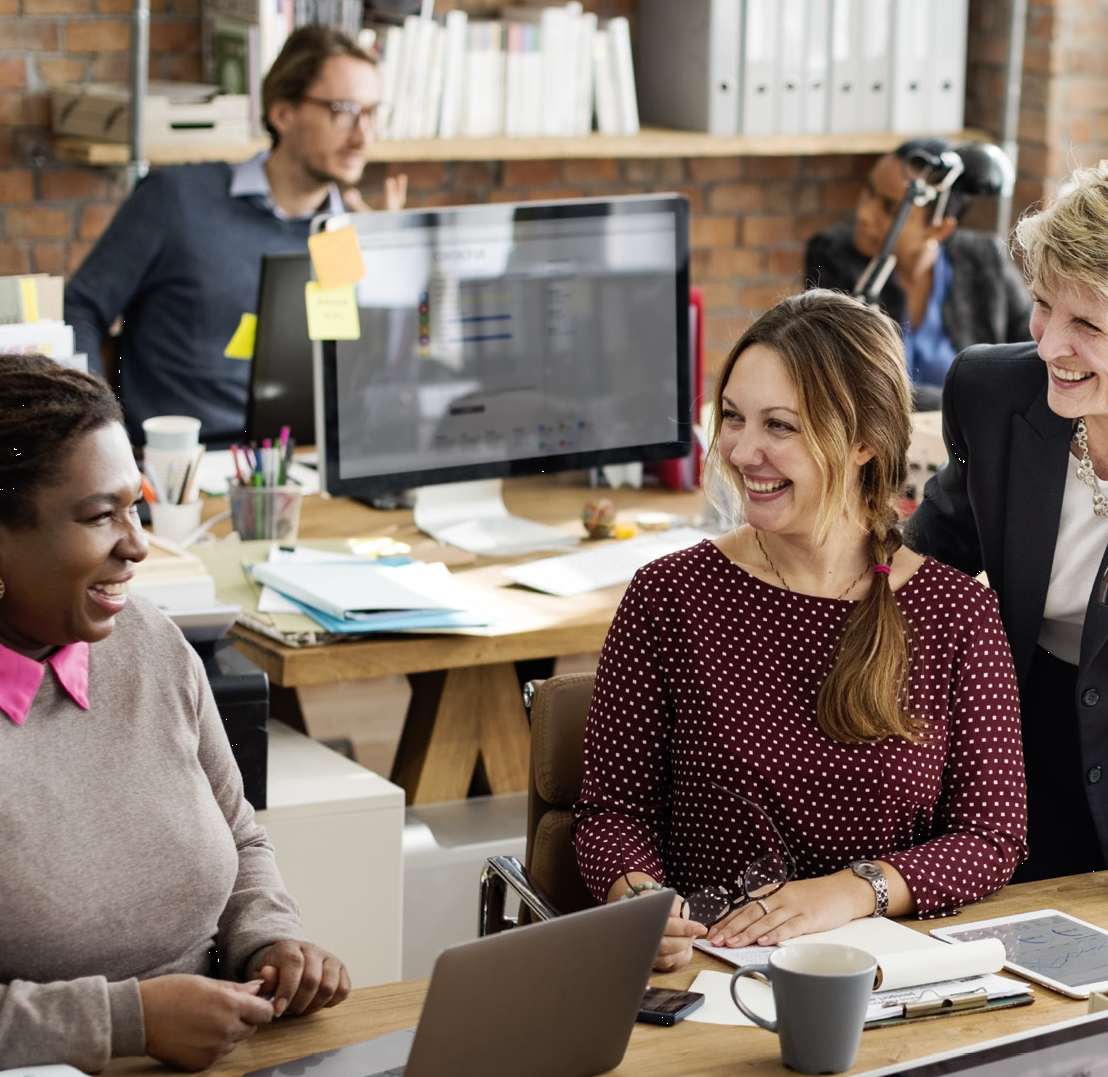
A recent survey has 80 percent of manufacturers and energy companies implementing or developing a digital workplace transformation plan. Only 18 percent are allocating at least a quarter of their budget toward these efforts over the next 12 months, however—and that’s the minimum percentage needed to get started, according to Dan Chalk, director of solution engineering for NTT Data Services, Plano, Texas.
Another 32 percent say they are investing 10 percent toward these efforts, and 6 percent have no workplace transformation investment plans. The study of senior IT and business leaders was conducted in 2017 by IDG Research Services and examines the approach manufacturing and energy firms are taking to enable a digital workplace and the obstacles they encounter.
According to the study, a digital workplace is the concept that there is a virtual equivalent to the physical workplace, which must be planned and managed coherently because it is fundamental to people’s productivity, engagement and working health.
Chalk said for customers in almost any segment, a 25 percent allocation will get the business started, but it’s going to take 2 years or so to make meaningful gains toward a successful transformation. “It’s a pretty complicated undertaking unless you dedicate a good, healthy amount of time to it, and it costs some money.”
The benefits of a successful transformation, however, can be significant. Chalk provided the airline industry as one example, “where engineers are dealing with some of the most complicated 3D CAD rendering models that exist.”
He said: “If you look at their key design elements, it’s about their access to quickly stand-up projects anywhere the labor is available to design in real time and exchange information back and forth, and you can’t afford to have those engineers being in isolated centers of excellence that are physically located in customer facilities or in their own facilities. They have to be able to go anywhere in the world. So if you can virtualize those workloads and present them to any type of device, regardless of location, not only do you enable that broader workforce of partners that are in the industry, but you protect your intellectual property. You don’t have to worry about people stealing the data route.”
Ultimately, the transformation exposes a manufacturer to more customers and more supply chain participants in the business transaction itself, Chalk added.
A less-than-optimal investment strategy might be the result of a manufacturer being focused on some “cool” technology tool—a “shiny object” that people latch onto because of its cool factor—as opposed to determining how to deliver new value, he said. “How am I going to move the people who are making a product closer to the people who are with our customers to shrink that cycle time, get more efficient and enable more customer interaction and value-added discussions?”
To foster a dynamic workplace, NTT Data Services says transformation success hinges on a well-planned, four-step approach:
- Framwork – Guide, departmentalize and institutionalize the journey
- Analytics – Provide measurable business insights and allow manufacturers to be proactive against pain points
- Flexibility – Support the device and user, while remaining relevant
- Long-term viability – Continuous, incremental improvements deliver business value for every stage
The complete report is available at NTT Predictable Success Marketpulse White Paper.
Related Glossary Terms
- centers
centers
Cone-shaped pins that support a workpiece by one or two ends during machining. The centers fit into holes drilled in the workpiece ends. Centers that turn with the workpiece are called “live” centers; those that do not are called “dead” centers.
- computer-aided design ( CAD)
computer-aided design ( CAD)
Product-design functions performed with the help of computers and special software.