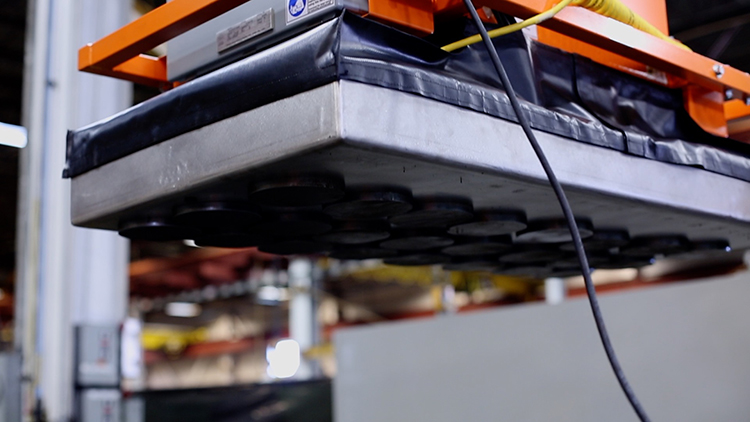
Family-owned and -operated since 1968, Brannon Steel built a strong reputation as one of North America’s premier suppliers of carbon steel parts-to-print.
Brannon’s 200,000-square-foot facility in Brampton, Ontario, Canada, houses state-of-art manufacturing equipment, giving the capacity and redundancy to ensure an uninterrupted supply of parts. The company has become well known for its wide range of capabilities, such as beveling, flame-cutting, high-definition plasma cutting, laser cutting, plasma bevel cutting, saw cutting, cleaning, and packaging, and forming and flattening.
Brannon is dedicated to quality and safety in all areas. This commitment includes selecting only the most advanced equipment and machinery for use within its facility. When the company needed a lift magnet for its plasma cutting table, management chose an Eriez Full Coverage Lift Magnet. This powerful magnet has been exceeding expectations since September 2018, according to Brannon Steel purchaser Dave Lee.
“Brannon Steel has been cutting strips out of a 60-inch by 360-inch sheet of 3/16-inch thick steel. These strips range in widths from 6 to 12 inches, usually almost the full 360-inch length,” says Lee. “We’ve been using Eriez APL Lift Magnets with great success for quite some time for most of our other cutting tables, but they weren’t appropriate for this particular application due to the thin steel and long flexible parts. We contacted the Eriez sales office to see what alternatives they may have, and they introduced us to their Full Coverage System.
After Eriez and Brannon discussed the installation requirements, operating procedures, and safety benefits of the system, the Full Coverage Lift Magnet was perfectly suited for the facility and operational requirements. However, the company’s due diligence didn’t stop there. They decided to investigate other magnet system suppliers to determine if any could provide a competitively priced system with the features and performance offered by Eriez.
Full Coverage Lift Magnet Performance
“After more research, we decided to go forward with Eriez,” Lee says. “The past performance of Eriez’s smaller permanent lift magnets and history of stellar customer service gave us all the confidence we needed. We knew we would receive a quality product and solid local after-sales support from Eriez.”
Lee says that once the new system arrived, they integrated it into their crane controls. “We started seeing the benefits almost immediately. The operators were able to not only clear the cut parts off the table much more efficiently and safely, but they also loaded full sheets onto the table with the same performance,” he adds.
Lee explains that the Eriez Full Coverage Lift Magnet was a game-changer for Brannon in terms of improved safety and reduced labor requirements. He says, “Prior to installing the Eriez system, parts removal involved two operators manually removing 350-inch-long strips of steel from the cutting table and stacking them on a long skid. The process was very labor intensive and involved the operators often walking on the cutting table, which the management team wanted to avoid at any cost.”
The Eriez system enables operators to unload the long strips without having to climb up on the table. The magnet system also reduces the unload time of a 60-inch by 360-inch sheet from 1.5 hours down to about 15 minutes. This time reduction adds incredible efficiency to the operation. Lee points out, “We’ve more than quadrupled our output on this table as a result.”
Lee continues, “The Eriez system provides huge time savings because we no longer need to manually remove the strips from the cutting table. This system was built specifically to fit the Brannon Steel application, but this style magnet has the versatility to handle a large variety of sheet and part sizes.” He notes, “Competitors we explored could not customize their systems to our exact needs as economically as Eriez did with their system. Our new system uses standard designed components in an assembly that accommodates our steel sheet and part sizes. However, because the individual magnets can be rearranged, we can handle other applications, if necessary.”
Brannon Steel’s Commitment to Safety and Quality
Brannon Steel’s size allows the company to offer many customer advantages, including a 24-hour work cycle, direct mill buying privileges, and the flexibility to quickly respond to customers’ needs. Brannon is highly committed to innovation and cultivates a company culture that encourages creative solutions from all team members. Continual and significant investments in the latest technology and a dedication to research and development-oriented projects keep the company on the leading edge.
Brannon Steel‘s commitment to safety and quality is demonstrated through its ISO 9001 and ISO 14001 certifications. It also uses Lean Manufacturing and Six Sigma Tools. In addition, Brannon Steel’s KanBan, Kitting, and JIT programs are supported by fully integrated ERP, EDI and barcoding capabilities to ensure tight quality control and tracking capabilities.
Burn Table Design
Moving numerous parts from a burn table can be a very time-consuming process. Eriez’s new air-operated Burn Table Full Coverage Lift Magnet System utilizes a large, full-contact magnetic surface area to move multiple cut parts from the burn table in a single lift. The magnetic circuit design eliminates gaps on the surface, enabling the magnet to pick up skeletons as well.
Another benefit of the Eriez design is the ability to pick up single sheets of thinner material from a stack for table loading, down to a 3/16-inch sheet. This feature eliminates the need for spacers between individual sheets and adds efficiency to table loading as well. The full coverage capabilities eliminate manual handling and the need for operators to climb on the table, resulting in safer, more efficient burn table operation.
Operation of the system requires only an overhead hoist and an air supply. The simple solenoid valve on the unit can wire into existing crane controls, whether it’s a wired pendant control or hands-free radio control. The air source can be from shop air or a small, dedicated compressor mounted above on the crane bridge. The permanent magnet circuit eliminates costly lift magnet controllers and safety concerns due to power failures. The system is also very energy efficient, requiring only a small amount of air to cycle fully.
Contact Details
Related Glossary Terms
- just-in-time ( JIT)
just-in-time ( JIT)
Philosophy based on identifying, then removing, impediments to productivity. Applies to machining processes, inventory control, rejects, changeover time and other elements affecting production.
- lean manufacturing
lean manufacturing
Companywide culture of continuous improvement, waste reduction and minimal inventory as practiced by individuals in every aspect of the business.
- milling machine ( mill)
milling machine ( mill)
Runs endmills and arbor-mounted milling cutters. Features include a head with a spindle that drives the cutters; a column, knee and table that provide motion in the three Cartesian axes; and a base that supports the components and houses the cutting-fluid pump and reservoir. The work is mounted on the table and fed into the rotating cutter or endmill to accomplish the milling steps; vertical milling machines also feed endmills into the work by means of a spindle-mounted quill. Models range from small manual machines to big bed-type and duplex mills. All take one of three basic forms: vertical, horizontal or convertible horizontal/vertical. Vertical machines may be knee-type (the table is mounted on a knee that can be elevated) or bed-type (the table is securely supported and only moves horizontally). In general, horizontal machines are bigger and more powerful, while vertical machines are lighter but more versatile and easier to set up and operate.
- quality assurance ( quality control)
quality assurance ( quality control)
Terms denoting a formal program for monitoring product quality. The denotations are the same, but QC typically connotes a more traditional postmachining inspection system, while QA implies a more comprehensive approach, with emphasis on “total quality,” broad quality principles, statistical process control and other statistical methods.
- sawing machine ( saw)
sawing machine ( saw)
Machine designed to use a serrated-tooth blade to cut metal or other material. Comes in a wide variety of styles but takes one of four basic forms: hacksaw (a simple, rugged machine that uses a reciprocating motion to part metal or other material); cold or circular saw (powers a circular blade that cuts structural materials); bandsaw (runs an endless band; the two basic types are cutoff and contour band machines, which cut intricate contours and shapes); and abrasive cutoff saw (similar in appearance to the cold saw, but uses an abrasive disc that rotates at high speeds rather than a blade with serrated teeth).
- shop air
shop air
Pressurized air system that cools the workpiece and tool when machining dry. Also refers to central pneumatic system.