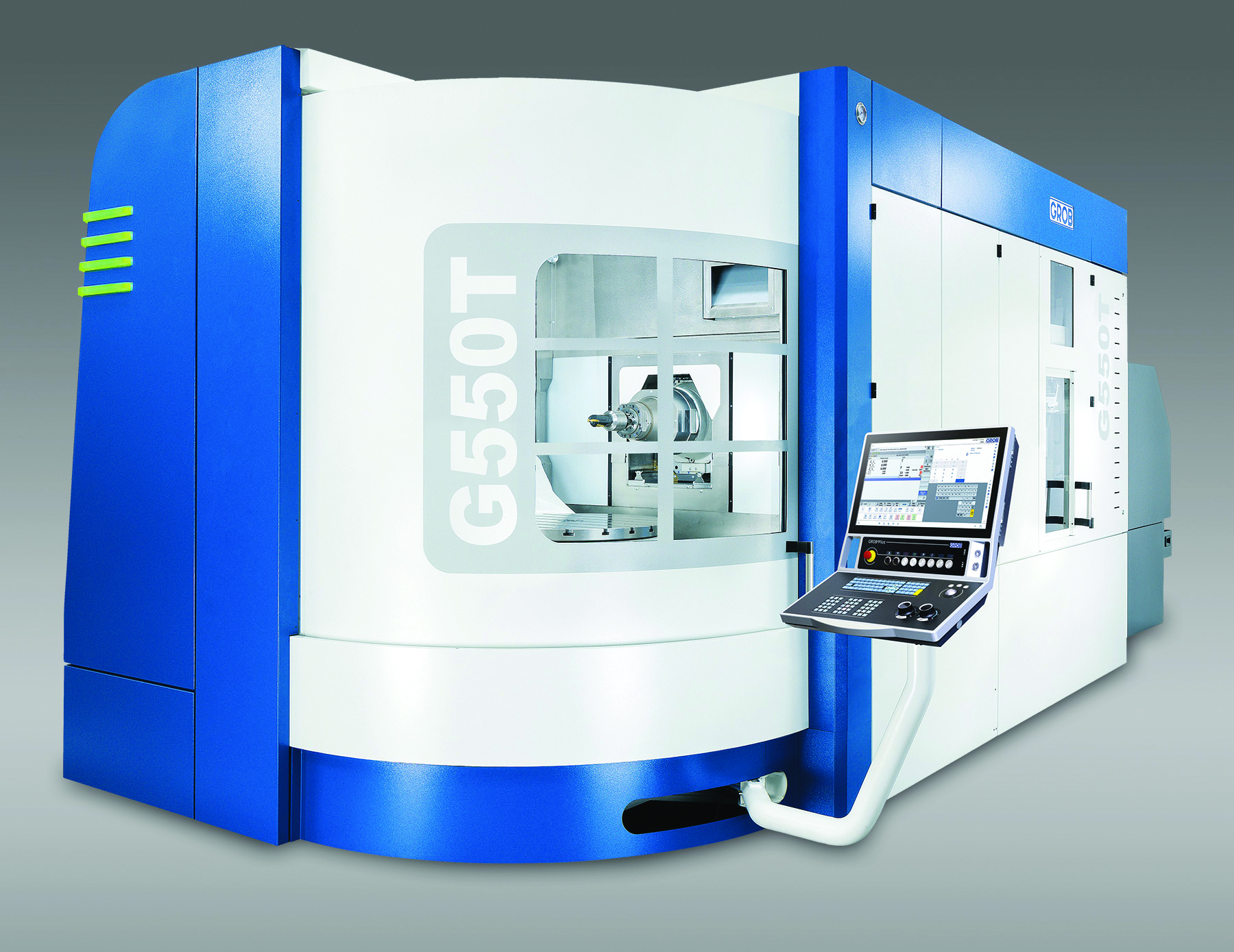
GROB Systems Inc., a developer of manufacturing systems and machine tools, plans to demonstrate power skiving capabilities as well as innovative fir tree mill finishing on its GROB G550T 5-axis mill-turn universal machining center at Manufacturing Technology Series East (formally known as EASTEC) in booth #1720 at Eastern States Exposition in West Springfield, MA from May 13-15, 2025.
The company says that attendees can see how GROB meets and exceeds precision manufacturing demands with its equipment. GROB personnel will be on-hand to answer specific customer application questions.
The GROB G550T offers maximum stability and excellent maintainability, and provides the greatest possible positioning flexibility due to the axes' large swivel range (230ﹾ in the A axis and 360ﹾ in the B axes). A horizontal spindle position permits the longest possible Z-travel path and optimum chip fall.
According to the company, the G550T features a unique arrangement of the three linear axes that minimizes the distance between the guides and the machining point (TCP), providing stability in part production.
A tunnel concept permits the largest possible component (even in the case of extremely long tools) to be swiveled and machined within the work area without collision. The three linear and two rotary axes allow 5-sided machining, 5-axis simultaneous interpolation, as well as GROB TRAORI-turning for precise cutting control.
GROB machining centers are made in the U.S. at the GROB Systems full production facility in Ohio, which has recently been expanded to 500,000 square feet. The facility can include advanced automation solutions for dramatically increased productivity.
Click here to learn more about the GROB G550T 5-axis mill-turn universal machining center.
Contact Details
Related Glossary Terms
- centers
centers
Cone-shaped pins that support a workpiece by one or two ends during machining. The centers fit into holes drilled in the workpiece ends. Centers that turn with the workpiece are called “live” centers; those that do not are called “dead” centers.
- interpolation
interpolation
Process of generating a sufficient number of positioning commands for the servomotors driving the machine tool so the path of the tool closely approximates the ideal path. See CNC, computer numerical control; NC, numerical control.
- machining center
machining center
CNC machine tool capable of drilling, reaming, tapping, milling and boring. Normally comes with an automatic toolchanger. See automatic toolchanger.
- milling machine ( mill)
milling machine ( mill)
Runs endmills and arbor-mounted milling cutters. Features include a head with a spindle that drives the cutters; a column, knee and table that provide motion in the three Cartesian axes; and a base that supports the components and houses the cutting-fluid pump and reservoir. The work is mounted on the table and fed into the rotating cutter or endmill to accomplish the milling steps; vertical milling machines also feed endmills into the work by means of a spindle-mounted quill. Models range from small manual machines to big bed-type and duplex mills. All take one of three basic forms: vertical, horizontal or convertible horizontal/vertical. Vertical machines may be knee-type (the table is mounted on a knee that can be elevated) or bed-type (the table is securely supported and only moves horizontally). In general, horizontal machines are bigger and more powerful, while vertical machines are lighter but more versatile and easier to set up and operate.