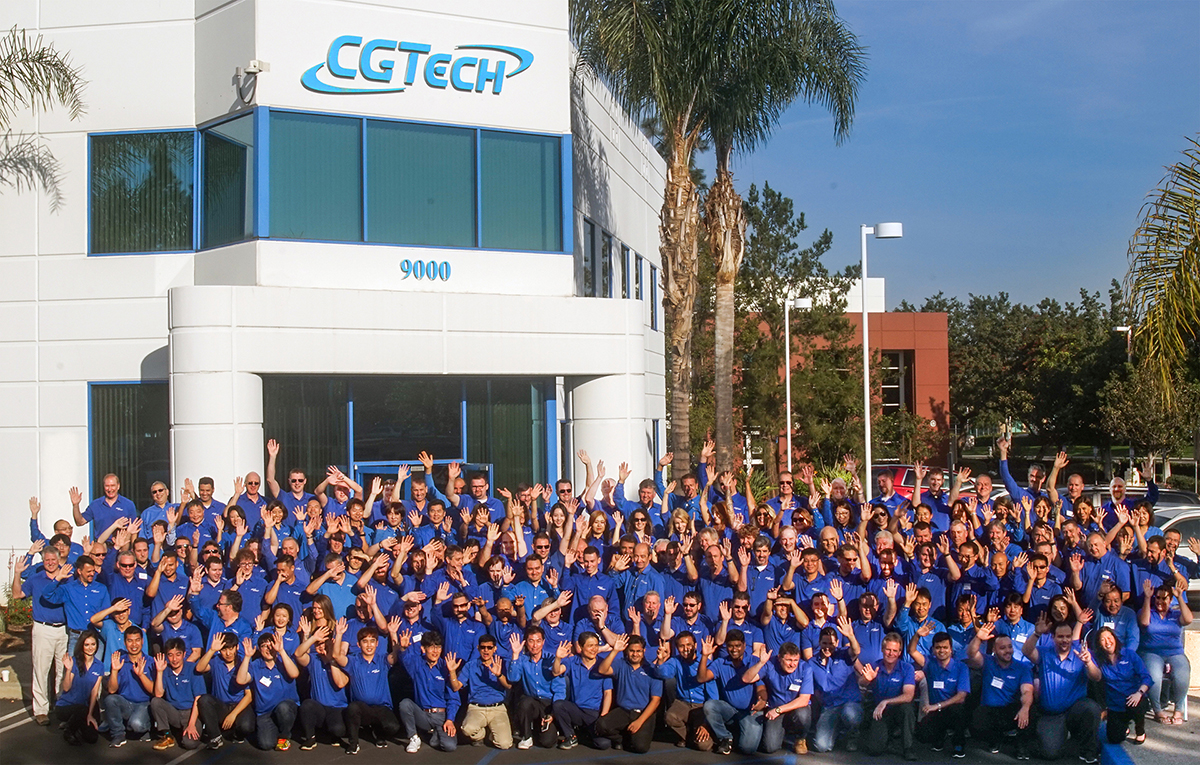
CGTech, the Irvine, California-based developer of VERICUT CNC machine simulation software, celebrated 35 years of growth and innovation in CNC simulation and optimization in 2023.
“Whether it's milling, turning, mill-turning or any other CNC-machining, VERICUT is the industry standard to simulate CNC machines, as well as optimize and verify NC programs,” said Margaret Schmitt, president of CGTech.
“For 35 years, CGTech’s technology leadership and experienced team have helped VERICUT evolve together with our customer base. CGTech’s solutions are deeply entrenched in the aerospace industry’s history and adopted today across industries ranging from oil and gas to Formula 1 racing. People are at the heart of CGTech’s success and have made it what it is today: an innovative software company driven by team spirit and customer care.”
CGTech was founded by Jon Prun in 1988 when he recognized the need to verify NC tool path programs without taking valuable machining time to prove-out a part. VERICUT was the first widely available method to test machine tool paths in a virtual environment. The software has grown to be the leader in the NC program verification space and has since expanded its original capabilities to include physics-based optimization with its Force module, composites programming and simulation, as well as additive and hybrid processes.
VERICUT is 100% developed in-house by software engineers and leaders experienced in manufacturing and the CAD/CAM space. Improvements are made with each release to support complex multi-axis kinematics, further reduce cycle times, increase tool life, and further optimize the simulation. New features are also continuously being developed, including live CNC machine monitoring features, tool performance optimization, and more.
“In my 30+ years with CGTech, it has been amazing to see this company grow globally, to satisfy even the most demanding NC manufacturing needs. I’m so proud to be part of the abundantly knowledgeable and creative staff at CGTech,” said Gene Granata, director of product management. “Together, we truly enjoy applying our collective experience to supporting our valued customers, helping them be more competitive and create parts as efficiently and safely as possible.”
Contact Details
Related Glossary Terms
- composites
composites
Materials composed of different elements, with one element normally embedded in another, held together by a compatible binder.
- computer numerical control ( CNC)
computer numerical control ( CNC)
Microprocessor-based controller dedicated to a machine tool that permits the creation or modification of parts. Programmed numerical control activates the machine’s servos and spindle drives and controls the various machining operations. See DNC, direct numerical control; NC, numerical control.
- gang cutting ( milling)
gang cutting ( milling)
Machining with several cutters mounted on a single arbor, generally for simultaneous cutting.
- milling
milling
Machining operation in which metal or other material is removed by applying power to a rotating cutter. In vertical milling, the cutting tool is mounted vertically on the spindle. In horizontal milling, the cutting tool is mounted horizontally, either directly on the spindle or on an arbor. Horizontal milling is further broken down into conventional milling, where the cutter rotates opposite the direction of feed, or “up” into the workpiece; and climb milling, where the cutter rotates in the direction of feed, or “down” into the workpiece. Milling operations include plane or surface milling, endmilling, facemilling, angle milling, form milling and profiling.
- numerical control ( NC)
numerical control ( NC)
Any controlled equipment that allows an operator to program its movement by entering a series of coded numbers and symbols. See CNC, computer numerical control; DNC, direct numerical control.
- turning
turning
Workpiece is held in a chuck, mounted on a face plate or secured between centers and rotated while a cutting tool, normally a single-point tool, is fed into it along its periphery or across its end or face. Takes the form of straight turning (cutting along the periphery of the workpiece); taper turning (creating a taper); step turning (turning different-size diameters on the same work); chamfering (beveling an edge or shoulder); facing (cutting on an end); turning threads (usually external but can be internal); roughing (high-volume metal removal); and finishing (final light cuts). Performed on lathes, turning centers, chucking machines, automatic screw machines and similar machines.