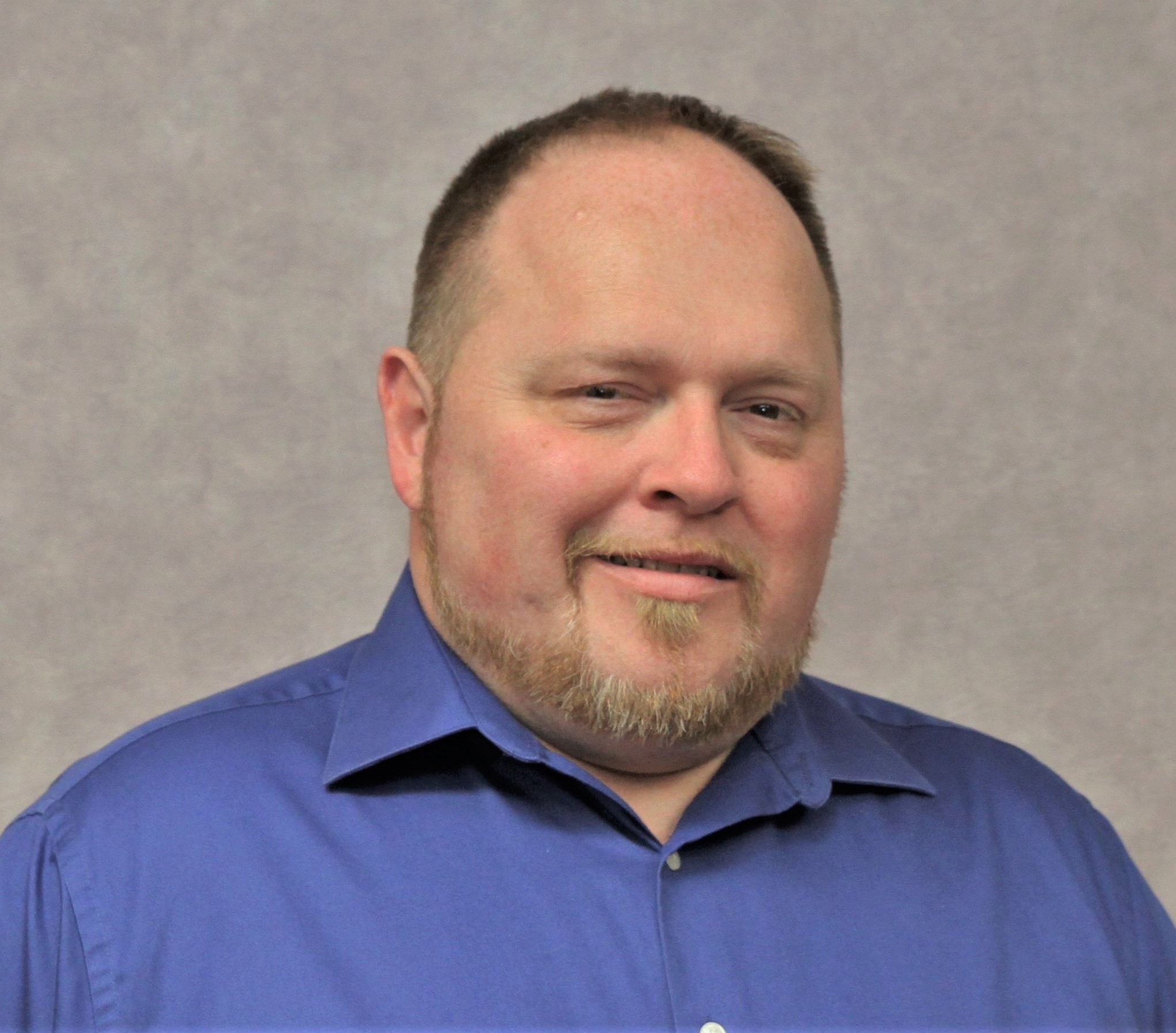
Kitagawa North-Tech Inc., Schaumburg, Ill., which manufactures standard chucks, advanced chucks, custom-engineered workholding and steady rests, hired Edward Borsos as regional sales manager. Mr. Borsos has over 30 years of machining and metalworking industry experience. He will be responsible for supporting and developing channel partners and end-users selling Kitagawa’s standard chucks, advanced chucks and engineered rotational and prismatic workholding solutions. Borsos has extensive experience in Automotive and Oil & Gas, as well as general turning and milling workholding applications.
Mr. Borsos began his career as a toolmaker and machinist and worked in various supervisory positions at metalworking machine shops and later transitioned into technical Workholding sales for MSCI Industrial Supply. In his most recent position we worked in regional sales management for Rohm, German-based workholding company before joining Kitagawa NorthTech.
Ed Borsos will help support and manage projects for the custom engineered solutions business. Kitagawa NorthTech’s engineered workholding solutions are supported by an in-house applications engineering team committed to developing custom workholding for turning and prismatic applications. In addition to designing and engineering custom solutions, Kitagawa NorthTech utilizes their in-house design, manufacturing, inspection and testing facility to manufacturer, modify and test components and Workholding systems for their customers.
Mr. Borsos resides in Waterford, Michigan and will be report out of Kitagawa NorthTech’s headquarters and full-service manufacturing facility for the Americas based in Schaumburg, IL. Upon joining the company, Mr. Boros adds, “I am excited to join a company with such a rich history in workholding. Kitagawa has always been the gold standard of chucks in the workholding industry. In addition, Kitagawa NorthTech’s custom engineered workholding capabilities offer customers superior part-specific machining solutions for turning and prismatic applications.”
Contact Details
Related Glossary Terms
- gang cutting ( milling)
gang cutting ( milling)
Machining with several cutters mounted on a single arbor, generally for simultaneous cutting.
- metalworking
metalworking
Any manufacturing process in which metal is processed or machined such that the workpiece is given a new shape. Broadly defined, the term includes processes such as design and layout, heat-treating, material handling and inspection.
- milling
milling
Machining operation in which metal or other material is removed by applying power to a rotating cutter. In vertical milling, the cutting tool is mounted vertically on the spindle. In horizontal milling, the cutting tool is mounted horizontally, either directly on the spindle or on an arbor. Horizontal milling is further broken down into conventional milling, where the cutter rotates opposite the direction of feed, or “up” into the workpiece; and climb milling, where the cutter rotates in the direction of feed, or “down” into the workpiece. Milling operations include plane or surface milling, endmilling, facemilling, angle milling, form milling and profiling.
- turning
turning
Workpiece is held in a chuck, mounted on a face plate or secured between centers and rotated while a cutting tool, normally a single-point tool, is fed into it along its periphery or across its end or face. Takes the form of straight turning (cutting along the periphery of the workpiece); taper turning (creating a taper); step turning (turning different-size diameters on the same work); chamfering (beveling an edge or shoulder); facing (cutting on an end); turning threads (usually external but can be internal); roughing (high-volume metal removal); and finishing (final light cuts). Performed on lathes, turning centers, chucking machines, automatic screw machines and similar machines.