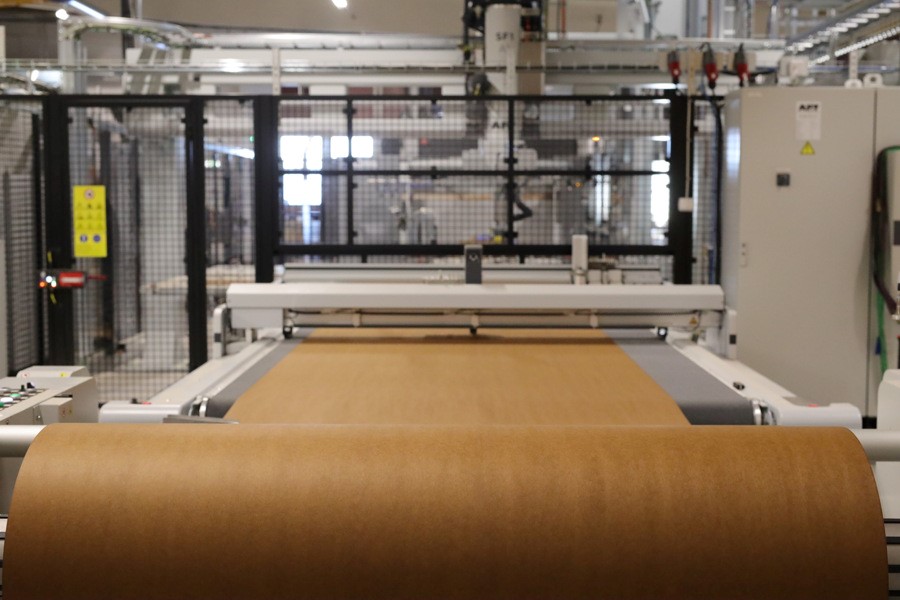
Swedish startup PaperShell has developed a cellulose fiber composite that they refer to as “wood metal” and it can be formed into flat or complex-shaped components.
The company says it is hard, strong, heat- and water-resistant and has an exceptionally low climate and environmental impact – all traits that make it an extremely interesting alternative to artificial composites, metal and some plastics.
Some of PaperShell’s targeted customer segments are the automotive industry, architects and manufacturers of sporting goods, interior design and electronics. To industrialize their manufacturing process, the company contacted AP&T in 2020.
“We turned to AP&T for numerous reasons – primarily, because it is a Swedish company with solid experience of meeting the stringent requirements of the automotive industry,” says Fredrik Westerberg, Production Manager at PaperShell.
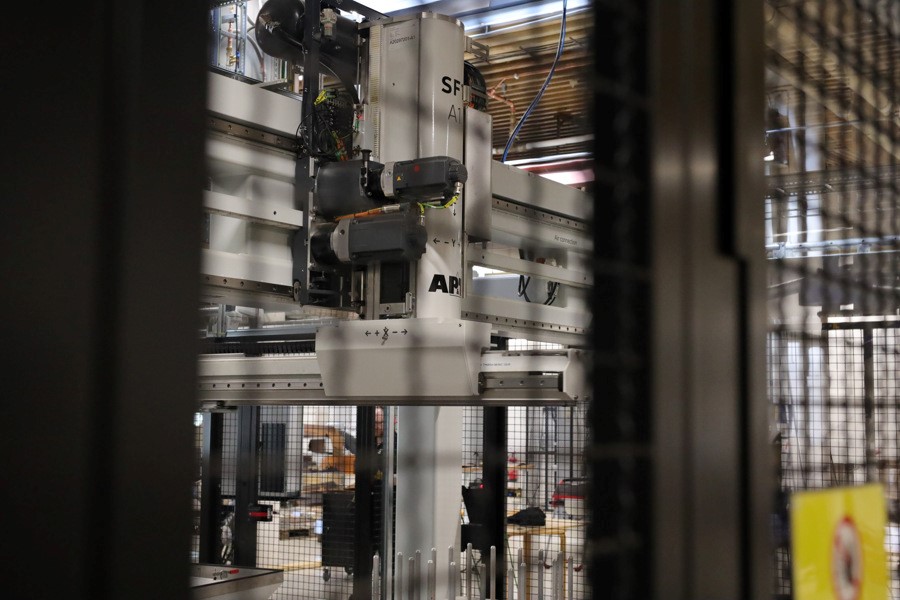
The first steps of the collaboration between the companies were taken when the Research Institutes of Sweden (RISE) used an AP&T servo hydraulic press to test-form bio-composites. Employed at RISE at the time, Westerberg collaborated with the AP&T team to develop a line concept for large-scale production of bio-composites. Westerberg intensified these efforts when he became PaperShell’s production manager.
Fully automated and energy-efficient
With the new material’s specific characteristics in mind, PaperShell and AP&T developed a fully automated, flexible and energy-efficient production line concept making it possible to rationally and efficiently manufacture components for many different areas of application using one line.
“We truly believe in PaperShell and their new material. It is very exciting to be part of realizing a production solution starting from the test environment and moving on to its industrialization, all the while dealing with process control and flexibility challenges. The fact that we can now make a contribution to creating sustainable components and products is fully in line with our own sustainability ambitions,” said Patrik Haglund, business development manager at AP&T.
Today, one production line is already running for test-manufacturing in PaperShell’s factory in Tibro. Operations will scale up during the course of 2024 with more lines being brought online to increase capacity.
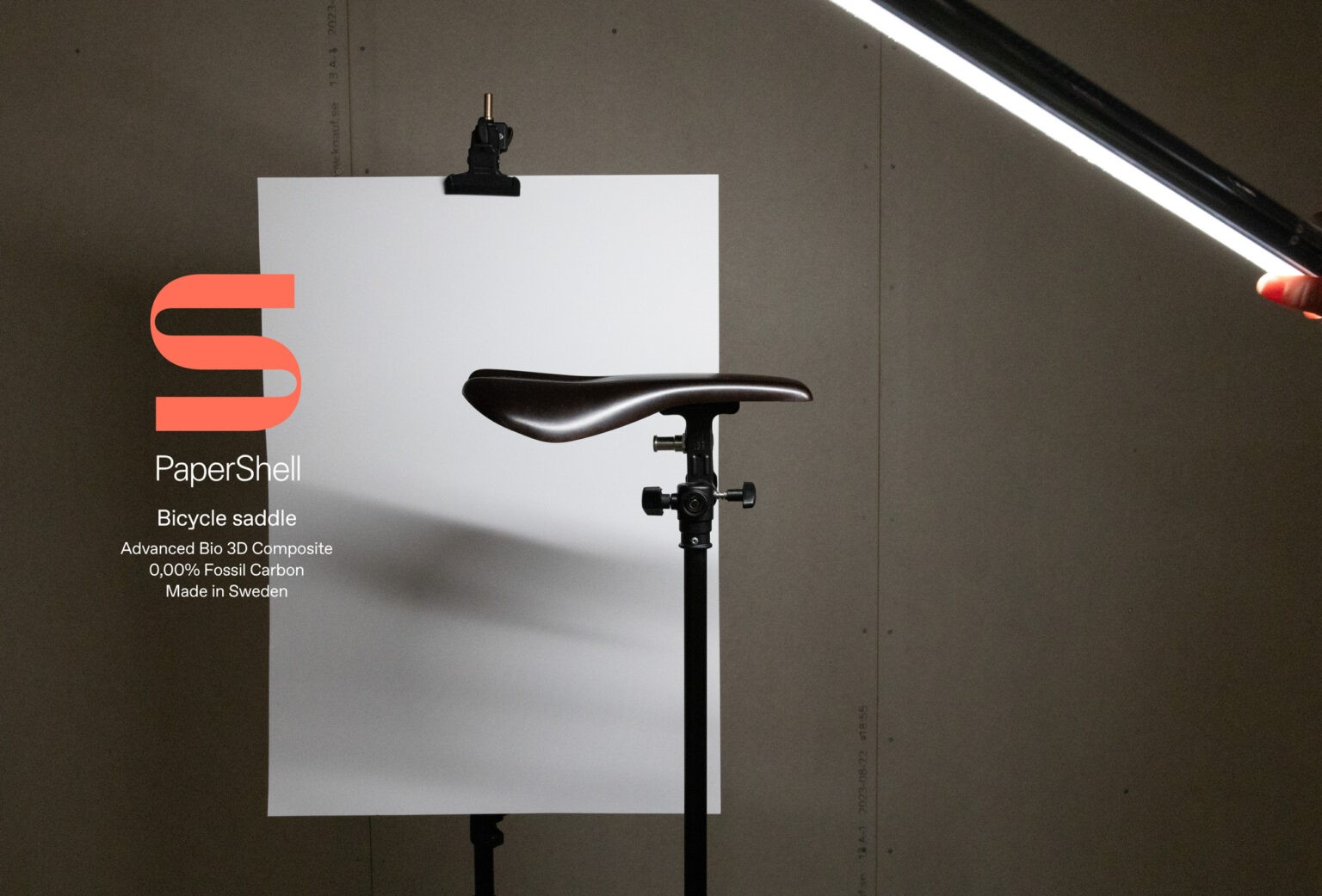
The manufacturing process is fully automated. The raw material is reinforced paper on rolls, which is cut into “blanks”, pressed and formed at elevated temperatures. According to Haglund, the magic is in the combination of heat, pressure and a binding agent.
To minimize the need for intermediary storage, labeling, cutting, stacking and inspection are all done in the same line, and all under the supervision of the line’s process monitoring system which ensures that the end products are of the right quality.
“The technical level of the equipment is on par with the most current press-hardening lines we deliver around the world. This lays the foundation for a stable, secure and extremely energy-efficient process,” he said.
Contact Details
Related Glossary Terms
- composites
composites
Materials composed of different elements, with one element normally embedded in another, held together by a compatible binder.
- flat ( screw flat)
flat ( screw flat)
Flat surface machined into the shank of a cutting tool for enhanced holding of the tool.
- process control
process control
Method of monitoring a process. Relates to electronic hardware and instrumentation used in automated process control. See in-process gaging, inspection; SPC, statistical process control.