Humans make mistakes. Machines don’t,” said Kevin O’Neil, regional sales manager for the Southwest U.S. territory at Hermle USA Inc. in Franklin, Wisconsin. O’Neil covers California, Arizona, Colorado, Utah and New Mexico.
By having a 5-axis machine to access five sides of a part in one setup, manufacturers of mission-critical aerospace components can increase part accuracy and reduce scrap by not having to re-fixture workpieces as many times as would be needed in a 3-axis machine, O’Neil explained. Fewer part setups equal less human interference. “Generally speaking, the vast majority of 5-axis work can be done on two ops as opposed to a lot of customers still doing it the old-school, 3-axis way, and having to do three or four flips.”
One of his projects, he added, involved machining a part that required 14 operations and reducing it to two. “Let’s allow the machine to do what it’s supposed to do and keep the hands out of it as much as possible.”
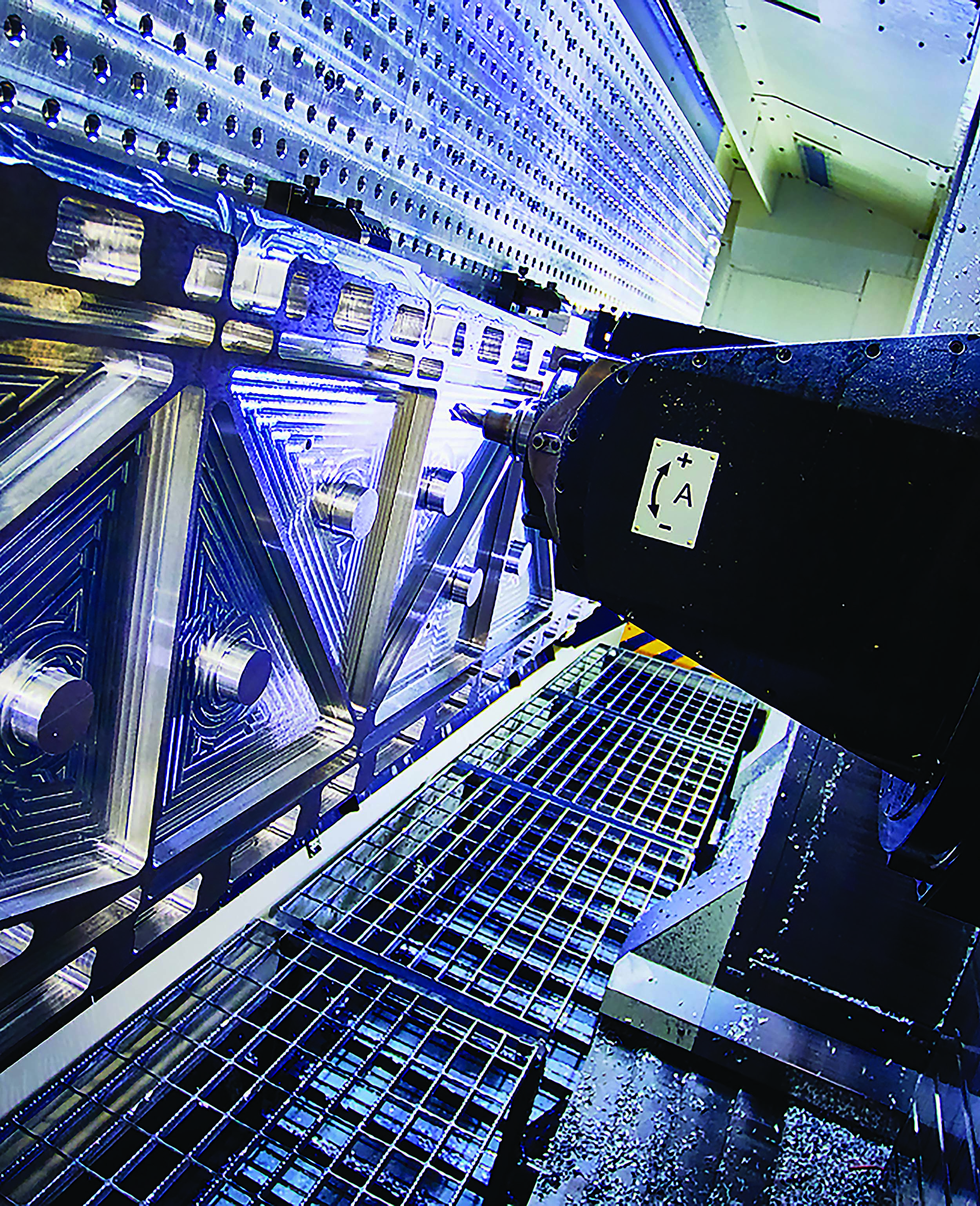
In his territory, O’Neil estimated that 60% to 65% of the machine tool builder’s nine models of 5-axis machines are purchased by aerospace customers and at least half for the company as a whole. Vertical machining center models, or 5-axis trunnions, are more prevalent than horizontals. All models of Hermle machines are built as simultaneous 5-axis machines, but many applications only require 3+2 machining, which still allows access to five sides of a part.
Instead of 3+2 machining, Makino Inc. prefers 2+3, said Karl Lippert, manager of the 5-axis advanced technology group for the Mason, Ohio, machine builder. The first number refers to the two rotary axes for positioning the workpiece to establish the best line of sight access for a tool normal to a feature. The second number is for the three linear axes used to machine the part. “Most of the aerospace work is 2+3 in the Makino vernacular.”
Across the Horizon
A newer addition to Makino’s 5-axis line, Lippert noted, is the aZ family of horizonal machining centers: a500Z, a800Z and a900Z. The machines are based on the company’s 4-axis platform. “We turned it into a 5-axis machine by altering the pallet carrier structure providing a tilt axis on the pallet.”
The arrangement keeps the pallet work requirements for the fixture and part all at the center of gravity within the bearing arrangement on the table, “which is somewhat unique to other kinematic designs,” he said. “It allows us to be competitive from a speed standpoint but also to maintain the same or better accuracy when positioning and full 5-axis contouring.”
On the vertical side, a newer offering is the DA300P trunnion machine, Lippert said, noting that the P is for package. “We made a package machine, which allows us to fully integrate a 40-pallet magazine with a unique interface in the pallet table of the machine.”
The DA300P has a hybrid design pallet interface, he added, which is similar in nature to a Sandvik Coromant Capto trigon-style on the outside and the ability to grab like a HSK toolholder on the inside.
Lippert said Makino divides aerospace production into two types of parts: aerostructures and for the jet engine portion. The former includes wings, fuselage, cockpit area, tail section and landing gear, while the latter includes blisks, impellers, single blades and vane segments.
HMCs are more suited for aerostructure requirements, and the company’s 5-axis horizontal equipment starts at 1.5 m (59.1") and goes up to 20 m (787.4"), he said. “The hard metals side really only goes up to 5 m, but the aluminum side goes up to 20 m in a horizontal, 5-axis configuration.”
When machining aerostructures, such as beams, bulkheads, spars and ribs, or “intercostal” parts, at most 10% of the features require full simultaneous 5-axis motion, according to Lippert. The inverse is true for engine components. “These parts require over 90% full 5-axis motion just to be able to produce the part feature content efficiently and effectively.”
He estimated 25% to 35% of Makino’s 5-axis machines are sold to aerospace manufacturers. The vast majority of those machines, as well as its 3-axis offerings, have some sort of Industrial Internet of Things requirement to tie it into a data collection monitoring system. “It’s pretty much every order.”
Material Matters
New workpiece materials are sometimes introduced for both commercial and defense aerospace applications, but Hermle’s O’Neil is seeing a continuing trend toward challenging materials making up a larger share. These include nickel-base superalloys, such as Inconel, Waspaloy and Hastelloy, as well as Anviloy tungsten, 13-8 stainless steel and others. “Titanium is still a big part of this whole deal, and I’m seeing more titanium being machined.”
Although numerous 5-axis machines are designed and built for cutting aluminum, O’Neil noted that Hermle focuses on equipment for tackling the challenging materials, which tend to be pricier.
He added that the movement to difficult-to-cut materials is occurring while parts and part features are becoming more complex, which requires more machining time, and tolerances are becoming even tighter. Aerospace customers frequently adapt to the changing environment by not running at the maximum machining parameters. “I can get away with 85% because the cycle times are so long and the demand on the tolerance is so high that if I run through an evening, I’m still making money.”
Nonetheless, aluminum, especially for aerostructures, continues to be commonly machined. New grades are also being introduced, primarily for military aircraft, Lippert said. He noted that the Makino MAG-Series of 5-axis HMCs are specifically built to produce aluminum structural parts quickly and efficiently. “Our market share is probably highest in this arena.”
For hard metals, where a machine with dynamic stiffness and proper damping is more critical than high spindle speed, he said Makino purpose built its T-Series 5-axis HMCs with Titanium ADVANTiGE machining technologies, but it can also cut superalloys and precipitation-hardened stainless “all day, every day. I need max torque capability to cut these material types.”
To help operate high-performance 5-axis machines in a complicated production environment, O’Neil said the machine’s human-machine interface should be as user-friendly as a smartphone interface. As an example, he pointed to the Heidenhain TNC7 CNC, which has a graphical programming feature that allows users to work directly with the part drawing on the touchscreen and interactively guides the user through the entire process.
“Obviously, I’m not going to say go out there and cut a 5-axis part if your experience is operating an iPhone,” O’Neil said, “but as far as navigating through it, yeah, you can pick it up as long as you can understand how to operate a phone.”
Moving On Up
To help transition smoothly from three to five axes, O’Neil noted that high-end CAM software plays a significant role. “The beauty of having 5-axis is you can edge break every surface simply. It’s all become CAM-driven now. You really need to step up if you’re going to step into high-end 5-axis. You have to look into what your options are for CAM software and postprocessing.”
Implementing a digital twin, or solid model, of the machine into the CAM program is beneficial and seamless, according to O’Neil. By signing a nondisclosure agreement, Hermle will provide a file of a machine’s digital twin free of charge.
Once an aerospace manufacturer has a 5-axis machine, it must be properly maintained. Lippert recommends establishing an in-house maintenance crew that understands the pitch, yaw and roll of the machine’s geometry and has the ability to measure and compensate for it. “You have to get those within spec. The next thing that needs to be done is you need to be able to accurately find the center of rotation for each rotary axis, then validate their locations with full 5-axis motion tests by tracking a tooling ball in 3D space.”
Proper maintenance reduces downtime while optimized cutting tool technology and machining software keeps the chips flying. “The tool has got to be in the part to be making money,” O’Neil said.
Contact Details
Contact Details
Related Glossary Terms
- computer numerical control ( CNC)
computer numerical control ( CNC)
Microprocessor-based controller dedicated to a machine tool that permits the creation or modification of parts. Programmed numerical control activates the machine’s servos and spindle drives and controls the various machining operations. See DNC, direct numerical control; NC, numerical control.
- computer-aided manufacturing ( CAM)
computer-aided manufacturing ( CAM)
Use of computers to control machining and manufacturing processes.
- dynamic stiffness
dynamic stiffness
Measure of a machining system’s ability to dampen vibration from a forced input. If the dynamic stiffness of a system is not sufficient to dampen vibration, chatter occurs. See static stiffness; stiffness.
- fixture
fixture
Device, often made in-house, that holds a specific workpiece. See jig; modular fixturing.
- machining center
machining center
CNC machine tool capable of drilling, reaming, tapping, milling and boring. Normally comes with an automatic toolchanger. See automatic toolchanger.
- pitch
pitch
1. On a saw blade, the number of teeth per inch. 2. In threading, the number of threads per inch.
- solid model
solid model
3-D model created using “building blocks.” This is the most accurate way of representing real-world objects in CAD.
- stiffness
stiffness
1. Ability of a material or part to resist elastic deflection. 2. The rate of stress with respect to strain; the greater the stress required to produce a given strain, the stiffer the material is said to be. See dynamic stiffness; static stiffness.
- superalloys
superalloys
Tough, difficult-to-machine alloys; includes Hastelloy, Inconel and Monel. Many are nickel-base metals.
- tolerance
tolerance
Minimum and maximum amount a workpiece dimension is allowed to vary from a set standard and still be acceptable.
- toolholder
toolholder
Secures a cutting tool during a machining operation. Basic types include block, cartridge, chuck, collet, fixed, modular, quick-change and rotating.
Contributors
Hermle USA Inc.
414-421-9770
www.hermleusa.net
Makino Inc.
866-271-65583
www.makino.com