interface, we would be forced to reset the tool each time an insert is changed.
When shopping for a quick-change system, consider the problem being addressed, look at all shop processes and make sure the system is as universal as possible. Beware of new items, because they can often have proprietary hardware that becomes obsolete if the product is discontinued. In addition, ask to see several successful implementations before making a purchase. When properly selected and implemented, quick-change tooling enhances the profitability of any shop. CTE
About the Author: Christopher Tate is engineering manager, combustion shop, for Mitsubishi Hitachi Power Systems Americas, Savannah (Ga.) Machinery Works. Email: [email protected].
Related Glossary Terms
- chuck
chuck
Workholding device that affixes to a mill, lathe or drill-press spindle. It holds a tool or workpiece by one end, allowing it to be rotated. May also be fitted to the machine table to hold a workpiece. Two or more adjustable jaws actually hold the tool or part. May be actuated manually, pneumatically, hydraulically or electrically. See collet.
- fixture
fixture
Device, often made in-house, that holds a specific workpiece. See jig; modular fixturing.
- gang cutting ( milling)
gang cutting ( milling)
Machining with several cutters mounted on a single arbor, generally for simultaneous cutting.
- lathe
lathe
Turning machine capable of sawing, milling, grinding, gear-cutting, drilling, reaming, boring, threading, facing, chamfering, grooving, knurling, spinning, parting, necking, taper-cutting, and cam- and eccentric-cutting, as well as step- and straight-turning. Comes in a variety of forms, ranging from manual to semiautomatic to fully automatic, with major types being engine lathes, turning and contouring lathes, turret lathes and numerical-control lathes. The engine lathe consists of a headstock and spindle, tailstock, bed, carriage (complete with apron) and cross slides. Features include gear- (speed) and feed-selector levers, toolpost, compound rest, lead screw and reversing lead screw, threading dial and rapid-traverse lever. Special lathe types include through-the-spindle, camshaft and crankshaft, brake drum and rotor, spinning and gun-barrel machines. Toolroom and bench lathes are used for precision work; the former for tool-and-die work and similar tasks, the latter for small workpieces (instruments, watches), normally without a power feed. Models are typically designated according to their “swing,” or the largest-diameter workpiece that can be rotated; bed length, or the distance between centers; and horsepower generated. See turning machine.
- machining center
machining center
CNC machine tool capable of drilling, reaming, tapping, milling and boring. Normally comes with an automatic toolchanger. See automatic toolchanger.
- milling
milling
Machining operation in which metal or other material is removed by applying power to a rotating cutter. In vertical milling, the cutting tool is mounted vertically on the spindle. In horizontal milling, the cutting tool is mounted horizontally, either directly on the spindle or on an arbor. Horizontal milling is further broken down into conventional milling, where the cutter rotates opposite the direction of feed, or “up” into the workpiece; and climb milling, where the cutter rotates in the direction of feed, or “down” into the workpiece. Milling operations include plane or surface milling, endmilling, facemilling, angle milling, form milling and profiling.
- toolholder
toolholder
Secures a cutting tool during a machining operation. Basic types include block, cartridge, chuck, collet, fixed, modular, quick-change and rotating.
- turning
turning
Workpiece is held in a chuck, mounted on a face plate or secured between centers and rotated while a cutting tool, normally a single-point tool, is fed into it along its periphery or across its end or face. Takes the form of straight turning (cutting along the periphery of the workpiece); taper turning (creating a taper); step turning (turning different-size diameters on the same work); chamfering (beveling an edge or shoulder); facing (cutting on an end); turning threads (usually external but can be internal); roughing (high-volume metal removal); and finishing (final light cuts). Performed on lathes, turning centers, chucking machines, automatic screw machines and similar machines.