Humans love to automate things. Since the day some prehistoric farmer slipped a harness around the neck of an unsuspecting animal, people have striven to reduce their manual efforts and improve the efficiency of their work. In manufacturing, starting with the 19th century’s first steam-powered lathes, automation technology has evolved to the point where lights-out machining is common, and labor costs are less of an issue.
Affordably Automated
One machine tool historically passed over for parts-handling and probing automation has been the vertical machining center. Unlike their horizontal cousins—most of which are equipped with built-in pallet changers, rotary tables and large tool magazines that make them ideal for automated machining—VMCs, as a rule, are basic affairs, suitable for low-volume work and a limited range of workpiece sizes. Walk into most shops and the sexiest thing you’ll see on a VMC is an indexing table or a pair of vises.
VMCs have one big advantage over horizontals, however—they’re inexpensive. Consider that a typical horizontal costs $200,000, perhaps far more. A decent vertical is half that price. Bolt on an aftermarket pallet changer and even a basic VMC gains much of the automation capability seen in its more expensive counterpart.
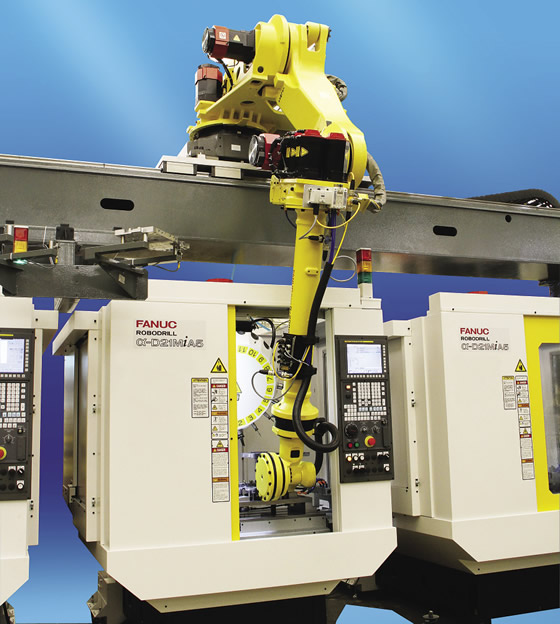
Courtesy of FANUC America
A gantry-mounted robot can service several VMCs from a single platform.
Mike Cayley Jr., vice president of manufacturing for Midaco Corp., Elk Grove Village, Ill., said the number of shops taking this route is on the rise. “We’re selling pallet changers to just about everybody.”
The biggest advantage to pallet changers, Cayley explained, is increased uptime. The machine is not sitting idle while the operator wrangles with a vise handle or blows chips off a fixture prior to loading a workpiece. For $40,000 and a day or so for installation, Midaco will be happy to fly a technician to your site, cut a big hole in the end of a VMC and bolt on a shiny new pallet changer.
The result is a device that can automatically swap an entire machine table’s worth of parts in a few seconds via an M code sent by the control. This frees the operator to tend other equipment, check parts, prepare the next job or load the next pallet. And increasing spindle time by just 1 hour per day at a $75 hourly shop rate means a 2-year return on investment. But, as Cayley pointed out, many shops see ROI much faster than that by eliminating several hours of daily downtime, depending on the application.
Myriad Mechanizations
Paul Robinson, automation manager at Florence, Ky.-based Mazak Corp., probably can’t help you retrofit a pallet changer for a VMC from another builder, but he’s more than willing to outfit a new Mazak with one from the factory, an increasingly popular option. “At least 50 percent of all machines we sell have some form of automation. For a vertical, that could be a simple two-position pallet changer, an articulated robot or a Palletech suitable for multiple machines,” he said.
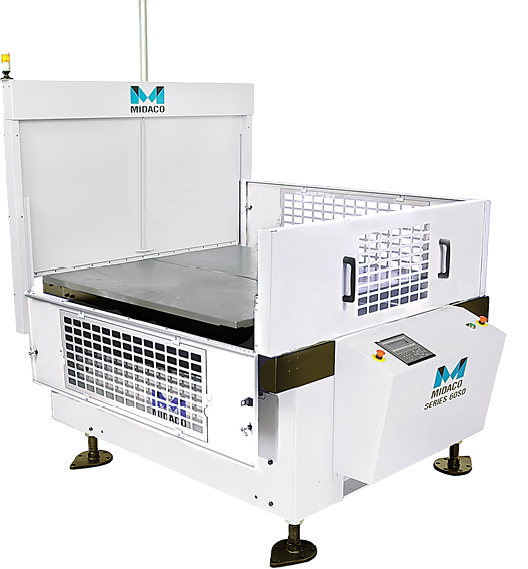
Courtesy of Midaco
A Midaco automatic pallet changer with safety guards in place.
Robinson added that in the past, only large job shops and automotive OEMs bought automated systems, while today even small shops are considering automation to improve their capabilities and productivity in the face of smaller lot sizes. “They need the flexibility to change setups quickly, and, in some cases, do so automatically,” he said. “If the machine and automation has all the necessary tooling and programs preloaded, then all that’s required is a schedule of what job to run next. Shops can change over on the fly.”
Taking automation to the next level takes more than a pallet changer, however, and additional capabilities are needed to have your machine tools dance solo. “One of the first things you should consider is the number of tools you’ll need,” Robinson said. “Many 20 "×40 " VMCs have 20 to 30 tools. This is frequently not enough for multiple pallets, especially if you want to accommodate additional setups and redundant tooling.”
Another consideration is coolant. Robinson recommends beefing up the coolant pump and filtration systems to handle an automated system’s increased productivity. Systems of 1,000 psi or more are readily available, providing an effective way to flush chips out of holes and pockets, particularly for lights-out machining. And increased coolant pressure reduces heat at the cutting edge and evacuates chips, helping to assure predictable tool life for those long, lonely nights. Finally, both of these goals are best served by clean cutting fluid—manufacturers of high-pressure coolant systems typically recommend filtration levels of better than 25µm to remove fine swarf and prevent catastrophic coolant interruption.
Robust Robotics
Methods Machine Tools Inc. is another company offering automated machines. John Lucier, automation manager for the Sudbury, Mass.-based machine supplier, explained that a large percentage of its automation projects are on verticals. “For many applications, we see auto-loaded VMCs as a great alternative to horizontals. They’re especially well-suited for smaller shops, where floor space is at a premium.”
Some of this automation comes in the form of gantry loaders. Often used for high-volume production, these stork-like devices straddle the top of a machine tool. The gantry arm, equipped with a gripper, plucks a casting or cut blank off a carousel. The blank is carried to the VMC’s work area and delivered to the workholding device, where it is swapped with the finished workpiece.
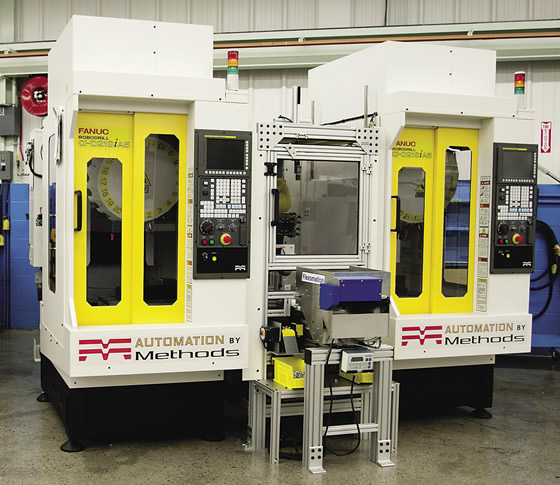
Courtesy of Methods Machine Tools
A Methods RoboDrill Twin Cell with two FANUC RoboDrills is serviced by a robot.
Lucier said gantry loaders are an effective solution for many applications, but while articulating robots usually cost more, they do offer enhanced flexibility. “Gantry loaders require more planning up front. The rail length is fixed when you buy one, so you can’t just decide one day to incorporate a wash station into your automated process or add a second machine to the cell. There’s not a lot of extra room with a gantry, so they don’t handle a variety of workpiece sizes very well, and, since most utilize a PLC rather than a CNC, programming for different jobs can be a bit more challenging.”
With an articulating robot, juggling the work typical for most job shops is straightforward, Lucier explained. As long as the workpiece, other mach-ine tools or ancillary equipment is with-in reach of the robot’s arm, modifying the process flow involves reprogram- ming its CNC and possibly changing the grippers.
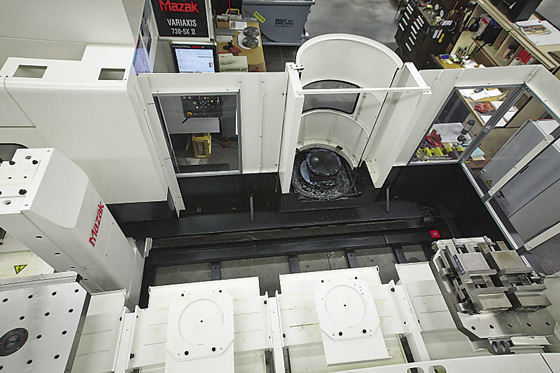
Courtesy of Mazak
Choice Precision Inc., Whitehall, Pa., uses a double-level, 12-pallet stocker station Palletech manufacturing system paired with a Mazak Variaxis 730-5X II 5-axis VMC.
Adding a robot to a VMC can cost as much as the machine itself—Methods’ JobShop Cell, for example, starts at around $85,000. Designed for use with a FANUC RoboDrill VMC, the JobShop cell comes with a FANUC 200iC 6-axis robot, integrated parts conveyors and double-gripper end-of-arm tooling. Add to that engineering, tooling and integration costs, and the final price tag is in the low six figures.
Articulating robots can handle parts like a human. Flipping a part for a secondary operation is no problem; nor is manipulating that workpiece beneath a deburring wheel or swishing it through a parts washer. Yet these “wonder machines” aren’t very bright. When the operator is removed from the parts-handling equation, foolproofing the entire system is critical. Aside from the improvements in coolant and chip evacuation mentioned previously, Lucier said verification of part loading and orientation is also needed and can be accomplished via proximity switches on the robot’s gripper arm. If the part is crooked or missing, the robot waits for human intervention.
No More Mistakes
Another way to poke-yoke (Japanese for “mistake-proof”) an automated VMC is with air gaps, which can be installed as follows. Drill a hole 1/16" or so in diameter where the workpiece seats into the vise or fixture. Drill an intersecting hole for a compressed air line, then wire an inline electronic pressure gage to the machine control. The system can now sense if the part is loaded improperly upon clamping and phone its human master for help.
Some shop owners might think this is too complicated. Modifications to the VMC, workholding and even the machining process itself make an already complex manufacturing setup even more so. Is it worth the hassle?
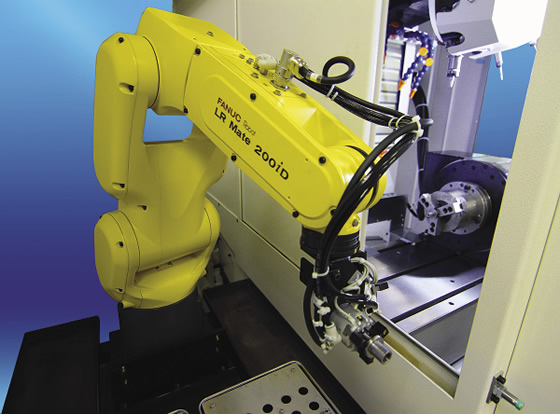
Courtesy of FANUC America
A FANUC robot loads parts into a rotary table.
Michael J. Cicco, general manager of distribution sales for FANUC America Corp., Hoffman Estates, Ill., gives a resounding yes. “Robots work through lunch. They never take a break. And the instant a part is finished, the robot is there to unload it. Robots increase spindle utilization and reduce load/unload time, easily justifying the cost and learning curve associated with implementing an automated system.”
Maybe you’re convinced, but are still worried about setting up and programming another machine, one that’s alien to your shop. Don’t fret. Robots are easier to program and operate than R2D2.
“We use the same hardware as on our CNCs, so the architecture is very similar,” Cicco explained. “It uses simple commands: open or close the grippers, wait for the machine, close the door, that sort of thing. You tell it to move to a certain point in space and it goes there. About the only information that’s required are the part dimensions and load/unload positions, and rest is fairly automatic.”
Nor is tooling a robot difficult. Cicco said various grippers are available, many of which are quick-change. Some even come with servomotors, making them infinitely adjustable and capable of a grip firmer than a politician’s handshake. Best of all, robots can be added to just about any VMC, even ones old enough to remember the Reagan administration. “Newer CNCs offer cool features such as automatic offset changes and integrated gaging, but even the most ancient machine can be outfitted with robotics,” Cicco said.
Programmed Probes
If you’re not making good parts, all the automation in the world is worthless. That’s where Sharad Mundra comes in. As the Mida probing product manager for Marposs Corp., Auburn Hills, Mich., Mundra said touch probes make a valuable contribution to an automated VMC. Probes automatically set tools, establish workpiece coordinates, measure parts in-process and make offsets, check cutting tools for wear or breakage and call for replacement tools. They shut the process down and phone a friend when the machining train goes off the tracks.
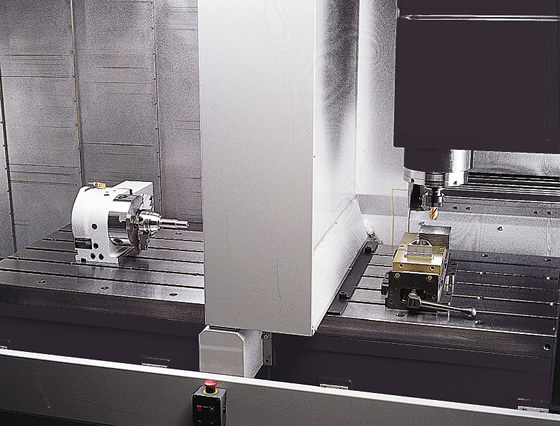
Courtesy of Mazak
A vertical turning center with a fixed table and removable center partition, such as this one from Mazak, provides an inexpensive two-pallet changer option and can connect to NC rotary tables and continuous-connection hydraulic fixtures.
Mundra said in-process probing can even take the place of a coordinate measuring machine. To those who worry about cutting and measuring parts on the same machine, Mundra pointed out that with the right probe, CAD-based NC measurement software and proper machine calibration, most features can be reliably measured on-machine.
Automated inspection does require additional programming, though, and may mean tossing traditional macro-style probing functions in favor of in-process measurement software. “Macros become very complicated as you move to in-situ inspection,” Mundra said. “Taking a few points to measure a hole, for example, is no problem for a macro. But when you need to measure hole-to-hole relationships to a datum or measure profiles or complex features, that’s when a math engine comes into the picture, eliminating the use of macros.”
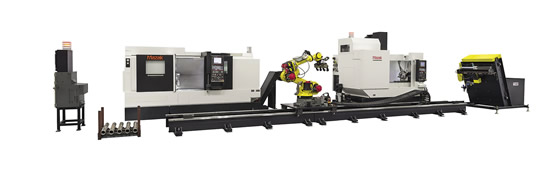
Courtesy of Mazak
A track-mounted robot tends a Mazak vertical turning center and VMC.
According to Mundra, math engines are used with software that can automatically generate probing G code and feature relationships based on a part’s CAD model. Marposs’ version is called 3DSI, but third-party systems, such as Capps-NC, are available. Whichever way you go, automating inspection on a VMC is made much simpler with a high-quality probe and software to drive it through complex measurement routines.
Automating your VMC is a great way to improve the bottom line. Considering the shortage of skilled labor, automation increases spindle uptime and gets more parts out the door. Pallet changers, gantry loaders, robotic parts handling and in-process inspection probing are mature technologies, but understanding what’s available and then investing appropriately can still give you a leg up on the competition. CTE
Contributors
FANUC America Corp.
(888) 326-8287
www.fanucamerica.com
Marposs Corp.
(248) 370-0404
www.marposs.com
Mazak Corp.
(859) 342-1700
www.mazakusa.com
Methods Machine Tools Inc.
(877) 668-4262
www.methodsmachine.com
Midaco Corp.
(888) 593-8420
www.midaco-corp.com
Related Glossary Terms
- calibration
calibration
Checking measuring instruments and devices against a master set to ensure that, over time, they have remained dimensionally stable and nominally accurate.
- computer numerical control ( CNC)
computer numerical control ( CNC)
Microprocessor-based controller dedicated to a machine tool that permits the creation or modification of parts. Programmed numerical control activates the machine’s servos and spindle drives and controls the various machining operations. See DNC, direct numerical control; NC, numerical control.
- computer-aided design ( CAD)
computer-aided design ( CAD)
Product-design functions performed with the help of computers and special software.
- coolant
coolant
Fluid that reduces temperature buildup at the tool/workpiece interface during machining. Normally takes the form of a liquid such as soluble or chemical mixtures (semisynthetic, synthetic) but can be pressurized air or other gas. Because of water’s ability to absorb great quantities of heat, it is widely used as a coolant and vehicle for various cutting compounds, with the water-to-compound ratio varying with the machining task. See cutting fluid; semisynthetic cutting fluid; soluble-oil cutting fluid; synthetic cutting fluid.
- fixture
fixture
Device, often made in-house, that holds a specific workpiece. See jig; modular fixturing.
- in-process gaging ( in-process inspection)
in-process gaging ( in-process inspection)
Quality-control approach that monitors work in progress, rather than inspecting parts after the run has been completed. May be done manually on a spot-check basis but often involves automatic sensors that provide 100 percent inspection.
- machining center
machining center
CNC machine tool capable of drilling, reaming, tapping, milling and boring. Normally comes with an automatic toolchanger. See automatic toolchanger.
- numerical control ( NC)
numerical control ( NC)
Any controlled equipment that allows an operator to program its movement by entering a series of coded numbers and symbols. See CNC, computer numerical control; DNC, direct numerical control.
- robotics
robotics
Discipline involving self-actuating and self-operating devices. Robots frequently imitate human capabilities, including the ability to manipulate physical objects while evaluating and reacting appropriately to various stimuli. See industrial robot; robot.
- swarf
swarf
Metal fines and grinding wheel particles generated during grinding.
- turning
turning
Workpiece is held in a chuck, mounted on a face plate or secured between centers and rotated while a cutting tool, normally a single-point tool, is fed into it along its periphery or across its end or face. Takes the form of straight turning (cutting along the periphery of the workpiece); taper turning (creating a taper); step turning (turning different-size diameters on the same work); chamfering (beveling an edge or shoulder); facing (cutting on an end); turning threads (usually external but can be internal); roughing (high-volume metal removal); and finishing (final light cuts). Performed on lathes, turning centers, chucking machines, automatic screw machines and similar machines.