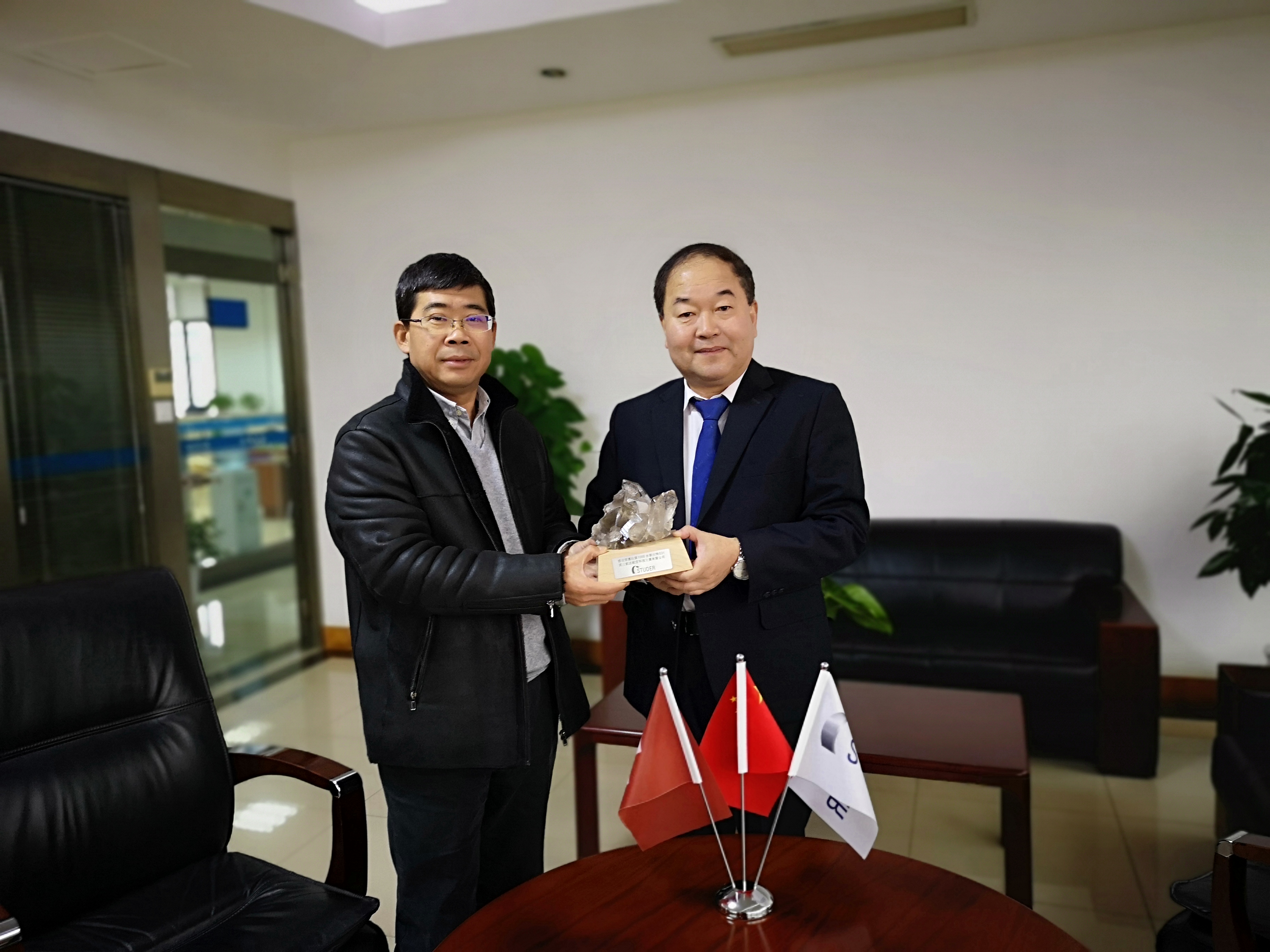
Wuhan Hangda Aero Science & Technology Development Co., Ltd. develops high-precision components for the aviation industry at the Dongxihu site in China. The company is experiencing steady growth and decided to invest in a new precision cylindrical grinding machine. After careful consideration and detailed technical discussions, Fritz Studer AG was awarded the contract for the S31. A special event: Towards the end of 2018, STUDER delivered the 1 000th S31 to Wuhan Hangda.
Reliable for complex tasks
The S31 is an all-rounder - suitable for medium-sized work-pieces in single, small and large series production. It scores in its compact size and is especially popular with contract manufacturers who have very high and often complex requirements for cylindrical grinding. 2'500 tons of Granitan® , a mineral casting that provides a vibration-damping, thermostable and wear-free machine bed, are used in 1'000 machines. An impressive figure in a successful history.
At the turn of the millennium, the first cylindrical grinding machine S31 left the halls of STUDER in Steffisburg, Switzerland, and it is still in operation today. It is installed at Shvabe Munich GmbH in Geretsried, Germany. "We are still very satisfied with our S31," says the head of the grinding department at Shvabe. The machine is in full operation for external and internal cylindrical grinding. The additional functions for form and thread grinding are used for the production of prototypes. "On the S31, as on all STUDER machines that are used in our house, I appreciate the high accuracy and that the machines are universally applicable," continues Tobias Traut. He proves that the S31 is an extremely reliable and consistent machine.
Ceremonial handover in China
Yongjun Wang, Deputy General Manager at Wuhan Hangda Aero Science & Technology Development Co., Ltd., can be pleased. With the S31 he receives a machine with the highest precision, which will pay off for Wuhan Hangda. "A STUDER cylindrical grinding machine is the guarantee for the highest quality," Yongjun Wang is convinced. A great benefit for him, apart from the advantage to grind high-precision aircraft components, are the many features such as external and internal cylindrical grinding, thread grinding and high-speed form grinding. Thus, Wuhan Hangda can realize various grinding applications on just one machine. "We already have several STUDER machines in our factory. This is also a selling point for our customers and with this we also gain their confidence, "says Yongjun Wang from his experience. With obvious pleasure he takes ownership of the 1'000th S31 in a festive setting.
Related Glossary Terms
- cylindrical grinding
cylindrical grinding
Grinding operation in which the workpiece is rotated around a fixed axis while the grinding wheel is fed into the outside surface in controlled relation to the axis of rotation. The workpiece is usually cylindrical, but it may be tapered or curvilinear in profile. See centerless grinding; grinding.
- grinding
grinding
Machining operation in which material is removed from the workpiece by a powered abrasive wheel, stone, belt, paste, sheet, compound, slurry, etc. Takes various forms: surface grinding (creates flat and/or squared surfaces); cylindrical grinding (for external cylindrical and tapered shapes, fillets, undercuts, etc.); centerless grinding; chamfering; thread and form grinding; tool and cutter grinding; offhand grinding; lapping and polishing (grinding with extremely fine grits to create ultrasmooth surfaces); honing; and disc grinding.
- grinding machine
grinding machine
Powers a grinding wheel or other abrasive tool for the purpose of removing metal and finishing workpieces to close tolerances. Provides smooth, square, parallel and accurate workpiece surfaces. When ultrasmooth surfaces and finishes on the order of microns are required, lapping and honing machines (precision grinders that run abrasives with extremely fine, uniform grits) are used. In its “finishing” role, the grinder is perhaps the most widely used machine tool. Various styles are available: bench and pedestal grinders for sharpening lathe bits and drills; surface grinders for producing square, parallel, smooth and accurate parts; cylindrical and centerless grinders; center-hole grinders; form grinders; facemill and endmill grinders; gear-cutting grinders; jig grinders; abrasive belt (backstand, swing-frame, belt-roll) grinders; tool and cutter grinders for sharpening and resharpening cutting tools; carbide grinders; hand-held die grinders; and abrasive cutoff saws.