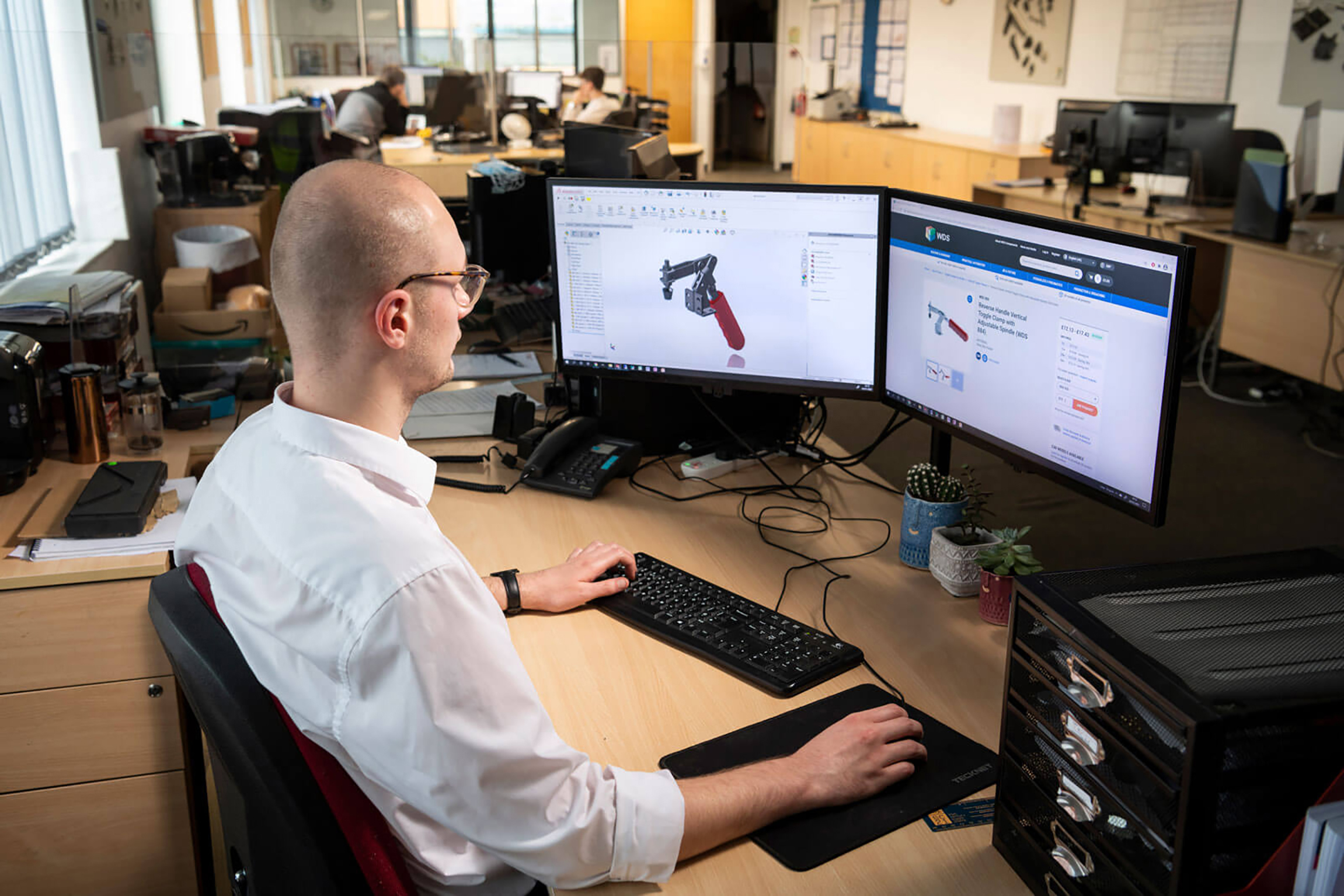
By John Marshall, technical manager at WDS Components
From castor wheels to handles, the components, standards parts and machine accessories industry has remained relatively stable in its product offering across nearly 70 years. This has been for good reason, as the design concepts behind many of these parts remain as important today as they did in the past, whether they're used in a food production factory or to adjust a modern camera tripod.
New product designs and materials have emerged since WDS Components was founded in Leeds in 1952, originally called the Woodside Die Sinking Company, but the most significant changes have taken place within manufacturing and design processes. The significance of these practices has enabled customers to design, manufacture and bring their products to market more quickly, and at more competitive prices. To maintain pace with customer requirements, WDS has progressed its technology and practices accordingly.
The automation of manufacturing
Perhaps the most significant development has been the automation of production. At outset, WDS used manually operated lathes, which formed the basis of metal cutting technology. Plug board auto lathes were the next advance before Computer Numerical Control (CNC) technology as we know it today emerged, with WDS investing heavily from the mid-1990s. CNC machines have enabled not just automated mass production, which has contributed to greater product availability at lower cost, but also a rise in consistency of production, which has reduced wastage and improved end product build quality. This is crucial for OEMs supplied by WDS that demand standardized production at sites across the globe.
Today's WDS CNC machinists are still trained in the skills of proving the design concept, although modern software that ensures aspects such as collision avoidance helps create a faster set-up. At the same time, WDS retains its traditional lathe machinery and expertise, which remains useful for one-off or limited-run manufacture of parts created on a manually operated machine.
Maintaining an in-house manufacturing capability
Despite the growth in the international supply of standard parts, WDS has continued to manufacture components onsite by retaining a highly skilled workforce and investing in the latest manufacturing technology and techniques. In 1999, WDS moved into its current site in Leeds, which today provides a modern, open-plan manufacturing facility. Further development plans have ensured that the in-house manufacturing capability will progress into the future.
Manufacturing on-site enables greater control over stock, meaning that customers aren't at the mercy of potentially long shipping times, especially for high volume orders. On-site manufacture also means greater control over product design, whether to meet customer demand and the ability to create bespoke items, or to create an exacting specification developed by WDS' R&D team. An in-house capability also ensures the quality of design and materials used, as well as greater confidence in production and its control.
Combined with in-house manufacturing, WDS also partners with international suppliers when beneficial to maximize stock volume, as well as for some components not manufactured on-site, such as plastic-based items. To enhance stock holding, the WDS headquarters includes large warehouse facilities and this enables the company to carry high stock volume across nearly all of its 20k-plus catalog of parts. This provides same-day despatch for virtually all items, as well as enabling competitive pricing.
Faster design and integration for customers
The way products are designed is the other most significant shift in the component and standard part industry. Like all industrial businesses of the era, WDS used the drawing board as the tool for product design, however by the 1980s the company was an early adopter of Computer-Aided Design (CAD) technology. For WDS, the introduction of CAD meant faster design, whether for completely new products or for new versions of existing designs. The advantage for customers was that it helped bring products to market more quickly, and it dramatically sped up their process as WDS' CAD drawings could be integrated directly into their designs.
In the 1980s, customers received 2D CAD model drawings from the WDS catalog, posted in 3.5" floppy discs. The graphical interface enabled users to browse an on-screen catalog and download 2D DXF or DWG files to integrate into designs in software packages such as AutoCAD. Fast forward to the mid-'90s, WDS adopted 3D CAD when SolidWorks was first introduced and WDS has kept pace with every software version thereafter. Being positioned at the forefront of the SolidWorks software and supply chain has enabled WDS to work closely with some of the world's largest engineering companies that are amongst its customer base.
Today, WDS provides over 20,000 3D CAD images, covering almost its entire product range, and these are free to download from wdscomponents.com. Compatibility is offered across a range of nine CAD packages, including niche packages for automotive and aerospace.
In addition to CAD, in the last ten years WDS has also introduced Coordinate Measuring Machines (CMM) inspections to measure manufactured parts and components to the highest levels of accuracy. As well as enhancing manufacturing accuracy, particularly for industries such as aerospace which requires exacting standards, it has given engineering customers greater confidence in their designs.
Global demand and rapid supply
Through the internet, WDS' business market has also changed and today the company exports worldwide. Carrying 98% of products in stock enables same-day despatch across the globe and some parts are even location-specific designed, such as the range of inch-size items typically required for the North American market.
While wdscomponents.com provides tools to select and purchase single or high volume orders of components from anywhere in the world, and new technology has enabled the company to make more products, faster, the demands of the industry's customers largely remain the same. High quality, fast availability, and competitive prices are still the most important criteria. The combination of experienced staff and new expertise will enable WDS to deliver these benefits in the future.
Contact Details
Related Glossary Terms
- computer numerical control ( CNC)
computer numerical control ( CNC)
Microprocessor-based controller dedicated to a machine tool that permits the creation or modification of parts. Programmed numerical control activates the machine’s servos and spindle drives and controls the various machining operations. See DNC, direct numerical control; NC, numerical control.
- computer numerical control ( CNC)2
computer numerical control ( CNC)
Microprocessor-based controller dedicated to a machine tool that permits the creation or modification of parts. Programmed numerical control activates the machine’s servos and spindle drives and controls the various machining operations. See DNC, direct numerical control; NC, numerical control.
- computer-aided design ( CAD)
computer-aided design ( CAD)
Product-design functions performed with the help of computers and special software.
- computer-aided design ( CAD)2
computer-aided design ( CAD)
Product-design functions performed with the help of computers and special software.
- lathe
lathe
Turning machine capable of sawing, milling, grinding, gear-cutting, drilling, reaming, boring, threading, facing, chamfering, grooving, knurling, spinning, parting, necking, taper-cutting, and cam- and eccentric-cutting, as well as step- and straight-turning. Comes in a variety of forms, ranging from manual to semiautomatic to fully automatic, with major types being engine lathes, turning and contouring lathes, turret lathes and numerical-control lathes. The engine lathe consists of a headstock and spindle, tailstock, bed, carriage (complete with apron) and cross slides. Features include gear- (speed) and feed-selector levers, toolpost, compound rest, lead screw and reversing lead screw, threading dial and rapid-traverse lever. Special lathe types include through-the-spindle, camshaft and crankshaft, brake drum and rotor, spinning and gun-barrel machines. Toolroom and bench lathes are used for precision work; the former for tool-and-die work and similar tasks, the latter for small workpieces (instruments, watches), normally without a power feed. Models are typically designated according to their “swing,” or the largest-diameter workpiece that can be rotated; bed length, or the distance between centers; and horsepower generated. See turning machine.
- numerical control ( NC)
numerical control ( NC)
Any controlled equipment that allows an operator to program its movement by entering a series of coded numbers and symbols. See CNC, computer numerical control; DNC, direct numerical control.