The foundation of robust and successful CNC milling and drilling processes consists of numerous elements, including high-quality machine tools, sturdy workholders and high-performance cutting tools.
Toolholders are another of the basic elements. Thumb through trade publications and catalogs and you will see an almost limitless variety of toolholders and options. It can be difficult to sort through the options and opinions.
Collet chucks may well be the most common type because they provide a great deal of value. Collets and collet chucks are relatively inexpensive compared to other types of toolholders. A countless number of sizes are available and each collet in a series will grip a range of tool sizes. Collet chucks provide good runout and gripping force characteristics for all but the most challenging operations. The most common collet styles are ER, TG and DA.
DA collets are the least expensive of the three and provide acceptable runout when performing light-duty milling, but can cause runout problems when performing close-tolerance holemaking operations such as reaming. They can also diminish the ability of high-performance drills to produce tight-tolerance holes, so avoid DA collets for those applications.
TG collets are the most expensive of the group and provide the highest gripping force because of their size and length. TG collets also offer better runout characteristics than DA collets and can be coerced into setups that produce close-tolerance holes. TG collets are an excellent choice for holding tools larger than 7/8" (22.2mm) in diameter and for use in machines with large spindle tapers, such as CAT 50. However, I don’t see TG collets offered in many catalogs. When I do, they are not prominently positioned, which leads me to believe TG collets are losing favor.
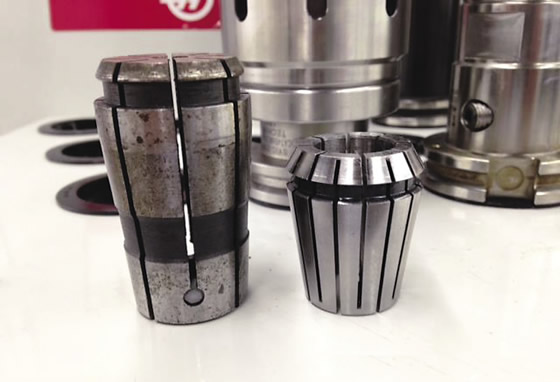
The length of the TG collet (left) provides a large contact area with the cutting tool, enhancing gripping force compared to the ER 32 collet (right).
ER collets probably provide the best value and are my first choice when tooling a new machine. They have the gripping force needed to perform many milling operations and have excellent runout characteristics. When paired with high-performance drills, reaming can be eliminated. ER collets can be found in a large range of sizes, from 0.020 " to 13/8" (0.51mm to 34.9mm).
As high-speed machining and aggressive milling become increasingly common, collets sometimes do not provide adequate gripping force. When an operation is too aggressive for the collet chuck, chatter occurs and can cause the cutting tool to pull out of the holder. Mechanical milling chucks present a possible solution to these problems.
These chucks grip a tool shank by means of mechanical deformation and provide substantially more gripping force than a collet. Because they are also much larger than collet chucks, their extra mass helps dampen vibration that can lead to chatter.
Milling chucks are more expensive than collet chucks but are easy to justify when tools pull out and scrap parts. I learned an expensive lesson while milling combustion components for gas turbines. I was using a 25mm (0.98"), high-helix endmill held in an ER 40 collet chuck to mill a part worth close to $100,000. The first operation was a cut around the part periphery followed by endmilling. Unfortunately, the endmill pulled out on the first cut, and, on the second cut, I removed too much stock because the tool was extended too far. Fortunately, we were able to correct the mistake with welding and remachine the part. Our second and more successful attempt was with the endmill held firmly in a milling chuck.
Hydraulic chucks are similar to milling chucks and, as the name implies, use oil to generate pressure and deform the holder’s ID around the tool shank. They are the most expensive of the types described and tend to have slightly better runout characteristics while providing excellent gripping force. The real benefit is their slim design, which allows more clearance around parts and fixtures than collet chucks or mechanical milling chucks.
A discussion about toolholders would not be complete without mentioning shrink-fit holders, which are uniquely simple in design and function. Shrink-fit holders are heated by means of induction; when the proper temperature is reached, the ID of the holder grows larger than the tool shank’s diameter. Tools are slipped into the holder and, when cooled, the holder shrinks to provide an interference fit with the tool. Shrink-fit holders have minimal runout and provide a gripping force that rivals that of hydraulic and milling chucks.
Shrink-fit holders do not require any internal passages or hardware to function. Lack of internal hardware means they are slimmer than any other toolholders. Lack of internal mechanisms also means long shrink-fit holders are more economical than long hydraulic or mechanical holders. Length is only limited by the capability of the machine tool.
Shrink-fit holders are used extensively in complex 5-axis machining and moldmaking because of their ability to maintain excellent runout characteristics over a long tool length, and because they can be used in tight places. Although shrink-fit holders are less costly than equivalent hydraulic holders, they require additional equipment to heat them.
Like other tooling decisions, determining the best type of holder depends on the application. DA and TG collet chucks are good tools to have but neither is my first choice when tooling a new machine. ER collet chucks are probably the best all-around toolholder when considering performance, cost and flexibility. Mechanical milling chucks are my first choice for heavy-duty milling because they are robust, relatively inexpensive and reliable. I consider hydraulic and shrink-fit holders to be the elite choices, because they are more expensive than other toolholders. Therefore, I use them only in situations where nothing else will work. CTE
About the Author: Christopher Tate is senior advanced manufacturing engineering for Milwaukee Electric Tool Corp., Brookfield, Wis. He is based at the company’s manufacturing plant in Jackson, Miss. He has 19 years of experience in the metalworking industry and holds a Master of Science and Bachelor of Science from Mississippi State University. E-mail: chris23tate@gmail.com.
Related Glossary Terms
- chatter
chatter
Condition of vibration involving the machine, workpiece and cutting tool. Once this condition arises, it is often self-sustaining until the problem is corrected. Chatter can be identified when lines or grooves appear at regular intervals in the workpiece. These lines or grooves are caused by the teeth of the cutter as they vibrate in and out of the workpiece and their spacing depends on the frequency of vibration.
- chuck
chuck
Workholding device that affixes to a mill, lathe or drill-press spindle. It holds a tool or workpiece by one end, allowing it to be rotated. May also be fitted to the machine table to hold a workpiece. Two or more adjustable jaws actually hold the tool or part. May be actuated manually, pneumatically, hydraulically or electrically. See collet.
- clearance
clearance
Space provided behind a tool’s land or relief to prevent rubbing and subsequent premature deterioration of the tool. See land; relief.
- collet
collet
Flexible-sided device that secures a tool or workpiece. Similar in function to a chuck, but can accommodate only a narrow size range. Typically provides greater gripping force and precision than a chuck. See chuck.
- computer numerical control ( CNC)
computer numerical control ( CNC)
Microprocessor-based controller dedicated to a machine tool that permits the creation or modification of parts. Programmed numerical control activates the machine’s servos and spindle drives and controls the various machining operations. See DNC, direct numerical control; NC, numerical control.
- endmill
endmill
Milling cutter held by its shank that cuts on its periphery and, if so configured, on its free end. Takes a variety of shapes (single- and double-end, roughing, ballnose and cup-end) and sizes (stub, medium, long and extra-long). Also comes with differing numbers of flutes.
- endmilling
endmilling
Operation in which the cutter is mounted on the machine’s spindle rather than on an arbor. Commonly associated with facing operations on a milling machine.
- gang cutting ( milling)
gang cutting ( milling)
Machining with several cutters mounted on a single arbor, generally for simultaneous cutting.
- inner diameter ( ID)
inner diameter ( ID)
Dimension that defines the inside diameter of a cavity or hole. See OD, outer diameter.
- metalworking
metalworking
Any manufacturing process in which metal is processed or machined such that the workpiece is given a new shape. Broadly defined, the term includes processes such as design and layout, heat-treating, material handling and inspection.
- milling
milling
Machining operation in which metal or other material is removed by applying power to a rotating cutter. In vertical milling, the cutting tool is mounted vertically on the spindle. In horizontal milling, the cutting tool is mounted horizontally, either directly on the spindle or on an arbor. Horizontal milling is further broken down into conventional milling, where the cutter rotates opposite the direction of feed, or “up” into the workpiece; and climb milling, where the cutter rotates in the direction of feed, or “down” into the workpiece. Milling operations include plane or surface milling, endmilling, facemilling, angle milling, form milling and profiling.
- milling machine ( mill)
milling machine ( mill)
Runs endmills and arbor-mounted milling cutters. Features include a head with a spindle that drives the cutters; a column, knee and table that provide motion in the three Cartesian axes; and a base that supports the components and houses the cutting-fluid pump and reservoir. The work is mounted on the table and fed into the rotating cutter or endmill to accomplish the milling steps; vertical milling machines also feed endmills into the work by means of a spindle-mounted quill. Models range from small manual machines to big bed-type and duplex mills. All take one of three basic forms: vertical, horizontal or convertible horizontal/vertical. Vertical machines may be knee-type (the table is mounted on a knee that can be elevated) or bed-type (the table is securely supported and only moves horizontally). In general, horizontal machines are bigger and more powerful, while vertical machines are lighter but more versatile and easier to set up and operate.
- shank
shank
Main body of a tool; the portion of a drill or similar end-held tool that fits into a collet, chuck or similar mounting device.
- toolholder
toolholder
Secures a cutting tool during a machining operation. Basic types include block, cartridge, chuck, collet, fixed, modular, quick-change and rotating.