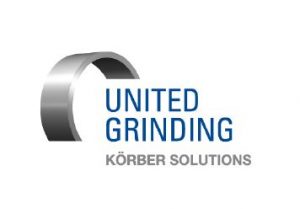
United Grinding North America Inc., Miamisburg, Ohio, will host "The Artistry of the Grinding Universe Event" April 18-19 at its new 110,000-sq.-ft. headquarters. The free 2-day educational event will give attendees an opportunity to explore the latest grinding technologies, automation and measurement systems that provide the turnkey solutions required to keep pace in today's evolving manufacturing landscape.
During the event, application engineers will perform machine demonstrations on a wide variety of WALTER, STUDER, EWAG and BLOHM machines. Attendees will learn how ID/OD, creep feed, centerless, radius, universal – with an emphasis on bearing grinding in shoes – thread grinding and other modern grinding techniques can improve productivity and boost part quality. Industry experts from all of UNITED GRINDING’s brands will be on hand to discuss the latest technologies and address specific grinding challenges.
Among the machines in action will be the WALTER HELITRONIC VISION 400 L, a high-precision CNC tool grinding machine that can grind lengths up to 16.5" and a BLOHM PROFIMAT MT, a high-performance production grinding machine. The company will also showcase an EWAG Laser Line Precision machine to show the latest technology for manufacturing cutting tools out of superhard materials. In addition, several of the latest model STUDER machines will be in operation, and attendees will get a virtual sneak peek at new expanded models of STUDER machines.
Another highlight at the event will be a series of educational presentations by industry experts from UNITED GRINDING and key grinding machine ancillary suppliers. Topics will include grinding process automation, coolant and filtration, abrasive and workholding solutions, inspection technologies and Factory 4.0 Digitization.
"This event is a great opportunity for manufacturers to get an up-close look at the state-of-the-art for all things grinding." said Steve Jacobson, President and CEO of United Grinding North America Inc. "Attendees will walk away with practical knowledge they can use to optimize their overall grinding process and have an opportunity to explore our new facility, which opened in November 2017, and enables us to offer the complete grinding experience, all under one roof."
Please visit www.grinding.com/universe to register for The Artistry of the Grinding Universe Event.
Contact Details
Related Glossary Terms
- abrasive
abrasive
Substance used for grinding, honing, lapping, superfinishing and polishing. Examples include garnet, emery, corundum, silicon carbide, cubic boron nitride and diamond in various grit sizes.
- computer numerical control ( CNC)
computer numerical control ( CNC)
Microprocessor-based controller dedicated to a machine tool that permits the creation or modification of parts. Programmed numerical control activates the machine’s servos and spindle drives and controls the various machining operations. See DNC, direct numerical control; NC, numerical control.
- coolant
coolant
Fluid that reduces temperature buildup at the tool/workpiece interface during machining. Normally takes the form of a liquid such as soluble or chemical mixtures (semisynthetic, synthetic) but can be pressurized air or other gas. Because of water’s ability to absorb great quantities of heat, it is widely used as a coolant and vehicle for various cutting compounds, with the water-to-compound ratio varying with the machining task. See cutting fluid; semisynthetic cutting fluid; soluble-oil cutting fluid; synthetic cutting fluid.
- feed
feed
Rate of change of position of the tool as a whole, relative to the workpiece while cutting.
- grinding
grinding
Machining operation in which material is removed from the workpiece by a powered abrasive wheel, stone, belt, paste, sheet, compound, slurry, etc. Takes various forms: surface grinding (creates flat and/or squared surfaces); cylindrical grinding (for external cylindrical and tapered shapes, fillets, undercuts, etc.); centerless grinding; chamfering; thread and form grinding; tool and cutter grinding; offhand grinding; lapping and polishing (grinding with extremely fine grits to create ultrasmooth surfaces); honing; and disc grinding.
- grinding machine
grinding machine
Powers a grinding wheel or other abrasive tool for the purpose of removing metal and finishing workpieces to close tolerances. Provides smooth, square, parallel and accurate workpiece surfaces. When ultrasmooth surfaces and finishes on the order of microns are required, lapping and honing machines (precision grinders that run abrasives with extremely fine, uniform grits) are used. In its “finishing” role, the grinder is perhaps the most widely used machine tool. Various styles are available: bench and pedestal grinders for sharpening lathe bits and drills; surface grinders for producing square, parallel, smooth and accurate parts; cylindrical and centerless grinders; center-hole grinders; form grinders; facemill and endmill grinders; gear-cutting grinders; jig grinders; abrasive belt (backstand, swing-frame, belt-roll) grinders; tool and cutter grinders for sharpening and resharpening cutting tools; carbide grinders; hand-held die grinders; and abrasive cutoff saws.