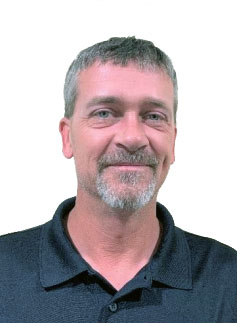
Brant Pascavis has filled a position of Sr. Application Specialist at GWS Tool Group.
In this role, Brant will be responsible for supporting GWS distributors and key metalworking customers in the application of GWS high-performance cutting tool solutions. Cutting tools from GWS include both standard and purpose-built tooling, such as end mills, form tools, step tools, drills, reamers, taps, and turning inserts.
“Brant’s extensive metalworking and management experience is an ideal fit for our organization” said Adam Lafferty, Executive Vice President of Sales. “His background in both the die/mold and automotive industries, coupled with a long successful track record working with key distribution, will immediately add value to our customers.”
Brant started his career in the plastic injection mold industry as a tool and die apprentice. His experience led him to become a machine tool application engineer for one of the premier machine builders in the world. After honing his skills on the machine tool side, Brant moved into the cutting tool world for a highly regarded global cutting tool manufacturer. Over his 17 years with this company, Brant elevated quickly in different roles from High-Speed Machining Specialist to East USA Sales manager. His most recent was as Group Manager for a new automotive sales division focused on the U.S. big three. For over 22 years, he has been applying his knowledge at the spindle to help North American manufacturers thrive. For GWS, Brant will be responsible for business development and key customer management in Michigan.
Contact Details
Related Glossary Terms
- metalworking
metalworking
Any manufacturing process in which metal is processed or machined such that the workpiece is given a new shape. Broadly defined, the term includes processes such as design and layout, heat-treating, material handling and inspection.
- turning
turning
Workpiece is held in a chuck, mounted on a face plate or secured between centers and rotated while a cutting tool, normally a single-point tool, is fed into it along its periphery or across its end or face. Takes the form of straight turning (cutting along the periphery of the workpiece); taper turning (creating a taper); step turning (turning different-size diameters on the same work); chamfering (beveling an edge or shoulder); facing (cutting on an end); turning threads (usually external but can be internal); roughing (high-volume metal removal); and finishing (final light cuts). Performed on lathes, turning centers, chucking machines, automatic screw machines and similar machines.