Before vehicle wheels roll into the market, up to 80 geometric features relevant to their function, such as radial and axial runout, width and diameter, are typically inspected randomly with tactile measurement devices under laboratory conditions away from the production line. The procedure consumes about 45 to 60 minutes per wheel, making 100 percent inspection of the wheels impossible.
The “Wheelinspector” overcomes those inspection obstacles, reports the Fraunhofer Institute for Factory Operation and Automation IFF, which developed the measurement system with Ascona GmbH, Meckenbeuren, Germany, a manufacturer of optical profile measurement systems.
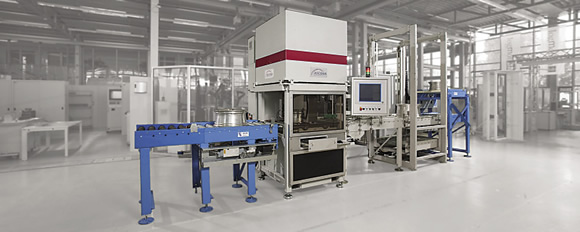
The “Wheelinspector” makes noncontact measurement of vehicle wheels directly in the production process.
“The system makes fully optical, noncontact measurement of light- alloy wheels directly in the production process possible for the first time,” said Ralf Warnemünde, deputy manager of the measurement and testing technology business unit at Fraunhofer IFF. “Immediately after they have been machined, that is, turned, milled and drilled, the new 3-D laser technology compares finished products with their 3-D CAD model. It scans a multitude of geometric features and, with a cycle time of 20 seconds to inspect one wheel, can be fully integrated into the production flow.”
In addition, the institute stated that deviations of parts resulting from tool wear or breakage are reported to the machines immediately, preventing serial defects and cost-effectively optimizing production processes.
The basis of the measurement system is the OptoInspect 3-D technology developed at Fraunhofer IFF. The system projects laser light and measures points and lines through triangulation. A camera registers the projection light reflected diffusely by the parts. Based on that perspective, the laser projection in the camera image changes according to the wheel’s shape.
The measurement system includes four sensors and axes for moving and positioning the sensors during measurement. The institute explained that after wheels are moved into the measuring unit on a conveyor, they are centered and mechanically locked into place. An image-based identification system recognizes the wheel type and transmits specific feature information to the measuring unit. These coordinates are used to align each of the positioning axes of the sensors to their correct positions. The sensor cluster revolves around the wheel 360° and scans the measured values.
For more information about Fraunhofer Institute for Factory Operation and Automation IFF, Magdeburg, Germany, call +49 391-4090-0 or visit www.iff.fraunhofer.de. CTE
Related Glossary Terms
- 3-D
3-D
Way of displaying real-world objects in a natural way by showing depth, height and width. This system uses the X, Y and Z axes.
- computer-aided design ( CAD)
computer-aided design ( CAD)
Product-design functions performed with the help of computers and special software.