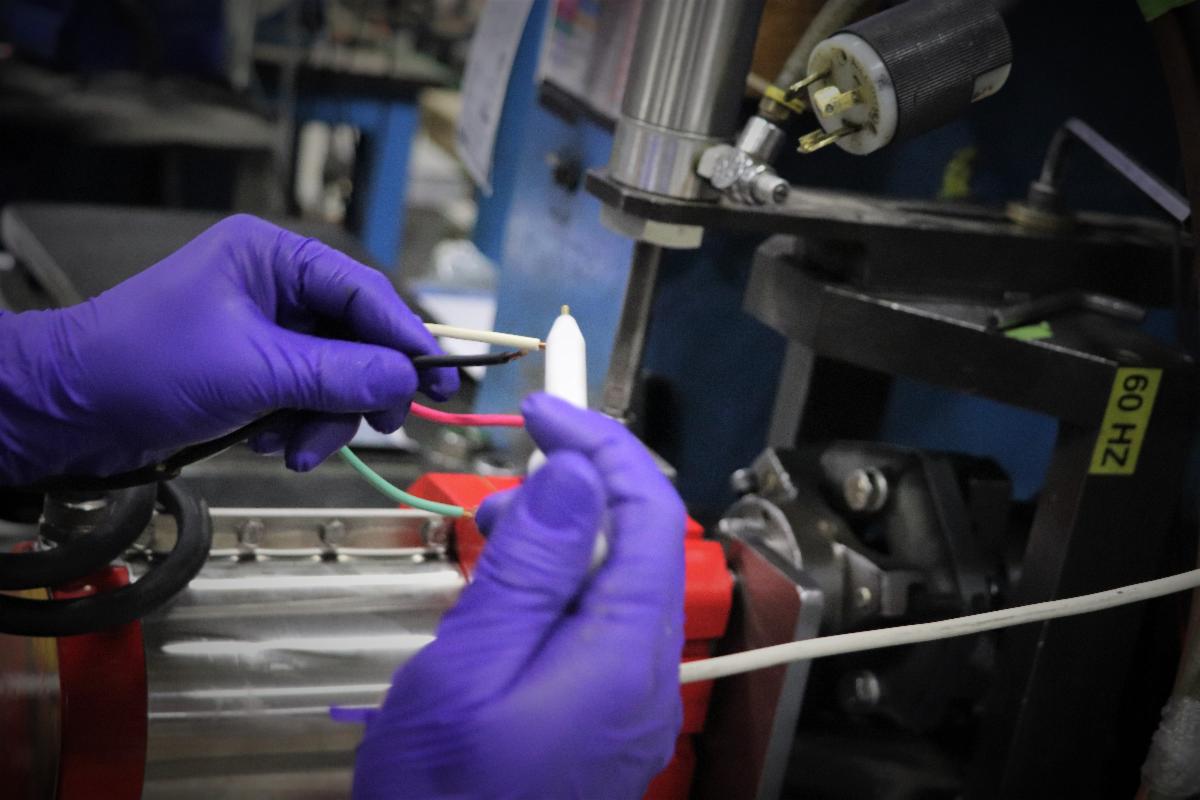
By Lindsey Padilla, Director of Quality, Bison Gear & Engineering
Product quality is a critically important consideration when purchasing electromechanical components, such as electric gear motors. But what does quality mean, and how do you evaluate it as a customer?
Quality involves materials and manufacturing processes that consistently result in high-performing, defect-free products that conform to specifications. That’s necessary, but not sufficient in ensuring that the product performs as needed in a particular application under particular conditions for the intended lifespan.
Ideally, a quality program should be holistic, integrating all aspects of a company. At Bison Gear & Engineering, for example, quality assurance encompasses every aspect of what we do, not only on the manufacturing floor, but also in every department from sales, application engineering, and product development, through manufacturing, quality control, and customer service.
The key is that quality assurance is comprehensive and integrated. Cross-functional teams bring diverse perspectives and challenge assumptions to proactively anticipate potential problems. And we take advantage of quality management system software to track and analyze data from across the company, to identify and correct problems in real time, and to drive continuous improvement.
Beyond the basics
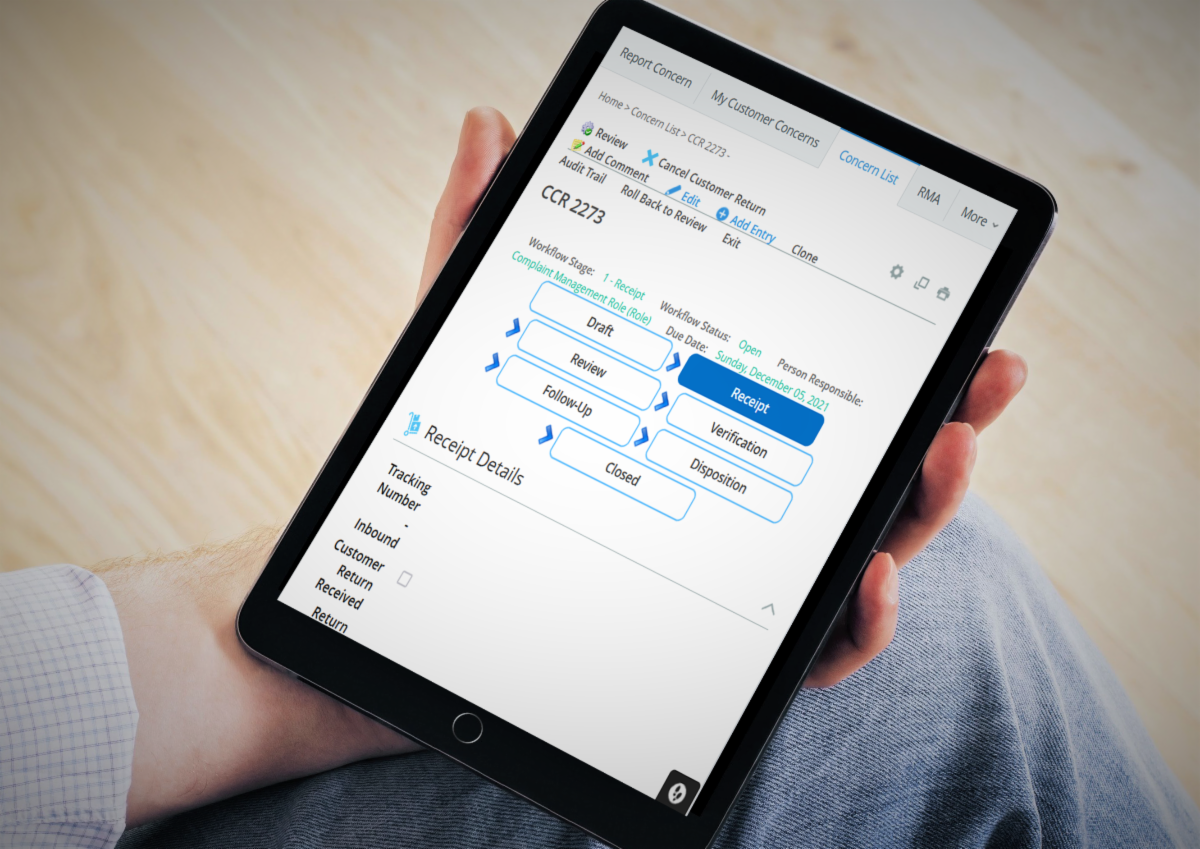
The certification program of the International Standards Organization (ISO) provides helpful general guidelines and imposes a degree of discipline to ensure a systematic approach to quality. The ISO 9001:2015 audits and periodic recertification process ensure that we have a carefully-considered, well-documented, and consistently-implemented program. But, an effective and comprehensive quality program is unique to each industry and Bison’s quality program far exceeds expectations of ISO 9001.
Bison chose to employ Advanced Product Quality Planning (APQP), the general framework of procedures and techniques developed by the automotive industry and broadly used in other industries.
According to the Automotive Industry Action Group (AIAG), the purpose of APQP is "to produce a product quality plan which will support the development of a product or service that will satisfy the customer."
A comprehensive and effective quality program goes beyond these standardized guidelines and frameworks, to include everything from the company philosophy, investment priorities and organizational structure, employee culture and capabilities, to the relationships with suppliers and customers.
Real-time data drives action
Systematic quality programs like ISO 9001 and APQP represent the skeletal framework, and real-time data represent the lifeblood of outstanding quality assurance. At Bison, our implementation of web-based quality management (QMS) software has allowed us to better use data throughout our company and in our relationships with suppliers and customers, resulting in significant, measurable improvement in quality. Access to reliable, real-time data has enhanced our efforts to be proactive and preventative.
The QMS software allows us to capture and analyze data, grouped by product, feature, or process, to identify problems and to drive improvements. Rather than solving issues in isolation, we can apply lessons across customers, products and processes. Instead of firefighting — expending resources correcting problems after they have already caused a negative impact — resources can be applied far more effectively and efficiently to prevent problems and drive continuous improvement.
For example, quality is measured in terms of defective parts per million (DPM), and have been able to reduce our DPM in our DC motors by 68% through analysis of data across multiple products in this category. The manufacturing of these types of motors requires precise pressing of laminations and winding of the wire so that the armature fits exactly in the machine.
By analyzing data across varied motor shafts and different lengths of swages, we improved the quality for the entire product category. Lengths and sizes of the shaft swages were standardized to reduce tooling change in our manufacturing process, thereby improving our cycle time and our ability to respond more quickly to customer orders.
Cross-functional teamwork
Teamwork is also essential to quality assurance. Subjecting concepts and designs to early cross-functional reviews is an investment in time and effort, but it pays off in a smoother process and far better quality. From the beginning of the process of developing new products and features or working with new customers and applications, bringing together multiple viewpoints produce better solutions and prevent future headaches.
Often the process starts with application engineers reaching out to customers, or vice versa, to understand the customer requirements. Design engineers and manufacturing engineers join the cross-functional development and review process to evaluate not only the performance of the design but also the manufacturability. The teamwork continues through the design, prototyping, manufacturing, and customer support stages, with quality engineers.
The teamwork approach also extends to the close working partnership with customers. In one case, a Bison quality engineer helped a manufacturer of commercial ice dispensing machines to identify and correct a problem causing failures in the field, even though it turned out that the root cause was not in the design or manufacture of the gear motor.
The QMS system ensures that any issues that an individual customer may have been analyzed with the benefit of the experience of all customers. Knowledge gained from a problem here, or a solution there, is shared and drives actions internally and throughout the customer base.
Partnership with suppliers
Suppliers, too, are well-integrated into the overall quality program. Bison’s documented Supplier Performance Improvement Process (SPIP) exemplifies our data-driven, team approach to doing business. Our ability to meet customer expectations is dependent on the quality and reliability of our suppliers, and we are actively engaged in systematically evaluating and supporting them.
Our suppliers receive quarterly quality and delivery scorecards. Among the data used to assess the quality and identify opportunities for improvement is a self-audit survey that the suppliers complete. We often have one of our quality engineers perform an onsite assessment. We find that it is critically important that we establish a close working relationship with at least one counterpart at the supplier so that we are prepared to quickly address and correct any issues that may arise.
For example, our incoming parts inspection process identified problems with the hardness of metal bar stock from a supplier. The hardness of the material must be within specified limits to ensure that shafts stand up to the torque applied during the life of the motor. The supplier was applying excessive heat treatment, causing areas of the bar stock to be too hard.
We visited the supplier and met with the quality manager and some of the operators and determined that the type of inspection they were doing was too cumbersome and time-consuming. Either they would continue to run products, while the inspection was happening or they would skip the inspection altogether. We identified an easier and quicker method of inspecting, using cylindrical ring gages that slip onto the bars, which we purchased for the supplier. The ring gauges were effective because an oversized condition is a byproduct of overheating.
Smart inspections
Inspections are critical. But you can’t test everything. We do perform final assembly testing for every item before delivery — including testing for air leaks, torque, and RPM — but incoming parts inspections and in-process inspections must be selective and strategic. There are an average of about 50 parts that go into each gear motor, and each product has up to 500 specifications on the print.
Strategic testing means that we do not just test at random. Our QMS software allows us to use data to drive the inspection process. Data analysis is used to identify parts and processes that are critical or have a history of failing. For example, specific testing protocols are implemented after retooling or other operations that present identified risks.
We will sometimes perform the same tests at multiple points in the process. For instance, we repeat a hipot test (High Potential Test) at various stages because protection against electrical shock is a particularly important safety requirement for electrical motors.
Every company measures quality differently. For us, it is all about meeting customer requirements, specifically defined as delivering more dependable performance, fewer field failures and longer service life. We have found that achieving this goal requires high commitment and investment and a data-driven, proactive, team-based approach.
Related Glossary Terms
- hardness
hardness
Hardness is a measure of the resistance of a material to surface indentation or abrasion. There is no absolute scale for hardness. In order to express hardness quantitatively, each type of test has its own scale, which defines hardness. Indentation hardness obtained through static methods is measured by Brinell, Rockwell, Vickers and Knoop tests. Hardness without indentation is measured by a dynamic method, known as the Scleroscope test.
- quality assurance ( quality control)
quality assurance ( quality control)
Terms denoting a formal program for monitoring product quality. The denotations are the same, but QC typically connotes a more traditional postmachining inspection system, while QA implies a more comprehensive approach, with emphasis on “total quality,” broad quality principles, statistical process control and other statistical methods.
- quality assurance ( quality control)2
quality assurance ( quality control)
Terms denoting a formal program for monitoring product quality. The denotations are the same, but QC typically connotes a more traditional postmachining inspection system, while QA implies a more comprehensive approach, with emphasis on “total quality,” broad quality principles, statistical process control and other statistical methods.