Joe’s struggling to package a truckload of parts before noon. Mary can’t keep up on the painting line. Jimmy’s in trouble with the boss because he can’t make quota. These are just a few of the challenges faced by workers on the manufacturing floor, problems that, in many cases, can be solved with collaborative robots.
More affectionately known as “cobots,” collaborative robots are opening new possibilities in manufacturing. In this brave new world, cobots and humans work side by side in a common space not segregated by fences or walls. Need to hand deburr a few hundred parts, or insert bushings into thousands of assemblies? Grab a cobot, show it what to do and go back to whatever intelligent task you were doing.
Cobots are perfectly happy getting stuck with the short end of the manufacturing stick and won’t complain about doing the dirty, dull and dangerous tasks we humans grumble about.
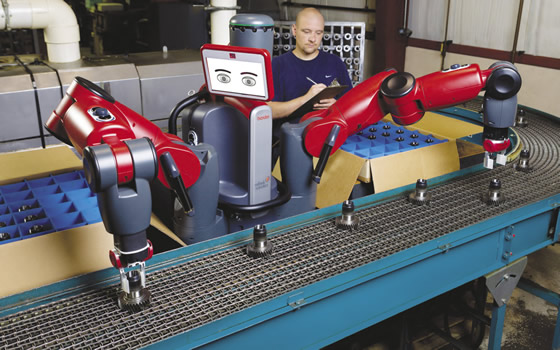
Courtesy of Rethink Robotics
Baxter from Rethink Robotics works side-by-side with humans.
But what are cobots, and how are they different from the robotic arms that load material in CNC machine tools and weld car chassis? The complete, mind-numbing details are available in the robotics safety specification ANSI/RIA R15.06-2012, jointly published by the American National Standards Institute and the Robotic Industries Association. Briefly put, the spec describes collaborative operations as ones where the robot monitors its surroundings and slows down or stops in the presence of a human, where force and power are limited in a work space shared by humans and robots, or where the robot is manually guided by a human.
Bob Doyle, director of communications for RIA, pointed out several additional differentiators between cobots and their stronger, faster and more accurate counterparts. The first is safety. Interfere with an assembly line drone as it bolts wheels onto an F-150 and you might be headed to the emergency room. Granted, safety barriers make this an unlikely situation, but unless using sharp or very heavy objects are part of its duties, injury such as this could never happen around a collaborative robot.
Cobots are also much easier to set up and program than their less human-friendly cousins. “Traditional robotic systems may take months of working with an integrator to implement,” Doyle said. “With a collaborative robot, you can often take it out of the box and have it working the way you want within half a day.”
Sweeping Up
Another factor is cost. Where many industrial robots run upwards of $100,000 after they’re tooled up and integrated with a machine tool or assembly line, cobots start at around $20,000 and don’t require a team of skilled technicians to hook them up. One of these is Baxter by Rethink Robotics Inc., Boston.
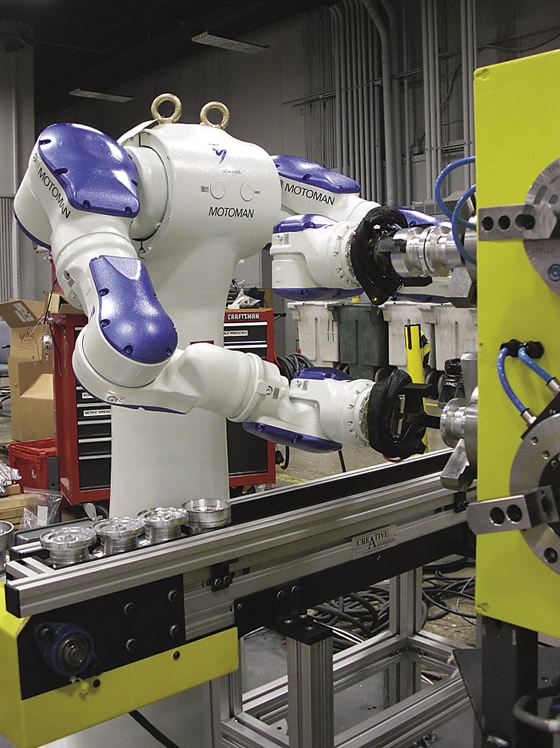
Courtesy of Yaskawa Motoman
This SDA dual-arm cobot is from Yaskawa Motoman.
Baxter is an example of a new breed of robots, ones that don’t have to be bolted to the floor or situated in a specific place to operate. These mechanical designated hitters utilize force-sensing technology and embedded vision to recognize objects and react in ways not possible with other industrial robots.
Cobots fill a need that the traditional robotics industry has ignored, according to Jim Lawton, chief marketing officer for Rethink. The long-held paradigm of specific types of automation for specific tasks—for example, welding, applying paint or performing a particular assembly operation—has led to a rigid, expensive automation platform. Worse, in places where robots would fall down on the job, production volumes don’t warrant investment in robotics, or the environment is too flexible for a robot’s set way, a human is plopped in to fill the gaps.
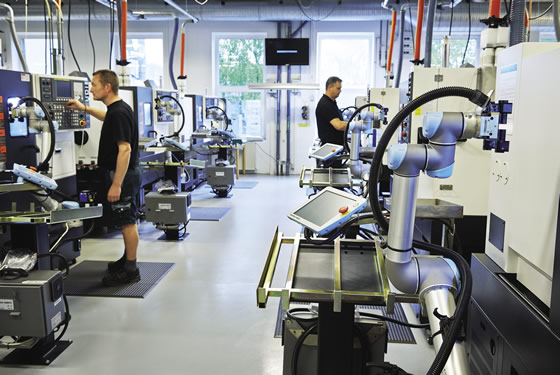
Courtesy of Universal Robots USA
Trelleborg Sealing Solutions in Denmark went from having no robots to having 42 UR robots in 2 years. The robots at Trelleborg enable one worker to manage a cell with eight CNC machines in operation.
According to Lawton, this sort of inflexible technology leads to using automation in places where it doesn’t make sense, creating barriers to innovation and continuous improvement. And while robot manufacturers have worked diligently to bring their wares out of the cage, he said this is not enough. “When we talk about collaborative, it means far more than removing the cage. It means robots that can work side by side with people, performing tasks companies have thus far been unable to automate in that environment.”
These include routine chores, such as counting parts or stuffing boxes, and dangerous tasks where a human might be injured or suffer repetitive motion injuries. In either case, Lawton explained, manufacturers need smart, capable robots that can bridge the gap between traditional, high-volume automation and an imperfect-yet-intelligent human labor force.
‘Owning’ the Robot
Baxter’s not alone. Edward Mullen, national sales manager for Universal Robots USA Inc., East Setauket, N.Y., said his UR-5 and UR-10 robot arms are for companies that either can’t afford or don’t want to rely on external integrators for their robotic needs.
“We’ve designed them so production workers can take ownership of the robot,” Mullen said. “They can set it up to do one thing today, but then reallocate the robot to do something completely different tomorrow.”
Like most collaborative robots, Universal’s URbot utilizes force-limiting technology, which enables it to recognize a collision and stop quickly enough to avoid impact. It performs this feat via smart joints which, if robots were humans, would be its wrists, elbows and shoulders.
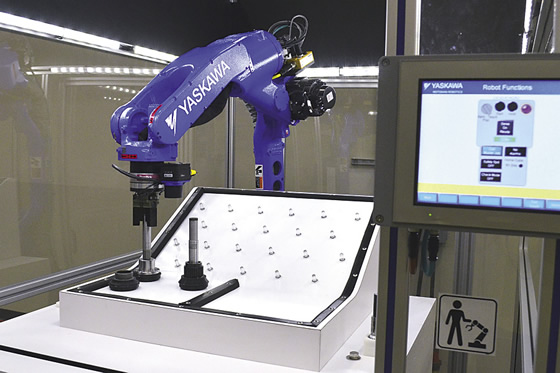
Courtesy of Yaskawa Motoman
Yaskawa Motoman says its Functional Safety Unit makes Motoman robots safe for collaborative environments where people interact with the robot during production.
Each smart joint contains a servomotor and electronics that allow it to model anticipated payload, trajectory and power requirements, and differentiate between the force required to do its job and that which occurs when running into a human or another unexpected obstruction.
Agile automation, the ability to quickly adapt robotics to a dynamic manufacturing environment, adds flexibility to the production floor. By eliminating the need for protective cages and lengthy, complicated installations, Mullen said even small manufacturers can now afford robots without sacrificing the valuable real estate consumed by traditional automation.
“Applying conventional technology in a 15- to 20-person shop doing short runs and high product mix doesn’t make sense,” he said. “The return on investment takes many years. By comparison, cobots provide a flexible piece of automation that can be moved around quickly and easily, with a typical payback time of 8 to 10 months.”
Suppose you’ve decided to stick a Universal cobot in front of a CNC machine. Now what? According to Mullen, there’s no need for a complex machine interface. Users can teach the cobot how to push the cycle-start button and open the machine door, eliminating much of the wiring and input/output work that comes with most robot installations. Many of the functions usually performed by a machine operator can be learned simply by dragging the cobot’s arm through the desired motions and telling it when to open and close its gripper.
Beyond Force-Limited
Yaskawa Motoman, a Miamisburg, Ohio-based division of Yaskawa Electric, is another company making robots easier to program and operate. As Tim DeRosett, director of strategic initiatives, explained, automotive manufacturers or their suppliers account for more than half of the robots in use, providing a large base of companies with the expertise to install and support those robots.
That’s good news for the automotive industry, but it doesn’t do much for mom-and-pop shops. “Unfortunately, the average machine shop or other small manufacturer may not have the expertise or know-how to deploy industrial robots, and it would be expensive to hire the resources to do so,” DeRosett said. “By recognizing that need and making it easier for those folks to adopt our products, robotic suppliers will help grow the overall market.”
That market extends beyond force-limited cobots. As mentioned previously, the definition of collaborative includes robots that look and act much like those used to install seats in a minivan or dispense glue on chair legs, but that slow down or stop when a human worker comes too close.
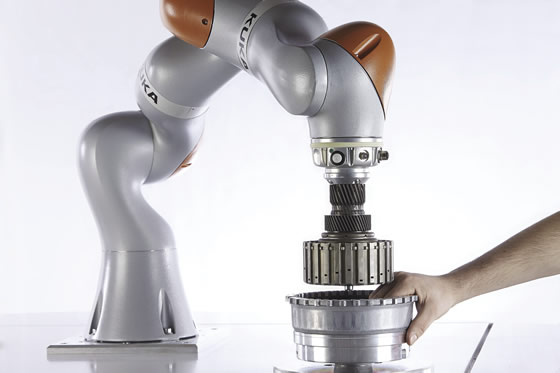
Courtesy of KUKA Robotics
There’s no risk of injury with a collaborative robot. Here a worker safely puts his hand in the path of the robot as it performs gear assembly.
Intelligent robots that take their more mobile and unpredictable human masters into consideration open the door to automation in nonmanufacturing environments as well. Whether it’s stuffing envelopes, manning the copy machine, changing bed linens or assisting the disabled, cobots will become increasingly prevalent in all aspects of our world. Robots have even made their way into the operating room.
One company with extensive experience in this area is KUKA Robotics Corp., Shelby Township, Mich. Corey Ryan, manager of medical robotics, said collaboration means many things to many people, but its most fundamental definition is about robots helping people.
Nowhere is this clearer than in the medical field. For example, one of KUKA’s partners uses collaborative robot technology to accurately find a predefined point in 3D space, improving control during delivery of radiation to cancer patients. In addition, the Children’s National Medical Center, Washington, D.C., has developed a robotic suturing system to assist physicians during surgical closure, and robots can measure and respond to the force applied by injured patients, making cobots tireless forces for physical rehabilitation.
These same capabilities work equally well in manufacturing. The control and sensitivity of force-sensing robots allows them to perform tasks that standard robots simply can’t do, such as gear meshing. “It’s very difficult,” Ryan said. “Traditional robots do little more than go from point A to point B, and have little regard for what’s in the way. Use one of these for gear meshing and the result is a set of stripped gears.”
By comparison, force-sensing robots, which KUKA calls lightweight, or LBR, robots are able to mimic the human hand. An LBR can feel whether the gears are aligned, give them a little jiggle when they don’t quite fit or adjust the force if there’s any resistance, just like a person would do.
What About My Job?
When it comes to robots in manufacturing, the writing’s on the wall. The RIA’s Bob Doyle said the robotics market in North America set a new record for the first half of 2014 and was expected to close the year with 15 to 20 percent growth. For those concerned about a robot giving them a pink slip, however, don’t fret. During this same time period, unemployment has decreased, a trend that Doyle said has repeated itself several times over the past 2 decades.
Robots aren’t about to completely replace humans, at least not anytime soon. Those interviewed for this article agreed that robots have a positive influence on employment levels. Companies that employ robots alongside people are ultimately more efficient and, therefore, more likely to win new business, hire more people and create additional opportunities for its employees. Most importantly, robots are content inserting tab A into slot B all day long. They don’t take breaks or complain, allowing humans to spend more time thinking about ways to make the company even better. That’s collaboration everyone can appreciate. CTE
![]() |
About the Author |
Contributors
KUKA Robotics Corp.
(866) 873-5852
www.kuka-robotics.com
Rethink Robotics Inc.
(617) 500-2487
www.rethinkrobotics.com
Robotic Industries Association
(734) 994-6088
www.robotics.org
Universal Robots USA Inc.
(631) 610-9664
www.universal-robots.com
Yaskawa Motoman
(937) 847-6200
www.motoman.com
Related Glossary Terms
- computer numerical control ( CNC)
computer numerical control ( CNC)
Microprocessor-based controller dedicated to a machine tool that permits the creation or modification of parts. Programmed numerical control activates the machine’s servos and spindle drives and controls the various machining operations. See DNC, direct numerical control; NC, numerical control.
- payload ( workload)
payload ( workload)
Maximum load that the robot can handle safely.
- robotics
robotics
Discipline involving self-actuating and self-operating devices. Robots frequently imitate human capabilities, including the ability to manipulate physical objects while evaluating and reacting appropriately to various stimuli. See industrial robot; robot.